Формування - процес виготовлення ливарних форм і стрижнів.
За способом виготовлення форми процес поділяється на формування ущільненням суміші (статичні методи - різні види пресування, динамічні - трамбування, вібрація, струшування, піскодувні метод, пескострельний і ін.) І формування без ущільнення суміші (насипна, набивна, електромагнітна, вакуумнопленочная і ін. ).
Струшування - ущільнення суміші в опоки, встановленої на струшувати столі формувальної машини, який піднімається під тиском повітря і різко опускається, б'ючись об станину з частотою до 250 ударів / хв.
При пресуванні суміш ущільнюється під тиском пресової колодки. Різновидами пресування є: уплотненіемногоплунжерной колодкою. (Пресування декількома пресовими колодками, що працюють під тиском масла або повітря); вибропрессование (ущільнення формувальної суміші в опоки, яка вібрує з великою частотою під тиском); піскодувні-прессовийспособ (ущільнення формувальної суміші з попередніми її наддувом і наступним пресуванням); високошвидкісне пресування (ущільнення суміші плитою, падаючої зі швидкістю 8 м / с).
При гравітаційному ущільненні суміш вільно або під тиском стисненого повітря падає в опоку з певної висоти.
Пріпескометном способі суміш подається на швидко обертається ротор з ковшем, який захоплює суміш і кидає її в опоку.
Імпульсний спосіб - ущільнення формувальної суміші одноразовим миттєвим ударом (імпульсом) стисненого повітря. Різновидом імпульсного ущільнення являетсяуплотненіе вибухом. при якому ударна хвиля створюється за рахунок вибуху газо-повітряної горючої суміші.
Вакуумно-плівкова формування - виготовлення форми з сухого піску без сполучного, який утримується в опоке за допомогою синтетичних полімерних плівок і вакууму. При заливці металу плівка газифіковане; газ проникає в форму, де конденсується на холодних зернах піску, виконуючи роль сполучної.
По використовуваній модельної оснащенні - формування по моделі, за шаблоном. За наявності опок - Опочня, безопочного формування, в знімних опоках і т. Д.
Найпоширенішим видом є лиття в піщані форми. Разові форми готують вручну (ручна формування), на формувальних машинах (машинна формування), напівавтоматичних і автоматичних лініях.
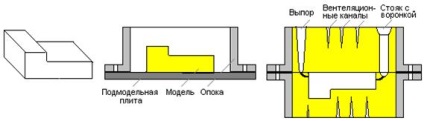
Ручна формовка. Застосовується в умовах одиничного, іноді дрібносерійного виробництва, при виготовленні унікальних виливків. Методи ручного формування різноманітні, їх використовують в залежності від складності, маси, габаритів виливка, умов виробництва і т. Д.
Основний технологічний варіант формування - це отримання форм в парних опоках по рознімної моделі (рис. 65).
Мал. 65. Ескіз виливки, півформа і форма
Модель і опоку встановлюють на подмодельную плиту. Поверхня моделі і плити посипають розділовим складом (сухі піском або тальком) для зменшення прилипання суміші до оснащення. Потім насипають в опоку шар облицювальної суміші, потім - шар наполнительной суміші, ущільнюючи її трамбуванням. Нижню полуформу разом з моделлю виливки повертають на 180 ° і знімають з модельної плити. На перевернуту опоку встановлюють другу опоку, в яку поміщають модель літніковойсистеми, після чого насипають формувальну суміш і ущільнюють її. Далі знімають верхню напівформи з нижньої, повертають її на 180 ° і відставляють убік. Витягають модель з форми. На нижню напівформи накладають верхню напівформи, скріплюють їх. Форма готова до заливання.
Крупні відливання отримують грунтової формуванням в ямах і кесонах, дно яких знаходиться нижче рівня підлоги цеху. Стінки і дно кессонов облицьовані бетоном для того, щоб не потрапили грунтові води.
При ручному формуванні, крім піщано-глинистих, можливе використання холоднотвердеющих, рідких і сипучих самотвердіючих сумішей, а також рідко-скляних з продувкою їх вуглекислим газом.
Машинна формування. Для отримання більш точних виливків, підвищення продуктивності праці використовують машинну формування. Існує багато різновидів формувальних машин, а на заводах масового виробництва (автомобільних, транспортних і ін.) Працюють автоматичні формувальні лінії.
Такі лінії складають комплекс ливарних машин, механізмів і підйомно-транспортних пристроїв, що виконують автоматично всі операції виготовлення форм, подачу на заливку, охолодження і вибивання. При цьому стрижні можуть встановлювати вручну.
За способом ущільнення суміші машини діляться на встряхивающие, пресові, піскодувні і пескострельние, гравітаційні, Піскомети, імпульсні, вакуумні; за способом вилучення моделі з форми. витяжні (з штифтовим підйомом опок, з протяжкою моделі); поворотно-витяжні (з поворотним або перекидним столом); по роду приводу і способу приведення в дію: пневматичні, гідравлічні, пневмогидравлические, електромагнітні, комбіновані; по конструктивної компонуванні. одно-, дво- і багатопозиційні; за способом переміщення опок. прохідні, човникові, карусельні; за ступенем автоматизації. неавтоматичні, напівавтоматичні, що включаються при кожному новому циклі; автоматичні.
Виготовлення стрижнів. Процес виготовлення стрижнів включає наступні операції: формування, затвердіння, обробка. Формування проводиться або вручну, або на машинах із застосуванням стрижневих ящиків різної конструкції.
У найзагальнішому вигляді процес ручного виготовлення стержня при одиничному і дрібносерійного виробництва такої: спочатку стрижневий ящик частково заповнюється сумішшю, легко ущільнюється, потім в нього встановлюють каркаси (арматуру з обпаленого сталевого дроту, зварні або литі з сірого чавуну) для додання стрижня міцності. Ящик наповнюється сумішшю, яка поступово ущільнюється трамбуванням, на струшуючих машинах, вібрацією або за допомогою пескометом. Для поліпшення вентиляції або вентиляційними голками (Душнікі) наколюють канали, або в стрижень закладають солом'яні джгути, воскові гноти, шнури, які випалюються або виплавляються під час сушіння стрижнів.
Великі стрижні виготовляються з внутрішніми порожнечами, куди закладають наповнювачі - шлак або тирсу. Завершальними операціями при виготовленні великих стрижнів є склеювання їх окремих частин, промазування швів, що спеціальними пастами, остаточна обробка, контроль і, при необхідності, нанесення на робочі частини стрижня протипригарних покриттів.
При масовому і великосерійному виробництві для формування стрижнів широко використовують піскодувні (рідше - пескострельний) метод ущільнення суміші. Стрижні постійних перетинів (круглого, квадратного і т.д.) можуть виготовлятися на мундштучних машинах. У таких машинах стрижневий ящик замінений змінною гільзою (мундштуком), перетин якого визначає форму стрижня. Стрижень будь-якої довжини отримують видавлюванням з мундштука машини ущільненої суміші.
Отверждение стрижнів може здійснюватися за рахунок теплової сушки поза оснастки; самоотвержденія в холодній або нагрітої оснащенні.
Для затвердіння стрижнів поза оснащення застосовують сушку в спеціальних сушилах періодичного або безперервної дії. Сушка підвищує міцність стрижнів, зменшуючи їх газотворность. Стрижні поміщаються в сушилах на сушильних плитах, температура сушіння залежить від природи сполучного матеріалу, а час сушіння - від конфігурації і маси стрижня.
При затвердінні стрижнів в холодній оснащенні використовують холоднотвердеющих суміші, отверждаемие при нормальній температурі під впливом твердих, рідких або газоподібних реагентів - отвердителей і каталізаторів. В даний час під ХТС найчастіше мають на увазі холоднотвердеющих суміші на синтетичних смолах ( «Cold-Box process»). Для виготовлення стрижнів широко застосовується СО2 - процес, при якому жидкостекольной суміш засипається в стрижневий ящик і продувається вуглекислим газом. Для поліпшення вибіваемость стрижнів в суміш вводять спеціальні добавки.
Вологі піщано-смоляні і сухі термореактивні суміші застосовують для отримання стрижнів в нагрівається оснащенні.
Фарбування і складання форм. З метою зменшення фізико-хімічного впливу між металом виливки і матеріалом форми в процесі заливки і подальшого охолодження для отримання чистої поверхні частини форми і стрижнів покривають вогнетривкими матеріалами.
Перед складанням напівформи і стрижні ретельно перевіряють за зовнішнім станом. В операцію збірки входять: очищення полуформ від сміття, установка стрижнів, контроль правильності їх установки, накриття верхньої напівформи на нижню, скріплення їх між собою штирями або втулками. Зверху на капці встановлюють вантаж для запобігання зсувів полуформ і підйому верхньої напівформи щодо нижньої.
Заливка металу Отримані метал з плавильного агрегату переливають в ківш (рідше в міксер). З ковша розплав заливають у форми, встановлені на підлозі цеху (в одиничному виробництві) або на конвеєрах (в масовому виробництві).
Охолодження - процес витримки виливка в формі до температури, при якій її можна отримати з форми без пошкоджень. Залежно від маси виливки тривалість охолодження коливається від декількох секунд до декількох діб.
Вибивання - це процес видалення охолодженої виливки з форми і стрижнів з виливків. Для вибивання відливок використовуються вибивні решітки. При цьому форма руйнується, а в атмосферу виділяється велика кількість тепла, пилу і газів. Для видалення стрижнів з виливків застосовують гідрокамери, в яких руйнування стрижнів і видалення залишків стрижневий суміші виробляється потужним струменем води.
Після вилучення виливки з форми слід фінішна обробка: очищення, обрубка, зачистка, термообробка.
Обрубка літників, прибутків (елементів ливникової системи для харчування виливки розплавом в період затвердіння і усадки) і випоровши (елементів ливникової системи для виведення газів з порожнини форми) здійснюється стрічковими і дисковими пилами; повітряно-дугового різкою, при якій метал розплавляється електродугою і віддаляється спрямованої струменем стисненого повітря.
Очищення полягає у видаленні з поверхні виливки пригару, залишків формувальної і стрижневої суміші. Очищення проводиться в дробометних барабанах або камерах, де виливки очищаються під ударами сталевий і чавунною дробу; в галтувальних барабанах - під ударами зірочок.
Зачистка нерівностей виконується ручними шліфувальними машинками або на верстатах.
Термообробка полягає в нагріванні і охолодженні за певним режиму виливків для поліпшення їх властивостей.
Контроль якості. Методи контролю діляться на руйнують і неруйнівні.
Ти, що руйнуєш контроль може здійснюватися як на спеціальних зразках, вирізаних з різних ділянок контрольованої виливки, так і на зразках, що відливаються одночасно з відливанням або є частиною виливки.
Неруйнівний контроль залишає виливок придатної до експлуатації, при цьому можуть використовуватися такі методи: магнітний, електричний, електромагнітний, оптичний, радіаційний, акустичний і ін.
Контроль макро- і мікроструктури виробляють для оцінки якості сплаву і виливки. Контроль макроструктури (макроанализ) проводять візуально або за допомогою оптичних приладів при невеликому збільшенні. Контроль мікроструктури (мікроаналіз) здійснюють на мікрошліф, вирізаних з різних частин виливки, литих проб.
Виливки піддають проміжному контролю на різних стадіях процесу з отримання, а також остаточного контролю після завершення всіх фінішних операцій. Контроль може бути суцільний і вибірковий.
Основні дефекти виливків: Пригара (частина поверхнівиливки забруднена формувальної сумішшю); просечки (прожилки на поверхні через затікання металу в тріщини на поверхні форми); ужіміни (заповнені формувальної сумішшю і прикриті шаром металу поглиблення через відшарування суміші при заливці); усадочная раковина (порожнину, що утворилася при затвердінні металу через усадки). Після контролю частина бракованих виливків йде на переплавку, а деякі - на доопрацювання (заварку, просочення спеціальними складами).