- огранювання алмазів в діаманти;
Технологічний процес ограновування природного і синтетичного каміння складається з операцій:
- попередній огляд сировини і розмітка;
- розпилювання або різка;
- огранювання, шліфування, полірування;
Попередній огляд каменю проводиться для вибору найбільш оптимального способу його обробки з урахуванням дефектів, нерівномірності забарвлення, можливої форми огранювання.
Форма сировини обумовлює втрати матеріалу при огранювання. Наприклад, кристали турмаліну - це вузькі олівці з трикутним перетином. Турмаліну зазвичай надають смарагдову огранювання, тому такий кристал є природною заготівлею і втрати невеликі. Цитрин, аметист, берил поставляються у вигляді шматків неправильної форми. Втрати будуть максимальні у подовжених і гострокутих шматків в порівнянні з шматками сферичної або кубічної форми.
При обдирання можна прибрати тільки поверхневі тріщини. Глибокі тріщини, що йдуть до центру каменю, залишаться недоторканими. Тріщини часто можна виявити при огляді каменю під прикритої рефлектором настільною лампою (рис. 6.1). Світло не повинен потрапляти в очі. Камінь розташовується біля краю відбивача. Одна його половина освітлена лампою, інша перебуває в тіні. Очі спостерігача знаходяться в тіні вище освітленій області. Вхо-дящій в камінь світло висвітлює включення та інші дефекти, добре помітні на темному тлі. Огляд необхідний з усіх боків, так як деякі дефекти видно тільки під певним кутом.
Виразні площині спайності видають себе сріблястими рефлексами або невеликими райдужними кружками. Тріщини по площині спайності можуть в подальшому призвести до руйнування каменю.
Розмір ограночного сировини важливий з точки зору забарвлення. Практичне правило: якщо видно задня сторона необробленого каменю під час огляду при хорошому освітленні, то при огранювання сировину придатне для виготовлення одного каменю. Якщо сировина виглядає чорним і його колір можна побачити лише при освітленні ззаду яскравим світлом, то з такого зразка можна тільки виготовити кілька дрібних каменів.
Крім того, занурюючи шматки сировини в імерсійним рідини, можна легко побачити всі внутрішні дефекти каменю. При відсутності іммерсійних рідин можна скористатися гасом, мінеральним, касторовою, гірчичним маслом або інший прозорою рідиною з підвищеним показником заломлення світла. Чим ближче показник заломлення рідини до такого каменю, тим краще.
Розмітка каменів здійснюється під лупою з шестиразовим збільшення або бінокулярним мікроскопом таким чином, щоб найбільш густо-забарвленої була нижня сторона огранованого каменю. Лінії розпилювання або розколювання намічають фломастером, при цьому необхідно враховувати, як краще прибрати дефекти каменю в процесі ограновування. Операція по розмітці каменю дуже відповідальна і вимагає великого досвіду і знань особливостей каменю - його властивостей, кристаллографического будови і т.д.
Розпилюванням або розколюванням ювелірні камені поділяють на частини, придатні для подальшої обробки. Розколювання в даний час застосовують рідше розпилювання, в основному при обробці алмазів спотвореної форми або алмазів з дефектами, усувається при розколюванні. Алмаз закріплюють спеціальним цементом на оправці, на ребрі алмазу осколком алмазу наносять ризику (рису), а потім за допомогою спеціального ножа, що вставляється в ризику, відколюють частина алмаза.
Розпилюють алмази за певними площинах, що не відповідає напрямкам розколювання. Ці площини розташовуються паралельно гранях куба або ромбододекаедра. Розпилюють алмази на спеціальному верстаті тонкими дисковими пилами, покритими алмазним мікропорошки. На верстатах, використовуваних у нас в країні, діаметр дисків становить 75 мм, товщина від 0,04 до 0,09 мм в залежності від розміру, що розпилюється кристала.
Технологічний процес розпилювання починається з наклейки розмічених кристалів спеціальної масою, що складається з медичного гіпсу і клею в пропорції 1: 1. потім кристал орієнтують для суміщення площині лінії розмітки з площиною розпилювального диска. Робиться це візуально або за допомогою мікроскопа МБС-2, оснащеного спеціальним пристроєм. Після цього проводиться підріз кристала на глибину 1-1,5 мм на малих швидкостях (щоб не зіпсувати пилу і нормально «увійти» в кристал) і подальше його розпилювання. Навантаження на алмаз при розпилюванні становить від 120 до 300 г залежно від маси кристала (від 0,1 до 5 кар і вище) і товщини диска (від 0,05 до 0,08 мм). В даний час для розпилювання алмазу широко застосовуються напівавтоматичні верстати. Кольорові ювелірні камені розпилюють на спеціальному верстаті за допомогою тонких алмазних дисків з частотою обертання до 8000 об / хв. Для охолодження каменю використовують охолоджуючі рідини: воду, водомасляні емульсії (як на металорізальних верстатах), ефірні олії, гас в суміші з моторним маслом в співвідношенні 10: 1, дизельне паливо.
Камінь закріплюють в затиску і вручну (або під власною вагою) подають назустріч руху диска, що обертається.
До появи алмазних пилок для різання використовувалися абразивні порошки, наприклад, наждак або карбід кремнію, які подавалися до периферії сталевого диска або полотна у вигляді рідкої суспензії або шламу.
Алмазні пили відрізняються тим, що абразив в них включений безпосередньо в сталевий диск з його периферії. Диск виготовляється з м'якої сталі, а якщо диск маленького діаметру, то з бронзи або міді. Пили діаметром до 100 мм застосовуються для різання цінних матеріалів, діаметром 200 мм - для підрізування, більші, до декількох десятків сантиметрів, - для розпилювання каменю на пластини і блоки.
Деякі мінерали засмічують ( «засолюють») відрізні диски - нефрит, малахіт, жадеїт, везувіан. Іноді мінерал налипає на диск, і замість того, щоб різати камінь, диск його просто полірує в глибині розрізу. Швидкість розпилювання при цьому знижується, диск перегрівається і деформується або ж заклинюється. Щоб уникнути цього небажаного явища використовуються мінімальні швидкості подачі інструменту. Якщо це не допомагає, то до ріжучої кромці диска, що обертається підносять шматочок цегли. Останній очищає диск і оголює частки алмазу.
Останнім часом для розпилювання також стали використовувати алмазні стрічкові і дротові пилки.
Обдирання - це абразивний процес, призначений для додання каменю попередньої (грубої) форми.
При обдирання кольорових каменів використовуються шліфувальні абразивні кола. Самі звичайні кола виготовляються з карбіду кремнію і бувають різних розмірів і форм. Відрізняються вони і за розмірами абразивного зерна - в залежності від призначення кола. В останні роки стали застосовувати обдирні круги з алмазними зернами, включеними в металеву або пластмасову основу.
Грубе зерно вибирають для виготовлення кіл, які повинні швидко видаляти зайвий матеріал. Тонке зерно використовують в тих випадках, коли бажано м'яке і легке абразивну дію.
Обдирні кола застосовують для додання форми Кабошон, при підготовці сировини до ограновування, а також для зняття фасок у плоских пластин, для об'ємної різьби, вирізання набраних деталей мозаїк та інших цілей.
Обдирання алмазу виробляють вручну алмазним різцем, закріпленим в державке. Алмазу надають круглу або іншу форму, гострі ребра і грані згладжують. Зазвичай розмір каменю, яким виробляють обдирання, відповідає розміру обдирають каменю. Обдирають алмази також і на спеціальних верстатах за допомогою кола, армованого алмазами. Камінь обертається з частотою 100-700 об / хв, а алмазний диск - з частотою 3000 об / хв. Діаметр диска 250 мм, зернистість алмазів 125/100 мкм, маса алмазів 300 кар. Опрацьований камінь приклеюють спеціальною мастикою до торця оправки, яку вставляють у відповідний пристрій на верстаті. Обробляють камінь в струмені води. Для отримання заготовок складної форми (овальної, грушоподібної, маркіза) камінь обробляють спеціальним копиром.
Обдирання алмазів також може проводитися на спеціальних автоматизованих обдирні верстатах. Заготовки закріплюються на оправках і за допомогою комп'ютера, де зображення проектується на великий екран, точно позиціонуються в безпосередньому контакті один з одним. Заготовки приводяться в обертання один щодо одного, і при контакті проводиться їх взаємна обдирання. Кожен камінь при цьому є одночасно і заготівлею та інструментом.
При обдирання вручну кольорових каменів подається вода повинна змочувати всю поверхню повністю. Опрацьований камінь бажано тримати великим і вказівним пальцями кожної руки, з'єднавши вказівні пальці внизу так, щоб камінь лежав на них як на опорі - це найзручніший і надійне захоплення. Опрацьований камінь повинен бути спрямований вниз по ходу руху кола щоб уникнути видовбування кола гострими краями каменю. Чим менше розмір каменю, тим важче утримувати його в руках і контролювати його стан.
Необхідно враховувати, що м'які камені, наприклад, опал, бірюза, змійовик, дуже швидко сошліфовивать. При обробці пластин спочатку сошліфовивать маленька фаска на гострих краях, щоб уникнути сколювання. Після зникнення фаски її необхідно відновлювати. Невеликі плоскі поверхні можна обробляти на бічній поверхні круга, а не на периферійній.
Не можна допускати сильного нагрівання каменю щоб уникнути його руйнування. Якщо на абразивному колі з'являються білі плями, це означає, що кам'яна пил не змивається, і необхідно посилити подачу води. Теплий на дотик камінь також свідчення недостатнього зволоження. При сильному перегріві камінь може тріснути або розколотися.
Необхідно враховувати, що саме на етапі обдирання створюється форма каменю. І саме обдирання є головною причиною руйнування більшості виробів в подальшому, незважаючи на те, що наступні етапи виконуються добре.
Доведення. Процес доведення нескладний. Для цього потрібно терти камінь про плоску плиту з насипаним на неї абразивним матеріалом або про абразивний круг, розташований на поворотній планшайбе. До нього вдаються, коли необхідно отримати рівну плоску поверхню.
Як і обдирання, доведення зазвичай починають з великого зерна, щоб якомога швидше вирівняти поверхні. Потім застосовують дрібний абразив, який готує поверхню до подальшого полірування.
Принцип обробки плоскої поверхні вільним абразивом показаний на рис. 6.2. При русі каменю і планшайби в протилежних напрямках зерна абразиву обертаються між поверхнями. Метал планшайби порівняно м'який і під зернами злегка вдавлюється. Камінь вдавлюватися не може, і тому сколюється. Багаторазове повторення цього процесу численними зернами абразиву призводить до того, що вся поверхня каменю покривається дрібними ямками. Якщо її сполоснути водою, вона буде виглядати матовою. Коли поверхня оброблена правильно, ця матовість однорідна. Якщо ж обробка не завершена, на поверхні каменя спостерігаються подряпини або ділянки, що відрізняються від іншої поверхні за блиском. У міру використання все більш дрібного порошку матовість стає все слабшою, поки не досягається як би напівпрозорість. Зазвичай це є ознакою того, що камінь вже готовий для полірування.
При роботі необхідна постійна подача води для охолодження каменю.
При обробці тонких пластин їх рекомендується наклеювати на підкладку, наприклад з фанери, сумішшю бджолиного воску та парафіну, або одним воском. Тепла, що виділяється при обдирання, недостатньо для розплавлення воску і зсуви пластини з підкладки. Якщо обробка проводиться на повстяному полировальник, то тепла виділяється більше, тому пластини приклеюють смолою, або шелаком *, які накладаються і видаляються при нагріванні.
Сендінг. При виготовленні багатьох виробів з каменю вдаються до сендінгу як до останнього етапу обробки перед заключною поліруванням. Хоча цей процес в основному використовується при роботі з кабошонами, нерідко його застосовують і для шліфування плоских пластин, замінюючи їм операцію тонкої доведення.
При сендіге використовується м'яка поверхня, наприклад шкіра, або менш м'яка, наприклад дерево, що має канавки (або без них) в поєднанні з фіксованим або вільним абразивом.
Незалежно від кваліфікації майстра поверхню кабошона після обробки на доводочному колі завжди покрита плоскими ділянками. Еластична абразивний поверхню такі ділянки ліквідує так само, як і ризики. Поверхня каменю стає рівномірно криволінійної, гладкою і готової для полірування.
Найбільш поширеним матеріалом, використовуваним для сендінга, є міцна тканина, покрита шаром абразиву. Дуже часто потрібно охолоджувати тканину водою в процесі обробки. В цьому випадку для з'єднання абразиву з тканиною використовують нерозчинний клей на основі синтетичних смол. Абразивну тканину випускають у вигляді дисків, стрічок і ременів стосовно до різного устаткування. На поверхню іноді наноситься пластмаса, яка містить алмаз.
Найбільший недолік сухого сендінга - місцевий нагрів каменю. Від перегріву камінь може відокремитися від оправлення, а також растрескаться. При мокрому сендінге виключено попадання на поверхню тканини кам'яного пилу, завдяки постійній подачі води. Крім того, мокрий сендінг дозволяє отримувати більш якісну поверхню каменю. Вода діє як мастило, а кількістю води, що поступає змінюється абразивну дію тканини. При великій кількості води вона діє як мастило, і камінь піддається тільки слабкого абразивного впливу. При меншому її кількості камінь більш щільно прилягає до абразивної тканини і обробляється швидше.
Для сендінга можуть використовуватися диски, барабани і стрічки, а також шліфовальніка з твердою поверхнею.
Диск - це сталевий диск з центральною бобишкою з різьбленням, що дозволяє закріплювати диск на валу шпинделя. Диск покритий губчастої гумою, а зверху приклеєна тканину за допомогою засихає липкого клею (для простоти заміни). Диск може мати увігнуту або вигнуту поверхню, що полегшує обробку криволінійних поверхонь каменю. У деяких типах дисків тканину просто натягнута на ободок, що дозволяє їй прогинатися під тиском каменю і автоматично підлаштовуватися під форму кабошона.
Барабан (рис. 6.3) забезпечений плоскою губчастої гумовою підкладкою, має паз, куди вставляються кінці смужки абразивної тканини і затиск для їх міцного закріплення. Звичайне робоче положення - вертикальне, хоча він може працювати і в інших положеннях.
Стрічка для сендінга складається з «нескінченною» стрічки абразивної тканини, одягненою на два покритих гумою шківа, розташованих на відстані один від одного.
Шліфовальніка з твердою поверхнею, як правило, використовуються для обробки дуже твердих каменів (хризоберил, корунд, жадеїт, родоніт). Шліфовальніка роблять у формі дисків і планшайб - гладких або забезпечених канавками. Канавки призначені для обробки кабошонов різної кривизни. Найбільш відповідний матеріал - щільне дерево. Воно добре утримує шліфувальний і полірувальний порошки.
Операції шліфування й полірування з використанням вільних абразивів або полірувальних порошків, що наносяться у вигляді водних і масляних суспензій, можуть виконуватися на дерев'яних колах або шпулях. Шпули виготовляються з центральної частини стовбура або товстої бічної гілки. Виточують їх на токарному верстаті в формі простого барабана, або в формі шпулі з канавками різної кривизни (рис. 6.4). По центру просверливается наскрізний отвір паралельно волокнам. Шпуля кріпиться на обертовому валу двигуна.
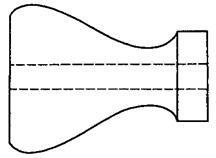