Тому виплавка чавуну в електропечах зазвичай ведеться з використанням попереднього нагрівання шихтових матеріалів і частково відновленої металевої шихти. При використанні багатих руд і окатишів витрата електроенергії на плавку нагрітої і відновленої на 50% шихти знижується до 700 - 1300 кВт • год / т. При переробці бідних кремнеземистих руд він становить 1500 - 1800 кВт • год / т чавуну.
Прикладом підприємства, що використовує технологію виплавки чавуну в руднотермічеських електропечах, є Побузький феронікелевий комбінат (Кіровоградська область, Україна). Технологічна схема цього підприємства показана на малюнку 5.8.
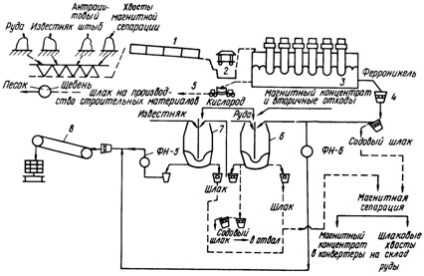
Малюнок 5.8 - Технологічна схема Побузького феронікелевого комбінату: 1 - трубчаста обертається піч; 2 - вагон-Кюбель; 3 - Руднотермічні електропіч; 4 - чавуновозних ківш; 5 - шлаковая чаша; 6 - кисневий конвертер з кислою футеровкою; 7 - кисневий конвертер з основною футеровкою; 8 - розливна машина.
До складу заводу входять: рудник з видобутком руди відкритим способом, склад руди, цех підготовки руди і випалу, плавильний цех, киснева станція, ремонтно-механічний і залізничний цех.
Після доставки з рудника руду зважують на автомобільних вагах і розвантажують на складі заводу. Кранами перевантажувачами з цієї руди формують три штабеля масою 40 - 50 тис. Т кожен. При цьому один штабель відпрацьовують, один формують і один знаходиться в запасі. На заводський склад надходить також використовується в якості відновника антрацитовий штиб, вапняк і залізна руда.
Після операції дроблення руду, відновник і флюси подають на шіхтарнік, звідки через систему ВАГОВИМІРЮВАЧ і дозаторів завантажують в трубчасті обертові печі з встановленими в них мазутними пальниками.
Для нагріву та відновлення шихти використовують трубчасті обертові печі з наступними характеристиками: довжина 70 м, діаметр 4,5 м, корисний об'єм 820 м 3. швидкість обертання 0,4 - 1,2 об / хв, кут нахилу 3 о. висота опорних кілець 1,15 м.
Печі футеровані цеглою марки ЦМ, товщина кладки 300 мм. Кожна піч має чотири пари опорних роликів, а також два контрольних (опорних). Встановлена потужність головного приводу 250 кВт.
Нижче представлена змінна режимна карта роботи однієї з трубчастих печей заводу:
Температура недогарка, К - 1100
суха руда - 100
Кількість пилу з електрофільтрів, т / зміна - 30
Температура газів, що відходять, К - 600
Гарячий недогарок з бункерів трубчастих печей футеровані вагонами-кюбеля транспортують на плавку в електропечі.
Електропечі Побузького феронікелевого комбінату за принципом роботи відносять до трифазних Руднотермічні печей прямої дії. Піч має зварений герметичний кожух овальної форми, закрита склепінням, через який проходять шість самоспекающіхся електродів, розташованих в лінію. Електропіч отримує харчування від трьох однофазних трансформаторів. Піч має три шлакові і три металеві льотки.
Нижче дана характеристика Руднотермічні електропечі Побузького феронікелевого комбінату:
Потужність, МВ • А - 48
Межі зміни вторинної напруги, В - 297 - 500
Діаметр електрода, м - 1,2
Відстань між осями електродів, м - 3,2
Робочий хід електродів, м - 1,2
Габаритні розміри, м:
Площа поду, м2 - 220
Загальний вигляд Руднотермічні електропечі Побузького феронікелевого комбінату представлений на малюнку 5.9. Для підвищення стійкості вуглеграфітової футерування поду піч експлуатується в гарніссажном режимі. Режимна карта змінної роботи промислової електропечі приведена нижче:
Витрата електроенергії на 1 т сухої руди, кВт • год - 780
Рівень металу в печі, м - 0,55
Температура металу, К - 1550
Перепуск електродів, м - 0,1
Рівень рідкої ванни, м - 2,2
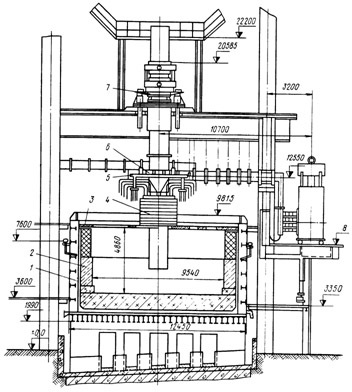
Малюнок 5.9 - Загальний вигляд промислової Руднотермічні печі Побузького феронікелевого комбінату: 1 - кожух печі; 2 - футеровка; 3 - звід; 4 - ущільнення електрода; 5 - гнучка підвіска; 6 - токоподвод; 7 - гідравлічний перепуск електродів
З Руднотермічні печі пріроднолегірованний чавун (електропічний ферроникель) складу,%: 2,0 - 2,5 C, 4 - 6 Si, 0,1 - 0,2 Mn, 4 - 5 Ni, 1,3 - 1,7 Cr, 0,1 - 0,25 S, 0,1 - 0,15 P при температурі 1230 - 1350о С періодично випускають в 40-т ковші, де проводять десульфурацию попередньо розплавленої кальцинованої содою. Після видалення ковшового шлаку метал зливають в 50-т кисневий конвертер з кислою футеровкою, де проводять знекремнювання до змісту кремнію 0,7 - 0,9%. Після цього метал при температурі 1450 - 1500о С переливають в кисневий конвертер з основною футеровкою, де проводять завершальний етап рафінування з використанням в якості охолоджувача вапняку.
Товарний ферроникель транспортують до розливних машин, де розливають в чушки масою 50 - 75 кг.