Схема розташування обладнання.
3. Поняття про калібрування валків.
4. Якість продукції та основні деффекти.
5. Перспективи розвитку способу виробництва.
6. Техніко-економічні показники.
Холодна прокатка в порівнянні з гарячою має дві великі переваги: по-перше, вона дозволяє виробляти листи і смуги товщиною менше 0,8-1 мм, аж до декількох мікрон, що гарячої прокаткою недосяжно; по-друге, вона забезпечує отримання продукції більш високої якості за всіма показниками - точності розмірів, обробці поверхні, фізико-механічними властивостями. Ці переваги холодної прокатки обумовили її широке використання як в чорній, так і в кольоровій металургії.
Разом з тим необхідно відзначити, що процеси холодної прокатки є більш енергоємними, ніж процеси гарячої прокатку При холодної деформації метал зміцнюється (наклепивается), в зв'язку з цим для відновлення пластичних властивостей доводиться проводити відпал. Технологія виробництва холоднокатаних листів включає велику кількість переділів, вимагає застосування складного і різноманітного обладнання.
В даний час частка холоднокатаних листів в загальній масі тонколистового прокату становить близько 50%. Виробництво холоднокатаних листів, смуг і стрічок продовжує інтенсивно розвиватися. Основну масу (приблизно 80%) холоднокатаних листів становить низьковуглецевий конструкційна сталь товщиною 0,5-2,5 мм, шириною до 2300 мм. Таку тонколистовую сталь широко використовують в автомобілебудуванні, тому часто її називають автолист. Методом холодної прокатки виробляють майже всю жесть - продукцію, що йде в великих кількостях для виготовлення харчової тари, зокрема консервних банок. Матеріалом для жерсті також служить низьковуглецева сталь, але в більшості випадків жесть випускають із захисним покриттям, найчастіше - олов'яним. Жесть прокочують у вигляді смуг товщиною 0,07-0,5 мм, шириною до 1300 мм. До поширених видів холоднокатаної продукції також відносяться: декапируют (травлення і відпалений сталь, застосовувана при виробництві емальованого посуду та інших виробів з покриттями), покрівельний лист (часто випускається оцинкованим), низьколеговані конструкційні стали. Особливо слід відзначити дві важливі групи легованих сталей - корозійностійкої (нержавіючу) і електротехнічну (динамную і трансформаторну).
У кольоровій металургії холодна прокатка застосовується для отримання тонких смуг, листів та стрічок з алюмінію і його сплавів, міді і її сплавів, нікелю, титану, цинку, свинцю і багатьох інших металів. Найменшу товщину має фольга. Наприклад, алюмінієва фольга випускається у вигляді смуг мінімальною товщиною 0,005 мм, шириною до 1000-1500 мм. Різноманітність сортаменту холоднокатаної листової продукції забезпечується застосуванням прокатних станів різної конструкції, з дуже різними технічними характеристиками і рівнями продуктивності.
1. Виробництво електротехнічної листової сталі
Електротехнічна сталь умовно ділиться на динамную і трансформаторну. Сама назва цих сталей вказує на області їх застосування. Динамная сталь використовується в основному для виготовлення електромоторів (динамо-машин) і генераторів, трансформаторна - для виготовлення трансформаторів і різних електромагнітних приладів. Електротехнічні стали працюють в умовах перемагнічування змінним струмом і повинні мати низькі ватні (гістерезисна) втрати і високу магнітну індукцію.
Опір деформації і пластичність електротехнічних сталей сильно залежать від процентного вмісту кремнію. Збільшення його кількості в стали призводить до підвищення опору деформації і різкого падіння пластичності. Тому холодна прокатка трансформаторної сталі здійснюється значно важче, ніж прокатка динамної.
2. Технологічний процес та обладнання табору.
Схема розташування обладнання.
Холодна прокатка трансформаторної сталі на вітчизняних заводах здійснюється на одноклітьових реверсивних (рис.1), трехклетевих і пятиклетевом безперервних і багатовалкових станах.
Прийняті при холодної прокатки трансформаторної стали інтенсивні обтиску в першому пропуску (35-45%) в результаті значної деформації забезпечують нагрівання смуги до 100-150 ° С, що сприятливо впливає на процес прокатки рулону в подальших пропусках, так як нагрів смуги до такої температури ( в результаті деформації) призводить до значного зниження опору деформації при прокатці.
Для знежирення смуги після холодної прокатки можуть бути застосовані різні способи, в тому числі електролітичний, хімічний, ультразвукової.
В даний час для знежирення рулонів хімічним способом застосовують розчини наступного складу, г / дм3:
Сода кальцинована. 50
Каустична сода. 5
Емульгатор ОП-7. 3
Вирішальний вплив на якість холоднокатаної трансформаторній стали надає термічна обробка - попередній, проміжний і остаточний високотемпературний отжиги.
Зміни магнітних характеристик трансформаторній стали при термічній обробці викликаються: а) зміною форми вуглецю (кращі властивості виходять, коли вуглець знаходиться у вигляді графіту); б) вигоранням вуглецю і дегазацією металу; в) збільшенням розмірів зерен; г) рекристалізацією наклепанной стали (при якій відбувається зняття внутрішніх напружень, зміна величини зерен і їх орієнтація),
Проміжний відпал рекристалізації холоднокатаної трансформаторної сталі необхідний для зниження твердості стрічки після першого переділу холодної прокатки. Досвід роботи показав, що такий отжиг трансформаторної сталі в колпакових печах з різною захисною атмосферою практично не впливає на зниження вмісту вуглецю в стали.
Високотемпературний відпал холоднокатаної трансформаторної
стали проводиться в колпакових печах при 1100-1200 ° С у вакуумі або в сухому водні.
При високотемпературному відпалі відбувається укрупнення зерен фериту, коагуляція включень, зміна форми вуглецю і зменшення кількості шкідливих домішок в стали.
В останні роки для обезуглероживания і остаточного відпустки трансформаторній стали будували баштові і горизонтальні печі, які характеризуються високою продуктивністю, що дозволяють проводити значітельноеобезуглерожіваніе металу.
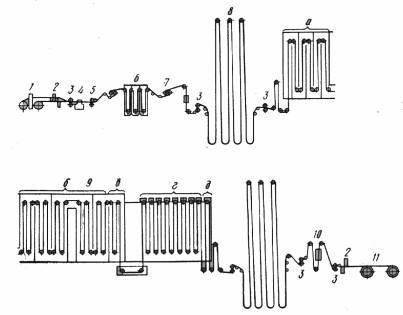
Мал. 21. Лінія термічної обробки трансформаторної сталі з баштової піччю;
а - камера нагріву; б - камера витримки; в - камера регульованого охолодження;
г - камера прискореного охолодження; д - камера обдування; 1 - разнативатель;
2 - гільйотинних ножиць; 3 - тягнуть ролики; 4 - зварювальний машина; 5 - струменево-щіткові машини; З - ванна електролітичного знежирення; 7 - сушарка;
8 - петльові ями; 9 - баштова піч; 10 - установка Для нанесення захисного покриття; 11 - моталка.
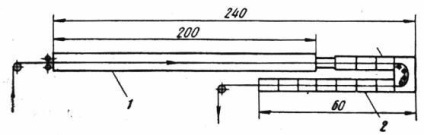
На рис. 21-24 показані агрегати для термічної обробки трансформаторної сталі, а на рис, 132 - відділення електроізоляційного покриття цеху холодної прокатки трансформаторної сталі.
Мал. 22. Протяжна піч для нормалізації рулонів трансформаторній стали:
1, 2 - камери нагріву і охолодження відповідно.
У сучасному виробництві підкату з трансформаторної
стали передбачається технологічний переділ зливків великий маси в сляби на блюмінгах або слябінгах або отримання слябів з установок безперервного розливання сталі з використанням сталі, що містить 2,9- 3,2% Si. При виробництві катаних слябів злитки в колодязні печі завантажуються гарячим всадом з температурою поверхні зливків під час посадки 800-950 ° С. Тривалість нагріву зливків в залежності від температури всадив 7-10 год, маючи на увазі, що не менше 75% загального часу має витрачатися на ловлення злитків при температурі видачі. Прокатані сляби в потоці обтискних станів піддаються зачистці на машинах вогневого зачищення, після чого піддаються термічній обробці (відпалу) при температурі 750 ° С із завантаженням слябів в піч гарячим всадом. Охолодження садки після відпалу має бути уповільненим зі швидкістю 40-50 ° С. Регламентований режим нагріву і охолодження слябів кременистої стали виключає утворення тріщин через значних термічних напруг.
При необхідності додаткової зачистки поверхневих дефектів на слябах її здійснюють на охололи слябах на Ад'юстаж.
Сляби перед прокаткою на широкосмуговому стані нагріваються в залежності від хімічного складу трансформаторної сталі до 1200-1400 ° С. Перевагою використання напівнеперервних станів для прокатки рулонного підкату є можливість
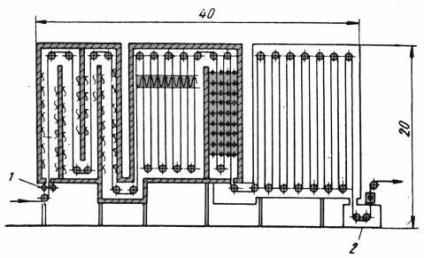
Мал. 23. Баштова електрична піч для обезуглероживания і відпалу трансформаторної сталі камерами нагрівання, витримки та регульованого охолодження:
1 - роликовий затвор; 2 - бак для замочування у воді
регулювання числа проходів і величини обтиску в залежності від хімічного складу стали, температури сляба і товщини рулонного підкату. Перед чистової групою клітей температура розкату товщиною 18-25 мм повинна бути в межах 950-1050 ° С, температура кінця прокатки не нижче 850 ° С і температура смуги при змотування на моталку не вище 600 ° С.
Товщина рулонного гарячекатаного підкату визначається режимом його прокатки на стані холодної прокатки і конструкцією стану. Зазвичай товщина підкату дорівнює 2,5 мм.
3. Матеріал і профілювання валків станів холодної прокатки.
Валки станів холодної прокатки відчувають вплив дуже високих контактних тисків, які, як правило, в декілька разів перевищують величину межі текучості деформованого металу при кімнатній температурі. У зв'язку з цим валки повинні мати відповідну міцність і твердістю. Друге, що необхідно враховувати, - це підвищені вимоги до якості поверхні холоднокатаних листів. Щоб задовольнити їх, валки повинні мати певний мікрорельєф поверхні; тим більше неприпустимі різні макроповрежденія і дефекти.
Робочі валки станів холодної прокатки виготовляють з високовуглецевих сталей, легованих хромом, ванадієм, вольфрамом та іншими елементами. Найчастіше застосовують валки з сталей 9Х, 9ХФ, 9х2, 9Х2В, 9Х2СФ, 9Х2МФ, 9Х2СВФ, 60Х2СМФ. Після відливання і кування валки піддаються складної термічній обробці, на заключній стадії - поверхневому загартуванню з відпусткою. Твердість бочки робочих валків зазвичай знаходиться в межах 90-102 HSD) (по Шору), твердість шийок 30-55 HSD. Товщина загартованого поверхневого шару валків повинна бути не менше 3% радіуса валків. Для робочих валків великого діаметра (близько 500-600 мм) раціональна товщина загартованого шару складає приблизно 10-12 мм. В останні роки робочі валки багатовалкових станів, призначених для прокатки особливо твердих і тонких стрічок, іноді виготовляють з твердих металокерамічних сплавів на основі карбіду вольфраму (85-90% карбіду вольфраму і 10-15% кобальту). Методом гарячого пресування і спікання вдається отримувати цільні валки діаметром до 80 мм, довжиною до 1500 мм. Твердість таких валків досягає 115-125 HSD. Їх зносостійкість в 30-50 разів перевищує стійкість валків з легованих сталей. Завдяки дуже високому модулю пружності, Карбід вольфрамові валки сплющуються в осередку деформації в 3 рази менше, ніж сталеві валки. Разом з тим треба мати на увазі, що Карбід вольфрамові валки мають велику вартість і підвищену крихкість. Останнє ускладнює їх використання при ударному навантаженні і значних прогинах.
Опорні валки бувають трьох типів: цельнокование, литі і складові (бандажірованного). Найбільш распросгранени цельнокование опорні валки. Їх виготовляють з сталей 9Х, 9х2, 9ХФ, 75ХМ, 65ХНМ. Для виготовлення осей складових валків використовують більш прості, менш леговані марки сталей: 70, 55х, 50ХГ, 45ХНВ, 45ХНМ. Бандажі за своїм хімічним складом відповідають цельнокование валянням. Твердість бочки опорних валків зазвичай становить 60 85HSD.
На практиці встановлено, що працездатність нових валків, особливо робочих, які пройшли складну термічну обробку, значно підвищується при вилежуванні їх протягом 5-6 місяців; це сприяє зняттю внутрішньої напруги в валках.
Важливою операцією є підготовка поверхні валків до прокатці. Застосовуються робочі валки зі шліфованої, полірованої і насеченной поверхнею. Шліфування валків до 7-9 класу чистоти поверхні є найбільш поширеною операцією; вона виконується на спеціальних вальцешліфувальних верстатах. Інструментом для обробки служать шліфувальні круги з карбіду кремнію, карбіду бору, електрокорунду, синтетичних алмазів і інших матеріалів. При шліфуванні спочатку проводиться обдирання з метою видалення накопичених поверхневих дефектів, а потім - під чистове обробка з профілюванням бочки валка і доведенням поверхні до заданого класу чистоти. Знімання поверхневого шару за одну планову перешліфовці (при відсутності глибоких ушкоджень) для робочих валків становить приблизно 0,05-0,1 мм на діаметр.
Поліровані робочі валки 10-12 класу чистоти поверхні застосовуються на багатовалкових станах, зокрема при прокатці нержавіючої сталі, а також дуже часто при прокатці деяких видів кольорових металів, наприклад фольги. Полірування здійснюється також на вальцешліфувальних станах із застосуванням дрібнозернистих корундових кіл на бакелітовій зв'язці з графітовим наповнювачем, графітових і повстяних кіл. На поверхню повстяних кіл наноситься полірувальна паста типу ГОІ.
Насічені, шорсткі робочі валки застосовуються в першій і останній клітях безперервних станів: в першій кліті - для поліпшення умов захоплення, в останній кліті - з метою запобігання зварювання витків рулонів або аркушів в пачках при відпалі. Насічені валки застосовуються і в деяких інших випадках, коли необхідно отримати шорстку поверхню продукції. Операція насічки виконується на спеціальних дробоструминних установках. Робочим тілом служить чавунна або сталева колота дріб, іноді різана сталевий дріт (січка).
В даний час для отримання високоякісної, зносостійкої поверхні валків з будь-вимагається шорсткістю все більш широко використовується електроїськровая і електроерозійна обробка.
Під дією великих зусиль, що виникають при холодної прокатки, валки зазнають значну пружну деформацію: вони прогинаються і