При виборі заготовок (виливок, штампування, прокат, і ін.) Враховують форму, розміри і вага деталі, матеріал (який призначається виходячи з експлуатаційних умов), масштаб виробництва, періодичність повторення, розміри припусків на обробку і точність розмірів (допуски).
Від правильності вибору заготовки залежать трудомісткість і собівартість обробки; при виготовленні заготовки, максимально наближається за формою і розмірами до готової деталі, значна частина трудомісткості процесу доводиться на частку заготівельних цехів, а менша - на механообробні цехи і, навпаки, при виготовленні заготовок з великими припусками основна частка трудомісткості припадає на механообробні цеху.
Матеріал заготовок зазвичай задається на робочому кресленні конструктором. Вид заготовки, форму і розміри визначають, виходячи з умов найбільшої простоти і економічності обробки з урахуванням конкретних виробничих можливостей заготівельних цехів і термінів окупності капітальних витрат на підготовку виробництва.
Правильне рішення у виборі заготовок, якщо за технічними умовами застосовні різні їх види, можна отримати тільки на основі техніко-економічних розрахунків шляхом зіставлення технологічної собівартості деталі при тому чи іншому вигляді заготовки.
Однак деякими загальними міркуваннями можна керуватися при виборі заготовок. Так, наприклад, фасонні деталі, що не піддаються ударних навантажень і дії розтягування і вигину, доцільно виготовляти з чавунних виливків; фасонні деталі, які відчувають велику напругу, - зі сталевих виливків.
Заготовки у вигляді поковок, виготовлених куванням, і штамповок, виготовлених в штампах, застосовують для деталей, що працюють переважно на вигин, розтягнення і крутіння при значній різниці в поперечних перетинах.
Заготовки у вигляді поковок застосовують для великих деталей, а в одиничному і дрібносерійного виробництва - і для дрібних.
Заготовки у вигляді штамповок можуть застосовуватися в тому випадку, якщо за обсягом виробництва потрібна значна кількість їх, так як для їх виготовлення потрібні дорогі штампи, собівартість яких у цьому випадку розкладається на велику кількість заготовок.
У штампованої заготівлі структура металу більш однорідна, розміри найбільш близькі до остаточних, а в ряді випадків штампування використовуються і без подальшої механічної обробки або з дуже незначною, при цьому собівартість їх менше, ніж Коган # 558;
# 8; Однак оеревод жаготовкі з поковки на штампування вимагає економічного обґрунтування, наприклад шляхом визначення мінімального випуску штамповок, при якому буде виправданий цей переклад. Розрахунок мінімального випуску Вм в штуках здійснюється за формулою
де См - собівартість штампів, коп;
Див. П .. Див. П. - собівартість металу на поковки і штампування;
З м. К. - хвилинна зарплата коваля з нарахуванням, коп .;
Нк - коефіцієнт, що виражає частку загальних накладних витрат ковальського цеху, рівний 4 (без урахування амортизації, вартості штампів, палива і енергії);
Зс - хвилинна зарплата верстатника в механічному цеху, коп .;
Тп, Тих - трудомісткість поковки і штампування;
Пм - коефіцієнт, що виражає частку цехових накладних витрат механічного цеху, рівний 2;
Т1, Т2 - трудомісткість механічної обробки поковки і штампування, хв.
Заготовки з прокату застосовують для деталей, по конфігурації прібліжающіся до якого-небудь виду прокату (круглого, квадратного, шестигранного), ко-
гда немає значної різниці в перетинах і для отримання готової форми немає необхідності знімати великий шар металу.
Основним показником, що характеризує економічність обраного методу виготовлення заготовок, поряд з наведеними вище міркуваннями, є також коефіцієнт використання матеріалу, який визначається відношенням фактичної маси готової деталі q до чорної масі заготовки Q
-Технологічні вимоги, що пред'являються до заготовок, обумовлені необхідністю дотримуватися технічні умови, що визначають припуски, клас чистоти поверхонь, твердість і оброблюваність.
-Поверхня, використовувані при механічній обробці в якості опорних, повинні бути рівними і гладкими, без літників, прибутків, випоровши, ливарних або штампувальних ухилів і задирок.
Ці опорні поверхні повинні по можливості утворюватися моделлю і перебувати в одній опоке, щоб уникнути можливого впливу перекосу опок або стрижнів, на якість поверхонь.
Для взаємозв'язку оброблюваних поверхонь на кресленні заготовки позначають опорні поверхні механічної обробки, використовуючи їх в якості вихідних поверхонь при виготовленні і перевірці заготовок, а також при виготовленні моделей і штампів.
Дефекти заготовок виявляють при огляді чорних або попередньо оброблених поверхонь. Всі виявлені дефекти або відхилення від встановлених вимог (наявність формувальної землі, Пригара, раковин, заток, окалини, задирок, тріщин, нерівностей та ін.) Повинні бути усунені відповідними методами.
Основний дефект сортового прокату - це викривлення осі прутка або заготовки в результаті нерівномірності їх охолодження після виготовлення або дефект процесу виготовлення (прокатки, різання, механічної обробки) і транспортування.
Крім візуального виявлення дефектів у заготовок застосовують і інші види контролю в залежності від вимог, наведених в технічних умовах. Вони можуть бути з частковим або повним руйнуванням зразка з партії або без руйнування із застосуванням рентгено-та магнітної дефектоскопії, ультразвуку, гамма-променів радіоактивних речовин і ін. В ряді випадків виробляються механічні випробування і металографічні дослідження.
2.8. Попередня обробка заготовок
Виправлення. Щоб усунути викривлення заготовок, застосовують правку в гарячому або холодному станах молотом, на правильно-калібрувальних верстатах і правильно-ексцентрикових пресах, а також на гідравлічних і ручних гвинтових пресах.
У ряді випадків заготовки правлять не тільки перед механічною обробкою, але і в процесі обробки, коли при знятті зовнішніх шарів металу виникають внутрішні залишкові напруги, що викликають викривлення осі заготовки або її викривлення.
Листовий прокат будь-якої товщини правлять на правильних вальцях, в холодному стані або з місцевим підігрівом на плиті і тими ж способами безпосередньо в конструкції.
Рекомендоване обладнання для правки прокату в залежності від необхідної точності
Матеріал, що піддається виправленню
Точність на 1 м довжини, мм
Для чорних прутків 0,5-0,9; Для оброблених прутків 0,1-0,2
Правильно-калібрувальні верстати і ролико-правильні машини
Різка. Як правило, прокат надходить на виробництво у вигляді прутків або бухт, листового матеріалу або смуги. Тому перед запуском у виробництво прокат ріжуть і правлять.
Листовий або широкосмуговий матеріал ріжуть на так звані карти, розміри яких призначають стосовно розміри готових деталей. Оптимальний розкрій металу, тобто розкрій з найменшим відходом металу, передбачає розміщення на картах конфігурацій заготовок з мінімальними перемичками і з урахуванням способу подальшої їх обробки. На рис.2.17 наведені приклади розкрою металу для вирубки заготовок на пресах.
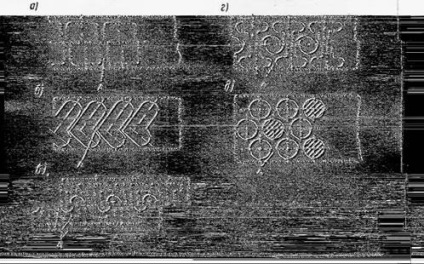
Щоб отримати більш чистий зріз вирубаної заготовки, а також зменшити задирки і викривлення заготовки, рекомендується вести вирубку з перемичками. Лише у випадках, коли до заготівлі не пред'являють підвищених вимог щодо точності і якості зрізу, застосовують вирубку без перемичок. Ширину перемичок зазвичай беруть яка дорівнює одній-двом толщинам вихідного металу. З огляду на, що ширина перемички впливає на величину відходу металу, її слід брати по можливості меншою (розміри перемичок нормалізовані).
Мал. 2.17 Розкрий металу з перемичками: а) прямий; б) похилого; в) зустрічній; г) комбіновано; д) многорядной; А - перемички
Відхід металу у відсотках визначають, як відношення площі поверхні висікання (відходи після вирубки) до площі поверхні карти.
Різання виробляють на обладнанні різних видів. Прессножніци застосовують для різання листового і смугової сталі товщиною до 25 мм. Гільотинні та дискові ножиці застосовують для різання матеріалу товщиною до 40 мм.
Тонкий прокат можна різати дисковими і вібраційними ножицями.
Для матеріалу товщиною від 5 до 100 мм застосовують газове різання: ацетилено-кисневу і кисневу. При товщині понад 100 мм (до 450 мм) застосовують киснево-флюсових різання.
Заготовки з матеріалів високої твердості ріжуть абразивним кругом, анодно-механічним або електроіскровим методом.
Існує також прогресивний метод різання високоміцних матеріалів фрикційними дисками, що працюють зі швидкістю обертання до 100 м / с. В результаті тертя опрацьований матеріал нагрівається в робочій зоні понад 1000 0 С і частково оплавляється, завдяки чому легко видаляється.
Прокат ріжуть також на пресах, приводних ножівках, на відрізних верстатах, оснащених дисковими і стрічковими пилками, відрізними різцями на токарних верстатах, а також дисковими фрезами на фрезерних верстатах.
Ширина різу залежить від способу різання і товщини металу. Так при різанні на токарному верстаті відрізним різцем металу товщиною 20 ... 30 мм ширина різу становить 3 мм, при різанні дисковою фрезою на фрезерному верстаті металу тієї ж товщини - 2 мм. При різанні металу тієї ж товщини ширина різу становить: дисковою пилкою - 4 мм; стрічковою пилкою - 1,5 мм; приводний ножівкою - 2,5 мм, абразивним кругом - 2 мм; анодно-механічним методом - 1,5 мм.
Центрування заготовок. При обробці зовнішніх поверхонь тіл обертання (валів) базою для виконання ряду операцій є центрові отвори. Вони призначаються не тільки для обточування, нарізування резьб, шліфування і т.п. але і для редагування і контролю. Правильна форма і розташування центрових отворів впливають на точність обробки. Тому від правильного центрування, відповідності кутів конуса центрових гнізд кутах конуса центрів верстатів, на яких будуть обробляти заготовки, залежить точність виготовлення деталей. Форму і розмір центрових отворів вибирають по ГОСТ 3725, які поділяються на три типи. Так, тип А має найбільшого поширення при обробці деталей в центрах, він має кут при вершині конуса 60 0 (іноді цей кут при обробці металоемкость деталей збільшують до 75, 90 0 і вище); тип Б має додаткову конічну поверхню (фаску) з кутом при вершині 120 0. яка призначається для запобігання центрових отворів від пошкоджень, а також для здійснення можливості підрізування торця; тип В крім запобіжної фаски забезпечений різьбленням, призначеної для різьбових пробок, угвинчується в центрові отвори при транспортуванні заготовок.
Центрування заготовок виробляють на токарних, револьверних і свердлильних верстатах, а також і на спеціальних одно- та двосторонніх Центрувально верстатах свердлом і зенковкой, що утворює конічну поверхню, або комбінованим інструментом, що об'єднує ці види обробки (свердління і зенкування).
Попередня обробка литих і кованих заготовок передбачає видалення окалини, задирок, пригару, літників, прибутків і напусків.
Очищення проводиться на копіювально-шліфувальних верстатах; великі заготовки обрубуються пневматичними зубилами і зачищаються переносними шліфувальними машинками. Очищення поверхонь роблять також дротяними обертовими щітками або в дробоструминних камерах.
Дрібні заготовки очищають здебільшого в очисних барабанах, що обертаються. Застосовується також спосіб очищення заготовок в струмені робочої рідини, що спрямовується під тиском на поверхню оброблюваної заготовки. Робоча рідина складається з кальцинованої соди, абразив і води.
Деякі види заготовок - поковки і штампування з високовуглецевих сталей (С> 0,5%), чавунні чи сталеві виливки - піддають також термічній обробці (відпалу або нормалізації) для поліпшення структури і оброблюваності.