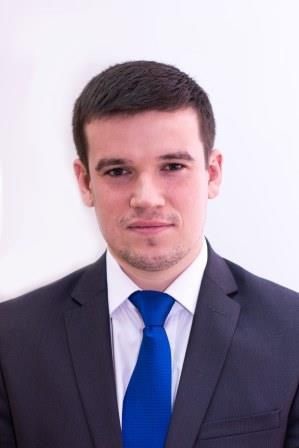
комерційний директор ТОВ ФОРМОТРОНІК®
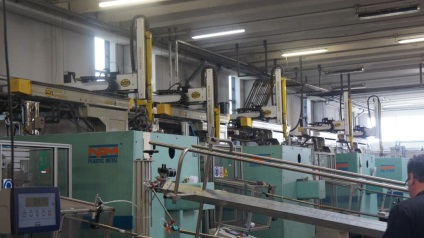
Cлово «АВТОМАТИЗАЦІЯ» зараз, мабуть, у всіх на слуху і вживається все частіше і частіше. Особливо воно актуальне у виробничій сфері. І це цілком зрозуміло - в умовах сучасної непростій економічній ситуації будь-яка розсудлива керівник прагне організувати роботу на своєму підприємстві так, щоб з найменшими витратами досягти максимальної ефективності та оптимального співвідношення вкладених коштів і отриманого результату. Саме тут і допомагає «АВТОМАТИЗАЦІЯ».
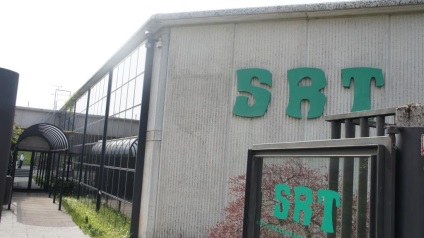
Нещодавно наші фахівці в рамках програми навчання відвідали ряд італійських компаній, проізводящіхпластмассовие вироби. Одна з компаній - S.R.T. Srl - спеціалізується на виробництві плічок для одягу різних брендів (в тому числі і дуже відомих). Нам вдалося не просто побачити роботу самого виробництва, але і поспілкуватися безпосередньо з керівником і власником компанії.
Здивували дві речі: зручний і комфортний, в істинно італійському стилі, офіс при практично повній відсутності фахівців в цеху з 28 термопластавтоматів (!). І це було в піковий сезон, коли виробництво було завантажено на 100%.
Пояснили нам це просто:
«Ми постаралися автоматизувати всі основні виробничі процеси - подачу матеріалу, відведення готової продукції, складання виробів і упаковку готової продукціі.Расчет дуже простий: середня зарплата робітника 1500,00 євро, податки - ще 1200,00 євро. При цьому, співробітники помиляються, звільняються, йдуть у відпустку, хворіють. Все це - ризики, пов'язані з людським фактором. Але подібні моменти не повинні впливати на робочий процес. Тому ми намагаємося максимально автоматизувати всі операції ».
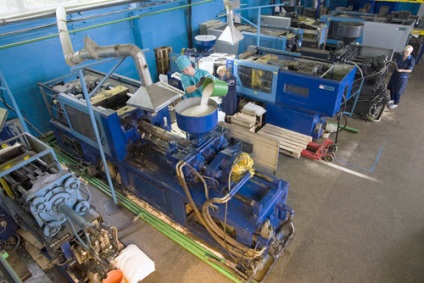
На жаль, ефективність російських виробництв істотно відрізняється від європейських. Продуктивність праці на 30-40% нижче, ніж в Європі, та й зарплати працівників значно нижче. Може бути, тому керівники підприємств не завжди замислюються про автоматизацію процесів. І дарма!
Пропонуємо розглянути кілька прикладів автоматизації виробництв на наших російських підприємствах.
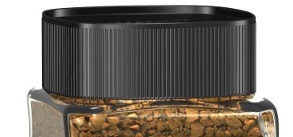
Виріб: кришка для кавових банок.
Кількість гнізд в прес-формі: 12 шт.
Кількість виробів в коробі: 110 шт.
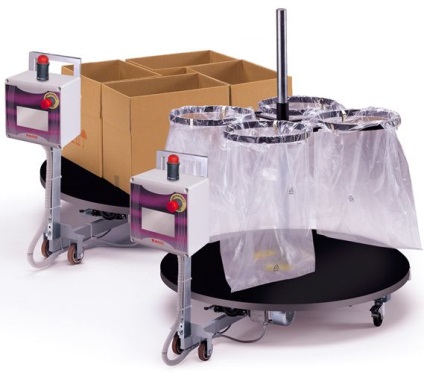
В рамках автоматизації виробництва на підприємстві були встановлені поворотні столи на 4 коробки. Період зміни тари зменшився в 4 рази і один оператор зміг обслуговувати спокійно вже 3 ТПА.
Крім того, при використанні поворотних столів у виробництві фактично виключається операція перерахунку кількості виробів при упаковці в коробку.
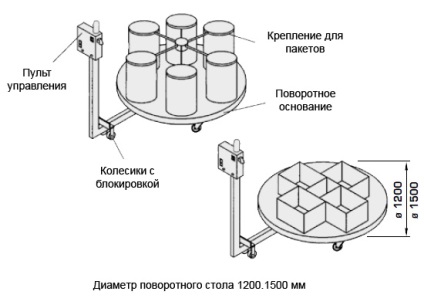
Поворотний стіл являє собою платформу, на якій розміщується від 2 до 8 пакувальних місць. На блоці управління поворотним столом задається кількість деталей, яке необхідно завантажити в пакувальну ємність. Коли ємність заповнена, стіл повертається і починається завантаження наступної ємності.
Вартість столу (в залежності від варіанту виконання) порядку 2 520 євро.
Термін окупності при цілодобовому виробництві не більше 6 місяців.
Підприємство виробляє пластикову фурнітуру для меблів.
Вага заглушки: 20 м
Розмір: 30 мм х 8 мм.
Підрахунок виробів ведеться оператором. Відхилення + 5 виробів не допускається.
Ми встановили у одного з ТПА систему вагового обліку та упаковки - ваговий конвеєр.
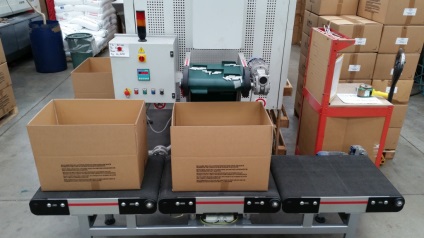
Ваговій конвеєр являє собою один або кілька стрічкових конвеєрів. Система може складатися з 3-х і більше секцій:
- секція зважування - конвеєр з тензодатчиками;- секція для порожньої тари;
- секція для наповненою тари.
Готові вироби надходять на ваговій конвеєр за допомогою стрічкового конвеєра. Устаткування задає максимальна вага, який визначає наповненість коробки. При досягненні заданої ваги подає конвеєр зупиняється, а наповнена тара переміщається на наступну секцію. Порожня тара направляється на секцію зважування.
При використанні вагового конвеєра вдалося домогтися високої точності фасування виробів і повністю автоматизувати цей процес. Крім того, за рахунок буферної зони конвеєра вдалося зменшити частоту зміни коробів в 4 рази.
Але головне у використанні конвеєрів - звільнити виробничу зону від готової продукції. Щоб вона не накопичувалася, що не захаращувала територію навколо ТПА, а своєчасно відводилась в зону складання, упаковки, складування.
Вартість ваговій станції (в залежності від варіанту виконання) близько 7 400 євро. Термін окупності проекту при цілодобовому виробництві становить не більше 1,5 років.
Підприємство виготовляє вироби електротехнічного призначення. У виробництві використовуються холодноканальние форми з відривним літником.
Готові вироби разом з літником надходять на стрічковий конвеєр з лопатевим сепаратором.
Після сепаратора літники надходять в дробарку, а вироби в спеціальну тару.
Матеріал подається на ТПА з допомогою двокомпонентного завантажувача. Перший компонент - основний матеріал, другий - вторинний подрібнений матеріал - забирається прямо з дробарки.
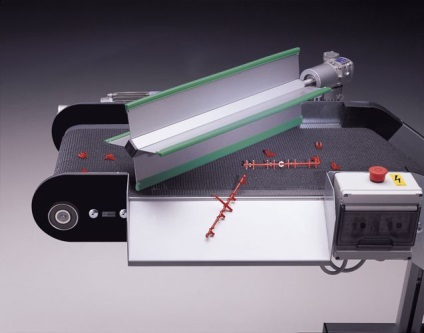
Лопатеві сепаратори використовуються у випадках, коли виріб за габаритними розмірами відрізняється від литника більш ніж на 3-5 мм. Сепаратори літників встановлюються безпосередньо на конвеєрах, закріплюючись на корпусі в зоні скидання виробів в тару. На лопастном сепараторі встановлюється зазор між стрічкою конвеєра і лопатями обертового вала. Вал з лопатями закріплений під кутом до напрямку руху стрічки конвеєра, тому деталі, що не проходять у встановлений зазор під лопатями вала, стикаються їм на бічній лоток. Інші деталі проходять в основний приймальний лоток конвеєра.
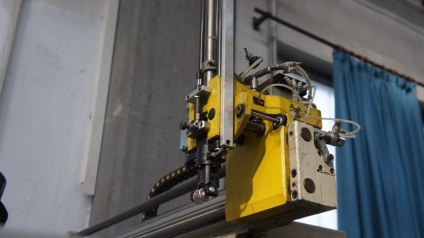
Ще один варіант автоматизації цього процесу - використання робота-пікера.
Робот-пікерзахвативает литник в порожнині форми і відправляє його безпосередньо в дробарку, готовий виріб потрапляє на конвеєр, після чого надходить в тару. При використанні робота досягається 100-процентна автоматизація поділу літників і деталей. Це рішення, безумовно, більш універсально і не залежить від співвідношення розмірів ливника і деталі.
Вартість конвеєра з лопатевим сепаратором 2 400 євро. Термін окупності при цілодобовому виробництві становить не більше 6 місяців.
Для однієї з компаній в м.Санкт-Петербурзі був проведений розрахунок окупності роботизованої системи, що складається з 2 роботів і 6 конвеєрів загальною вартістю 105 000 євро на кожен Термопластавтомат.
Виріб: корпусні деталь блоку управління
Розмір виробу: 40х20 мм
Комплекс обладнання повинен забезпечити виконання наступних операцій:
- з'їм деталей з ТПА;
- укладка деталей в спеціальну тару в 5 шарів;
- укладка сепаруючої прокладки між шарами;
- установка наповненою тари в стопку по 10 шт .;
Потрібна повна автономність роботи системи мінімум на 120 хв, тобто протягом двох годин оператор не підходить до системи, вона повинна працювати в повністю автоматичному режимі.
При виконанні перерахованих операцій вручну поруч з кожним термопластавтоматами повинен сидіти оператор, не залишаючи свій пост ні на хвилину. І так щозміни, 7 днів на тиждень без упину!
Навіть при такій високій, на перший погляд, вартості роботизованого комплексу окупність його становить 7,5 років. Це дуже гідний показник для засобів автоматизації.
Все це реальні приклади діючих виробництв, взяті з нашої практики виконаних проектів в різних регіонах Росії.
Як легко помітити, автоматизація виробничих процесів дозволяє не тільки оптимізувати схему роботи підприємства, уникнути проблем, пов'язаних з людським фактором, перерозподіливши більш раціонально людські ресурси, а й підвищити загальну культуру виробництва виробів з пластмас, створити більш привабливий образ підприємства, як на галузевому ринку, так і на ринку праці.
Фахівці ТОВ "ФОРМОТРОНІК" ® будуть раді посприяти підприємствам Росії та країн ближнього зарубіжжя в рішенні питань автоматизації виробничих процесів.