У сучасній практиці виробництва широкого спектру марок стали вакуумна обробка є невід'ємним інтегрованим ланкою технологічного процесу.
Здебільшого ці агрегати виведені з експлуатації і демонтовані. Після кризи 90-х років на українських заводах побудовані і введені в експлуатацію чотири вакууматора камерного типу VD / VOD (табл.1.7).
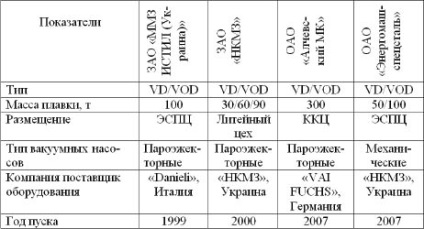
Вакуумирование стали в ковші (VD / VOD), є найбільш простим і надійним способом вакуумної обробки рідкого металу. Устаткування камерного вакууматора не контактує з рідкої сталлю, не вимагає спеціальних вогнетривів для футеровки камери, немає необхідності в попередньому підігріві вузлів установки, на них не впливає періодичність користування, що особливо важливо при відсутності поточного виробництва.
Вакуумної обробці піддають як неокислених, так і розкислення сталі. Для підвищення ефективності вакуумирования застосовують перемішування розплаву інертним газом через донні продувальні пробки сталеразливочного ковша, оскільки бульбашки аргону барботують розплав в значній мірі сприяють прискоренню ходу реакцій обезуглероживания і дегазації. Крім того, пневматична перемішування забезпечує посилення взаємодії високоосновного рафінувальні шлаку з металом, що сприяє десульфурації сталі і видалення азоту. Таким чином, кінцевий результат в камерному вакууматора досягається в ході однієї технологічної стадії.
Для досягнення необхідної межі вмісту водню в сталі (1,5-2,0 ppm), як правило, вибирають шлях вакуумирования раскисленной стали в сталерозливних ковші безпосередньо перед розливанням у злитки із застосуванням способів примусового перемішування для посилення масообміну між металом і газовою фазою.
Основна ідея технології вакуумної обробки сталі виходить з термодинамічної можливості зміщення рівноваги хімічних реакцій в бік виділення газоподібних продуктів в результаті зниження атмосферного тиску. Перш за все, це відноситься до розчиненого в стали водню, азоту, а також кисню. При цьому в результаті хімічної реакції з вуглецем кисень виділяється з розплаву у вигляді оксидів вуглецю, забезпечуючи поряд з раскислением обезуглероживание стали. Дана обставина представляє особливий інтерес при виробництві сталі з особливо низькою концентрацією вуглецю, а також високохромистих низьковуглецевих сплавів. В останньому випадку вакуумирование дозволяє уникнути надмірно високого перегріву розплаву, необхідного для досягнення низьких концентрацій вуглецю і зниження окислення хрому при атмосферному тиску. При виробництві сталі з особливо низькою концентрацією вуглецю розчиненого в розплаві кисню недостатньо для проведення глибокого зневуглецювання. Тому його вводять в метал під вакуумом через спеціальну кисневу фурму.
Газоподібні продукти реакції окислення вуглецю виділяються в глибинних шарах розплаву і полегшують екстракцію розчиненого в металі водню і азоту. Разом з тим, спосіб вакуумування неокислених і полураскісленной стали не гарантує отримання низького вмісту газів в готової продукції в силу ряду причин, одна з яких полягає в тому, що після закінчення вакуумної обробки, як правило, потрібне проведення операцій розкислення, легування і десульфурації. Таким чином, якщо головним завданням вакуумирования є видалення з металу водню і азоту, то, як правило, вакуумної обробці піддають глибоко розкислення сталь безпосередньо перед розливанням.
Для забезпечення достатньої площі поверхні розділу взаємодіючих фаз вакуумну обробку раскисленной стали поєднують з продувкою розплаву інертним газом. При цьому слід зазначити, що під вакуумом можна досягти принципово новий кількісний результат пневматичного перемішування металу інертним газом, так як величина потужності перемішування при зниженні тиску до практично досяжних у вакуумній камері значень збільшується в чотири-п'ять разів. Слід зазначити, що при атмосферному тиску така величина потужності перемішування практично недосяжна. Тому на установці ковшового вакуумування необхідно мати вільний борт сталеразливочного ковша висотою до 600 мм, а в окремих випадках - до 1000 мм внаслідок можливого підйому рівня розплаву в ході вакуумирования.
Ефективність десульфурації сталі істотно підвищується в результаті перемішування металу під рафінувальні шлаком в вакуумі, що дозволяє досягти концентрації сірки 0,003% і менше.
До складу камерної установки для вакуумування сталі в ковші (VD / VOD) входить: вакуумкамерах (частіше стаціонарна), накатну кришка, система дозування і подачі сипучих матеріалів, вакуумпровод, високопродуктивні вакуумні насоси і АСУ ТП (рис. 1.5).
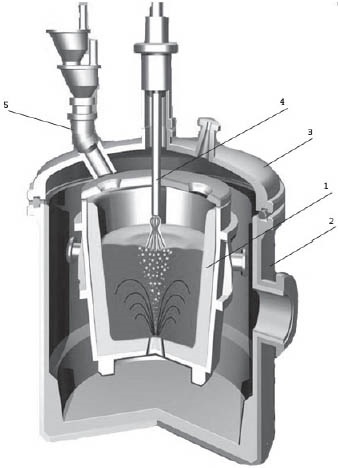
Малюнок 1.5 - Загальна схема камерного вакууматора VD / VOD: 1 - сталерозливних ківш; 2 - вакуумна камера; 3 кришка вакуумної камери; 4 - киснева фурма; 5 - пристрій для подачі сипучих під вакуум
У корпусі вакуумкамерах, яка футерована вогнетривкою цеглою, є стенд для розміщення сталеразливочного ковша. Корпус обладнаний отвором-мембраною з термодатчиком для аварійного зливу стали, з'єднувальним патрубок вакуумпровода, а також системою подачі азоту при розгерметизації. Верхній торець вакуумкамерах має ущільнювач для забезпечення надійної герметизації. На робочому майданчику вакууматора встановлюють трайб-апарат.
Кришка вакуумкамерах встановлена на транспортний візку і може вертикально переміщатися за допомогою гідроприводу. Кришка вакуумкамерах розміщує такі пристрої: захисний тепловий екран з елементами підведення і відведення охолоджуючої води, систему візуального контролю процесу вакуумної обробки, пристрій відбору проб та заміру температури, фурму для продувки стали киснем (VD / VOD), шлюзові пристрої для введення легуючих і добавок.
Для проведення обробки сталерозливних ківш з допомогою мостового крана поміщають в вакуумкамерах. Кришку вакууматора за допомогою візка транспортують до камери і встановлюють на ній. За допомогою вакуумних насосів створюють необхідне розрідження і проводять необхідні технологічні операції.
Для створення вакууму незалежно від типу вакууматора найбільшого поширення набули пароежекторниє вакуумні насоси, які не містять рухомих частин, тому їх робота дуже надійна, а термін служби практично не обмежений; їх виготовлення не вимагає дорогих матеріалів. Ними можна відкачувати гази, в тому числі агресивні і забруднені механічними домішками, без установки спеціальних фільтрів. Вони прості в управлінні і можуть працювати як від автономних парогенераторна установок, так і на відпрацьованому парі ТЕЦ і котелень. Маса насосів навіть найбільшої продуктивності відносно невелика, вони компактні, не вимагають потужних фундаментів. Окремі елементи насоса можуть бути закріплені на стінах і колонах будівлі цеху, тому зайнята ними корисна площа невелика. Часто для зниження експлуатаційних витрат систему пароежекторних насосів доповнюють двома-чотирма паралельно працюючими водокільцевими вакуумними насосами.
В умовах міні заводу, в деяких випадках, є вельми раціональним застосування механічних вакуумних насосів, так як для їх роботи не потрібно спорудження парогенератора, який, в свою чергу, є досить енергоємним агрегатом. Це дозволяє істотно знизити витрати по переділу вакуумированной стали. Разом з тим, система механічних насосів чутлива до пилу і температурі, що викликає необхідність піддавати очищенню і охолоджувати газ на виході з вакуумкамерах. Крім того механічні насоси вимагають організації обслуговування і ремонту.
Схема компонування вакуумних агрегатів в сталеплавильному цеху визначається перш за все обсягом і сортаментом вакууміруемой стали, хімічним складом рідкого напівпродукту, необхідністю виконання ряду інших технологічних операцій по маршруту позапічної обробки, а також можливістю розміщення того чи іншого типу обладнання. При цьому для забезпечення заданої продуктивності і зниження капітальних витрат можливі наступні варіанти компонування обладнання з однією системою вакуумних насосів:
- однокамерний вакууматор;
- двокамерний вакууматор з однією кришкою;
- двокамерний вакууматор з двома кришками.
З огляду на безперервно зростаючі вимоги до чистоти стали по неметалевих включень, змістом сірки і газів, а також однорідності великого злитка всі сучасні цехи оснащені вакуумної техникой- вакууматора і вакуумними камерами для розливання.