Черв'ячні колеса виготовляють цільними і складовими. Вінці складових черв'ячних коліс відливають з чавуну (для тихохідних передач) і фосфористої бронзи (для швидкохідних передач). Черв'як-гвинт має спеціальну, зазвичай трапецеидальную різьблення. При невеликих діаметрах черв'яка його різьблення нарізають на валу, а при великих діаметрах - на втулці, яку насаджують на вал. Черв'яки закріплюють на ведучому валу, а черв'ячні колеса - на відомому.
Черв'ячні передачі в сучасному машинобудуванні мають широке поширення. Найбільше застосування черв'ячні передачі знайшли у металорізальних верстатах, автомобілях, тракторах і т. Д. Значна перевага черв'ячних передач полягає також в плавності й безшумної їх роботи.
Недоліком черв'ячних передач є низький коефіцієнт корисної дії.
Збірка черв'ячних передач починається із збірки черв'ячного колеса. Вінець напресовують на маточину під пресом в холодному або попередньо нагрітій (до 120-150 ° C) стані. Потім засверливают отвори, нарізують різьблення під стопори і вкручують стопори з подальшим їх раскерніваніем. Після цього черв'ячне зубчасте колесо перевіряють на биття. Установка черв'ячних зубчастих коліс на валах і перевірка їх виробляються так само, як і при складанні звичайних циліндричних зубчастих коліс.
Істотним при складанні черв'ячних передач є забезпечення правильного зачеплення черв'яка з зубами колеса. Для цього необхідно, щоб кут схрещування осей черв'яка і зубчастого колеса і міжцентрову відстань А (рис. 15.5, б) відповідали кресленням, середня площина збігалася з віссю черв'яка, а бічний зазор в зачепленні відповідав технічним вимогам. Перед установкою черв'яка і колеса часто необхідно перевірити стан осей отворів в корпусі.
3. Здійснити збірку кулисного механізму.
Кулісний механізм є різновидом кривошипно-шатунного механізму. Він застосовується в тих випадках, коли потрібно перетворити обертальний рух в зворотно-поступальний, наприклад, в поперечно-стругальних, довбальних верстатах і інших машинах. Лаштунки можуть бути коливаються (в стругальних верстатах) і обертаються (в довбальних верстатах).
Основною деталлю кулисного механізму є куліса 1 (рис. 16.5), що сидить на осі 12 і коливається щодо неї. Ззаду лаштунки насаджений кривошипний диск 4, що має радіальний паз, в якому може переміщатися палець кривошипа 2 за допомогою гвинта 3, приводиться в рух валиком 5 через конічні зубчасті колеса 13 і 14. Диск 4 своїм хвостовиком сидить в стінці станини 9 і приводиться в обертання зубчастим колесом 10 від приводу верстата.
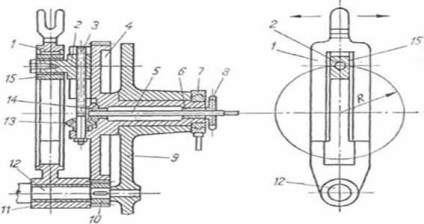
Мал. 16.5. Механізм що хитається лаштунки поперечно-стругального верстата
На пальці 2 насаджений камінь (сухар) 15, який входить в подовжній паз куліси. При обертанні кривошипного диска камінь змушує кулісу гойдатися біля своєї осі, а сам переміщається уздовж паза куліси. Верхній палець лаштунки вільно з'єднується з повзуном верстата і змушує його рухатися поступально по горизонтальних напрямних. Перевагою кулисного механізму є велика швидкість зворотного ходу повзуна. Це особливо важливо в верстатах, де зворотний хід є холостим. Але, з іншого боку, кулісні механізм може передавати значно менші зусилля, ніж кривошипно-шатунний.
Деталі кулисного механізму, т. Е. Кулісу, кривошипний диск і камінь, роблять з чавунного лиття. Пальці, валики, осі, зубчасті колеса виготовляють зі сталі. Кривошипний диск одночасно виконує роль маховика.
Збірку кулисного механізму зазвичай починають з з'єднання кривошипного диска 4 з вкладишем 6, через який пропускають валик 5 (рис. 16.5). На кінець валика на шпонке встановлюють конічне зубчасте колесо 14. Гвинт 3 ввинчивают в отвір пальця кривошипа 2, а на іншому кінці гвинта, де немає різьблення, в шпонкові гніздо встановлюють шпонку. Потім конічне зубчасте колесо 13 зчіплюють з зубчастим колесом 14 і монтують в отвір уступу. Коли палець 2 увійде в паз кривошипного диска, гвинт 3 закріплюють гайкою. Після цього весь зібраний вузол хвостовиком диска 4 вставляють в отвір станини 9. Потім на вісь куліси 12 надягають втулку 11, а на неї встановлюють кулісу 1. Далі на вісь 12 на шпонке встановлюють зубчасте колесо 10. В поздовжній паз куліси вводять камінь 15 і весь зібраний вузол з'єднують з кривошипним диском. При цьому вісь 12 повинна увійти у відповідний отвір станини, а головка лаштунки - в паз повзуна. Після цього палець 2 вводять в отвір каменю 15 і закріплюють гвинтом. На кінець хвостовика кривошипного диска надягають ексцентрик механізму подачі 7, на різьбу валика 5 нагвинчують стопорну гайку 8 (рис. 16.5).
Далі регулюють механізм зміни довжини ходу повзуна. Це регулювання здійснюється за рахунок зміни радіуса R кривошипного пальця (ексцентриситету). При обертанні валика 5 рукояткою, яка одягається поверх його квадратний кінець, через конічні зубчасті колеса 13 і 14 гвинт 3 переміщує палець 2 уздовж кривошипного диска і змінює ексцентриситет. Найбільша довжина ходу буде при найбільшому ексцентриситеті.
В правильно зібраному і встановленому верстаті напрямні куліси повинні знаходитися в площині, перпендикулярній осі 12. Ця вісь повинна займати горизонтальне положення, а напрямні куліси - лежати в вертикальній площині. Їх перпендикулярність перевіряють рамним рівнем. Крім того, індикатором перевіряють перпендикулярність торця кривошипного диска 4 до осі 12.
1. Розповісти чим відрізняється вузловий і поузловой методи ремонту?
Вузловий метод ремонту полягає в тому, що потребують ремонту складальні одиниці (вузли) устаткування знімають з машини і замінюють запасними (новими або відремонтованими). Даний метод найбільш ефективний на підприємствах зі значною кількістю однотипного обладнання, а також в умовах поточно-масового виробництва.
Метод має такі переваги:
різко скорочуються простої устаткування в ремонті, час якого в цьому випадку витрачається на зняття вузла з машини і установку запасного, що дозволяє зберегти режим виробничого циклу; з'являється можливість централізованого ремонту вузлів на спеціалізованих робочих місцях, оснащених необхідними (в тому числі спеціальними) інструментами і пристосуваннями; зростає економічна доцільність механізації ремонтних робіт; повніше використовуються потужності ремонтно-механічного цеху; виникає можливість спеціалізації робочих по виконанню певних робіт; підвищується якість ремонту і знижується його собівартість.
Порядок виконання робіт при вузловому методі ремонту наступний:
1) технічна діагностика всіх вузлів машини з метою виявлення несправностей;
2) демонтаж вузлів, що вимагають ремонту;
3) отримання зі складу та установка запасного вузла;
4) випробування встановлених вузлів, а також механізмів, до складу яких вони входять;
5) транспортування знятого вузла в ремонтний цех (завод);
6) розбирання, очищення і дефектация деталей вузла;
7) отримання зі складу необхідних запасних деталей і матеріалів;
8) відновлення зношених деталей;
9) складання ремонтується вузла;
10) обкатка і випробування відремонтованого вузла;
11) нанесення антикорозійних і консервують покриттів;
12) здавання вузла на склад.
Повузлової (послідовно-вузловий) метод полягає в тому, що всі складальні одиниці (вузли) машини послідовно, з інтервалами за часом, піддають ремонту. Він використовується в основному при капітальному ремонті найбільш завантаженого обладнання, значний простий якого за умовами виробництва неприпустимий. Застосовується для підйомно-транспортних машин, які обслуговують весь цех, а також для обладнання, вузловий метод ремонту якого економічно недоцільний внаслідок потреби в дорогих запасних вузлах.
У ряді випадків економічно обгрунтовано поєднання вузлового і повузлова ремонтів обладнання.
2. Перерахувати технічні вимоги до напрямних ковзання, кочення,
В останні роки все більш широке застосування в металорізальних верстатах знаходять напрямні кочення (рис. 16.7, б). При коченні кульок або роликів по замкнутим напрямних виникає тертя кочення, сила якого приблизно в 20 разів нижче сили тертя ковзання, в зв'язку з чим їх знос значно менше в порівнянні з зносом напрямних ковзання. Крім того, забезпечується більш плавний рух, так як відсутній ефект прилипання, характерний для напрямних ковзання.
Гідростатичні напрямні (рис. 16.7, в) застосовують у випадках, коли необхідна дуже висока точність переміщення рухомих вузлів, наприклад в прецизійних верстатах і верстатах з програмним управлінням.
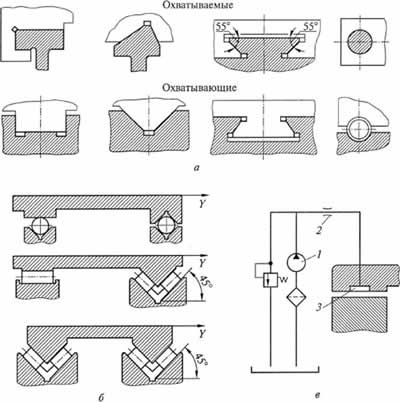
Мал. 16.7. Напрямні ковзання (а), кочення (б) і схема гидростатических незамкнутих напрямних (в): 1 - насос; 2 - дросель; 3 - канал
Завдяки наявності між сполучаються деталями масляного шару завтовшки в декілька мікрометрів вони працюють майже без тертя, в зв'язку з чим ККД практично дорівнює 1.
Рухомий вузол переміщається як би на масляній подушці, яка створюється за рахунок подачі масла під тиском від насоса 1 в зазор між рухомим і нерухомим вузлами через дросель 2 і канал 3, виконаний в нерухомому вузлі.
Застосування гидростатических напрямних обмежене їхньою високою вартістю.
Для забезпечення нормальної роботи механізму з поступально рухомими частинами, слід дотримуватись таких технічних вимог до напрямних:
· Вони повинні бути прямолінійними і без задирів на поверхні;
· На напрямних повинні бути мастильні канавки, що містяться в нормальному стані;
· Відхилення напрямних від прямолінійності повинне становити 0,01-0,05 мм на 1000 мм їх довжини, від паралельності - 0,01-0,05 мм, від перпендикулярності - 0,01-0,02 мм;
· Шорсткість поверхні напрямних після їх остаточної обробки повинна становити: для напрямних загального призначення Ra = 1,25-0,63 мкм; для напрямних прецизійного обладнання Ra = 0,04 мкм.
3. Здійснити установку і пригін накладних направляючих.
Напрямні можуть бути виконані за одне ціле із станиною або накладними (знімними). Накладні напрямні виготовляють окремо від станини у вигляді пластин зі сталі або з високоякісного чавуну з наступною термообробкою. Довгі пластини роблять складовими з окремих пластин, короткі - з цілого шматка і кріплять їх до попередньо обробленим місцях. Після установки на станину напрямні пластини остаточно обробляють: шліфують, шабрують, або притирають.
Пригін напрямних і пов'язаних з ними рухомих частин з необхідною точністю - операція трудомістка. Тому для полегшення пригін і регулювання зазору між поверхнями, що труться як при складанні машини, так і під час її роботи вузли з поступально-рухомими деталями повинні мати регулювальні пристрої - компенсатори.
Компенсатори бувають прямокутні або косокутні з ухилом від 1: 40 до 1: 100 (рис. 16.8, б). Планки 1 для регулювання зазору (рис. 16.8, а) і клини 3 переміщаються в поздовжньому напрямку і закріплюються на встановленому місці за допомогою гвинтів 2. Регулюючу планку пли клин (рис. 16.8, в, г), як правило, потрібно ставити з незавантаженої боку рухомий деталі.
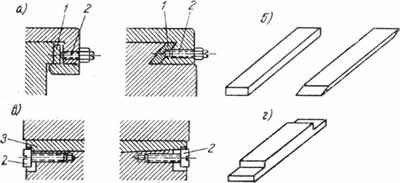
Мал. 16.8. Регулюючі пристрої (компенсатори):