До цієї групи методів належать процеси, загальним для яких є те, що частинки порошкоподібних або гранульованих полімерів прогрівають до оплавлення або розм'якшення тільки поверхневого шару, в той час як їх серцевина зберігає вихідне фізичне (аморфне) або фазовий (кристалічна) стан.
спікання
Спіканням виробляють вироби з полімерів, температура плавлення яких перевищує температуру термодеструкції. Основним представником таких пластмас є фторопласти, а саме Ф-4 і Ф-4-НТД.
Вони поставляються у вигляді білого пухкого, жирного при розтиранні пальцями порошку з насипною щільністю 400-500 кг / м 3. При нагріванні фторопласт НЕ плавиться, в інтервалі температур 260-380 ° С він розм'якшується, а при 415 ° С починається його інтенсивне розкладання з освітою більш ніж шкідливих токсичних газоподібних продуктів, що представляють собою сполуки фтору (перфторизобутилен, фтористий водень та ін.). Фторопласт - кристалічний полімер. Його кристалличность може досягати 90%, але ступінь кристалічності залежить від режиму нагрівання-охолодження при температурі від 260 до 380 ° С.
Фторопласт характеризується набором вельми цінних властивостей, а саме: абсолютної хімічну стійкість, теплостійкість до 250 ° С, високими діелектричними показниками, високою антифрикційні (# 956; тр 15 МПа), швидка зношуваність при швидкостях декільком більше 0,3 м / с і важка засвоюваність в вироби.
Виготовлення виробів з Ф-4 і Ф-4-НТД включає наступні основні операції: холодне формування заготовок, спікання заготовок в вироби у вільному стані, охолодження виробів і при необхідності механічна обробка.
Формування заготовок виконується на гідравлічних пресах при питомому тиску в прес-формі 30-40 МПа. Збільшення тиску вище 40 МПа може привести до холодної витяжці і надалі - до появи тріщин у виробі. Завантаження в форму порошок повинен бути легкосипких. Оскільки фторопласт при зберіганні може комковаться, то перед використанням порошок рихлять, а в окремих випадках термостатируют при 240-250 ° С до 120 хвилин для видалення низькомолекулярних фракцій.
Порошок в формі розрівнюють для досягнення равноплотності по всьому об'єму заготовки. Тиск пуансона має розвиватися повільно і після досягнення максимального значення витримуватися протягом 2-3 хв. Кращі результати щодо равноплотності дає двостороннє пресування таблеток.
Щільність фторопласта в отформованной заготівлі повинна становити 1,83-1,85 т / м 3.
Спікання заготовок виконується в спеціальних печах з багатостороннім електричним нагріванням і повітряної циркуляцією, вирівнює температуру. Нагрівання ступінчастий, з витримкою при температурі 342 ° С (аморфізація кристалічної фази) і 360-380 ° С (розм'якшення всієї маси фторопласта і її «сплавом», що супроводжується проявом ефекту прозорості). Щільність спеченной заготовки повинна складати 2,2 т / м 3. супроводжує його усадка досягає 4-7%.
Тривалість спікання визначається з розрахунку приблизно 1 годину на 3 мм товщини виробу.
Охолодження заготовок, тобто освіту власне виробів з необхідним комплексом властивостей, - дуже відповідальна операція. Залежно від швидкості охолодження в виробі формується переважно аморфна або кристалічна структури, які визначають такі властивості, як еластичність, газонепроникність, твердість, жорсткість.
Кристалічна структура (ступінь кристалічності до 70%) формується при повільному охолодженні спечених виробів безпосередньо в остигає печі. Заготовки товщиною більше 100 мм для запобігання внутрішньої напруги слід охолоджувати повільно.
Механічна обробка (токарна, фрезерування, свердління і інші способи) спечених заготовок застосовується при виробництві плівок і виробів різної конфігурації. При роботі з фторопластом рекомендуються високі швидкості ріжучого інструменту при його малих подачах.
Фторопластові плівки отримують двома основними способами. Перший полягає в тому, що циліндричну заготовку обробляють за допомогою широкого токарного різця; отриману плоску стружку товщиною 15-1000 мкм розгортають між гарячими валками до зменшення її товщини до 5-7 мкм. Така плівка менш пориста, має підвищену подовжню міцність і поліпшені діелектричні характеристики (електрична міцність до 250 кВ / мм). Другий спосіб є безперервним. Його суть полягає в наступному: порошкоподібний полімер з вибропитателя подається на двухвалковий горизонтальний каландр і одноразово прокочується до товщини 10-50 мкм, а потім надходить в ванну з сольовим розплавом, що має температуру приблизно 380 ° С, де і відбувається процес рівномірного і швидкого спікання. Далі плівка проходить через тягнуть валки, надходить на валки розгортальні, потім у неї обрізають кромку і намотують в котушки і рулони.
Фторопластові труби, шланги, капіляри і профільні вироби отримують екструзійним методом, використовуючи поршневий або черв'ячний екструдер і головку з подовженим дорном. Для полегшення переробки в порошок фторопласта додають бензин або 6% -ний розчин поліізобутилену в бензині. Сипучість Ф-4 також можна поліпшити попередніми спеканием вихідного порошку з наступним його подрібненням або гранулювання.
Процес черв'ячної екструзії виробів з фторопласту полягає в наступному. Порошок або гранули полімеру надходять в не обігрівається матеріальний циліндр, захоплюються черевиками і транспортуються в головку (черв'як одно- або двухзаходная, з постійними кроком і глибиною нарізки). З огляду на низький коефіцієнт тертя фторопласту і відсутність нагріву або охолодження матеріалу, на внутрішній поверхні циліндра слід передбачити поздовжні канавки глибиною до 1-2 мм. Стиснення полімеру відбувається в голівці, конічний перехід якої до форми каналу становить близько 20 °.
Особливість формуючої головки складається в збільшеній довжині дорновой частини, що досягає 90D (D - діаметр вироби), а також в її терморегулювання. У початковій частині формуючого зазору фторопласт повинен спекаться при температурі 380 ° С, а в кінці - охолоджуватися до 250 ° С. Для центрування настільки довгого дорна використовують концентричну втулку, вільно посаджену на його кінець. При пуску екструдера утворюється виріб виштовхує цю втулку і далі трикулачні положення дорна.
Регулюючи ступінь стиснення порошку фторопласту і температуру по довжині дорна, можна отримувати вироби з різною щільністю і, відповідно, проникністю. Крім того, використовуючи проміжну кільцеву завантаження, вдається отримувати трубки і капіляри з різною пористістю по товщині стінки. Таким чином виробляють вироби з мембранним ефектом, необхідним в кардіохірургічному ендопротезуванні.
Екструзійним методом отримують ізольовані проводи та кабелі для екстремальних умов експлуатації (агресивність середовища, підвищені температури), ущільнювачі, труби, фітинги для потреб хімічної промисловості. Листовий фторопласт використовують для покриттів у вигляді циновок в спортивних спорудах (літні трампліни і лижні траси).
З композицій на основі фторопластов з різним наповнювачем (кокс, графіт, дисульфід молібдену, тальк) отримують антифрикційні, які не потребують змащення деталі підшипників ковзання й сепаратори для підшипників кочення.
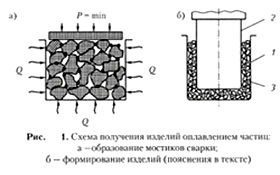
Для ПЕ використовують гранули розміром 0,1-0,4 мм з марок з показником плинності розплаву менше 2 г / 10 хв.
Один з найпростіших способів отримання виробів опалювальному полягає в тому, що полімер засипають у відкриту форму, закривають кришкою і поміщають в піч, де витримують до розплавлення шару, який контактує з формою. Після досягнення необхідної товщини цього шару форму витягують з печі, охолоджують, розкривають і висипають нерозплавлений гранулят. Потім форму з виробом знову поміщають в піч для оплавлення його внутрішньої поверхні.
Методом оплавлення отримують безшовні вироби у вигляді баків ємністю до 200 л, ванн, ящиків та коробок місткістю до 500 л, і навіть великогабаритні ємності до 5000 л.
Таким же способом отримують і пористі вироби медико-біологічного призначення. У цьому випадку використовують зернистий або дрібногранульований (бісер) порошковий термопласт, який ретельно стерилізують, після чого їм заповнюють підготовлені форми, піддають їх нагріванню з необхідною інтенсивністю подачі теплової енергії, потім охолоджують і витягають пористе виріб. Так в плоских дрібних формах отримують матеріал поропласт, який використовується в пластичної відновної хірургії (рис.2).
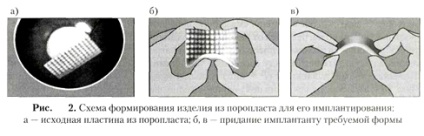
Після імплантації в організм пори матеріалу проростають живою тканиною. Імплантант необхідної форми хірург вирізає ножицями з заготовки, враховуючи особливості операційного поля. Матеріал імплантанта повинен забезпечувати можливість ручного деформування при температурі 60-80 ° С для надання йому необхідної конфігурації, з її збереженням при охолодженні (рис.2, б, в).
Нанесення полімерних покриттів на металеву поверхню також здійснюється методом оплавлення, а точніше розплавлення на матричної поверхні. Такі покриття отримують з термо- і реактопластів.
Основні технологічні операції процесу:
1) підготовка металевої поверхні (очищення, знежирення);
2) нанесення тонкого шару порошку полімеру на поверхню;
3) оплавлення полімеру;
4) охолодження (термопласти) або затвердіння (реактоп-ласти) покриття;
5) охолодження або додаткова термообробка вироби.
Застосовується чимало способів нанесення порошку на металеву поверхню, серед них найбільш поширеними є такі.
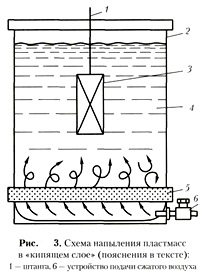
Нанесення в киплячому шарі порошку. Для цього використовується установка, схема якої приведена на рис.3. Порошок полімеру 4 завантажений в ємність 2, в яку знизу через фільтр 5 подається стиснене повітря. На виході з фільтра повітря турбулізуется і утворює псевдозріджених полімер-повітряну суміш, звану киплячим шаром. У киплячий шар поміщають на кілька секунд деталь 3, попередньо нагріту на 50-150 градусів вище температури плавлення полімерного матеріалу. Порошок, стикаючись з гарячою поверхнею деталі, оплавляється і утворює на ній покриття. Після вилучення деталь з покриттям з термопласту охолоджується, а з покриттям з реактопласту - направляється в термокамеру для затвердіння.
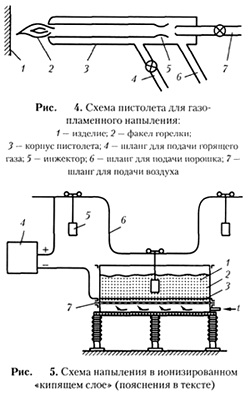
Спосіб простий аппаратурно і технологічно, але має ряд істотних недоліків. Серед них: неконтрольована товщина покриття; опливаніе розплавленого покриття по висоті вироби; разнотолщинность покриття на деталях складної конфігурації аж до його зникнення.
При газополуменеве напилювання струмінь порошку, що виходить зі спеціального пістолета (рис.4), проходить через полум'я пальника (ацетиленового), протягом часток секунди нагрівається до температури плавлення і утворює на поверхні холодного вироби суцільний шар. Товщина одержуваного покриття становить 0,1 -0,3 мм. При зовнішній простоті спосіб має низьку продуктивність; покриття різнотовщинності; в покритті утворюються внутрішні напруги, що призводять до його відшарування. Спосіб в основному застосовується в ремонтній практиці.
Значно більш якісні покриття отримують з використанням напилення в іонізованому киплячому шарі. Цей метод заснований на використанні електричних зарядів для осадження і утримування частинок порошку на поверхні холодного вироби. Установка (рис.5) складається з ванни 1 з електродом 3 у вигляді тонкого дроту, натягнутій над фільтром 7. Виріб 5 переміщається по ходовому шляху 6, підключеному до клеми (+) джерела струму 4, мінус (-) якого з'єднаний з електродом 3 . подачею стисненого повітря через фільтр в ємність з порошком полімеру створюють киплячий шар. При пропущенні через шар електричних зарядів частки порошку 2 отримують негативний заряд (через іони повітря) і осідають на позитивно зарядженому виробі. Товщина шару регулюється напруженістю електричного поля і швидкістю руху вироби, що визначає тривалість його перебування у ванні. Далі конвеєр 6 переміщує товар камеру для оплавлення і подальшого затвердіння (реактопласти) або охолодження (термопласти). Різновид цього методу - нанесення в електричному полі - універсальна і дозволяє наносити полімерні покриття на вироби будь-якої конфігурації і розмірів.
Редакція оплачує на договірній основі
технічні статті, маркетингові звіти, рецептури, огляди ринку
і іншу галузеву інформацію та права не її розміщення
Повне або часткове використання будь-яких матеріалів, розміщених на Plastinfo.ru,
в ЗМІ, друкованих виданнях, маркетингових звітах, дозволяється тільки за умови посилання
на «Plastinfo.ru» і в деяких випадках вимагає письмового дозволу ТОВ Пластінфо