Дугова сталеплавильна піч складається з металевого корпусу у вигляді кожуха, як правило, циліндричної форми з сферичним днищем (рис.1.6).
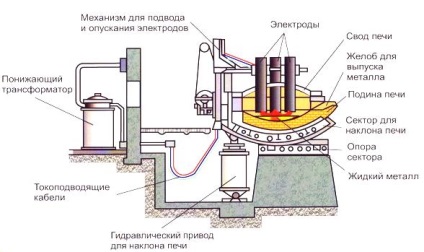
Малюнок 1.6 - трифазний електродугова піч
Зсередини кожух футерован високо матеріалами. Плавильний простір печі зверху перекривається знімним склепінням, вогнетривка кладка якого виконана в спеціальному сводовом кільці. У стінах печі є одне або два робочих вікна і один випускний отвір з жолобом для зливу металу і шлаку в ківш. Робочі вікна служать для завантаження шлакоутворюючих, руди, феросплавів і ряду технологічних операцій - спуску шлаку, взяття проб металу і шлаку.
Дугова піч спирається на два опорних сегмента - люльки, за допомогою яких піч може нахилятися в бік робочого вікна або випускного отвору. Нахил печі здійснюється за допомогою механізму нахилу з електричним або гідравлічним приводом. Шихта в плавильний простір опускається за допомогою спеціальної кошика із дном (бадді).
Застосовують графітові електроди, що виготовляються з малозольних вуглецевих матеріалів (нафтового, пекового і сланцевого коксу) і сполучних - кам'яновугільного пеку та смоли.
Технологія плавки в основній дуговій електропечі
Шихта при плавці з повним окисленням складається, головним чином, із сталевого брухту і чавуну, а також шлакообразующих (вапно, вапняк, плавиковий шпат, шамотний бій).
Плавка включає наступні основні періоди - заправка печі, завантаження шихти, плавлення, окислювальний період, відновлювальний період, випуск.
Заправка печі виконується для підтримки футерування плавильного простору в робочому стані.
Завалка шихти починається відразу після закінчення заправки. Завалку шихти здійснюють зверху за допомогою бадді.
Плавлення. Після закінчення завалювання звід з електродами встановлюють на піч, електроди опускають і включають струм. Під дією високої температури електричної дуги шихта плавиться спочатку під електродами, рідкий метал стікає вниз і накопичується в центральній частині подини. Поступово відбувається повне розплавлення шихти. У період плавлення відбувається утворення шлаку як за рахунок присадок вапна, так і за рахунок окислення елементів, що входять до складу шихти. За час плавлення повністю окислюється кремній, 50-60% марганцю, частково окислюються вуглець і залізо, окислюється фосфор.
Відновлювальний період плавки має на меті розкислення металу, видалення сірки, доведення хімічного складу стали до заданого, регулювання температури. Всі ці завдання вирішуються паралельно протягом усього відновного періоду. Після повного видалення окисного шлаку в піч сідаю шлакообразующие суміші разом з раскислителями, т. Е. Наводиться новий шлак (карбідний або білий). Як розкислювачі зазвичай використовують феромарганець, феросиліцій, алюміній. У пічсідаю також легуючі добавки для введення в метал необхідних легуючих елементів.
Після цього метал випускають з печі в установлений під жолобом сталерозливних ківш, для чого піч нахиляють в сторону сталевипускного отвори. При необхідності в ковші можна проводити додаткове розкислення і легування стали. Так здійснюється двушлаковий процес виплавки.
Технологія плавки в кислому дугової електропечі
Електродугової печі з кислою футеровкою зазвичай використовуються при виплавці сталі для фасонного лиття. Ємність їх складає від 0,5 до 6,0-10 т. Кисла футеровка більш термостійка і дозволяє експлуатувати піч з урахуванням умов перериваної роботи багатьох ливарних цехів машинобудівних заводів. Основним недоліком печей з кислою футеровкою є те, що під час плавки з металу не видаляються сірка і фосфор. Тому пред'являються високі вимоги до якості застосовуваної шихти за змістом цих домішок.
Процес плавлення шихти проводять так само як в основних печах. Для зниження чаду легуючих елементів, а також заліза, в ванну вводять шлак від попередньої плавки, а також кварцовий пісок і вапно. До кінця періоду плавлення в кислому залозистому шлаку міститься 40% FеО,> 45% SiO2.