Основним заповнювачем керамзитобетонних блоків є власне керамзит. Його ж, в свою чергу, отримують з глини. Основна вимога до сировини для виробництва керамзиту - здатність до спучування при термообробці. В результаті випалення такої глини отримують натуральний пористий матеріал з закритими порами. На відміну від газобетону і пінобетону, в керамзиті немає хімічних піноутворювачів, які потім виділяються в процесі експлуатації будинку.
Глина - гірська порода, що складається з глинистих мінералів, і утворює в результаті вивітрювання скельних порід. Глини мають різноманітну забарвлення - сіру і білу (в більшості випадків), рідше зустрічаються червоні і інші кольори. Матеріал широко застосовується в будівництві, промисловості, в косметиці, в якості матеріалу для художніх робіт і для побутових потреб. Для виробництва керамзиту ми використовуємо так звану керамзитову глину.
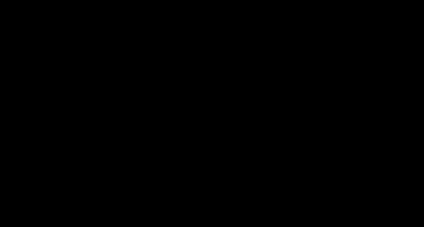
Глина має сірий колір.
Готові сирцовиє гранули подаються в спеціальні обертові печі, де і відбувається їх випал. Печі представляють собою металеві барабани діаметром кілька метрів і довжиною 40-75 метрів. Зсередини вони оброблені вогнетривким цеглою. Печі встановлені під нахилом 3%. Додатково відбувається опудривание гранул вапняної борошном для отримання захисної кірки на гранулах.
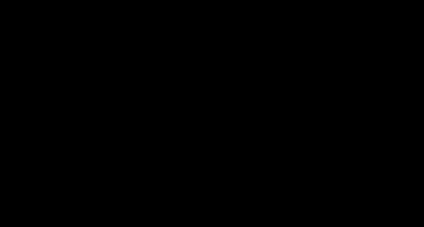
Випалювати глину відбувається тут
Щоб забезпечити правильну температуру спучування гранули, необхідно її попередньо висушити і підігріти. Тому печі працюють за принципом протитечії. Сировина подається в верхній кінець печі, а за рахунок її обертання навколо своєї осі, гранули повільно рухаються вниз. Назустріч їм іде потік гарячих газів, попередньо прогріваючи їх.
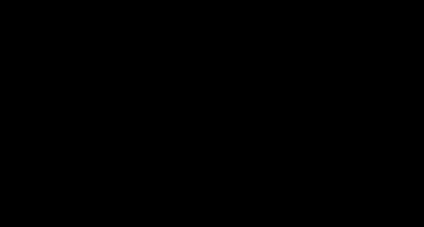
Газовий пальник печі
Залежно від розмірів, у керамзиту виділяють кілька фракцій. Зокрема, 5-10 мм, 10-20 мм і т.д. Кожна фракція може мати до 5% більших зерен і стільки ж дрібніших. Виходячи з розмірів і форми, керамзит підрозділяється на кілька видів:
Керамзитовий гравій. Має вигляд округлих частинок з порами всередині. Гравій, як правило, зовні має темно-бурий колір, і чорний на зламі. Розмір зерен - від 5 до 40 мм. Зазвичай використовується для заповнення при виготовленні легкобетонних конструкцій.
Керамзитовий щебінь. Відрізняється довільною формою, найчастіше незграбною. Його отримують дробленням шматків великого розміру спученої маси керамзиту. Розмір гранул може бути від 5 до 40 мм. Можна сказати, що щебінь - це подрібнений гравій. Його подрібнюють на щебінь для кращої сцепляемости, так як цементна паста з кулястими камінням зчіплюється набагато гірше, ніж з подрібненими.
Керамзитовий пісок. Має розміри гранули розміром 0,14-5 мм. Під час виробництва керамзитового маси утвориться деяка кількість відходів, які і мають вигляд піску. Також пісок отримують і методом дроблення.
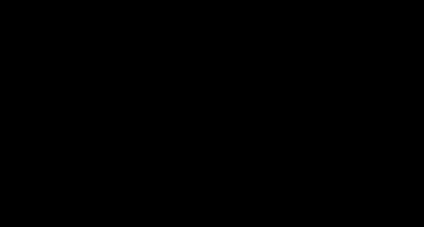
Дроблення для отримання керамзиту потрібної фракції
Коли основний заповнювач керамзитобетонних блоків готовий, можна приступати до їх формуванні.
Наступним етапом після видобутку сировини і отримання керамзиту є власне виготовлення керамзитобетонних блоків. Процес можна поділити на кілька етапів. Перший з них - приготування вихідної керамзитобетонний суміші.
Компонентами для виготовлення керамзитобетонних блоків служать цемент, пісок і вода. Основним наповнювачем є керамзит. У бетономішалку спочатку пускають керамзит з піском. Після перемішування цих компонентів пускають цемент. Коли суміш стає однорідною, порційно подають воду.
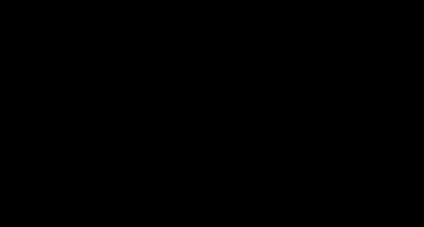
Готовність керамзитобетонний суміші визначає оператор бетонозмішувача. Суміш повинна бути напів-сухий і однорідною. На нашому виробництві до кожної виробничої лінії прикріплений досвідчений фахівець з суміші, який відповідає за візуальний контроль ступеня готовності. Ніякі автоматичні дозатори не впораються з цим завданням краще людини. Справа в тому, що ми використовуємо тільки річковий пісок, а він приїжджає на виробництво завжди з різною кількістю вологи. Тому за подачею води в змішувач стежимо особливо ретельно.
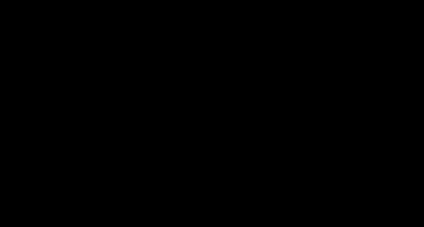
Відмінні характеристики продукції Чебоксарского Стройкомбіната досягаються завдяки використанню доброякісного сировини. Вихідна суміш для виготовлення керамзитобетонних блоків готується з чистої води, цементу М500 і дробленого керамзиту.
Вода забезпечує протікання хімічних процесів в керамзитобетону, в тому числі процес його затвердіння. Коли бетон починає тверднути його поверхня повинна бути вологою, за рахунок чого і забезпечується набір максимальної міцності. Домішки, кислоти і сульфати, які містяться в брудній воді, можуть перешкоджати гідратації цементу і руйнувати кристалічну структуру бетону. Тому вода неодмінно повинна бути чистою. Ми перевіряємо проби води в лабораторії кожні шість місяців.
Застосування цементу марки М500 забезпечує більш високі показники міцності в порівнянні з цементом М400. Також марка Д0 володіє більш високими показниками морозостійкості і вологостійкості. Цемент закуповуємо безпосередньо у заводу виробника, тому в виробництво він надходить завжди свіжий, з терміном виготовлення не більше трьох днів.
Використання дробленого керамзиту дозволяє домогтися кращої сцепляемости цементного розчину з заповнювачем і збільшити кількість керамзиту в блоці. Завдяки тому, що більш дрібні частинки заповнюють порожнечі між великими - блоки виходять на 30% міцніше.
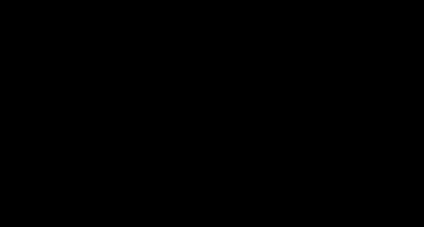
Формування керамзитобетонних блоків здійснюється на трьох вібропрессовальних лініях марки "Ріфей". Суміш подається в прес-форму, де піддається впливу вібрації і максимально ущільнюється. Вібрація дозволяє «прибрати» можливі порожнечі всередині суміші, тим самим підвищуючи щільність вироби. Одночасно з дією вібрації відбувається тиск зверху пуансоном за допомогою гідравліки.
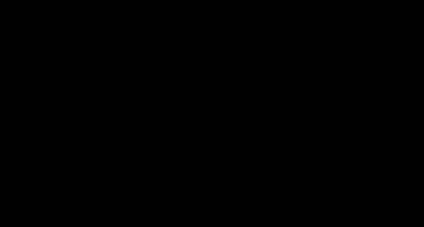
Метод вібропресування передбачає високий ступінь автоматизації і досить потужний:. Вироби, виготовлені на вібропресу, відрізняються високою міцністю і морозостійкістю.
До кожної вібропрессовальной лінії прикріплена досвідчена бригада працівників, яка відповідає за якість що випускаються блоків. У бригаді два ключових фахівця: майстер по формуванню і відповідальний за склад керамзитобетонний суміші. У нас в пріоритеті якість, а не кількість блоків.
Перед тим, як відправляти блоки клієнтам, вони ще повинні набрати міцність. А прискорити цей процес дозволяє пропарювання.
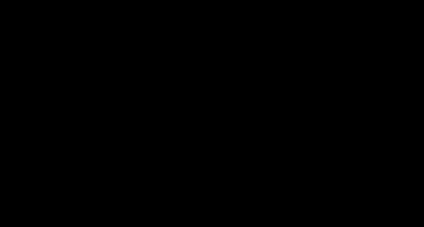
Після того як блоки відформовані, їм ще потрібно набрати свою міцність. Для цього вони будуть розміщені в пропарювальну камеру для теплової обробки. Тут готові вироби перебувають на протязі 10-20 годин при температурі 80-100 ° С. У звичайних умовах бетон набирає 100% своєї марочної міцності протягом 28 днів. А завдяки такій обробці паром, затвердіння бетону прискорюється в кілька разів і вже через добу блоки набирають половину своєї марочної міцності.
У нас використовуються два типи пропарювальних камер. Один вид - погружная камера, куди блоки завозяться навантажувачем на касетах. Вона служить для пропарювання важких керамзитобетонні блоки, в основному це повнотілі і потовщені.
І другий тип - пропарювальна камера зі стелажами, на які укладаються блоки на фанері. У цій камері пропарюють блоки до 15 кг: стандартні, перегородкові і двохпустотний.
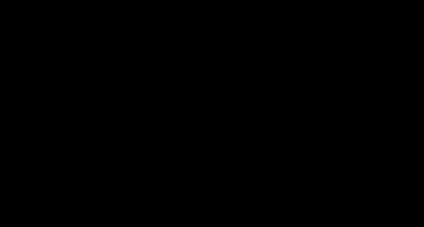
Пропарювання вважається найкращим способом обробки їх керамзитобетонних блоків. У камеру подається водонасищенний пар і, таким чином, тут створюється не тільки сприятлива температура, а й оптимальний рівень вологості. Вологість середовища необхідна, щоб зберегти вологу в керамзитобетону для його подальшого затвердіння.
Подачу пари в камери забезпечують два твердопаливних котлів-парогенераторів. Один основний робочий, інший резервний на випадок планового обслуговування.
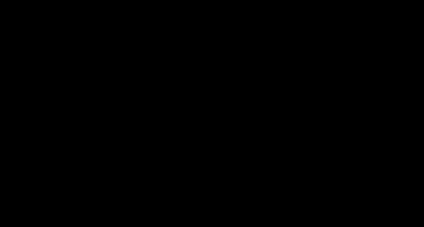