Пластмаси в автомобільній промисловості - другий за значимістю конструкційний матеріал після металів. Технологія виробництва і переробки полімерів дозволяє все більше і більше замінювати металеві комплектуючі на пластикові. Поліаміди (ПА) - синтетичні термопластичні матеріали, найбільш затребувані в автомобільній промисловості серед інших полімерних представників. Вдале поєднання високої механічної міцності і малої щільності з хорошими антифрикційними і діелектричними властивостями, хімічною стійкістю до мастил та бензину, роблять поліамід одним з найважливіших конструкційних
1. Виробництво відповідальних деталей.
Завдяки одночасному володіння низьким коефіцієнтом тертя, міцністю, ударною в'язкістю, а також збереженню цих властивостей в широкому діапазоні температур, поліамід є незамінним при виготовленні відповідальних деталей таких, як:
- підшипники ковзання, що направляють і вкладиші вузлів тертя, що працюють при навантаженні до 20 МПа, при мастилі маслом, водою або всуху;
- шківів, блоків і роликів вантажопідйомних механізмів з тяговим зусиллям до 30 тонн;
- корпусів, кронштейнів, маточин коліс і інших деталей, до яких пред'являються підвищені вимоги по ударостійкості;
- шестерень, зірочок і черв'ячних коліс різних пристроїв і механізмів;
- деталей ущільнення і манжет для систем високого тиску.
Поліамідні (капронові) порошки використовують для отримання антифрикційних шарів підшипників ковзання. При цьому, чим тонше шар, тим краще він працює, так як в меншій мірі проявляється негативна дія низької теплопровідності капрону (в 200-400 разів менше, ніж у металів) і високого температурного коефіцієнта лінійного розширення (в 8-11 разів більше, ніж у металів).
Капрон, особливо в поєднанні з загартованої сталлю, має виняткову зносостійкість і практично виключає знос сполученої деталі. Капроновое покриття захищає метал від корозії і дії лугів, слабких кислот, бензину і ацетону. Однак через низьку температурної стійкості капрону температура в вузлі тертя з ним повинна бути в межах від -30 ° С до +80 ° С.
Великі можливості при виробництві конструкцій зі зниженою масою відкривають високонаповнені поліаміди, армовані скловолокном на 60%. Їх модуль пружності при розтягуванні в два рази більше, ніж у стандартного поліаміду (ПА-6), наповненого скловолокном на 30%. При цьому полімер має ті ж властивості плинності, що і стандартний поліамід. Матеріал знайшов застосування при виробництві зовнішніх дверних ручок, опори педалей і самих гальмівних педалей.
2. Виробництво великогабаритних деталей.
У Німеччині розроблена так звана «гібридна технологія» - технологія використання металопластикових композитів. Раніше вона застосовувалася тільки для виготовлення деталей обрамлення фар ближнього світла (Audi A8). Зараз же вона поширена на виробництво всієї передньої частини кузова. Гібрид алюмінію і поліаміду-6, на 30% армованого скловолокном, дозволяє знизити вагу вироби на 15% в порівнянні з тими випадками, коли використовуються сталеві листи.
Величезним потенціалом використання в якості альтернативи металу мають високонаповнені поліаміди при виробництві деталей, що знаходяться під капотом автомобіля. З них можна робити кришки головки блоку циліндрів, контейнери для трансмісійного масла, ємності для моторного масла, вхідні колектора, піддони картера двигуна.
3. Виробництво шин.
Волокно на основі однієї з похідних поліаміду-6 досить успішно використовується виробниками кордної тканини при випуску текстильного армуючого матеріалу для покришок пневматичних шин. Подібні шини мають найширший спектр застосування: легкові та вантажні автомобілі, комерційний і громадський транспорт, сільськогосподарські машини, а також шасі авіаційної техніки.
Кордна тканина з поліамідних ниток перевершує традиційну тканину за такими критеріями, як міцність, термостабілізірованность (збереження міцності при високих температурах) і деякими іншими показниками. Її застосування істотно збільшує вантажопідйомність, швидкість, надійність і безпеку техніки, при цьому маса шин знижується.
В силу своїх фізико-механічних якостей кордна тканину з поліаміду-6 служить набагато довше за звичайну, а тому дозволяє економити на витратах на комплектуючі, що і пояснює швидко зростаючу популярність щодо нового матеріалу в шинній галузі.
4. Вторинний ринок.
Поліамідну масу використовують при ремонті декоративних і конструкційних деталей автомобілів. Номенклатура вироблених деталей досить обширна, в їх числі хрестовини кардана, втулки ресор, шкворни поворотної цапфи, а також шестерні приводу спідометра, маслянки підшипника виключення зчеплення, рукоятки важеля перемикання передач, кнопки сигналу, зливні краники, і ін. Собівартість капронових деталей в кілька разів нижче в порівнянні з відпускною ціною металевих деталей, виготовлених в умовах масового виробництва.
Крім переваг, пов'язаних з фізико-хімічними властивостями поліамідних в готових виробах, важливе значення має економічний ефект, отриманий в технологічному процесі їх переробки. Використання поліамідів, крім зменшення вагових характеристик автомобіля, дозволяє домогтися чудової якості поверхні, а також, за рахунок зниження температури переробки, скоротити час виробничого циклу на 15-30%, що, в свою чергу, знижує собівартість вироби.
Лиття стеклонаполненного матеріалу проводиться при тиску на 40% нижче тиску, необхідного при виробництві стандартних марок поліаміду-6. Це сприяє зниженню зносу прес-форм і скорочення витрат на їх технічне обслуговування та ремонт. Крім того, з'являється можливість робити більш тонкі стінки і точніше відтворювати складні геометричні конструкції. При цьому потрібна менша кількість точок уприскування, що дозволяє досягти єдиного напрямку скловолокна і знизити таким чином усадку і деформацію. Додаткова економія забезпечується більш низькою температурою лиття (споживання енергії, цикл обробки).
Всього за 10 років споживання пластиків у виробництві автокомпонентів збільшилася більш ніж в 2 рази. Якщо на початку століття полімерні деталі становили 5-7% від ваги автомобіля, то зараз їх частка вже перевищила 15%, і цей процес буде розвиватися далі. Основними факторами, які зумовлюють значне впровадження пластмас в конструкцію автомобілів, є;
1. Зниження ваги автомобіля, а отже і зниження витрати палива і обсягу шкідливих викидів в атмосферу.
2. Легкість переробки, що розширює можливість для нових конструкційних рішень і, отже, дозволяє втілювати всілякі дизайнерські ідеї. Завдяки цьому можна отримувати деталі самих хитромудрих форм і кольорів без додаткових операцій по механічній обробці і фарбуванні.
3. Скорочення енерго- і трудовитрат в процесі виробництва, можливість відмови від дорогих кольорових металів і нержавіючих сталей і, як підсумок, зниження вартості автомобіля.
4. Підвищення довговічності і експлуатаційних характеристик автомобіля.
Деталі з поліаміду витримують навантаження, близькі до навантажень, допустимим для кольорових металів і сплавів. Антифрикційні властивості ПА, особливо наповнених, значно перевершують фторопласти, полиформальдегид і полікарбонат (табл. 1).
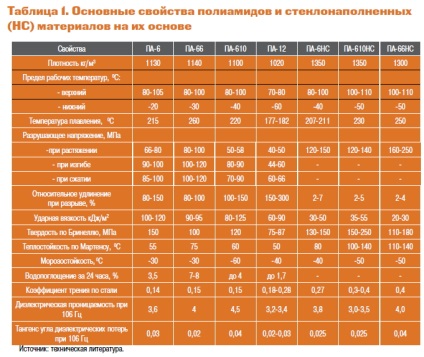
Для виготовлення автомобільних деталей знайшли застосування наступні поліаміди і їх склонаповнені модифікації - ПА-6, ПА-66, ПА-610, ПА-12, склонаповнені поліаміди, ПА-11.
ПА-6 найдешевший матеріал з поліамідів. За механічними властивостями він перевершує інші поліаміди, має хороші антифрикційні властивості.
В автомобілебудуванні застосовується для виготовлення корпусу розподільника нагрітого повітря, опори кульової тяги приводу управління коробки передачі, пластини опори педалі акселератора, повідця тяги виключення замку дверей, втулок валика педалі зчеплення, валика акселератора, ізолюючої втулки важеля покажчика та ін. Втулок, пробки горловини бачків, штуцерів, шайб.
Як приклад на малюнку 1 представлена ефективність використання ПА-6 в порівнянні з бронзою.
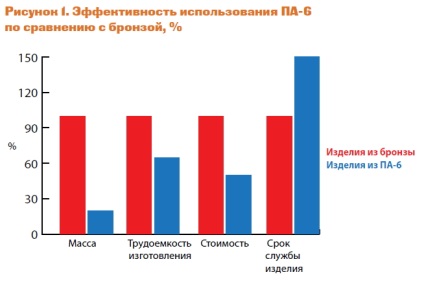
ПА-66 відрізняється найбільш високими властивостями міцності, високу твердість, деформационной стабільністю, підвищеною теплостійкістю.
В автомобілебудуванні з ПА-66 випускаються автомобільні деталі типу вкладишів і сепараторів підшипників, вентиляторів системи охолодження, шестерень корпусу приводу спідометра, втулок педалей зчеплення і гальма, розпірних втулок, втулок дуги оббивки даху, обмежувальних втулок, гайок-баранчиків кріплення запасного колеса, шайб, контактних колодок для зовнішніх і внутрішніх штекерів, каркасів котушок, пістонів кріплення, вкладишів кульового кільця, скоб тощо.
ПА-610 за значенням показника плинності розплаву і модуля пружності перевершує практично всі термопласти. Поєднання невеликого водопоглинання з хорошими властивостями міцності і тепломорозостойкостью уможливлює використання ПА-610 в відповідальних деталях антифрикційного призначення.
З ПА-610 виготовляють методом лиття під тиском вкладиші і важелі управління коробкою передач, вкладиші і втулки опорних тяг рульової трапеції, фільтр паливного насоса, ручки фіксаторів шарніра, зубчасті передачі, ущільнювальні пристрої, муфти, підшипники ковзання, лопаті гвинтів, а також антифрикційні покриття металів.
Використання обмежене його високою вартістю.
ПА-12 має невелику щільність, відрізняється від інших поліамідів підвищеної водо- і морозостійкістю, що дає можливість експлуатувати вироби з нього в середовищах змінної і високої вологості. Властивості і розміри виробів з нього відрізняються стабільністю. ПА-12 найеластичніший з розглянутих поліамідів, добре працює на знакоперменний вигин, має хороші антифрикційні і діелектричні властивості. До недоліків матеріалу відносяться низька теплостійкість у порівнянні з іншими поліамідами.
Застосовується для виготовлення трубок, хомутів, скоб, засувок замків, мов замку дверей, ізоляції електричних проводів, перемикачів, мікроконтактів, релейних деталей, трамблеров, трубопроводів для подачі пального.
Склонаповнені поліаміди містять 20-30% скловолокна. Їх механічна міцність і теплостійкість збільшується по порівняння з ненаполненного в 2-3 рази. Значно зростає опір повзучості, втомна міцність, зносостійкість.
В автомобілебудуванні склонаповнені ПА використовують для виготовлення деталей з жорсткими розмірними допусками, які працюють в інтервалі температур від -60 ° С до 150 ° С, а також деталей, несучих навантаження. Склонаповнені поліаміди мають невелику щільність, високою міцністю, високою міцністю до ударних навантажень, хорошою масло і бензостойкость, низьким коефіцієнтом тертя і непоганими діелектричними показниками. Найбільшого поширення вони отримали при виробництві таких деталей, як обмежувачі ходу шестірні, важелі включення приводу, крильчатки, шестерні, корпусу запобіжників, корпус клапана бензобака і карбюратора, кришки картера зчеплення, бачки радіатора опалювача, чашка шарніра зовнішнього дзеркала, деталі паливної апаратури, різні втулки .
У Росії досить багато підприємств, що випускають поліамід, однак для автомобільних деталей потрібні спеціальні модифіковані ливарні марки, виробництво яких у нас або відсутня, або припинилося, або випускається в обмежених обсягах.
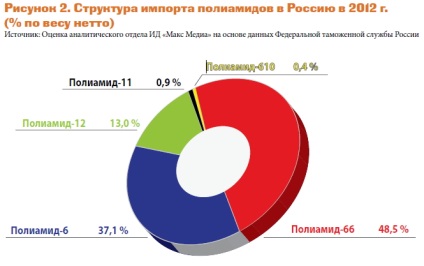
Імпортований поліамід, головним чином, призначений для виготовлення автомобільних деталей методом лиття під тиском (основні постачальники - компанії Dupon, Basf), для лиття деталей поділених вузлів зчеплення і гальма (Delphi, Nilit Plastics Europe), для виробництва корпусу двигуна автомобіля і виробництва сепаратора підшипника (A. Schulmann), для трубопроводів приводу автотранспортних засобів (Arkema), а також інших виробів.
При виборі матеріалу для знову освоюваних деталей автомобіля в переважній більшості випадків оптимальне рішення здійснюється виходячи з наявного промислового марочного асортименту поліамідів. Нижче наводиться консолідовану думку фахівців - конструкторів-автовиробників і хіміків, сформульоване в якості основних вимог, що пред'являються до деталей з поліамідів:
- підвищена плинність розплаву марок поліамідів, що застосовуються для лиття великогабаритних і тонкостінних деталей;
- мінімальне термокоробленіе матеріалу у виробі для відповідності заданої геометрії;
- відсутність зовнішніх технологічних дефектів типу «тигрова шкура», розлучень і плям;
- забезпечення при необхідності адгезії до зовнішніх покриттів (забарвлення, металізація);
- допустимі довготривалі і короткочасні робочі температури;
- допустимий рівень ударної в'язкості без надрізу і з надрізом;
- допустимий рівень ударної в'язкості при мінімальній робочій температурі;
- допустимі рівні модуля жорсткості при максимальній робочій температурі;
- недопущення повзучості під навантаженням при максимальній робочій температурі;
- здатність матеріалу до зварювання в єдину деталь з окремих частин;
- відповідність усадки (з урахуванням напрямку) і її заданого значення в литтєвий формі;
- забезпечення здатності матеріалу до рециклінгу після виходу виробів з експлуатації;
- мінімізація термічної і термоокислительной деструкції матеріалу при переробці;
- допустимий рівень опору дряпання з оцінкою по конкретній методиці;
- відсутність помітної міграції низькомолекулярних інгредієнтів до поверхні;
- мінімізація емісії летких речовин, недопущення в них і в матеріалі особливо шкідливих компонентів;
- мінімізація рівня запаху при литті і на свіжовиготовлених деталях;
- виключення «фоггінга», т. е. відкладень на лобовому склі низькомолекулярних продуктів;
- мінімізація швидкості светотеплового старіння по конкретним прискореним методикам;
- стійкість до впливу наявних робочих середовищ і до миючих засобів;
- стійкість до дорожніх солей, в тому числі до соляного туману (наприклад, CaCl2);
- глянцевость або матовість поверхні в залежності від естетичних вимог;
- однорідний колір, його відповідність координатам кольоровості і світлини;
- термостійкість кольору в умовах переробки матеріалу і його стійкість при експлуатації.
Автомобільну промисловість можна вважати справжнім полігоном для випробування і впровадження полімерних матеріалів. Прийде час, коли автомобіль, виготовлений повністю з полімерних матеріалів, перестане бути екзотикою.