Обробка рідкої сталі під вакуумом поза печі має більш широкі можливості, ніж плавка в вакуумних печах, застосовані-травня для виплавки високолегованих сталей і сплавів і вимагає великих капітальних витрат. Вакуумна обробка при-Меним для різних, в тому числі і для пересічних (конструкційн-них, легованих) сталей, що виплавляються в будь-яких підприєм-ня агрегатах, і дозволяє одночасно дегазувати зна-ве кількості металу (до 250-350 т).
Основними способами вакуумної обробки сталей є наступні:
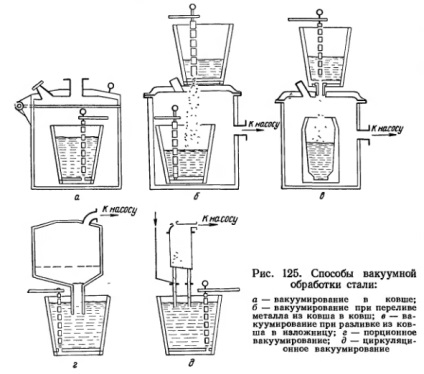
На кришці камери зазвичай є пристрій для введення в метал розкислюючих і легуючих добавок, вироблених після дегазації. Після закінчення вакуумування відкривають ка-міру, витягають ківш і розливають сталь звичайним способом на повітрі.
В результаті вакуумування сталі в ковші, так само як і при інших способах дегазації, досягається зниження содер-жания газів в металі - кисню, азоту та особливо водню; відповідно зменшується забрудненість стали оксидними Немі-металевими включеннями. Ступінь зниження вмісту газів в значній мірі визначається ступенем розкисленням металу.
Вакуумна обробка шарикопідшипникової стали ШХ15 до її розкислення кремнієм і алюмінієм дозволяє зменшити со-тримання кисню в металі на 40%, знизити кількість Немі-левих включень приблизно в два рази і знизити концен-трація водню на 50%.
Для підвищення інтенсивності перемішування металу, а сле-послідовно, поліпшення умов дегазації іноді поєднують вакуумну обробку з продувкою металу нейтральним газом (аргоном), що подається в ківш з металом через спеціальну футерованную трубу. Для цих же цілей застосовується електромагнітних-нітних перемішування металу в ковші.
Недоліком вакуумирования в ковші є обмежена тривалість обробки внаслідок досить значного охолодження металу і розливання вакуумированной стали на воз-дух, що призводить до повторного поглинання газів. Для підтрим-жания необхідного температурного режиму можливий дугового або індукційний підігрів металу в ковші. Для виключення повторного поглинання газів застосовують розливання вакуумованого металу в захисній атмосфері.
Дегазація струменя металу здійснюється при переливу його з ковша в ківш (рис. 125, б); в цьому способі створюються більш бла-гопріятние умови, ніж в попередньому, для видалення газів. Порожній ківш поміщають в камеру, в якій створюється розріджена-ня 133,32-399,96 н / м 2 (1-3 мм рт. Ст.). На кришці вакуумної камери встановлюють спеціальний проміжний ківш або воронку. Вакуумна камера закривається алюмінієвим листом, що є свого роду пробкою, розплавляють струменем рідкої сталі. Струмінь металу у вакуумі розпадається на краплі, що збіль-лічівает поверхню металу, покращує і прискорює процес дегазації. Для 40-т ковша вакуумирование цим способом зани-томить 8-10 хв.
Дегазація струменя металу під вакуумом відбувається також при розливанні його в виливниці (рис. 125, в), поміщені у вакуумну камеру.
В останньому випадку усувається недолік всіх інших спо-собів вакуумної обробки - розливання відбувається у вакуумі і метал не піддається впливу атмосфери повітря при напол-неніі виливниці. Розлив в вакуумі застосовується для відливання великих злитків масою 150-300 т.
Застосування вакуумної розливання для нержавіючої сталі, трансформаторної, конструкційної легованої сталі позво-ляет значно підвищити якість металу, призначеного для великих поковок.
При вакуумуванні окремих порцій металу (рис. 125, г) через опущену в розливний ківш футерованную трубу жид-кая сталь окремими порціями засмоктується в вакуумну камеру. Після короткочасної (30 сек) витримки в камері порція стали повертається в ківш. При цьому піднімається камера з трубою або опускається ківш. Труба весь час залишається зануреною в метал.
Вакуумована подібним способом сталь відрізнялася чисто-тій по неметалевих включень, хорошою оброблюваністю і підвищеною стійкістю проти корозії.
Переваги способу порційного вакуумування заклю-ються в наступному:
- представляється можливим обрабат-вать великі кількості металу (плавок до 270-360 т);
- не потрібні великі вакуумні камери та потужне вакуумне обо-нання;
- можливість нагріву металу у вакуумній камері в значній мірі усуває зниження його температури.
Недоліком способу є складність механічного обо-нання установки і розливання вакуумированной стали на воз-дух з повторним поглинанням металом газів.
При вакуумуванні циркуляційним способом - у відкритий ківш з рідким металом (рис. 125, д) занурюють дві футерован-ні труби, що примикають до нижньої частини вакуумної камери. Завдяки розрідженню, створюваному в вакуумній камері, і подається в нижню частину однієї з труб газу-носія (ар-гону), метал піднімається по цій трубі і надходить в камеру. Інжектіруемого аргоном струмінь металу при вході в камеру раз-бризгівается, метал піддається Дегазують впливів-ствию, стікає по похилому дну камери до другої трубі, і воз-обертається по ній в ківш. Швидкість циркуляції при ємності камери 1 т складає 5-20 т / хв. Витрата аргону близько 25 л / т сталі. Передбачено підігрів металу індуктором, встановленим на трубі, по якій метал повертається в ківш.
Циркуляційний метод відрізняється високою виробник-ністю. Йому властиві приблизно ті ж недоліки і переваж-вин, що і порционному вакуумированию.