Ремонт машинно-тракторного парку в майстерні Володимирській МТС
У IV кварталі 1955 року в майстерні (побудованої за проектом тисячі шістсот шістьдесят два) Володимирській МТС Володимирській області був застосований вузловий метод ремонту машинно-тракторного парку. Вузловий метод був розроблений на основі типової технології.
У майстерні цієї МТС одночасний ремонт різних марок тракторів, комбайнів та інших сільськогосподарських машин проводиться в одному виробничому потоці на суміщених робочих місцях. Ремонтний процес розбитий на п'ять груп ремонтних робіт.
Для виконання ремонтних робіт організовано 32 суміщених робочих місця.
Для виконання ремонтних робіт організовано 32 суміщених робочих місця.
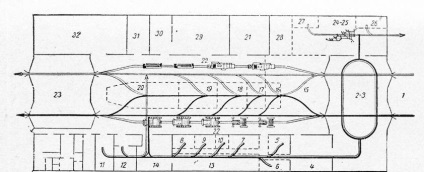
Мал. 2. План майстерні з нанесенням суміщених робочих місць і вантажопотоків.
Номери робочих місць:
1 - доставка, зовнішня очистка і миття машин; 2 - розбирання машин, мийка деталей і вузлів; 3 -Контрольний огляд вузлів і дефектовка деталей; 4 - КОМПЛЕКТУВАЛЬНЕ відділення; 5 - ремонт блоку; 6 - ремонт головок циліндрів і клапанного механізму; 7 - розбирання; 8 - розбирання, ремонт і складання масляних насосів, фільтрів і серво-гідромеханізму; 9 - розбирання, ремонт і складання муфт і картерів зчеплення, вентиляторів і редуктора двигуна комбайна; 10 розбирання, ремонт і складання пускового. двигуна і редуктора; 11 - розбирання, ремонт і складання дизельної паливної апаратури і карбюраторів; 12 - розбирання, ремонт електрообладнання; 13 - збірка основного двигуна; 14 - обкатка, випробування і контрольний огляд двигуна; 15 - ремонт рам; 16 - ремонт бортових фрикційних, диференціалів і редукторів; 17 - ремонт коробок передач; 18 - ремонт ходової частини; 19 - ремонт переднього моста, рульового управління і вузлів молотильної частини комбайна; 20 - ремонт кабін, крил, капотів і вузлів молотильної частини комбайнів; 21 - мідницьким-заливальні роботи, ремонт радіаторів, баків, воздухоочистителей і трубок; 22 - складання тракторів і комбайнів; 23 - обкатка, контрольний огляд і забарвлення машин; 24-25 - ремонт робочих вузлів сільськогосподарських машин; 26 - ремонт допоміжних вузлів сільськогосподарських машин; 27 - ремонт рам, складання та регулювання сільськогосподарських машин; 28 - оббивно-теслярські та шорні роботи; 29 - ковальські роботи; 30 - зварювальні роботи; 31 - інструментально-роздавальна комора; 32 - слюсарно-механічні роботи.
На відміну від типової технології ремонт тракторів різних марок прийнятий в одному виробничому потоці, на суміщених робочих місцях.
Як видно, кількість суміщених робочих місць при організації ремонту в одному потоці дорівнює 32 замість 48 при ремонті в різних потоках (рис. 2).
Процес ремонту машин, як і зазвичай, починається з зовнішньої очищення і мийки, потім слід розбирання машин на вузли і деталі.
Однак при цьому не розбирають вузли або агрегати, які не потребують ремонту, і не допускають знеособлення деталей.
У майстерні є вантажопотоки вузлів і деталей, придатних до постановки без ремонту; вузлів і деталей, що вимагають ремонту; деталей, що підлягають вибракуванню; нових або відремонтованих вузлів і деталей.
Деталі й вузли, придатні до постановки на машини без ремонту, після дефектації (робочі місця 2 і 3) направляються на робочі місця (5, 6, 7, 8, 9, 10, 11, 12) по ремонту вузлів двигунів і по ремонту вузлів шасі (15, 16, 17, 18, 19, 20 і 21). Потім вони йдуть на робоче місце (13) по збірці двигунів або на робоче місце (22) по збірці машин.
Вузли, що вимагають ремонту, з дефектувальних відділення доставляються відразу на робочі місця по ремонту вузлів двигунів і шасі машин. Тут розбирають вузли, миють, де-фект і ремонтують деталі, збирають і потім проводять контрольний огляд вузлів.
Деталі, які потребують ремонту, після дефектації направляються через КОМПЛЕКТУВАЛЬНЕ відділення на робочі місця по ремонту та виготовленню деталей (28, 29, 30, 31 і 32).
Деталі, що підлягають вибракуванню, здаються на склад металевого брухту.
Відремонтовані деталі, а також нові зі складу запасних частин через КОМПЛЕКТУВАЛЬНЕ відділення доставляються на робочі місця по ремонту вузлів двигунів і шасі.
Відремонтовані вузли двигунів надходять на робоче місце № 13, де здійснюється складання двигунів. Зібрані двигуни проходять випробування і контрольний огляд і потім направляються на робоче місце № 22. На це ж робоче місце приходять вузли шасі. З цих вузлів і двигунів тут збирають машини.
Зібрані машини після обкатки на робочому місці 23 оглядають і забарвлюють.
Для ремонту сільськогосподарських машин організовані робочі місця № 24, 25, 26 і 27.
Для більш раціонального розміщення технологічного обладнання довелося дещо змінити планування відділень і робочих місць.
За існуючою плануванні мотороремонтний відділення займає 67 м2. Фактично для розміщення тільки одних робочих місць потрібно 76 м2, а якщо врахувати проходи, - 100 м2.
У майстерні, побудованої за проектом 1662, передбачено дві ремонтні лінії, за якими на візках повинні рухатися трактори, автомашини і комбайни. Технологічне обладнання для ремонту вузлів шасі в цьому випадку має розташовуватися уздовж стін, т. Е. Між стінами і ближнім рейкою ремонтної лінії. Однак практично так розмістити обладнання дуже важко через малу ширину цієї ділянки майстерні.
У Володимирській МТС змінили планування майстерні. Мотороремонтний відділення розширили, перенісши випробувальне відділення в мідницьким-радіаторне. Мідницьким-радіа-торні відділення утворили за рахунок вулканізаційного і оббивно-плотницкого відділень. Оббивно-теслярські відділення перенесено в відділення по ремонту сільськогосподарських машин, а вулканизационное відділення - в гараж для автомашин.
Мотороремонтний відділення також можна розширити за рахунок скорочення площ, займаних дефектувальних і комплектувальних відділеннями. Робочі місця №15, 16, 17, 18, 20 по ремонту вузлів шасі ремонтно-монтажного відділення для тракторів і комбайнів розташували на центральній ділянці майстерні, розширивши на 1,4 м площадку між двома ремонтними лініями.
У мотороремонтному і ремонтно-монтажному відділеннях розмістили по сім робочих місць, у відділенні ремонту сільськогосподарських машин - чотири робочих місця, в раз-борочно-мийному і дефектувальних відділенні - три, в куз-нечно-зварювальному відділенні-два і в інших відділеннях - по одного робочого місця.
З 103 видів технологічного обладнання, необхідного для організації об'єднаних робочих місць, 26 було розроблено і виготовлено заново і 11 вдосконалено.
Особливий інтерес представляє серія стендів і пристосувань по ремонту і регулюванню муфт зчеплення, коробок передач, головок блоку циліндрів, картерів головного зчеплення і інші. Це обладнання значно полегшує працю і до 65% підвищує продуктивність праці робітників на ремонті.
Після перепланування відділень і відповідного. розташування робочих місць повний комплект технологічного обладнання було встановлено на площі 185 м2, що склало 15% всієї корисної площі майстерні. Для організації всіх робочих місць потрібно 858 м2, або 71% всієї корисної площі майстерні. Майже одна третина площі майстерні залишилася під проїздами і проходами.
Організація об'єднаних робочих місць і проведені удосконалення в технологічному процесі і устаткуванні не тільки дозволили більш раціонально використовувати площу майстерні, а й полегшили працю робітників, підвищили його продуктивність і дали можливість поліпшити якість і знизити собівартість ремонтних робіт.
Розглянемо більш докладно кілька прикладів з організації об'єднаних робочих місць в майстерні Володимирській МТС.
У разборочно-мийному і дефектувальних відділеннях на площі 196,6 м2 розташовані робочі місця № 1, 2 і 3.
Робочі місця № 1 і 2 організовані для робіт з доставки машин на ділянку зовнішньої очищення їх, мийки і розбирання.
Для виконання зазначених робіт тут розміщено необхідне технологічне обладнання: насос РВ-ОЮ1 високого тиску (рис. 3), два стелажа для деталей Р0-2804, слюсарний верстак М0-5001А 3, три монтажних столу М0-5004 4, вдосконалена машина МУ-1 для мийки деталей, шафа РВ-3721 б для пристроїв, три бачка для збору відпрацьованих масел і два каналізаційних колодязя 9.
Для доставки тракторів на місце розборки є силова електроустановка, що складається з фрикційної електролебідки, переносного блоку, закріпленого на гаках,
які приварені до рейок, і троса діаметром 16 мм і довжиною 80 м. Щоб уникнути стиснення рейок, в місцях їх кріплення уварені розпірки.
Мийна машина МУ-1 була значно вдосконалена, змінений також спосіб підігріву води.
З цією метою в мийній машині (рис. 4) зроблена друга двері, були також виготовлені шляху для викочування візка під завантаження деталей. Під шляхами прокладені лотки, що забезпечують стік содового розчину і забрудненої води безпосередньо в ванни. Обидві ванни використані тільки для підігріву содового розчину і з'єднані між собою трубою.
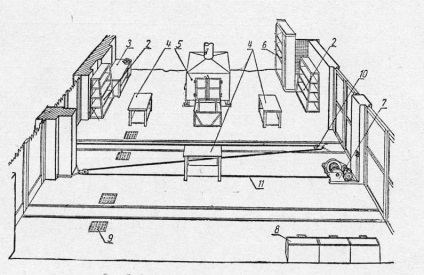
Мал. 3. Общии вид робочих місць № 1 і 2
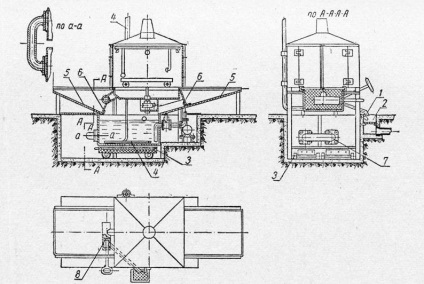
Мал. 4. Схема вдосконаленою мийної машини:
1 - труба для відводу в каналізацію грязвого содового розчину і промивної води; 2 - колодязь для брудного содового розчину; 3 - електроплитка для підігріву содового розчину; 4 - змійовик; 5 - лоток; 6 - сітка; 7 - труба; 8 - засувка.
Труба, розташована вгорі ванни і виведена в водостічний поглинає колодязь, підтримує необхідний рівень розчину.
Промиті содовим розчином деталі обмиваються водою з водопроводу, яка стікає в каналізацію. Стік води регулюється засувками 8.
Гарячі деталі добре обмиваються водою і охолоджуються, що дає можливість відразу їх переносити на робочі місця.
Ванна підігрівається парою або електрикою залежно від пори року. У тепліше час, коли відсутня пар, застосовується підігрів за допомогою двох електропліток 3, змонтованих на висувних візках.
У зимовий час содовий розчин нагрівається парою за допомогою змійовиків, змонтованих в ваннах.
Для виконання контрольного огляду вузлів і дефектації деталей було організовано робоче місце №3.
На цьому робочому місці машини розбирають на вузли і деталі, а також проводять гідравлічне випробування блоків і головок циліндрів.
При розбиранні машин вузли попередньо оглядають, маркують і направляють на відповідні робочі місця, де проводиться дефектовка і встановлюється вид та обсяг ремонту. Результати дефектації заносяться в спеціальну відомість.
Відомість дефектів служить основним документом для складання нарядів на ремонт вузлів і деталей і видачу запасних частин.
При визначенні дефектів, виду та обсягу ремонту в майстерні користуються спеціальними приладами, пристосуваннями і вимірювальними приладами, наявними не тільки на робочому місці № 3, але і на інших робочих місцях.
Так, наприклад, дефектовка шатунно-поршневих груп, масляних насосів, муфт зчеплень, коробок передач, головок блоку, пускових двигунів, масляних фільтрів, паливної апаратури, карбюраторів, бортових фрикційних та інших вузлів проводиться на відповідних робочих місцях.
Робоче місце № 3 займає 32 м2. На цьому робочому місці встановлені вдосконалений універсальний стенд КП-0406 для гідравлічного випробування блоків, головок блоків, випускних і впускних труб, стелаж для деталей, ящик для вилучених деталей, шафа РВ-0509 для приладів, три столи М00508 для дефектації, повірочна плита з центрами , тумбочка і стіл.
На універсальному стенді КП-0406 випробовуються блоки зазвичай з вивернутими шпильками кріплення головок.
На викручування шпильок витрачається багато часу. Для того щоб уникнути викручування шпильок, в змінних верхніх плитах 1 (рис. 5) для головок блоку і блоків свердлити отвори відповідно розташуванню шпильок. Шпильки повинні вільно проходити через отвори в плиті при її установці на блок.
Для щільного притиснення плити до площини блоку застосовуються три спеціальні підставки, які встановлюються на шпильки зверху плити і притискаються гвинтами притискних кронштейнів.
На малюнку 6 показаний загальний вигляд робочого місця № 6 по розбиранню, ремонту і складання головок циліндрів і клапанного механізму.
Це робоче місце розташоване в лівому кутку мотороремонтного відділення. Воно займає площу 9,2 м2. Обладнання робочого місця № 6 складається з монтажного столу МО-5004, стелажа для деталей, верстата М-2 (ХП-1408) 3 для притирання клапанів, нового-пристосування до верстата М-2 для ремонту головок циліндрів, приладу КП-0507 для перевірки пружності клапанних пружин, верстата Х0-1407 6 для шліфування клапанів, слюсарного верстата 7, слюсарних лещат 8.
Розташований таким чином комплект обладнання полегшує працю робітника і підвищує його продуктивність на 170%. Це досягається тим, що на верстаті М-2, обладнаному новим пристосуванням 4, можна виробляти, крім притирання клапанів, розбирання головок циліндрів, шарошку клапанних гнізд, розгортання направляючих клапанів, промивання головок циліндрів, перевірку якості притирання і складання головок циліндрів двигунів тракторів СХТЗ , «Універсал», АСХТЗ-НАТІ, ДТ-54, КД-35, ХТЗ-7, С-80 і двигунів автомашин ГАЗ-ММ, «Перемога», ГАЗ-51, ЗІС-5 і ін.
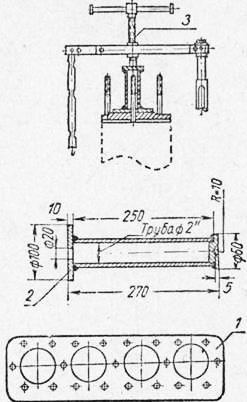
Мал. 5. Пристосування до стенду КП-0406 для випробування блоків з їх шпильками.
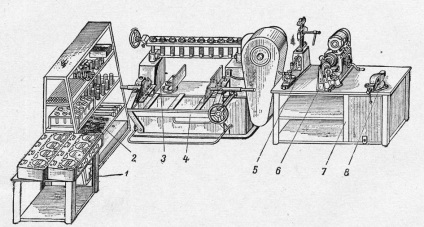
Мал. 6. Загальний вигляд робочого місця № 6.
Крім того, на робочому місці № 6 проводяться випробування клапанних пружин, шліфування клапанів, ремонт штанг штовхачів та інших деталей клапанного механізму.
Робоче місце № 17 (з розбирання, ремонту і складання коробок передач) розташоване в центрі ремонтно-монтажного відділення для тракторів і комбайнів і займає площу 9,8 м2. Обладнання робочого місця складається з слюсарного верстата на одного робітника, двох нових стендів для розбирання, ремонту, складання і обкатки коробок передач, монтажного столу МО-5004 і стелажа для деталей.
На новому стенді можна виконувати всі ремонтні роботи, в тому числі і відновлення посадочних місць корпусів коробок передач тракторів СХТЗ, «Універсал», ДТ-54, КД-35, АСХТЗ-НАТІ, комбайнів С-4, автомобілів ГАЗ-ММ, ГАЗ- 51, ЗІС-5. Цей стенд можна легко пристосувати для ремонту інших коробок передач, виконаних в окремому корпусі.
За таким принципом були організовані і інші робочі місця в майстерні Володимирській МТС.
У майстерні при випуску одного трактора чи комбайна в день працюють 37 постійних робочих. Розподіл робочих по відділеннях дано в таблиці 3.
Із загальної кількості робітників, зайнятих на роботі в майстерні МТС, виконували зварювальні, ковальські, механічні та інші роботи, пов'язані з виготовленням і ремонтом деталей, 10 осіб. Решта 27 осіб проводили розборку, ремонт і складання вузлів машин, а також інші демонтажні і монтажні роботи.
Нова організація виробничого процесу ремонту машинно-тракторного парку вузловим методом відкриває такі додаткові резерви: - по-перше, дає можливість ремонтувати різні марки машин в одному виробничому потоці на суміщених робочих місцях; - по-друге, дозволяє здійснити агрегатно-вузлову систему розбирання машин, виключає знеосібку деталей; - по-третє, забезпечує більш економічну роботу майстерні відповідно до цілорічним графіком ремонту машин, планом обмінного фонду агрегатів і вузлів; - по-четверте, створює можливість широкого застосування і максимального використання універсального технологічного обладнання; - по-п'яте, підвищує продуктивність праці і полегшує працю робітників, підвищує використання корисної площі майстерні, зменшує потребу в коштах і металі на оснащення робочих місць.
До атегорія: - Досвід ремонту тракторів