Устаткування для призводства OSB (ОСП):
Область розробки і виготовлення пресувальних систем для виробництва плитних матеріалів на основі дерева, в сучасних умовах вимагає комплексного підходу в багатьох областях - технології, хімії та фізики. Сучасні лінії пресування - це високотехнологічні підприємства обладнані інноваційною технікою. Досить сказати, що лінія ContiRoll (безперервного способу пресування) для виробництва плит OSB (ОСП). коштує 60-70 млн. Євро, без монтажу, налагодження та запуску. У світі існують дві фірми, які стали синонімами гідравлічного преса у виробництві древ. плит. Це німецькі компанії Зімпелькамп (Siempelkamp) і Діффенбахер (Dieffenbacher). Пресами цих двох компаній обладнано переважна більшість великих заводів з виробництва OSB. як в Європі, так і в Північній Америці.
Основні етапи процесу виробництва
Схема на прикладі лінії фірми «Dieffenbacher»:
I. Доставка і сортування колод
Насамперед на завод доставляється деревину - круглі лісоматеріали. Осика, тополя, сосна, клен - найбільш ходові породи, які закуповують виробники OSB. Як тільки сировину прибуло на майданчик заводу, його відразу розвантажують за допомогою автонавантажувачів, спеціально призначеного гідроманіпулятора або крана з грейферним захватом.
II. Окаріваніе колод на ланцюговому транспортері
Частина деревини складають на біржі сировини, частина відразу пускають у виробництво. Далі потрібний обсяг сировини на заданий час занурюють в пропарювальні басейни, після чого окорівают. Якщо деревина недавно зрубана і незамерзла, то її відразу пускають на окорке і далі в стружкових верстат.
III. Розпиляні на короткі заготовки колоди завантажуються в стругальну установку, яка розщеплює їх на стрічкову стружку у напрямку деревного волокна
Розміри стружки задаються відповідно до процесом технологічної обробки. Стружка має рівномірну товщину. Більшість заводів використовує суміш стружки розмірами від 75 до 150 мм в довжину і 15-25 мм в ширину. А от середня товщина стружки зменшилася з 0,8 мм, яку робили в 80-х роках, до 0,6 мм в наші дні. Частина, що залишилася дрібна стружка і кора служать паливом для енергетичної системи заводу.
IV. Сушка і сортування отриманої стружки
Сира стружка після стружкової верстата накопичується в спеціальних бункерах, з яких порціями подається в барабан сушильної установки. Концепція конвеєрної сушки OSB -стружкі була запозичена з харчової промисловості - технології виробництва картопляних чіпсів. Потік стружки просушується рівномірно, і при цьому температура на виході з сушарки невисока. Це дуже важлива обставина, тому що чим нижче температура на виході сушарки, тим вище пожежна безпека процесу і нижче емісія забруднюючих речовин (летких органічних сполук). Після сушіння стружку сортують, щоб відокремити занадто дрібну і занадто велику стружку від основного потоку.
V. Відсортована стружка змішується з воском і водостійким сполучною (зазвичай фенольним або ізоціанатні полімерним сполучною речовиною)
Ці водостійкі і стійкі до впливу окропу сполучні речовини забезпечують внутрішню міцність, жорсткість і вологостійкість панелі. Змішувач являє собою циліндричний барабан, який обертається із заданою швидкістю. Всередину барабана по окремих трубопроводах подаються парафін, смола і інші компоненти клею. Але, незалежно від того, який парафін використовується, сирої або емульгований, він вводиться перед смолою. Для внутрішнього та зовнішнього шарів найчастіше використовують різні типи смол - для зовнішнього шару може подаватися в рідкому або порошкоподібному вигляді, в той час як смола внутрішнього шару може бути, крім того, фенолформальдегидной або ізоціанатні. Цікаво, що обертовий диск, який розподіляє смолу всередині змішувача, був запозичений з обладнання для фарбування автомобілів і став прямо-таки революційним відкриттям в технології осмоления стружки.
VI. Формування та укладання стружки
Формує станція має вбудованими вагами, магнітами, притискними вальцями, а також системою двостороннього підрівнювання крайок килима з поверненням зайвої стружкової маси в бункер середнього шару. Орієнтує головка стружки зовнішнього шару чимось дуже схожа на фермерські борони. Вона складається з ряду круглих дисків, які направляють падаючу вниз стружку, вирівнюючи її паралельно довгій стороні килима. Орієнтує головка стружки внутрішнього шару складається з роликів в формі зірки з плоскими лопатями. Обертаючись, вони вирівнюють стружку паралельно ширині килима, перпендикулярно до напрямку руху конвеєра. Стружка в поверхневому шарі плити зазвичай укладається уздовж довгої сторони панелі (для надання більшої згинальної міцності і жорсткості в поздовжньому напрямку). Два або три внутрішніх шару зазвичай укладаються поперек поверхневого шару. Для виловлювання сторонніх включень служить котушковий металошукач. Попередня подпрессовка килима у виробництві плит OSB не потрібно. Для відсіву включень і непридатною стружки передбачений спеціальний бункер.
VII. пресування
Пресування відбувається при дуже високій температурі і тиску до утворення твердої щільною будівельної панелі. Завдання преса ущільнити стружкових килим і підвищити температуру всередині нього до заданого значення. Температура затвердіння смоли знаходиться в проміжку між 170-200 ° С. Ширина сталевої стрічки преса - 3 м, товщина - 3 мм. Сталеві стрічки нагріваються котлом потужністю 8 МW за допомогою термомасла до температури 220 ° С. B передній зоні ущільнення тиск пресування досягає 5 N / мм2. Розрахунковий час затвердіння становить 9 секунд на кожен міліметр товщини плити. Тиск і температуру необхідно заміряти протягом 3-5 хвилин. Пил і відпрацьована пара після преса видаляються вентилятором вологим способом.
VIII. Фінальна (остаточна) доведення
Після пресування нескінченне полотно плити переміщається по рольгангу, де відбувається перевірка на геометричне відповідність і обрізка поздовжніх крайок. Для поперечного розкрою полотна на плити потрібної довжини використовується спарена діагональна пила. Охолодження плити відбувається на віялових охолоджувачах. В кінці виробничої лінії за допомогою відповідних контрольно-вимірювальних приладів перевіряються товщина і вага плит, а також наявність в них розшарувань чи інших дефектів. Після пресування плити ще якийсь час витримують на складі для того, щоб дати можливість клею повністю затвердіти і полимеризоваться. Як правило, час остаточної витримки становить від 12 до 48 годин.
Великоформатні плити складаються в стопи і перевантажуються за допомогою штабелеукладчіка. Для розкрою плит, на стандартний формат, використовується високопродуктивна круглопильного установка. Відформатовані плити надходять на фрезерну установку, де їх кромки профілюються. Багато Північноамериканські виробники захищають кромки OSB-плит від впливу вологи. Для цього перед тим, як упакувати штабель плит, на його бічні поверхні розпорошується фарба з низькою проникаючою здатністю, яка забиває пори і ущільнює торці плит.
Готова продукція передається на пакувальну лінію
Розвиток технології виробництва плит OSB. Детальний опис типової технології, яка найбільш поширена в Північній Америці при виробництві OSB. далі.
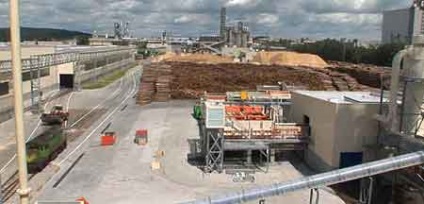
Сира стружка після стружкової верстата накопичується в спеціальних бункерах, з яких порціями подається в барабан сушильної установки. Концепція конвеєрної сушки.