Шабруванням називається процес обробки поверхні виробів, при якому з окремих ділянок шабером соскабливают тонкі шари металу.
Шабери робляться з інструментальних сталей У12, У12А. Ріжучий кінець шабера гартується без відпустки до твердості HRC 60-65.
Шабер заточують на наждачному колі так, щоб штрихи від заточення розташовувалися поперек леза, при заточуванні шабер періодично охолоджують у воді. Після заточування лезо шабера доводять на точильних брусках-бруском або на абразивних кругах, поверхня яких покривається машинним маслом.
Шабери бувають з одним або двома ріжучими кінцями, перші називаються односторонніми, другі - двосторонніми. За формою ріжучого кінця шабери поділяють на плоскі, тригранні і фасонні.
Плоскі односторонні шабери з прямим або відігнутим вниз кінцем застосовують для шабрування плоских поверхонь, пазів, канавок. Для шабрування кривих поверхонь (при обробці втулок, підшипників і т. П.) Застосовують тригранні шабери.
Фасонні шабери призначені для шабрування фасонних поверхонь, складних за профілем канавок, жолобків, пазів і т. П. Фасонний шабер являє собою набір сталевих пластинок, форма якого відповідає формі оброблюваної поверхні.
Пластинки насаджують на металеву державка шабера і закріплюють гайкою.
Залежно від довжини і ширини оброблюваної плоскій поверхні величина припуску на шабреніе повинна бути від 0,1 до 0,4 мм.
Ручне шабреніе. Поверхня деталі або заготовки перед шабрением обробляють на металорізальних верстатах або обпилюванням. Потім починають шабреніе. Для перевірки якості шабрування поверхню повірочної плити покривають тонким шаром фарби (сурик, синька або сажа, розведені в маслі). Оброблювану поверхню ретельно протирають ганчіркою, акуратно накладають на перевірочну плиту і повільно переміщують по ній круговими рухами, після чого обережно знімають.
В результаті такої операції всі виступаючі на поверхні ділянки забарвлюються і чітко виділяються плямами. Забарвлені ділянки (плями) разом з металом видаляють шабером. Потім оброблювану поверхню і перевірочну плиту очищають і плиту знову покривають шаром фарби, деталь знову накладають на неї і процес повторюють.
Плями при повторних операціях будуть робитися меншого розміру, а кількість їх буде збільшуватися. Шабрують до тих пір, поки плями не будуть рівномірно розташовані по всій оброблюваної поверхні, а кількість їх буде відповідати технічним умовам.
При шабруванні кривих поверхонь (наприклад, вкладиша підшипника) замість повірочної плити користуються шийкою вала, яка повинна знаходитися в сполученні з оброблюваної поверхнею вкладиша. В цьому випадку вкладиш підшипника накладають на шийку вала, покриту тонким шаром фарби, обережно повертають його навколо неї, потім знімають, затискають в лещата і шабрують по плямам.
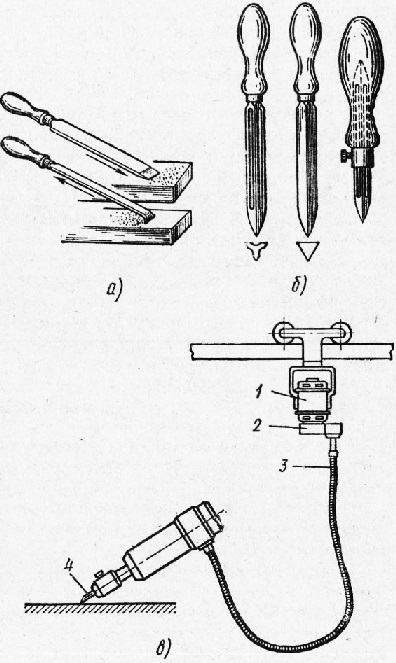
Мал. 1. Шабери ручні: а - прямий плоский односторонній і плоский односторонній з відігнутим кінцем, б - тригранні, в - механізований; 1 - електродвигун, 2 - редуктор, 3 - гнучкий вал, 4 - шабер
При шабруванні шабер встановлюють по відношенню до оброблюваної поверхні під кутом 25-30 ° і тримають його правою рукою за рукоятку, притиснувши лікоть до тулуба, а лівою рукою натискають на шабер. Шабрування проводиться короткими рухами шабера, причому якщо сусід плоский прямий, то рух його має бути направлено вперед (від себе), плоским шабером з відігнутим вниз кінцем рух виробляють назад (до себе), а тригранним шабером - убік.
В кінці кожного ходу (руху) шабера його відривають від оброблюваної поверхні, щоб не вийшли задирки і уступи. Для отримання рівної і точної оброблюваної поверхні напрямок шабрування кожен раз після перевірки по фарбі змінюють так, щоб штрихи перетиналися.
Точність шабрування визначають за кількістю рівномірно розташованих плям на площі розміром 25 х 25 мм 2 обробленої поверхні шляхом накладення на неї контрольної рамки. Середня кількість плям визначається перевіркою кількох ділянок оброблюваної поверхні.
Механізація шабренія. Ручне шабреніе замінюється по можливості шліфуванням, гострінням або його здійснюють механізованими шаберами.
Механізований шабер приводиться в дію електродвигуном через гнучкий вал, приєднаний одним кінцем до редуктора, а іншим до кривошипа. При включенні електродвигуна кривошип починає обертатися, повідомляючи шатуну і прикріпленому до нього шабер зворотно-поступальний рух. Крім електричного шабера, застосовують пневматичні шабери.
Притиранням називається процес обробки поверхонь деталей за допомогою абразивних порошків і паст з метою зняття найтонших шарів металу. Притирання застосовується в тих випадках, коли потрібно отримати високу точність пов'язаних поверховий двох ілй кількох деталей.
Притиранням можна досягти точності обробки в 0,001-0,002 мм. Притиранням отримують також поверхні з високим класом шорсткості і з'єднання, що забезпечують герметичність. При притирання знімається найтонший шар металу (за один хід притиру 0,002 мм), тому перед притиранням поверхні деталей повинні бути відшліфовані і припуск на притирання повинен залишати не більше 0,01 0,02 мм.
Притиральні матеріали. При притирання застосовують абразивні тверді і м'які матеріали. З твердих абразивних матеріалів для обробки стали застосовують порошки корунду, електрокорунду, для чавуну і крихких матеріалів - карбід кремнію, для твердих сплавів - карбід бору, синтетичні алмази. До м'яких абразивних матеріалів відносяться порошки оксидів хрому, заліза, алюмінію, які застосовуються для обробки отожженной стали, чавуну, сплавів міді, алюмінію.
Широке поширення при притирання знаходять пасти: абразивні на основі електрокорунду або окису хрому (пасти ГОІ) і алмазні (АПЮО. АП40, АП14, АП1 і ін.) На основі синтетичного алмазу. Абразивні пасти випускаються трьох типів: груба для грубої доведення, середня для попередньої доведення і тонка для остаточного доведення.
При притирання використовують мастильні та охолоджуючі рідини: гас, легкі мінеральні масла, бензин, содову воду і ін. Добавка олеїнової кислоти і каніфолі в гас різко підвищує продуктивність притирання.
Інструментами для притирання служать прітіри. Вони виготовляються з високою точністю за формою оброблюваної поверхні, мають правильну геометричну форму (допустиме відхилення - кілька мікрон). Матеріал прітіров повинен мати однорідний склад і твердість і бути м'якше матеріалу притираються деталі. Найчастіше прітіри виготовляють з дрібнозернистого перлитного чавуну твердістю НВ 150-200, а також зі сталі, міді, латуні, свинцю, скла.
Процес притирання. При притирання твердими абразивними матеріалами обробка ведеться за рахунок механічного впливу зерен цих матеріалів на частинки металу.
При роботі м'якими абразивними матеріалами та пастами під впливом поверхнево-активних речовин (олеїнової кислоти, стеарину, каніфолі) на оброблюваної поверхні утворюється м'яка окісна плівка товщиною близько сотої частки мікрона, яка потім знімається механічним шляхом (хіміко-механічна обробка).
Притирання за допомогою прітіров підрозділяється на доведення шаржовані прітірамі і доведення з намазуванням абразивної сумішшю (доведення вільним абразивним зерном).
У першому випадку притир шаржує, т. Е. В його поверхню до початку обробки вдавлюють абразивні зерна. У другому випадку абразивний суміш (паста) розлучається до напіврідкої маси, який покривається поверхня притиру.
До атегорія: - Автомобілебудування