Проводиться абразивними брусками, які здійснюють коливальні зворотно-поступальні рухи з великою частотою і малим ходом, по поверхні, що обертається деталі.
Застосовують для обробки зовнішніх і внутрішніх циліндричних поверхонь.
М'які дрібнозернисті абразивні бруски під час роботи притискаються до оброблюваної поверхні пружинами або гідравлічними пристроями.
Як МОР застосовують гас з маслом.
Припуск на обробку не залишають.
Процес полягає в знятті гребінців з поверхні залишилися від попередньої обробки.
Притирання здійснюється прітірамі на поверхню яких наносять дрібнозернистий абразивний порошок змішаний з мастилом або пастою.
Притири можуть бути чавунні, сталеві, бронзові, свинцеві. Як абразивний матеріал застосовують порошок з карбіду кремнію, алмазної пилу, електрокорунду, наждаку.
Як пасти застосовують окис хрому, окис алюмінію.
Припуск на обробку залишають 0,005-0,02 мм.
Виконується хонинговальной головкою, оснащеною дрібнозернистими брусками, сегментами.
Головка здійснює обертальні рухи і зворотно-поступальні поза рухомий деталі.
Високі ріжучі властивості інструменту забезпечуються:
1. правильним підбором інструментального матеріалу
2. оптимальної геометрією інструменту
3. правильно проведеної термічною обробкою (інструмент набуває твердість і зносостійкість)
4. умовами експлуатації інструменту
Існує ряд методів дозволяє підвищити стійкість ріжучої частини інструменту шляхом проведення додаткових операцій.
а) насичення поверхневого шару інструменту (цанірованіе, хромування, сульфідування)
б) підвищення стійкості при термічній обробці шляхом поліпшення структури (обробка холодом, обробка парою)
5. підвищення якості поверхні інструменту (доведення, притирання)
Цанірованіе - хімікотерміческій процес, який полягає в насиченні поверхневого шару стали вуглецем і азотом шляхом дифузії при певній температурі.
Рідке цанірованіе низькотемпературне.
Буває газове і сухе ціанування.
Сульфідування - процес насичення поверхневих шарів металу сірої, що утворилося на поверхні сірчисте з'єднання знижують коефіцієнт тертя і підвищують зносостійкість.
Процес відбувається при температурі 550ºС в ваннах ≈ 40-90 хв.
Стійкість інструменту при цьому стає в 1,5-2 рази вище.
Хромування - піддають стали, бронзи в гальванічних ваннах.
Товщину шару доводять до двох сотих міліметра.
Інструмент: протягання, Долбіков.
Процес обробки паром.
Інструмент з бронзи, стали.
1. промивка гарячою водою
2. промивка в 70% розчині соди
3. витримка 15-30 хв. в електропечі при температурі до 400ºС.
Піч продувається водяною парою і при температурі 560ºС витримується 30-40 хв. Потім охолоджений матеріал до 50-70ºС опускають в підігріте масло, на інструменті утворюється 0,05 мм плівки окислів.
Стійкість підвищується в два рази.
Обробка металів тиском.
Основні види обробки металів тиском: прокатка, пресування, волочіння, кування, штампування.
Прокатка. При прокатці нагріті або холодні заготовки пропускають між обертовими балками прокатних станів.
Існує три види прокатки: поздовжня (для сортових і фасонних профілів), поперечна і поперечно-гвинтова (для тіл обертання). При поздовжньої прокатки балки обертаються в різні боки і деформують заготовку. При поперечному балки обертаються в одному напрямку.
Пресування - це спосіб обробки металів тиском, при якому метал видавлюють із замкнутої порожнини через отвір, в результаті чого отримують виріб з перетином за формою отвори.
Існує два види пресування: пряме і зворотне.
Волочіння - полягає в протягуванні під дією зовнішньої сили заготовки (зазвичай в холодному стані) через отвір, переріз якого менше вихідного перерізу заготовки.
Кування - обробка металу, що знаходиться в пластичному стані, статичним або динамічним тиском.
До операцій кування відносяться протяжка, осаду, гнучка, пробивання або прошивання отворів, рубка і т.д.
Штампування - це обробка металу за допомогою штампів. Велика продуктивність. Штампування бувають гарячої і холодної, звичайної і листової.
Напилення є одним із способів обробки поверхні матеріалів, який використовується на промислових підприємствах, як спеціальний вид обробки.
Основне призначення напилення - це захист від корозії, ремонт зношених поверхонь, деталей машин і інструменту.
Розробка нових методів напилення, заснованих на використанні плазмових струменів, енергії детонації і інших явищ дозволяє отримувати покриття з таких матеріалів, які не могли бути використані.
Напиленням можна наносити покриття з самими різними властивостями. Можна напилювати: теплостійкі, теплоізоляційні, зносостійкі, корозійностійкі, електроізоляційні і інші покриття.
При створенні високовиробничих машин, апаратів і інструментів в першу чергу виникає проблема отримання таких матеріалів, які могли б протистояти жорстким умовам роботи.
За типом джерела теплової енергії, яка використовується для розплавлення напилюваного матеріалу, існуючі конструкції апаратів для напилення в основному можна розділити на два види: газополумяні і електричні.
У газополуменевих апаратах використовується теплота, що виділяється при горінні суміші горючий газ + кисень.
В електричних апаратах використовують теплоту електричної дуги.
Найбільш широке застосування знаходить метод газопламенного напилення, який використовують для напилення покриттів із сплавів на основі нікелю і кобальту, керамічних і інших тугоплавких матеріалів.
Спеціальними видами газопламенного напилення є напилення при якому використовується енергія детонації суміші ацетилену з киснем.
Детонація - це швидко що протікає реакція вибуху.
Цей вид напилення дозволяє наносити покриття з матеріалів з ще більш високою температурою плавлення.
З електричних видів напилення найбільш старим є спосіб електродугової металізації.
Раніше використовували дугу, палаючу на змінному струмі, що не дозволяло отримувати стійкий процес розпилення.
Зараз для отримання дуги використовують постійний струм, що забезпечує кращу стабільність роботи.
В останні роки стали застосовувати плазмові рапилітелі і установки для високочастотного індукційного напилення, які дозволяють напилювати будь-які матеріали.
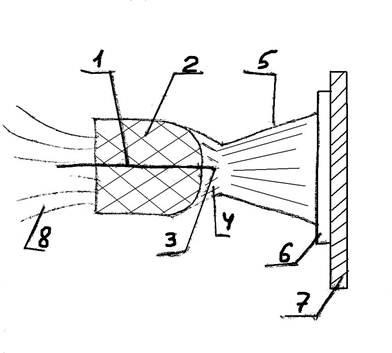
2 - полум'я, що утворюється при згоранні
3 - оплавлятися кінець дроту
4 - повітряний потік
5 - частинки металу
Джерело теплової енергії - це полум'я, що утворюється в результаті горіння суміші кисень + горючий газ (ацетилен).
Залежно від стану напилюваного матеріалу напилення може бути: дротове, пруткове і порошкове.
Принцип дротяного і пруткового напилення однаковий.
Напилюваний матеріал у вигляді дроту або прутка подається через центральний отвір пальника і розплавляється в полум'я.
Струмінь стислого повітря розпилює розплавлений матеріал на дрібні частинки, які осідають на оброблюваної поверхні.
Подача дроту проводитися з постійною швидкістю роликами, які приводилися в рух вбудовані в пальник повітряної турбіни, що працює на стисненому повітрі або електродвигуном при цьому необхідна точне регулювання швидкості обертання турбіни або двигуна.
Пальник з електродвигуном дозволяє більш точно регулювати подачу дроту і підтримувати її постійну швидкість, але вони дуже громіздкі.
Діаметр напиляемой дроту 3 мм, легкоплавких дротів (Al-Zn) до Ø7 мм.
Газополум'яне напилення порошкового матеріалу.
Напилюваний порошок надходить в пальник, розганяється потоком транспортує газу (О2 + горючий газ) і на виході з сопла потрапляє в полум'я, де відбувається його нагрівання. Струмінь гарячого газу захоплює частинки порошку і завдає на Напилювана поверхню.
У порошкових пальниках, як і в дротяних, подача напилюваного матеріалу в полум'я і розгін утворюються розплавлених частинок може здійснюватися за допомогою струменя стиснутого повітря. Таким же чином можна напилювати і пластмаси.
Газополуменевим напиленням можна наносити тугоплавкі покриття.
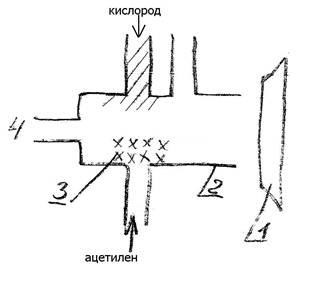
Детонаційне напилення - призначене для отримання твердих зносостійких покриттів.
2 - охолоджуваний ствол
У камеру подається О2 і ацетилен (С2 Н2) в строго певних кількостях. Стовбур направляється на деталь. Через спеціальні отвори в камері азотом виштовхується порошок напилюваного матеріалу.
Газову суміш, в якій в підвішеному стані перебувати напилюваний порошок підпалюють електричної іскрою, виникає вибух. В результаті вибуху відбувається виділення теплоти і утворюється хвиля, яка розігріває і розганяє частки порошку.
При цьому способі частинкам порошку повідомляється велика кінетична енергія. Після вибуху суміші горючих газів проводитися продування ствола азотом для видалення продуктів горіння.
Електричні методи напилення.
У електрометаллізатор безперервно подаються дві напилювані дроту. Між кінцями цих дротів збуджується електрична дуга.
У електрометаллізаторе. через яке подається стиснене повітря. Струмінь стислого повітря відриває з електродів частки розплавленого металу і забирає їх до напиляемой поверхні.
Електрометаллізатор може працювати як на постійному так і на змінному струмі.
При використанні змінного струму дуга горить нестійкий і супроводжується горіння великим шумом, при постійному струмі характер роботи стійкий, напилений матеріал має дрібнозернисту структуру.
Продуктивність напилення висока.
Для напилення використовується дріт Ø 0,8; 1; 1,6 і 2 мм.
Переваги електродугового методу:
1. висока продуктивність процесу.
2. значно скорочується час процесу.
3. отримують більш міцні покриття, які краще з'єднуються з основою, ніж при газополуменеве напилювання.
4. в якості електродів можна брати дріт різних металів, тому можна отримувати покриття з їх сплавів.
1. перегрів і окислення напилюваного матеріалу.
2. вигоряння легуючих елементів, що входять в напилюваний сплав.
Якщо нагріти газ, молекули якого складаються з декількох атомів до температури перевищує 1000 ° К, відбудеться процес руйнування молекулярних зв'язків і газ перейде в атомарний стан (відбудеться дисоціація). Температура цього процесу визначається родом газу і тиском.
Газ, в якому атоми або молекули іонізовані - називається плазмою.
Плазма має високу електропровідність.
В даний час в промисловості для отримання плазми використовують два типи пальників: плазменно-дугові та плазмово-струменеві.
Покриття отримані методом плазмового напилення мають високу щільністю і хорошим зчепленням з основою.
Однак плазмового напилення має низьку продуктивність, супроводжується шумами і сильним ультрафіолетовим випромінюванням.
До недоліків цього методу відносяться висока вартість обладнання та його експлуатаційні витрати.