Екструзійно-раздувной агрегати. ці
Агрегати призначені для провадження у-лих полімерних виробів, які вико-ються в якості різних таропакувальних засобів (пляшки, банки, флакони, каністри, баки, бочки та ін.). Основними характеристи-ками, що відрізняють різні типи цього устаткування, є максимальні зна-ня обсягу порожнини формованих виробів і штучної продуктивності (табл. 7.3.2).
Принципове пристрій всіх екстру- Зіон-раздувной агрегатів ідентично (рис. 7.3.17). До їх складу, як правило, входять одне - черв'ячний екструдер 1, оснащений кільцевої екструзії головкою 4, яка призначені-чена для отримання трубчастої заготовки з розплаву полімерного матеріалу, і приймальний пристрій 2 з раздувной напівформах, змонтованими на його рухомих плитах 3, які призначені для прийому отримує-мій трубчастої заготовки та подальшого її роздування стисненим газом в порожнє виріб.
Принцип роботи екструзійно-роздувши - них агрегатів полягає у тому, що вихідне полімерну сировину у вигляді гранул або порошку захоплюється з бункера-накопичувача 5 вра-щающую черв'яком, а в міру просування в обігрівається циліндрі плавиться, пластикується - ється і продавлюється через формующий инст- румент - обігрівається кільцеву екструзії - онную головку 1 (рис. 7.3.18), виходячи з неї у вигляді трубчастої заготовки 2, потрапляючи потім у простір між роз'єднаними половина-ми охолоджувальної раздувной форми 4, смонті-рова на рухомих плитах прийм ого пристрою. По досягненню заготівлею ви-
Поділеній довжини проводиться змикання раз - дувних полуформ із захопленням заготовки та її роздування стисненим газом, що подається в по-лость заготовки через раздувной ніпель 3. Після охолодження здійснюється розмикання полуформ і з'їм готового полого вироби 5. Потім цикл формування виробу повторюється. При виробництві виробів малого обсягу ис-користуються многоручьевим екструзійні головки і багатогніздові раздувной форми [4].
Для формування великогабаритних виро-лій (каністр, баків, бочок та ін.) Використовуються екструзійно-раздувной агрегати, оснащені копільним пристроєм (акумулятором), розташованим між черв'яком екструдера і екструзійної головкою, в якому накопичуючи-ється розплав полімеру, що нагнітається неодмінно-ривно обертовим черв'яком екструдера за час, протягом якого відбувається роздування-ня і охолодження вироби у формі. Після на-копления необхідного обсягу розплав полі- міра під дією поршня копильника з великою швидкістю видавлюється з нього через екструзійну головку з утворенням трубчастої заготовки.
З метою зниження різнотовщинності формованих виробів, обумовленої гравітаційних-ної витяжкою одержуваних заготовок і їх неоднорідним деформацією при роздування-ванні, екструзійні головки часто постачають спеціальним пристроєм, що дозволяє в процесі екструзії цілеспрямовано змінювати розмір кільцевого зазору її формуючої щілини, що забезпечує бажане розподіл товщини стінки по довжині одержуваної екстра-Зіон заготовки. Для цього використовують коні-етичні дорни 2 і мундштуки / с щодо відповідності-ним зміщення їх в процесі екструзії заго-товки (рис. 7.3.19), забезпечуваним окремих-ним, як правило, гідравлічним приводом, керованим за заздалегідь заданою програмою.
Приймальні пристрої раздувной агрега-тов призначені для виконання дотримуюся-чих технологічних і допоміжних опе-рацій: переміщення раздувной полуформ до екструзійної голівці для прийому екструді- руемой заготовки; змикання та замикання раз-дувних полуформ; відрізання заготовки у екс-трузіонной головки; подачі стисненого газу для роздування заготовки; відведення раздувной напів-форм від екструзійної головки; охолодження вироби; розмикання полуформ і знімання гото-вого виробу.
За кількістю робочих позицій приймальні пристрої поділяються на одно-, дво - і мно-гопозіціонние. Одне - і двохпозиційні приймальні пристрої можуть бути оснащені спеціальними механізмами, осуществляющі-ми вертикальне, горизонтальне або складне кінематичне переміщення (підведення і відведення) раздувной полуформ щодо осі екстра - Зіон головки, що дозволяє забезпечувати безперервний процес отримання заготовок. Багатопозиційні приймальні пристрої ис-користуються в тих випадках, коли час отри-ня заготовки набагато менше часу її роздування і охолодження одержуваного виро-лія. Такі приймальні пристрої являють собою періодично або безперервно обертаю-щійся ротор 4, на якому змонтовано НЕ-скільки раздувной полуформ 3, забезпечених індивідуальним приводом для їх змикання - розмикання (рис. 7.3.20).
Екструзійно-раздувной агрегати, осна-щенние багатопозиційними прийомними уст-ройствамі, працюють безперервно, що забезпе-чує їх високу продуктивність. Неко-торие моделі таких агрегатів, що випускаються АТ КБАЛ ім. акад. Л. Н. Кошкіна, виробляють до 15-20 виробів в 1 хв при використанні однієї екструзійної головки. Крім того, багатопозиційні приймальні пристрої по-зволяют одночасно виготовляти вироби різної конфігурації, але тільки в тому слу-чаї, коли для їх формування може бути ис-користування мож один типорозмір екструзійної заготовки.
Важливою особливістю екструзійно - раздувной агрегатів є злагоджена робота черв'ячного екструдера і приймального пристрою, умовою якої є рівний-ство або кратність суми часу роздування, охолодження і знімання готового виробу зі вре-іменем отримання заготовки. Час роздування вироби
Де V0, Уф - обсяг порожнини відповідно
Заготовки і виробу, що формується; Pq, ри - • відповідно вихідне тиск газу в по-лости заготовки і тиск газу, що закінчується в порожнину роздувається заготовки; до - показу-тель адіабати газу, що подається в порожнину роздувається заготовки через раздувной НІП-пель.
Об'ємна витрата газу GH, що минає
У порожнину роздувається заготовки через роздування - ної ніпель [33],
Де | Ір - коефіцієнт витрати пневмокомму-
Нікаціонной системи, що забезпечує під-вод стисненого газу з ресивера в порожнину роздам-ваемой заготовки; S- площа прохідного перетину раздувной ніпеля; - від-
Повідно питома газова стала та тим-пература цього газу в ресивері.
Час, необхідний для охолодження через делия в раздувной формі [4, 45],
Рівномірність розігрівання заготовок забезпе-чується внаслідок їх обертання навколо осі симетрії в процесі поступального пере-міщення вздовж нагрівальних елементів /. Нагріті заготовки переміщаються в механізм роздування, оснащений раздувной охлаж-даємо напівформах 4. Формування заготовки в виріб 5 відбувається при подачі стисненого газу в порожнину останньої через раз - дувной ніпель 3. Після формоутворення
Вироби і його охолодження раздувной полуфор-ми розмикаються, а готовий виріб 5 сбраси-ється з раздувной ніпеля.
Як правило, раздувной механізм осна-щен багатогніздна раздувной формами [4], що забезпечує високу виробник-ність обладнання. Для підвищення ступеня двухосной орієнтації макромолекулярной структури матеріалу заготовки при її поділу-вання в виріб цей механізм часто оснащують спеціальним пристроєм, що забезпечує додаткову примусову витяжку роздувається заготовки в осьовому напрямку. Реалізація двухосной орієнтації матеріалу заготовки для деяких полімерів дозволяє підвищити його характеристики і знизити газопроникність формованих виро-лій.
При реалізації поєднаною технології використовуються инжекционно-раздувной агрега-ти, створювані на базі ливарних машин з попередньої черв'ячної пластикацией. З цією метою ливарні машини додатково оснащують пристроєм, що забезпечує раз - дувное формування виробів з одержуваних заготовок, які переміщуються на позицію роздування за допомогою спеціальних автомати-чеських пристроїв безпосередньо після їх інжекційного формування [4, 14]. Відмінність цього способу виробництва порожніх полімерних виробів від роздільної технології їх формо-вання полягає в тому, що отримується за допомогою на-гою литтєвий машини заготівля відливається на спеціальному підлогою осерді [14], оснащений-ном клапанним пристроєм, через яке потім виробляють подачу стисненого газу в по-лость відлитою заготовки, забезпечуючи її поділу-вання.
До переваг методу инжекционно - роздувне формування порожнистих виробів слід віднести високу ступінь механізації і авто-мотузці, а також високу виробник-ність обладнання. Лінії для роздувне формування порожнистих виробів з інжекційних заготовок, що випускаються фірмами Сидів ь (Франція), Крупп-Каутекс (Німеччина), позво-ляють виробляти від декількох сотень до декількох десятків тисяч виробів в 1 ч, що забезпечується за рахунок паралельного викорис тання декількох механізмів роздування, оснащених багатогніздна раздувной формами.
Штучна продуктивність обладнання д-ня, що забезпечує реалізацію інжекції - Онно-раздувной методу виробництва порожніх полімерних виробів, залежить від часу цик-ла їх формування. При використанні раз-слушною технології час циклу ливарного преформи
Де T0- час охолодження одержуваної пре-форми, що описується залежністю (7.3.10).
При використанні поєднаної техно-логії виробництва визначальним моментом є умова рівності часу циклів інжекційного формування заготовок і раз-дувного формування з них виробів. Послід-неї умова накладає цілком певні вимоги до вибору типорозміру литого обладнання, на базі якого проектуються инжекционно-раздувной агрегати.
Лінії для виробництва рукавних плівок. Велика кількість термопластичних полімерів переробляється в плівкові ма-теріали. Існують два різних методу їх отримання: рукавний роздувне формування і плоскощілинній. Найбільшого поширення в практиці переробки полімерів отримав рукавний метод. Він може бути реалізований за наступними технологічними схемами: верти-кально знизу - вгору або зверху - вниз і гори-зонтальним. Для реалізації рукавного методу виробництва полімерних плівок використовують плівкові лінії. Основними технічними характеристиками таких ліній є мак-симально розмір одержуваного плівкового рукава в його подвійному складання і діапазон товщини плівок, які можуть бути на них отримані.
Лінія для виробництва рукавних плівок за схемою знизу - вгору управляється за допомогою пульта управління 13 (рис. 7.3.23). Початкове полімерну сировину у вигляді гранул завантажується в бункер екструдера 77, звідки захоплюється його обертовим черв'яком і в міру продвиж-ня в обігрівається циліндрі преса плавиться, пластикується і продавлюється (Екструдуйте - ється) через формующий інструмент - обігр ваемого кільцеву екструзійну головку 9,
виходячи з неї у вигляді трубчастої заготовки. Як і останньої під дією стисненого повітря не-великого тиску, що подається через спеці-ально отвір в екструзійної голівці, роздувається в рукав, охолоджується подається через обдувочной кільце 8 повітрям, нагнися-Таєм в нього повітродувкою 12. Отриманий охолоджений плівковий рукав відбирається тягне пристроєм 4 , при цьому пристрій 5, встановлений на естакаді 6. складає його в полотно подвійного складання. Складене по-лотно через систему напрямних роликів 2 надходить на пристрій /, в якому намати-ється на бобіну. При необхідності подвійне полотно за допомогою пристрою 3 може разре-тися на одне або два одинарних. Для очищення одержуваного розплаву полімеру від можливих сторонніх включень використовується спеці-ний змінний фільтр 10, а для додання ус-тойчивости отримується рукаву - ограничи-кові «кошик» 7.
Недоліком реалізації такої техноло-ня схеми отримання рукавних плівок є те, що охолодження одержуваного ру-кава здійснюється за рахунок його обдування потоком повітря, що володіє відносно низькою теплоємністю. В результаті цього зона охолодження одержуваного плівкового рукава досягає значних розмірів (до неяк-ких метрів), що збільшує габаритні раз-заходи плівкових ліній і ускладнює їх об-слуговування. Цей недолік частково когось пенсирующие при отриманні рукавних плівок за схемою зверху - вниз », при цьому роздувається плівка додатково охолоджується водою.
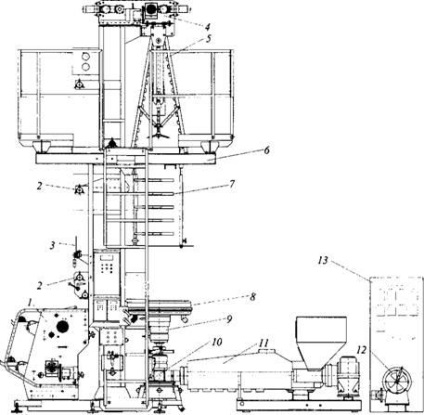
Мал. 7.3.23. Лінія для виробництва рукавних полімерних плівок за схемою знизу - вгору
Лінія для отримання плівок за схемою зверху - вниз управляється з пульта 7 (рис. 7.3.24). Трубчаста полімерна заготовка ви-давлівается екструдером 5 через кільцеву екструзійну головку 4 вертикально вниз і роздувається в плівковий рукав, який перед-ньо охолоджується потоком повітря через
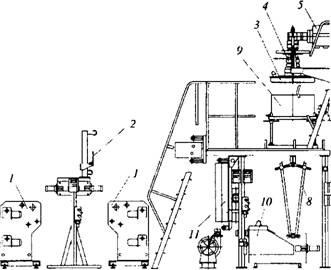
Мал. 7.3.25. тягнучий пристрій
Принципова відмінність намотувальних пристроїв з центральним приводом від намот-ків з периферійним приводом полягає в тому, що обертання штанг з встановленими на них бобінами безпосередньо забезпечується приводом. Це дозволяє підвищувати щільність намотування, що є важливим при виробництві стве плівок з жорстких полімерних ма-лов. У конструкції намотувальних пристроїв такого типу передбачається автоматичне регулювання кутової швидкості намотування в міру збільшення діаметра намотуваного ру-лона.
Основну розрахункову залежність, свя-викликають параметри одержуваної плівки з технологічними параметрами процесу її виробництва і конструктивними параметрами різних механізмів плівковою лінії, можна отримати з умови практично не-стисливості полімерних середовищ, яка в даний-ном випадку має вигляд:
Де / 2р - товщина одержуваного плівкового рукава; 5Ф - ширина формуючої щілини коли-цевой екструзійної головки, утвореної поверхнями її дорна і мундштука; ре,
Р0 - щільність розплаву полімеру відпо-венно, екструдіруемого через екструзійну головку, і охолодженого матеріалу в відбирали-мом тягне пристроєм плівковому рукаві: К1 'К2
Відповідно подовжню і поперечну деформації екструдіруемой трубчастої заго-товки при формоутворенні з неї плівковий-го рукава;
V3, V0- відповідно середнє інтегральне
Значення швидкості розплаву полімеру на вихо-де з екструзійної головки і лінійна ско-кість відбору плівкового рукава тягне уст-ройством; Dp, Оф - діаметр відповідно
Одержуваного рукава і середній діаметр фор-мующей щілини кільцевої екструзії го-спритні.
Середня інтегральна швидкість екструзії полімеру через кільцевої формующий капав головки, що входить в залежність (7.3.13). оп-ределяется з урахуванням об'ємної витрати рас-плаву полімеру Q наступним чином:
Лінійна швидкість відбору плівкового рукава тягне пристроєм
І радіус приводного валка тягне устройст-ва.