Термічна обробка стали, в результаті якої змінюється хімічний склад поверхневих шарів, називається хіміко-термічною обробкою. Виріб нагрівається в спеціально вибраному середовищі і зміна хімічного складу поверхні відбувається завдяки переходу і впровадження атомів цієї речовини в кристалічну решітку стали.
Процес проникнення однієї речовини в іншу при їх зіткненні називається дифузією. Залежно від середовища, в якій нагрівається виріб, розрізняють кілька видів хіміко-термічної обробки. Найбільш поширеними з них в промисловості є: цементація, азотування і ціанування.
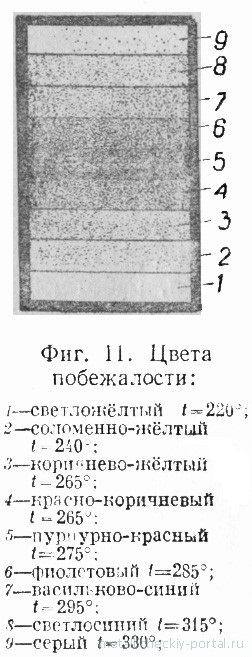
В інструментальному виробництві цементація застосовується при виготовленні вимірювального інструменту, пристроїв, деяких видів монтажного інструменту і т. П.
Цемент сталь в твердій, газової та (рідко) рідкої середовищах, здатних віддати свій вуглець. Ці середовища носять назву карбюризаторів.
Цементація в твердому карбюризаторі. В якості твердого карбюризатора в промисловості широко застосовується суміш деревного вугілля з вуглекислими солями (вуглекислим барієм, вуглекислим натрієм, вуглекислим кальцієм).
Для приготування карбюризатора вугілля роздрібнюють на шматочки розміром 3-10 мм і просівають для видалення пилу. Вугілля використовують дубовий або березовий, так як вугілля з м'яких порід швидко згоряє. Вуглекислі солі подрібнюють в порошок і просіюють через дрібне сито.
Перший спосіб, при якому виходить найбільш рівномірна суміш, полягає в наступному: сіль розчиняють у воді, поливають цим розчином вугілля, перемішують і висушують. Допустима вологість 5-7%.
Другий спосіб полягає в ретельному перемішуванні вугілля і солі в сухому вигляді. Погано перемішаний карбюризатор дає нерівномірний шар цементації, плямистість.
Багато заводів застосовують готовий карбюризатор, виготовлений Бондюжского заводом, з вугілля і декількох видів вуглекислих солей. Карбюрізатори, виготовлені заводами для своїх потреб, зазвичай складаються з 85-90% деревного вугілля і 10-15% по вазі вуглекислого натрію (кальцинованої соди). Для цементації застосовують суміш з 20-30% свіжого карбюризатора і 70-80% відпрацьованого. На окремих заводах застосовують замість вугілля деревна тирса, додають в карбюризатор обвуглену кістка, шкіру і т. П. Однак всі ці добавки, а також заміна вугілля тирсою, погіршують якість цементації.
Деталі, які надходять для цементації, повинні бути сухими і очищені від окалини, іржі, бруду, масла, стружки і т. П.
Запобігання поверхонь виробів, що не підлягають цементації. Ділянки деталей, які за технологічними умовами не повинні цементованного, оберігають від науглероживания наступними способами:
1. залишені припуску у виробах, що обробляються різанням. У місцях, що не підлягають цементації, залишають припуск більший, ніж задана глибина цементації. Перед загартуванням цей припуск видаляється на верстаті.
2. накладання обмазки. Як обмазки, що накладається на місця, що не підлягають цементації, застосовуються: а) глина, змішана з рідким склом; б) суміш з глини, піску і азбестового дрібниці, замішана на рідкому склі; в) суміш з термоизоляционного порошку або кварцового піску (75%) і дрібної окалини (25%), просіяних через сито з осередками 1 х 1 мм.
3. обміднений. Ділянки, що не підлягають цементації, покривають шаром міді товщиною 0,03-0,04 мм. Цей спосіб вимагає спеціального гальванічного обладнання.
4. фосфатировании. Місця, що підлягають цементації, попередньо покриваються цапон-лаком, після чого виріб повністю занурюється у ванну з гарячим водним розчином фосфатів ортофосфорної кислоти, при цьому непокриті місця виробів фосфатується, що можна спостерігати по виділенню бульбашок на поверхні розчину. Припинення виділення бульбашок вказує на закінчення фосфатирования. Процес простий і надійний.
Деталі, що підлягають цементації, упаковують в ящики з карбюризатором. Ящики найкраще виготовляти за формою деталей. Це зменшує час для прогріву скриньок і покращує якість цементованного шару. Однак виготовляти такі ящики раціонально тільки при цементації великих кількостей деталей. У всіх інших випадках ящики виготовляють круглі, квадратні або прямокутні, розміри їх вибираються в залежності від розміру печі і скільки повідомлень потрібно завантажувати в них виробів.
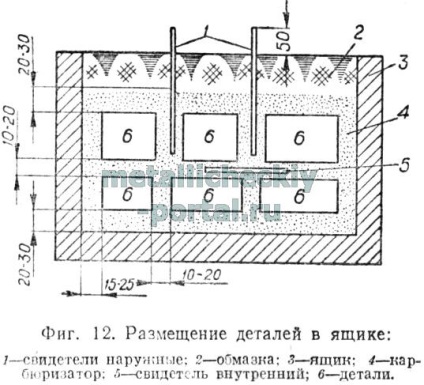
Найбільший розмір ящиків при цементації в печах середньої величини 250 х 500 х X 300 мм при товщині матеріалу від 4 до 8 мм. Матеріалом для ящиків служить жаростійкий сталь, а при її відсутності - звичайна малоуглеродистая сталь. При упаковці деталей в ящики слід витримувати відстань між деталями 10-20 мм, а між деталями і дном 20-30 мм (фіг. 12).
При упаковці деталей карбюризатор щільно трамбується, а ящик зверху обмазується сумішшю з двох частин глини і однієї частини річкового піску, розведених водою до тістоподібної стану. Свідки вкладаються в ящик для визначення глибини цементації: один всередину пакета для пред'явлення контрольного майстра, а два зовнішніх для контролю ведення процесу самим робітникам. Свідки виготовляються зі сталі марки 15 або 20 діаметром 8-12 мм.
Технологічний процес цементації. Перед завантаженням ящиків в піч треба підсушити глину, щоб вона не потріскалася. Завантаження виробляти в піч, нагріту до 900 - 950 °. В результаті завантаження холодних ящиків в піч температура останньої дещо знизиться. Наскрізний прогрів ящиків проводити при температурі 780-800 °. Практично закінчення прогріву визначають за кольором подовой плити; при недостатньому прогріві плита під ящиком буде темна, а при повному прогріві колір подовой плити буде скрізь однаковий. Після прогріву скриньок при температурі 780-800 ° швидко піднімають температуру до 900 - 950 ° і проводять процес цементації. Швидкий нагрів ящиків до температури цементації відразу після посадки їх у піч не рекомендується, так як внаслідок великої різниці температур між центром і краями ящика глбіна цементації буде неоднакова. Тривалість витримки в залежності від глибини цементуемие шару приведена в табл. 12.
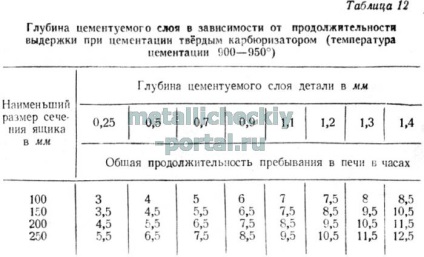
Закінчення процесу цементації визначають по зламу загартованого свідка. Один зі свідків виймається з шухляди і гартується приблизно за годину до передбачуваного закінчення цементації, а другий - до моменту вивантаження.
Глибину цементованного шару найкраще визначати шляхом травлення зламу загартованого свідка реактивом, що складається з 100 см 3 денатурованого спирту, 1 см 3 соляної кислоти і 2 г хлористого міді.
Тривалість травлення - одна хвилина. Місця не цементованного покриваються міддю.
Охолодження ящиків після цементації проводять на повітрі. Розпакування гарячих ящиків не рекомендується, так як це не безпечно в протипожежному відношенні і не економно витрачається карбюризатор.
Процес газової цементації, розроблений радянськими вченими Н. А. Мінкевича, С. К. Ильинским і В. І. Просвірін, здійснюється шляхом нагрівання деталей в атмосфері газів, що містять вуглець. У порівнянні з цементацією в твердому карбюризаторі цементація в газовому карбюризаторі має такі переваги: відпадає необхідність приготування карбюризатора; скорочується час перебування ящика з деталями в печі; зменшується кількість необхідної робочої сили і площ цеху і значно поліпшуються умови праці. Деталі, що підлягають цементації, закладають в муфель печі, підігрітий до 900-950 °, герметично закривають і подають газ.
Для газової цементації застосовуються: 1) природний газ (дашавський, саратовський, приазовский); 2) штучний газ; 3) генераторний газ і т. П.
З штучних газів найбільше застосування отримав газ, що готується шляхом розкладання нафтопродуктів. Процес приготування газу такий: гас подається краплями в нагрітий сталевий посудину і там розкладається на суміш газів (процес розкладання називається піролізом). Частина піролізного газу піддають додатковій обробці - крекінг-процесу, при якому змінюється склад газу, так як при цементації одним піролізного газом виходять щільні відкладення сажі на деталях, мала глибина цементації і т. Д. Для цементації застосовують суміш з 40% піролізного газу і 60 % крекірованного газу.
Термічна обробка цементованих виробів
Цементованного деталіпіддаються загартуванню та відпуску. Загартування виробляють подвійну або одинарну. При подвійний гарту перша проводиться при температурі 860 -900 ° для поліпшення структури серцевини, а друга при температурі 760 -800 ° для додання твердості зовнішнього шару.
На деяких заводах вважають раціональним виробляти одинарну загартування при температурі 760-800 °. Інструменти, що піддаються цементації, повинні володіти високою твердістю і тому для них можна обмежитися одинарної загартуванням, крім випадків, обумовлених в технології. Після гарту вироби піддають низькотемпературного відпуску для зняття внутрішніх напружень. Інструмент, що проходить газову цементацію, можна розжарювати безпосередньо з муфеля цементаціонной печі, злегка остудити його на повітрі.
Азотування і ціанування
Азотування. Процес азотування полягає в насиченні поверхневого шару стали азотом. В результаті азотування цей шар набуває досить високу твердість і зберігає її при нагріванні до 530-550 °. Для азотування застосовують головним чином сталь, що містить алюміній, хром і молібден.
Процес азотування полягає в пропущенні аміаку через герметично закупорений муфель, в якому знаходиться деталь. Температура азотування 500-600 °. Газ, що складається з азоту і водню, при цій температурі розкладається на складові частини, з яких азот проникає в сталь, а водень віддаляється з печі. Дифузія азоту в сталь відбувається дуже повільно - протягом 40 -90 год. Велика тривалість процесу і крихкість азотированного шару є недоліками цього виду обробки.
Ціанування. Процес насичення поверхневого шару сталі азотом і вуглецем називається ціануванням. Розрізняють два види ціанування: високотемпературне-прі 750 -850 ° і низькотемпературне прі 530-560 °. В інструментальному справі застосовують в основному низькотемпературне ціанування інструментів, виготовлених зі швидкорізальної сталі для підвищення їх стійкості. Ціанування проводиться в рідкій, газової і твердої середовищах.
Рідке ціанування проводиться в розплавлених ціаністих солях. Глибина ціанування залежить від складу ванни і тривалості витримки.
Ціанування піддається остаточно оброблений і заточений інструмент, тому процес слід вести ретельно як в частині дотримання температур, так і в частині обережного поводження з інструментом.
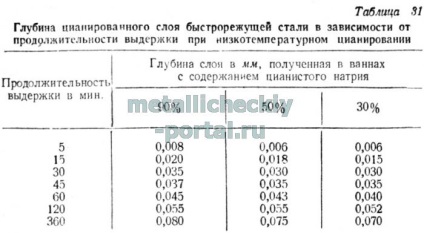
Тверде ціанування проводиться в суміші сухого деревного вугілля (60-70%) і жовтої кров'яної солі (30-40%). Приготування суміші, упаковка в ящики і обмазка виробляються так само, як і прп цементації. Тривалість витримки від 1 до 3 год. в залежності від розмірів інструменту. Після закінчення витримки ящик охолоджується на повітрі до температури 100-200 °, після чого розпаковується.