отримання відрізка хвилеводної труби, фланця та їх складання;
обробка контактної поверхні фланця і свер-ня кріпильних отворів;
нанесення захисних покриттів і обробка Токон-сущих поверхонь;
виготовлення діелектричних пластин поглинутої-ника;
нанесення на поверхню пластин поглинає покриття;
збірка хвилеводної узгодженої навантаження;
Перші три пункти детально розглянуті в попе-дущіх розділах. Специфічно тут лише тільки изго-товление пазів в порожнині хвилеводної труби. Їх напів-ють протягуванням, використовуючи спеціальну протяжку, яка одночасно формує необхідну кількість па-поклик і забезпечує їх чистову обробку.
Пази простягаються до збірки хвилеводної труби з фланцем.
Розглянемо більш докладно пп. 4, 5 і 6.
Тут в якості матеріалів діелектричного осно-вання поверхневих поглинаючих навантажень викорис-ся кераміка, скло, гетинакс, слюда, текстоліт. Роль поглинає покриття виконують тонкі плівки металів (сплавів) з високою питомою опору-ленням, наприклад тонкі плівки ніхрому. Можна ис-користувати і неметалеві провідні плівки, зокрема плівки лакосажевих суспензій.
Керамічні підкладки для поверхневих поглинутої-щающую хвилеводних навантажень товщиною від 0,3 до 1,5ммізготавлівают з високоглиноземисті маси «Міналунд» (М-7). Технологічний процес изготовле-ня керамічної плівки полягає в наступному. Шлік- кер, виготовлений на основі 3-4% -ного розчину нат- рійкарбоксіметілцеллюлози і маси М-7 у співвідношенні-ніі1: 1, розливається на склі і висушується в тече-ня 50-60чпрі кімнатній температурі. В результаті виходить еластичність керамічна плівка, кото-раю легко відділяється від скла і добре обрабат-ється.
У штампі або пристосуванні з діелектричної плівки вирубується підкладка хвилеводної навантаження за-даної конфігурації. Невелика кількість зв'язки в сирих деталях дозволяє застосувати одноразовий об-жиг при температурі 1720 ° С з витримкою 5-6ч.После випалу поверхню підкладки, що прилягала до скла, має чистоту 7-8-го класу, а протилежна поверхня - 5-6 -го класу шорсткості.
Тонку плівку нихрома наносять на поверхню ке-раміческой підкладки випаровуванням у вакуумі. Ніхром осідає на нагріту підкладку. Після нанесення шару заданої товщини він спікається в вакуумі при 450 ° С. Нагрівання підкладки непрямий.
Технологічний процес виготовлення плоских по-глощающіх навантажень на склі полягає в наступному. Пря моугольная скляна пластина ретельно обезжі-ється і з одного боку матируется. На краю пласти- ни вжіганіем наносять срібні контактні май-ки. Шар нихрома осаджують на матированную поверх-ність вакуумним розпиленням. Спікання шару нихрома відбувається за рахунок його нагріву електричним струмом, що підводиться до плівки через срібні контакти. При цьому опір плівки зменшується приблизно на 25%.
Далі слід лакування пластини (якщо воно пре-дусмотрено кресленням) і обрізка для отримання заданий-ний конфігурації.
При виготовленні поглинаючих пластин на слюди-них підкладках послідовність операцій та ж, що і на скляних, за винятком матирования. Слюди-ні очистки підкладки матуючого, шар нихрома наноситься на поверхню свежерасщепленной слюди.
Поглинають навантаження на підкладках з гетинаксу виготовляються без спікання з огляду на низьку термостійкість-сти гетинакса. Тому треба враховувати, що опираючись-ня шару нихрома після вилучення з вакуумної уста-новки буде збільшуватися.
Лакосажевие суспензії наносять на підкладки нама-зиваніем, зануренням або пульверизацією з подальші-щей сушінням.
При складанні поглинають пластини встановлюються в пази в стінках хвилеводної труби або кріпляться в за-Глушко. Перед цим торцеві поверхні пластин, з-доторкаються зі стінками хвилеводу, змащують клеєм. Для конструкції, показаної на рис. 3.2,6, по-глощающіе пластини спочатку кріпляться штифтами в па-зах заглушки, потім вклеюються в пази планки, після чого вийшла складальна одиниця встановлюється в порожнину хвилеводу і положення заглушки фіксує-ся гвинтами.
Налаштування хвилеводних узгоджених навантажень ве-деться на стандартних вимірювальних стендах (§ 4.1) по мінімуму коефіцієнта відображення.
Хвилеводні узгоджені навантаження з об'ємним сопротівленіемможно використовувати для розсіювання не тільки малих (одиниці ватів), але і великих рівнів потужності (до 1000Вт) .Малие значення КСХН цих на-грузок досягаються правильним вибором розмірів і форми поглинаючих опорів. їх клиноподібна
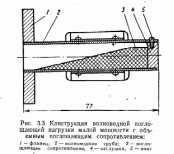
форма забезпечує мінімальний КСХН в широкому діапазоні частот і рівномірне нагреваніе'всего опору-тивления. Розглянемо найбільш типові конструкції хвилеводних узгоджених навантажень з об'ємним опору-опором.
На рис. 3.3 показана конструкція хвилеводної злагоди-сова навантаження з об'ємним опором, рассчи-танной на поглинання потужності до 5вт.Она виконана у вигляді відрізка хвилеводної труби2с фланцем1на од-ном кінці і короткозамикающего металевої заглушити-кою 4 на іншому кінці. Усередині хвилеводної труби жест-ко закріплено поглинає опір клінообраз-ної форми3.Заглушка кріпиться до хвилеводної трубі вінтом5.
Для поглинання великої потужності (сотні ват) ис-користується волноводная узгоджена поглинає навантаження, конструкція якої представлена на рис. 3.4. Корпус навантаження складається з двох частей2і3, изготов-ленних литтям. Обидві частини скріплюються вінтамі4і по-сле збірки утворюють прямокутний хвилевід з флан-цем і охолоджуючими ребрами. Хвилевід з боку,
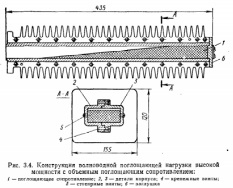
протилежної фланця, закритий металевою за-глушкой6, укріпленої за допомогою гвинтів. Усередині віл-новода встановлено поглинає сопротівленіе1, за-кріплене в волноводе стопорними вінтамі5.
Технологічні процеси, які використовуються для отри-ня корпусів хвилеводних узгоджених навантажень, по-дрібно розглянуті в попередньому викладі: рассмот-рим докладніше технологію виготовлення і установки об'ємних поглинаючих опорів.
Об'ємні поглинають опору низького і середнього рівнів потужності виконуються з матеріалів типу М (М-1, М-2, М-3), що представляють собою композицію карбонільного заліза і
полістиролу. Деякі характеристики цих матеріалів наведені в табл. 3.1.
В якості наповнювача використовується карбонильное залізо Р-41 сорти ВТУ 1024-54. Співвідношення полістирол-ла і карбонільного заліза в залежності від марки ма-териала показано в табл. 3.2.
Деяке підвищення теплостійкості і механічної міцності об'ємних поглинаючих опорів досягнень-гается заміною полістирольної зв'язки на поліетилен низького тиску. Формостійкість при цьому возра-стає на 30-40 ° С.
Через відсутність розчинників для поліетилену при виготовленні його композиції з карбонільним залізом лакова технологія не застосовується. Вихідні ма-ли у вигляді дрібнодисперсних порошків змішуються в кульової млині (співвідношення ваги куль і ваги компонентів 2: 1 при заповненні барабана на 60-70%). Неможливість використання лакової технології отри-цательного позначається на властивостях поглинає ма-теріала- обволікання частинок карбонільного заліза
діелектриком менш рівномірно, ніж у матеріалів типу М. Тому питомий об'ємний електричний опору-тивление матеріалів, що використовують в якості зв'язки поліетилен, менше, ніж у матеріалів типу М.
Формоутворення поглинаючих опорів у обох матеріалів однаково і визначається Термоплен-стичної зв'язкою, т. Е. Пресування на ливарних машинах або пресах. Воно ведеться при температурі вихідної мас-си 180-230 ° С і тиску 480-800кГ / см2для поліеті-. льонів зв'язки і 800-1200кГ / см2для матеріалів ти-па М. Висока плинність поліетилену полегшує прессо-вання. В процесі виготовлення об'ємних поглинаючих навантажень з матеріалу типу М можуть виникати внутрен-ня напруги, які знижуються термообробкою - витримка при 60-80 ° С протягом 1-3ч.
Крім поліетилену і полістиролу в якості зв'язки використовуються різні термореактивні матеріали. Вони дозволяють отримати опору з більш високою механічною міцністю і теплостійкістю. Об'ємні поглинають навантаження з термореактивної зв'язкою изго-тавлівают пресуванням без підігріву для додання необхідної форми і наступною термообробкою для поліконденсації зв'язки. Вихідна прес-маса ізготав-ється по лакової технології або сухим змішуючи-ням компонентів у кульових млинах. Перед прессо-ням, яке ведеться при 18-20 ° С і питомому давши-лення 8-10т / см2, вона змочується для полегшення формоутворення. Після пресування об'ємна поглинутої-щающая навантаження нагрівається до 30-40 ° С для видалити-ня вологи і зняття внутрішніх напружень в ферромаг- нітних наповнювачі. Тривалість термообробки 18- 20чпрі примусової циркуляції повітря. Потім проводять термообробку для поліконденсації смоли при 120-130 ° С протягом 2-4ч.
При використанні в якості зв'язки епоксидних компаундів (ферроепоксід) компоненти вихідної мас-си змішують в вакуум-змішувачі. Їх завантаження ведуть при працюючій мішалці в такому порядку: смола, пла-стіфікатор, карбонильное залізо.
При введенні затверджувача треба дотримуватися темпера-турний режим, так як при "підвищенні температури відбувається сублімація 'ангідридів, а при зниженні - їх випадання з розчину. В обох випадках змінюється со-ставши компаунда. Після змішування компаунда з отвер- ник і отримання однорідної маси компаунд вто-річно вакуумируют при залишковому тиску 10-15мм рт. ст.в ті-чення 10-15мін.От-вержденіе компаундов виробляють негайно після заливки форм.
Крім карбонільного заліза в якості наповнювача для всіх розглянутих раніше випадків можна вико-ти та інші матеріали, наприклад графіт, азбест і т. Д. Технологічний процес виготовлення при цьому істотно не змінюється.
Формоутворення об'ємних поглинаючих опору-тивления з епоксидними компаундами в якості зв'язки можна здійснити не тільки в формах, але і безпосереднім-ного в волноводе, в порожнину якого встановлює-ся оправлення з легованої сталі (4X13), формуюча поглинає клин. Потім в хвилевід заливається когось Паунд. Після затвердіння оправлення витягується.
Цей процес формоутворення поглинаючих со-спротиву застосовується при виготовленні хвилеводних узгоджених навантажень гальванопластики. Корпус віл-новодной узгодженої навантаження «(рис. 3.5) отримують нарощуванням на зворотних формах. У задній стінці корпусу передбачають технологічні отвори. Після опресовування в порожнину хвилеводу вводиться оправлення для формування поглинає опору. В образу-вод шляхом шприцювання через технологічні отвори в задній стінці вводиться епоксидний компаунд з напол нітелей. Матеріал поглинає опору має хорошу адгезію зі стінками хвилеводу, тому до-виконавчими кріплення поглинає опору не потрібно.
Високу термостійкість мають об'ємні поглинаю-щие опору з кристалічного кремнію з кер-мической зв'язкою. Процес їх виготовлення наступний. Ультрафарфоровая керамічна маса розмелюють в кульової млині і просівається ^ ерез сито 900отв / см2.Так ж обробляється і кристалічний кремній. Вагове співвідношення порцелянових куль і про-ється матеріалу для кремнію і кераміки1: 1.Смешіваніе компонентів здійснюється в кульової мілину-ниці протягом 8-10ч.Перед пресуванням в суміш ке-Рамик і кремнію додають 5-7% води і суміш про-тирана 3-4 рази крізь сито 144отв / мм2для рівномірний-ного зволоження. З неї пресують брикети при тиску-ванні 150-200кг / см2.Для забезпечення рівномірного розподілу компонентів в суміші брикети дробляться і маса вдруге протирається крізь сито. З підготов-ленній суміші відпресовують заготовки поглинаючих навантажень при тиску 400кг / см2.Заготовкі сушать при 100-110 ° С протягом 10-16чі просочують парафії-ном, занурюючи в розплав на 2-5ч (в залежності від розмірів заготовки). Після просочення їх механічно обробляють і обпалюють в електричній печі по сле-дме режиму (табл. 3.3).
Час витримки при кожній температурі 1ч.Обо-печіння деталі шліфуються, промиваються і ретельно просушуються при 700-800 ° С.
Фіксовані поглинають атенюатори для віл-новодовізготовляются з об'ємним поглинає з-спротивом. Конструктивно вони представляють (рис. 3.6, а, бив) відрізок хвилеводної труби з флан-цями на кінцях. Всередині неї встановлено поглинає опір, для якого використовуються ті ж матеріали, що і для хвилеводних злагоди-сова навантажень. Технологи-ний процес виготовлення фіксованих поглинаючих аттенюаторов складається в сле-дме:
отримання корпусу фік-сірованного поглинає атенюатора;
отримання об'ємного по-глощающего опору;
установка поглощающе-го опору в канал віл-новода.
Об'ємні опору при установці в канал образу-вода приклеюються до стінок або кріпляться гвинтами. Перс-тивні формоутворення об'ємного поглинає з-спротиву непосредственновканале хвилеводу. Складна форма обох кінців поглинутої-щающую опору досягнень-гается формуванням поглинаю-ного опору з застосований-ням двох оправок. Спочатку в порожнину хвилеводу встановлюється перша оправлення, формуюча один кінець об'ємного волноводного опору-тивления. З протилежного боку заливається когось Паунд з наповнювачем (кількість заливається мате-ріалу строго дозується), після чого вводиться друга оправлення, формуюча інший кінець об'ємного хвилевід-ного опору.
Ця оправлення має канали для видалення повітря з порожнини між компаундом і оправкой в процесі фор-мований.