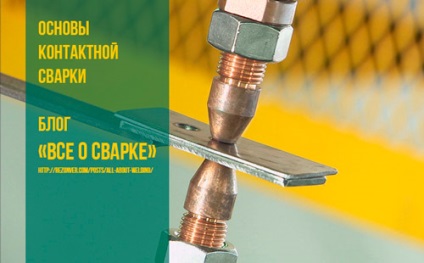
Творець контактного зварювання - англійський фізик Вільям Томсон, лорд Кельвін. У 1856 р він вперше застосував стикове зварювання. У 1877 р в США Еліху Томсон незалежно від англійця розробив стикове зварювання і впровадив її в промисловість. У тому ж 1877 в Росії Н. Н. Бенардос запропонував способи контактного точкового і шовного (роликового) зварювання. На промисловий потік в Росії контактне зварювання поставили в 1936 р
ПЕРЕВАГИ контактної ЗВАРЮВАННЯ ПЕРЕД ІНШИМИ СПОСОБАМИ
- Висока продуктивність (час зварювання однієї точки або стику становить 0,02 ... 1,0 с)
- Мала витрата допоміжних матеріалів (води, повітря)
- Висока якість і надійність зварних з'єднань при невеликому числі керованих параметрів режиму, що знижує вимоги до кваліфікації зварника
- Це екологічно чистий процес, що легко піддається механізації і автоматизації
Основні способи контактного зварювання - це точкова, шовна (роликовий) і стикове зварювання. Машини для контактного зварювання бувають стаціонарними, пересувними і підвісними (зварювальні кліщі). За родом струму в зварювальному контурі можуть бути машини змінного або постійного струму від імпульсу струму, випрямленого в первинному ланцюзі зварювального трансформатора або від розряду конденсатора. За способом зварювання розрізняють машини для точкового, рельєфною, шовного і стикового зварювання.
Як влаштований АПАРАТ ДЛЯ контактної ЗВАРЮВАННЯ
Будь-яка машина складається з електричної і механічної частин, пневмо- або гідросистеми і системи водяного охолодження (рис. 1).
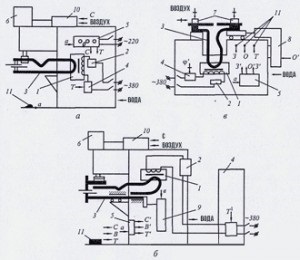
Мал. 1. Типові схеми машин для контактного точкового (а), шовного (б) і стикового (в) зварювання: 1 - трансформатор; 2 - перемикач ступенів; 3 - вторинний зварювальний контур; 4 - переривник первинного кола; 5 - регулятор; 6 - привід стиснення; 7- привід затиснення деталей; 8 - привід опади деталей; 9 - привід обертання роликів; 10 апаратура підготовки; 11 - орган включення
Електрична частина включає в себе силовий зварювальний трансформатор 1 з перемикачем ступенів 2 його первинної обмотки, за допомогою якого регулюють вторинну напругу, вторинний зварювальний контур 3 для підведення зварювального струму до деталей, переривник 4 первинному ланцюзі зварювального трансформатора 1 і регулятор 5 циклу зварювання, що забезпечує задану послідовність операцій циклу і регулювання параметрів режиму зварювання.
Механічна частина складається з приводу стиснення 6 точкових і шовних машин, приводу 7 затиснення деталей і приводу 8 опади деталей стикових машин. Шовні машини оснащені приводом 9 обертання роликів.
Пневмогідравлічні система складається з апаратури 10 підготовки (фільтри, лубрикатори, які змащують рухомі частини), регулювання (редуктори, манометри, дросселирующие клапани) і підведення повітря до приводу 6 (електропневматичні клапани, запірні вентилі, крани, штуцери).
Система водяного охолодження включає в себе штуцера розводящої і приймальні гребінок, що охолоджуються водою порожнини в трансформаторі 1 і вторинному контурі 3, розвідні шланги, запірні вентилі і гідравлічні реле, що відключають машину, якщо вода відсутня або її мало.
Всі машини обладнані органом включення 11. У точкових і шовних машин це ножна педаль з контактами, у стикових - це комплект кнопок. З органів управління надходять команди на стиск «С» електродів або затиснення «3» деталей, на включення «Т» і відключення «О» зварювального струму, на обертання «В» роликів, на включення «а» регулятора циклу зварювання. Ці команди відпрацьовуються відповідними блоками машини, забезпечуючи виконання операцій циклу зварювання.
Електроди в контактному зварюванні служать для замикання вторинного контуру через зварюються деталі. Крім цього при шовного зварювання електроди-ролики переміщають зварюються деталі і утримують їх в процесі нагрівання і опади.
Найважливіша характеристика електродів - стійкість. здатність зберігати вихідну форму, розміри і властивості при нагріванні робочої поверхні до температури 600 0С і ударних зусиллях стиснення до 5 кг / мм2. Електроди для точкового зварювання - це швидкозношуваний змінний інструмент зварювальної машини. Для виготовлення електродів використовують мідь і жароміцні мідні сплави - бронзи. Це може бути хромоцірконіевая бронза БрХЦрА; кадмієва БрКд1; хромистая БрХ; бронза, легована нікелем, титаном і берилієм БрНТБ або кремній-нікелева бронза БрКН-1-4. Останні дві бронзи мають підвищену зносостійкість, з них можна виготовляти електроди-губки стикових машин.
Матеріали для електродів повинні володіти також високою електро- і теплопровідністю, щоб їх нагрівання в процесі зварювання був менше. Температура разупрочнения бронз не перевищує 0,5 їх температури плавлення, а робоча поверхня електрода нагрівається до 0,6 Тпл. При таких умовах електродні бронзи відносно швидко разупрочняется. Підвищити зносостійкість електродів можна, використовуючи технологічні чинники. Зварювання алюмінієвих і магнієвих сплавів краще проводити на конденсаторних машинах, а не на машинах змінного струму. Замість механічної зачистки потрібна хімічне очищення поверхні, травлення і пасивація. Відстань l від робочої поверхні до дна охолоджувального каналу (рис. 2) не повинно перевищувати 10 ... 12 мм, збільшення його до 15 мм підвищує зношування електрода в 2 рази. При зварюванні чорних металів стійкість електродів можна підвищити в 3 ... 4 рази тільки за рахунок сферичної заточування електрода і зниження темпу зварювання до 40 ... 60 точок в хвилину.
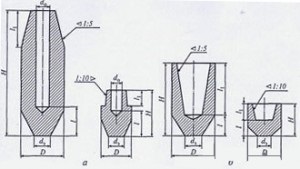
Мал. 2. Схеми електродів для точкового зварювання: а - із зовнішнім посадковим конусом; б - ковпачкових
Електрод повинен мати мінімальну масу, зручно і надійно встановлюватися на зварювальній машині. Діаметр D повинен забезпечувати стійкість електрода проти вигину при стисканні його зусиллям зварювання, а також можливість захоплення інструментом для зняття. Внутрішній діаметр повинен забезпечувати введення трубки з охолоджувальною водою і вихід води, звичайно d0 = 8 мм. Довжина конусної частини для кріплення електрода в свічці машини l1 <= 1,2 D. Угол конусности 1:10 при D <25 мм и 1. 5 при D> 32 мм. Діаметр робочої частини електрода вибирають залежно від товщини кромок зварювальних деталей d е = 3S.
Стійкість електродів із зовнішнім посадковим конусом (рис. 2, а) зазвичай не перевищує 20 000 сварок. Стійкість ковпачкових електродів (рис. 2, б) з внутрішнім посадковим конусом досягає 100 000 сварок внаслідок кращих умов охолодження. Для зварювання деталей складної конфігурації в важкодоступних місцях застосовують фігурні електроди.
Електроди для рельєфного зварювання конструктивно наближаються до форми вироби. У найпростішому випадку це плити з плоскою робочою поверхнею.
Електроди-ролики шовних машин мають форму дисків. Ширина робочої поверхні ролика В і його товщина Н залежать від товщини S деталі, що зварюється.
Токоведущие губки стикових машин за формою і розмірами повинні відповідати поперечному перерізі деталей, що зварюються. Довжину губок вибирають такий, щоб забезпечити співвісність деталей і запобігти їх прослизання при осаді. При зварюванні стрижнів вона становить 3 ... 4 їх діаметра, а при зварюванні смуг - не менше 10 товщин смуги.
ЯК ПІДГОТУВАТИ ПОВЕРХНЮ До ЗВАРЮВАННЯ
Є три основні вимоги:
- в контактах електрод-деталь має бути забезпечено як можна менший електричний опір Ке-д -> min),
- в контакті деталь-деталь опір повинне бути однаковим по всій площі контакту.
- поверхні, що сполучаються деталей повинні бути рівними, площині їх стику при зварюванні повинні збігатися.
Вибір конкретного способу підготовки поверхонь визначається матеріалом деталей, вихідним станом їх поверхонь, характером виробництва. Для штучного і дрібносерійного виробництва необхідно передбачити операції правки, рихтування, знежирення, травлення або зачистки, механічної обробки. В умовах великосерійного і масового виробництва, де забезпечується висока якість вихідних матеріалів в заготівельному і штампопрессовом виробництвах, підготовку поверхонь перед зварюванням можна не робити. Виняток становлять деталі з алюмінієвих сплавів, що вимагають обробки поверхні не раніше ніж за 10 год до зварювання.
Критерій якості підготовки поверхні - це величина контактних опорів Rе-д і Rд-д. Для їх вимірювання деталі затискають між електродами зварювальної машини, але зварювальний струм не включають. Опір вимірюють Мікроомметр за допомогою щупів. Для сталей опір більше 200 мкОм свідчить про погану якість поверхні. Висока Rе-д призводить до перегріву електродів і підплавлення поверхні деталей, внаслідок чого відбувається зовнішній і внутрішній виплеск металу і утворюється надмірна вм'ятина під електродами.
Основні параметри режиму всіх способів контактного зварювання - це сила зварювального струму, тривалість його імпульсу й зусилля стиску деталей. Теплота в зварюваної металі виділяється при проходженні через нього імпульсу струму I св тривалістю t у відповідність до закону Джоуля-Ленца:
де за Rсв приймають опір стовпчика металу між електродами. При розрахунку зварювального струму, часу імпульсу, зварювального трансформатора Rсв - вихідний параметр, так як його легко розрахувати, знаючи матеріал деталі, її товщину і необхідну температуру зварювання. При цьому опорами в контактах між деталями і між електродами і деталями нехтують. Відповідно до закону Джоуля-Ленца збільшення Rсв має збільшувати кількість теплоти, що виділяється. Але за законом Ома
де U2 - напруга на вторинному контурі зварювальної машини, a Z - повний опір вторинного контуру, до якого входить Rсв. Тому при збільшенні Rсв зменшиться Iсв, а він входить в закон Джоуля-Ленца в квадраті. Отже, збільшення Rсв не завжди збільшує кількість виділяється при зварюванні теплоти, багато що залежить від співвідношення Rсв і повного опору вторинного контуру зварювальної машини. Звідси випливають кілька практичних висновків. З ростом загального опору вторинного контуру від 50 до 500 мкОм тепловиділення в зоні зварювання зменшується в міру падіння Rсв приблизно в 10 разів. Недолік тепла компенсується збільшенням потужності (U2) або часу зварювання. Сварка на контактних машинах з малим опором вторинного контуру (
50 мкОм) супроводжується інтенсивним зростанням нагрівання в міру падіння Rсв в процесі збільшення зварного ядра. При досягненні рівності
нагрів досягає максимуму, а потім, у міру ще більшого зниження Rсв (після досягнення необхідного розміру ядра), зменшується. Таким чином, зварювання на контактних машинах з малим опором вторинного контуру (а їх більшість) супроводжується нестаціонарним нагріванням і нестабільним якістю з'єднань. Зменшити цей недолік можна надійним стиском зачищених деталей, що забезпечує підтримку Rсв на мінімальному рівні, або підтримуючи високий рівень Rсв за рахунок слабкого стиску деталей і поділу імпульсу зварювального струму на кілька коротких імпульсів. Останнє ще й економить енергію і забезпечує прецизійне з'єднання з залишкової деформацією 2 ... 5%.
При зварюванні на машинах з великим опором вторинного контуру (> 500 мкОм) зниження Rсв в процесі зварювання практично не впливає на виділення теплоти, нагрівання залишається стаціонарним, що характерно для зварювання на підвісних машинах з довгим кабелем у вторинному контурі. Зварені на них сполуки мають більш стабільною якістю.
ЗВАРНІ З'ЄДНАННЯ
Якість зварних з'єднань, виконаних контактним зварюванням, визначається підготовкою поверхонь до зварювання, а також правильним вибором параметрів режиму і їхньою стабільністю. Основний показник якості точкового і шовного зварювання - це розміри ядра зварної точки. Для всіх матеріалів діаметр ядра повинен бути дорівнює трьом толщинам S більш тонкого свариваемого листа. Допускається розкид значень глибини проплавлення в межах 20 ... 80% S. За меншим з цих меж слід непровар, за великим - виплеск. Глибина вм'ятини від електрода не повинна перевищувати 0,2 S. Розмір нахлестки в точкових і шовних з'єднаннях повинен вибиратися в межах 2,5 ... 5,0 діаметрів ядра.
Основні дефекти зварних з'єднань при точкового і шовного зварювання - це непровар, занижений розмір литого ядра, тріщини, рихлоти і усадочні раковини в литому ядрі і виплеск, який може бути зовнішнім, з-під контакту електрод - деталь, і внутрішнім, з-під контакту між деталями. Причини цих дефектів - недостатній або надмірний нагрів зони зварювання через погану підготовку поверхонь і поганий збірки деталей або через неправильно обрані параметрів режиму зварювання. При стиковому зварюванні з тих же причин можуть виникати непровари. Перегрів зони зварювання може викликати структурні зміни (укрупнення зерна) і обезуглеражіваніе сталей. Це погіршує механічні властивості з'єднань.
Контролюють якість контактного зварювання найчастіше зовнішнім оглядом, а також будь-якими методами неруйнівного контролю. Складність контролю полягає в тому, що цими методами непровар не виявляється, так як поверхні деталей щільно притиснуті один до одного, в їх контакті утворюється «склейка», проникаючі випромінювання, магнітне поле та ультразвук не відбиваються і не послаблюються. Найбільш оперативний метод контролю - руйнування контрольних зразків в лещатах молотком і зубилом. Якщо непровару немає, руйнування відбувається по цілому металу однієї з деталей, можна виміряти діаметр литого ядра при точкового і шовного зварювання.
Читайте так же: М.Д. Банів, Ю.В. Казаков, М.Г. Козулін. »Зварювання та різання матеріалів». -М