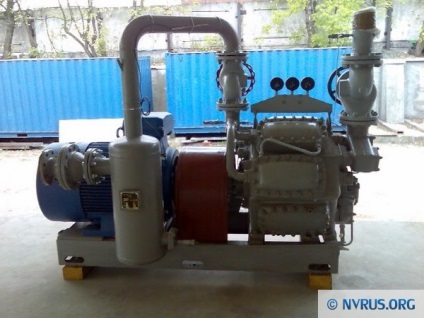
Тільки так можна буде підтримувати його на необхідному рівні. Також воно прослужить вам дуже довго, якщо дотримуватися всіх норм безпеки. Технічний стан обладнання визначається за рахунок дефектів, які негативно впливають на правильне функціонування всієї холодильної системи. Кожен власник і користувач холодильними установками повинен правильно з ними поводитися. Це відноситься не тільки до об'єкта в цілому, але також до кожного вузла окремо.
Найчастіше фахівцем визначається дефект за допомогою контрольно-вимірювальних приладів і також спеціальних технічних приладів. Дуже часто вони включають в себе тести. Засоби технічного діагностування дозволять виключити розбирання агрегату. У такому випадку система не завершить роботу, і параметри не порушуватимуться. В результаті супутні роботи навпаки підвищать ефективність робочого процесу і знизять ресурси на обслуговування і ремонт.
Схема діагностики обладнання
Технічне діагностування має типову схему, яка включає в себе сукупність виконавців і технічних засобів. Найпростіший варіант такої системи складається з наступних пристроїв:
- датчики, які можуть уловлювати необхідну інформацію про об'єкт;
- перетворювачі, які будуть перетворювати отриманий сигнал в ту величину, яка буде зрозуміла майстру;
- пристрою, які обробляють інформацію і виводять її.
Системи діагностування лінійної частини розділяються по виду наданої інформації на:
- на загальну і локальну;
- на функціональну і тестову.
Якщо говорити про локальний діагностуванні, то тут обстежується кожен вузол окремо. А ось загальне діагностування дозволяє оцінити роботу відразу всього холодильного обладнання. Тестова система дозволяє в результаті певних дій отримає відповідь від пристрою. Функціональна система діагностує стан об'єкта на момент роботу, тобто в той момент, коли здійснюється нормальний режим роботи. За допомогою таких систем можна вирішити ряд завдань з перевірки на справність обладнання, працездатність всього обладнання, а також пошук дефектів.
Системи діагностування лінійної частини застосовують послуги майстра, коли їх викликають перевірити обладнання. Вони перевіряють роботу пристрою перед установкою, під час установки і вже після. Також процедуру потрібно провести і перед ремонтом або для оцінки якості роботи. Не варто відкладати перевірку холодильних агрегатів на потім, так як під час роботи пристрій піддається вібрації, масовим обмінам і теплообміну. Все це відбивається на режим і параметри роботи. Ось так якщо розглядати компресор, як збір деталей, то тут визначаються такі показники, як температура, тиск, витрата масла, холодопродуктивність і витрата електроенергії.
Для вирішення поставлених вище завдань створюються математичні моделі, які перевіряють працездатність холодильного агрегату. Деякі фахівці створюють нелінійні і лінійні рівняння, щоб побудувати необхідну модель. Кожна модель об'єкта має базу для побудови, яка створюється з алгоритмів. Побудова таких алгоритмів полягає в сукупності перевірок і працездатний стан. В результаті розраховуються дефекти між собою.
Процес діагностування пов'язаний з рядом складних завдань, і тому за таку роботу візьметься тільки справжній фахівець. Алгоритм часто використовується для автоматизації системи. Сьогодні дуже багато холодильних агрегатів мають автоматику, яка дозволяє спростити експлуатацію, а також запобіжить від передчасного виходу з ладу всього пристрою.