Установки для автоматичного зварювання поздовжніх швів обичайок - в наявності на складі!
Висока продуктивність, зручність, простота в управлінні і надійність в експлуатації.
Зварювальні екрани і захисні шторки - в наявності на складі!
Захист від випромінювання при зварюванні і різанні. Великий вибір.
Доставка по всій Росії!
На токарних верстатах обробка циліндричних отворів проводиться свердлами, зенкерами, розгорненнями і розточувальними оправками з закріпленими в них різцями.
Головний рух різання під час свердління - обертальний, воно виконується заготівлею; рух подачі - поступальний, виконується інструментом. Перед початком роботи перевіряють поєднання вершин переднього і заднього центрів токарного верстата. Заготівлю встановлюють в патрон і перевіряють, щоб її биття (ексцентричність) щодо осі обертання не перевищувало припуску, що знімається при зовнішньому обтачивании. Перевіряють биття торця заготовки, при якому буде оброблятися отвір, і вивіряють заготовки по торця. Перпендикулярність торця заготовки до осі її обертання можна забезпечити підрізуванням торця. При цьому в центрі заготовки можна виконати поглиблення для забезпечення потрібного напрямку свердла і запобігання його відведення та поломки.
Свердла з конічними хвостовиками встановлюють безпосередньо в конусний отвір пінолі задньої бабки, а якщо розміри конусів не збігаються, то використовують перехідні втулки.
Для кріплення свердел з циліндричними хвостовиками (діаметром до 16 мм) застосовують свердлильні кулачкові патрони, які встановлюють в пінолі задньої бабки.
Перед свердлінням отворів задню бабку переміщують по станині на таку відстань від заготовки, щоб свердління можна було виробляти на необхідну глибину при мінімальному висунення пиноли з корпусу задньої бабки. Перед початком свердління заготівлю приводять в обертання включенням шпинделя.
Свердло плавно (без удару) підводять вручну (обертанням маховика задньої бабки) до торця заготовки і виробляють свердління на невелику глибину (надсверлівают). Потім відводять інструмент, зупиняють заготівлю і перевіряють точність розташування отвори. Для того щоб свердел не змістилося, попередньо виробляють центрування заготовки коротким спіральним свердлом великого діаметра або спеціальним центрувальні свердлом з кутом при вершині 90 °. Завдяки цьому на початку свердління поперечна кромка свердла не працює, що зменшує зсув свердла щодо осі обертання заготовки. Для заміни свердла маховик задньої бабки повертають до тих пір, поки піноль не займе в корпусі бабки крайнє праве положення, в результаті чого свердло виштовхується гвинтом з пінолі. Потім в піноль встановлюють потрібне свердло.
При свердлінні отвору, глибина якого більше його діаметра, свердло (також як при роботі на свердлильних верстатах), періодично виводять з оброблюваного отвору і очищають канавки свердла і отвір заготовки від накопичилася стружки.
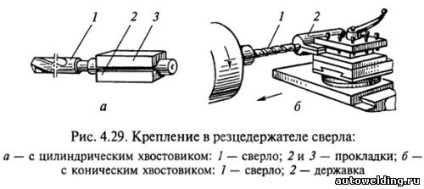
При ручному управлінні верстатом важко забезпечити постійну швидкість руху подачі. Для стабілізації швидкості подачі використовують різні пристрої. Для механічної подачі свердла його закріплюють у різцетримачі. Свердло 1 з циліндричним хвостовиком (рис. 4.29, а) за допомогою прокладок 2 і 3 встановлюють в резцедержателе так, щоб вісь свердла співпадала з лінією центрів. Свердло 1 з конічним хвостовиком (рис. 4.29, б) встановлюють в державке 2, яку кріплять у різцетримачі.
Після вивірки збігу осі свердла з лінією центрів супорт зі свердлом вручну підводять до торця заготовки і обробляють пробне отвір мінімальної глибини, а потім включають механічну подачу супорта. При свердлінні напроход перед виходом свердла з заготівлі швидкість механічної подачі значно зменшують або відключають подачу і закінчують обробку вручну.
При свердлінні отворів діаметром 5. 30 мм швидкість подачі S0 = 0,1. 0,3 мм / об для сталевих деталей і S0 = 0,2. 0,6 мм / об для чавунних деталей.
Для отримання більш точних отворів і для зменшення відведення свердла від осі деталі використовують розсвердлювання, т. Е. Свердління отвору в кілька прийомів. При свердлінні отворів великого діаметра (понад 30 мм) також вдаються до Розсвердлювання для зменшення осьового зусилля. Режими різання при розсвердлювання отворів ті ж, що і під час свердління.
зенкування
Зенкером обробляють отвори, попередньо штамповані, литі або просвердлені. Зенкування може бути як попередньої (перед розгортанням), так і остаточною обробкою. Крім обробки отворів, зенкери застосовуються іноді для обробки торцевих поверхонь заготовок.
Для підвищення точності зенкерования (особливо при обробці литих або штампованих глибоких отворів) рекомендується заздалегідь розточити (різцем) отвір до діаметру, рівного діаметру зенкера, на глибину, приблизно рівну половині довжини робочої частини зенкера.
Зенкери, як і свердла, встановлюють на токарних верстатах найчастіше в задній бабці або револьверної голівці.
розгортання
Для отримання на токарних верстатах отворів високої точності і заданої якості оброблюваної поверхні застосовують розгортання.
При роботі чистовими розгорненнями на токарних і токарно-револьверних верстатах застосовують хитні оправлення, які компенсують розбіжність осі отвору з віссю розгортки. Для того щоб забезпечити високу якість обробки, свердління, зенкування (або розточування) і розгортання отвори виробляють за одну установку заготовки в патроні верстата.
Вибір режимів різання при обробці циліндричних отворів стрижневими інструментами на токарних верстатах виробляють за тими ж таблицями довідника, що і при обробці на свердлильних верстатах. Однак, з огляду на малу жорсткість кріплення стрижневих інструментів на верстатах токарної групи, розрахункові значення режимів на практиці зменшують.
розточування
Якщо діаметр отвору перевищує діаметр стандартних свердел або зенкерів, то такий отвір розточують. Розточування застосовують також при обробці отворів з нерівномірним припуском або з непрямолінійних утворює.
Залежно від призначення розрізняють токарні розточувальні різці для обробки наскрізних і глибоких отворів. У токарних розточувальних стрижневих різців консольна частина виконана круглої, а стрижень для кріплення різців - квадратним; такими різцями можна розточувати отвори діаметром 30. 65 мм. Для підвищення вібростійкості ріжучакромка різців виконана по осі стержня.
На токарно-револьверних верстатах застосовують розточувальні різці круглого перетину, які кріпляться в спеціальних оправках-державках (рис. 4.30).
Форма передньої поверхні і всі кути у розточувальних різців (за винятком заднього) приймаються такими ж, як і у прохідних, що застосовуються при зовнішньому точінні. Кути різання у розточувальних різців можна змінювати шляхом установки ріжучої кромки різців щодо поздовжньої осі деталі (вище або нижче осі).
При розточуванні різець знаходиться в більш важких умовах, ніж при зовнішньому поздовжньому точінні, так як погіршуються умови для відводу стружки, підведення МОР і відведення тепла.
Розточувальний різець в порівнянні з токарним має меншу площу перетину державки і більший виліт, що обумовлює віджимання різця і сприяє виникненню вібрацій; тому при розточування, як правило, знімається стружка меншого розміру і знижується швидкість різання.
При чорновому розточуванні стали приймають глибину різання до 3 мм; подовжню подачу - 0,08. 0,2 мм / об; швидкість різання - близько 25 м / хв для різців з швидкорізальної сталі і 50. 100 м / хв для твердосплавних різців.
При чистовому розточування глибина різання не перевищує 1 мм, поздовжня подача - 0,05. 0,1 мм / об, швидкість різання - 40. 80 м / хв для різців з швидкорізальної сталі і 150. 200 м / хв для твердосплавних різців.