Сторінка 42 з 92
3. ТЕХНОЛОГІЧНА ОБРОБКА ОБМОТОК - СУШКА, Просочення
І запікання
а) Призначення технологічної обробки
б) Технологія і режими сушіння, просочення і запікання обмоток
Обмотки на напругу до 35 кВ можуть проходити сушку в сушильних камерах з паровим обігрівом. Камери обладнані витяжною вентиляцією для видалення парів вологи. Температура в камері не повинна перевищувати 105-110 ° С. Час сушіння встановлюється за найбільшою обмотці в даній партії і в залежності від температури в камері. Сушка обмоток на напругу 35 кВ і вище проводиться в вакуум-сушильних шафах горизонтального або вертикального типу. Вакуум, що створюється в шафі, сприяє поліпшенню процесу і скорочує час сушіння. Після прогріву обмотки вакуум, який створює різницю тисків між внутрішніми і зовнішніми шарами ізоляції, сприяє виходу вологи на поверхню. Крім того, наявність вакууму знижує температуру пароутворення, т. Е. Перехід вологи в газоподібний стан. Це дозволяє значно скоротити час сушіння і головне при порівняно невисокій температурі краще висушити ізоляцію (до десятих часток відсотка вологості). Чим менше залишковий тиск в шафі, тим краще показники сушіння.
Паровоздушная середовище, що утворюється в вакуум-сушильній шафі, відкачується вакуумними насосами. На шляху від шафи до вакуум насосу обов'язково повинна бути встановлена конденсаційна колонка, де проходять пари вологи конденсуються і стікають у вигляді конденсату (води). Колонка захищає вакуум-насоси від попадання в них води і дозволяє враховувати кількість вологи, що вийшла з обмотки.
Існує кілька режимів вакуумної сушки в залежності від розмірів і маси обмоток, величини напруги і матеріалу ізоляції, конструкції і призначення обмоток.
Кожен режим сушки ділиться на два основних етапи: 1) прогрів обмотки, коли обмотка нагрівається до необхідної температури і створюються умови, сприятливі для виходу вологи; 2) власне сушка, коли з обмоток видаляється велика частина вологи.
Обмотки в вакуум-сушильну шафу завантажують або візком (в шафу горизонтального типу), на яку ставлять по можливості однотипні обмотки, як показано на рис. 12-30, або опускають за допомогою мостового крана (в вертикальний шафа). Двері або кришку шафи герметично закривають. Обсяг шафи з'єднаний з атмосферою за допомогою вакуумного вентиля для зняття вакууму. Включають парової обігрів і починають прогрів обмоток. Для збереження якості ізоляції ставлять обмотки не ближче 300 мм від нагрівачів (радіаторів парового обігріву), а температура останніх не перевищує 110 ° С.
Залежно від характеристик завантажених обмоток прогрів триває 3-5 ч, після чого закривають вентиль для зняття вакууму і включають вакуум-насос. Вакуум створюють ступенями по 15-20 см рт. ст. протягом _1 ч. При наявності в обмотках паперово-бакелітові циліндрів вакуум створюють більш плавно, щоб уникнути розшарування циліндрів.
Залишковий тиск в шафі прагнуть знизити до мінімально можливого (близько 3-5 мм рт. Ст.), Т. Е. Створюють глибокий вакуум. Щогодини в журналі фіксують тиск пара в мережі, температуру і залишковий тиск в шафі, а також кількість конденсату, що виділився протягом 1 ч. Тривалість сушіння залежить від стану і характеристик обмоток, від режиму роботи шафи і становить 14-35 год.
Після закінчення сушіння вимикають парової обігрів, зупиняють вакуум-насос і відкривають вентиль зняття вакууму, після чого відкривають двері (або кришку) шафи. Викочують візок і, не знімаючи обмоток, підтягують гайки на стяжних шпильках. Розвантажують візок і передають обмотки на подальшу обробку: обробку, пресування, просочення, запікання.
До останнього часу ще не на всіх заводах обмотки пресують за допомогою гідравлічних пресів і сушать під тиском. Тому висушені обмотки внаслідок великої усадки ізоляції доводиться додатково обробляти, як було описано вище. На деяких заводах (в основному з ремонту електроустаткування) обмотки все ще просочують лаком. Нижче наводиться технологія просочення і запікання обмоток.
Висушені обмотки трансформаторів після їх остаточної обробки просочують в гліфталевим лаку ГФ-95 (ГОСТ 8018-56) або меламіно-гліфталевим лаку МЛ-92 (ВТУ УХП-13-57). Робоча в'язкість лаку при просочуванні повинна бути 28-36 с по ВЗ-З при 18- 20 ° С, а в зимовий час, коли температура в цеху нижче 18 ° С, - 20-28 с. Для отримання зазначеної в'язкості лак розбавляють сумішшю ксилолу та уайт-спіриту в співвідношенні 1: 1, додаючи розчинник в просочувальний лак невеликими порціями при безперервному помішуванні.
Час перебування обмоток на повітрі після сушки до просочення їх лаком регламентовано і становить не більше 10 ч при відносній вологості повітря приблизно 70%. Підготовлені обмотки, остиглі до 40-45 ° С, повільно занурюють в бак з лаком так, щоб рівень лаку був вище обмотки на 50 мм, і витримують до припинення виділення бульбашок повітря на поверхні лаку, але не менше 10 хв.
Обмотку повільно виймають з лаку і, давши стекти основним лишків лаку в просочувальний бак, ставлять на піддон, встановлений з нахилом. Тут обмотки витримують до повного стікання надлишків лаку протягом 2-4 ч, після чого їх ставлять на візок і завантажують в піч для запікання.
Технологічний процес запікання обмоток трансформаторів до 110 кВ включно полягає в наступному. Просочені обмотки завантажують в піч з обов'язковою циркуляцією повітря. З метою збереження тепла і підтримки необхідної температури відбувається часткова рециркуляція повітря. Приплив свіжого повітря і викид повітря з парами розчинників регулюються заслінками.
Після завантаження обмоток піч закривають, включають обігрів печі і повітря, систему циркуляції повітря. Потім поступово (по 20 ° С в 1 ч) піднімають температуру повітря в шафі до 100-110 ° С. Тривалість запікання залежить перш за все від властивостей просочувальних лаків і температури запікання. При 100-110 ° С обмотки, просочені лаком МЛ-92, запікають не менше 10 год, лаком ГФ-95 - не мен ^ її 20 год до повного зникнення відлила лакової плівки в нижній частині обмотки в місцях можливого напливу лаку.
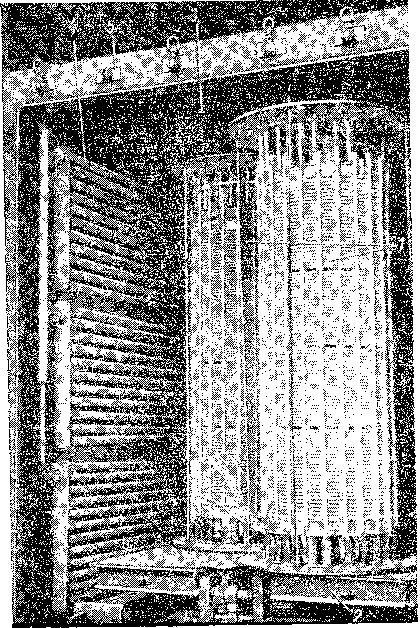
Мал. 12-30. Сушка обмоток в горизонтальному шафі.
1 - обмотка; 2 - візок; 3 - горизонтальний вакуум-сушильну шафу; 4 - радіатори парового обігріву, 5 - притиски для ущільнення відкидний двері шафи.
Після запікання лакова плівка повинна бути однорідною, без зморшок. Плівка, що не запечена до кінця, при роботі обмоток в гарячому маслі швидко розм'якшується і втрачає свої механічні властивості. Щогодини фіксують в журналі режим запікання. Після закінчення процесу запікання відключають обігрів печі і вивантажують з неї обмотки.
Технологічний процес вакуумного запікання обмоток класу напруги вище 110 кВ відмінний від описаного. Завантаживши обмотки в вакуум-сушильну шафу, двері закривають і герметизують, після чого подають пар в нагрівачі. Поступово (20 ° С в 1 ч) піднімають температуру повітря в вакуум-сушильній шафі до 95-105 ° С і при цій температурі нагрівають обмотки протягом 1 ч. Прогрівання обмотки, закривають вентиль для впуску повітря в шафу, включають вакуум насос і ступенями по 250 мм рт. ст. протягом 3 ч створюють вакуум в шафі до максимального, але не нижче 750 мм рт. сг. При цьому вакуумі і температурі 95 105 ° С запікають обмотки доти, поки вимірювання виходить конденсату протягом 3 год не покажуть, що виділення його припинилося. Знімають вакуум і, відкривши двері шафи, при 95-105 ° С продовжують запікання до повного зникнення отлипа лакової плівки на обмотках, але не менше 5 ч. Цей режим оберігає обмотки від освіти на їх поверхні повітряних бульбашок і порожнин під лакової плівкою. Після запікання лакова плівка повинна бути блискучою, однорідної, без зморшок і не давати відлипу.
в) Устаткування сушильно-просочувального відділення (цеху), протипожежні заходи
Комплекс обладнання для вакуумної сушки обмоток складається із сушильної шафи (рис. 12-30) з вбудованими в нього радіаторами парового обігріву 4, вантажний візком 2 з пневмо- або електроштовхачів, вакуум насосом або вакуум-насосною станцією, конденсаційної колонкою для уловлювання конденсату з оброблюваних виробів.
Вакуум-сушильну шафу являє собою зварений прямокутний бак з ребрами жорсткості і з теплоізоляцією зовнішніх поверхонь. Одна стінка бака являє собою відкидну двері, підвішену на поворотному кронштейні і обладнану електроприводом. Розміри шафи визначаються габаритами оброблюваних обмоток. По внутрішніх поверхнях шафи (його статі і стінок) розташовані радіатори парового обігріву. Міцність корпусу розрахована на повний вакуум всередині шафи (залишковий тиск дорівнює нулю). Всі зварні шви виконують міцно-щільними і ретельно перевіряють їх на герметичність.
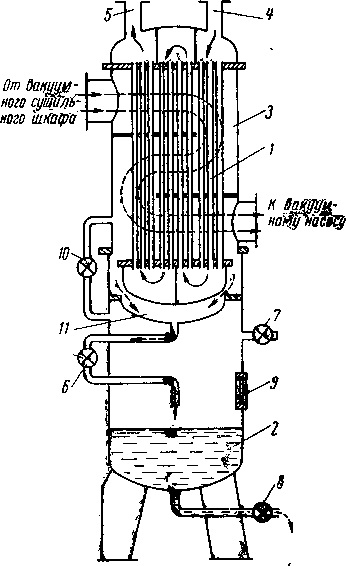
Мал. 12-31. Конденсаційна колонка.
1 - Теплообмінник; 2 - збірна конденсату; 3 - верхня порожнина колонки; 4 - вхід охолоджуючої води; 5 - вихід води; 6 - вентиль для спуску конденсату верхньої порожнини; 7 - вентиль для зняття вакууму; 8 - вентиль для зливу конденсату; 9 - оглядове вікно; 10 - вентиль для вирівнювання тиску; 11 - днище.
Герметичність закривання дверей забезпечується спеціальним гумовим джгутом, покладеним по периметру рами шафи, до якої прилягає двері.
Для отримання залишкового тиску 5 10 мм рт. ст. з вакуум-сушильного шафи відкачують повітря два, а іноді три вакуум-насоса типу РМК.ВН-6.12.ВН-300 і ін.
Для збору вологи, що міститься в откачиваемой пароповітряної суміші, а також для захисту насосів від вологи між вакуум-сушильною шафою і насосами в трубопровід врізають конденсаційну колонку (рис. 12-31). При проходженні пароповітряної суміші через верхню порожнину колонки 3 пар конденсується в теплообміннику 1 і стікає на днище 11. Закривши вентиль 7 і відкривши вентиль 10, вирівнюють тиск у верхній порожнині і в збірнику конденсату 2. Відкривши вентиль 6, зливають конденсат до збірки, після чого закривають вентилі 6 в 10, г вентиль 7 знову відкривають. За допомогою вентиля 8 конденсат зливають в мірну ємність для визначення кількості вилученої вологи.
Застосовувані в даний час просочувальні лаки ГФ-95 і МЛ-92 містять смоли, до складу яких входять жирні кислоти і масла, а також розчинники: бензин, бензол, толуол та інші легкозаймисті речовини. Крім того, гліфталевий і меламіно- гліфталевий лаки токсичні. У зв'язку з цим працюють в сушильно-просочувальному відділенні повинні дотримуватися протипожежні правила і правила техніки безпеки.
Сушильно-просочувальне відділення відокремлюють від інших ділянок цеху капітальною стіною і потрібно обладнувати приміщення відповідно до протипожежних правил. Все електрообладнання цього відділення має виконати у вибухонебезпечному виконанні. Сушіння, просочування і запікання обмоток повинні проводитися в добре вентильованому приміщенні, обладнаному припливно-витяжною вентиляцією.