З метою приско-ня темпів будівництва трубопроводів застосовують метод попередньої укрупненого і зварювання труб в секції (ланки) і їх ізоляції на трубозварювальних і трубоізоляціонних базах, після чого їх транспортують на трасу для укладання в траншею. Бази забезпечені сучас-менним обладнанням для напівавтоматичного та автоматичного зварювання поворотних стиків, а також пристроями для очищення і подальшого на-несення на трубні секції протикорозійних покриттів. Бази складаються з трьох основних технологічних ліній - збірки (центрування), зварювання та ізоляції. Вони бувають стаціон-Нарнії, напівстаціонарних і польові.
Переробка труб на стаціонарних базах організується так. Труби краном укладають на прийомних стелажах, звідки подаються на лінію збірки (центрування), де за допомогою центратору збирають в сек-ції довжиною 18, 24 і 36 м. Після складання на кожному стику спочатку виконуємо-ють «прихватку», а потім напівавтоматичну зварювання першого (кореневого) шару шва. Потім секцію через проміжний стелаж-накопичувач подають на лінію автоматичного зварювання наступних шарів. Зварену секцію подають на лінію ізоляції, де виробляють операції сушки, грунтовки (праймування) та ізоляції. Готову ізольовану секцію переміщують під кран-перевантажувач, який подає її на склад готової продукції або на трубоплетевоз.
Для складання і зварювання труб в секції довжиною 36 - 40 м в польових умовах викорис-товують польові трубозварювальні бази. Такі бази розташовують уздовж траси трубопроводу, що будується через 15-30 км один від одного.
Виготовлення криволінійних елементів. Зварні відводи изго-товляют з окремих секторів. Відведення з кутом 90 ° складається з чотирьох сек-торів: двох внутрішніх з кутом 30 ° кожен і двох зовнішніх з кутом 15 ° кожен. Відведення з кутом 60 ° можна виконувати з двох секторів з кутом 30 ° кожен. Відводи великих діаметрів (600 мм і вище) можна виготовити як з листового металу, так і з труб. При механізованому изготовле-ванні відводів з труб сектори ріжуть без розмітки на спеціальних верстатах.
При ручному різанні труб на сектори застосовують пристосування або шаблони, а при виготовленні секторів з листового металу заготовки раз-меча по шаблонах, а потім вирізують і вальці.
Гнуття труб необхідно в тих випадках, коли природний вигин тру-бопроводов у вертикальній і горизонтальній площинах неможливий. Тог-да криві необхідного радіусу і кута отримують шляхом вварки попередньо-тельно вигнутих колін, виготовлених способом холодного гнуття на трубогибочні верстатах типу ГТ для труб великих діаметрів із застосуванням дорнів. Причому труби діаметром 273 -530 мм гнуть на верстаті ГТ-531, діаметром 720 -1020 мм - ГТ-1021, діаметром 1220 - ГТ-2121 і діаметром 1420 - на верстаті ГТ-одна тисяча чотиреста двадцять один. Для гнуття підбирають труби з більш товстими стінками і з відхиленнями від діаметра в сторону позитивного допус-ка. При гнуття секцій з двох і більше труб кільцевої шов на відстані не менше 0,5 діаметра труби треба вивести із зони вигину.
Криві вставки, що виготовляються на трубогибочні верстатах, долж-ни відповідати нормалям, що вказані в робочих кресленнях. Нормалі передбачають радіуси вигину кривої, що забезпечує беспрепятст-венний прохід розділових поршнів або очисних пристроїв по трубо-проводу при його очищенні, а також проходження по поверхні кривої вставки очисних і ізоляційних механізмів під час будівництва тру-бопровода. Мінімально допустимі радіуси кривих при гнуття труб в холодному стані наведені в додатку 3.
Сталеві труби з'єднують між собою зварюванням, а в місцях уста-новки арматури (засувок, кранів, вентилів і ін.) - на фланцях. Види зварювання залежать від умов виконання зварювальних робіт (на трубосвароч-ної базі або на трасі) і від діаметра труб, що зварюються.
Зварювання труб включає наступні технологічні операції: під-готовка труб і кромок їх торців до збірки; розкладка труб на зварювальних підкладках (стелажах або стендах); центрування і стягування труб до досягнень-вання між крайками торців потрібного зазору; скріплення зібраного стику зварювальними прихватами; зварювання стику. При підготовці труб очищено-ють кромки шириною 10 - 15 мм, що з'єднуються труб від бруду, іржі і, особливо, від масел, вирівнюють вм'ятини і нерівності торців, виправляючи-ють овальність, щоб різниця діаметрів торців не перевищувала 1 - 1,25% номіналу. Товщина стінок труб, що з'єднуються не повинна мати відхилення більше 12 - 15% стандартного розміру.
Розкладка труб перед складанням повинна сприяти їх беспрепят-жавної і зручною центрівці - поєднанню геометричних осей і кро-мок труб при строгому дотриманні нормативних зазорів. Для цього примі-няют спеціальні затиски - центратори, які бувають зовнішні (вин-товие, ексцентрикові і ланцюгові, рис. 6.22, а - в) і внутрішні (гидравли-етичні, рис. 6.22, г). Завдяки синхронного дії розтискних кулачків центратори автоматично забезпечують калібрування і центрування
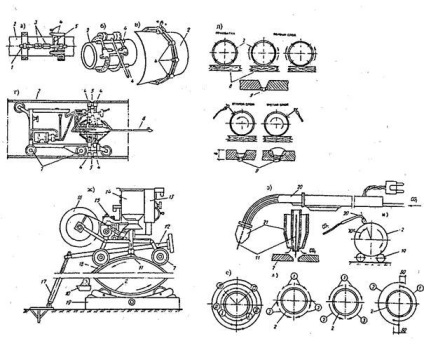
Мал. 6.22 - Складання і зварювання сталевих труб
а, б - центратори гвинтовий і ексцентрикові (для труб діаметром не більше 350 мм), в - те ж, зовнішній роликово-ланковий (для труб 520 - 1020 мм), г - то ж, внутрішній гідравлічний (для труб 520 - 1220 мм ), д, е - послідовність операцій при ручному електрозварювання стиків поворотним і неповоротним тришаровим швом, ж - схема застосування зварювальної головки ПТ-56 для поворотною зварювання стиків під шаром флюсу, з - то ж, для зварювання кореня шва шланговим держателем напівавтомата А-547 -р, і, е - порядок накладення кореневого шару шва при зварюванні труб великого диамет а трьома зварниками, л - то ж, для заповнення решти шва двома зварниками; 1 - натяжна гвинт, 2 - зварюються труби, 3 - отвір для воронки, 4 - центруючі елементи, 5 - стик труби, 6 - штанга, 7 - ролики, 8 - лежня під труби, 9 - кореневої шар шва, 10 - збірник для флюсів, 11 - зварювальна проволока, 12 - регулювальний гвинт, 13 - панель з реостатом, вольтметром і вимикачами, 14 - бункер для флюсу, 15 - механізм, що подає з двигуном і редуктором, 16 - касета зі зварювальним дротом, 17 - штатив, 18 - флюс, 20 - штанговий держатель, 21 - головка власника, 1, 2, 3 в гуртках - позиції зварників, I, II, III - послідовність накладено ия шва неповоротного стику
торців труб. З їх допомогою спочатку закріплюють труби, а потім накладають при-хватки і перший (кореневої) шар зварного шва. Далі сталеві труби сва-ють за допомогою дугового (ручний, напівавтоматичного і автоматичні-кою) зварювання, в тому числі під флюсом або в зоні захисних газів, наприклад СО2. а також за допомогою електроконтактного і газопрессовая зварювання (маги-стральние трубопроводи).
Дугове зварювання сталевих труб (рис. 6.22, д) здійснюють з поворотів-те їх навколо своєї осі (поворотні стики) і без повороту (неповоротні або стельові стики). Неповоротні стики зварюють в два або три шари, починаючи з нижньої твірної труби в 50 мм від вертикального діаметра труб (рис. 6.22, е). Перший шар, як уже вказувалося, називають кореневим, другий - що заповнює і останній - облицювальною. Труби діаметром до 500 мм зварюють безперервним швом, а труби великих діаметрів - пре-ривістим (як показано стрілками на рис. 6.22, е). Неповоротні стики труб великих діаметрів при необхідності прискорення виконання робіт зварюють одночасно два або три зварника за схемами, наведеними на рис. 6.22, і, л.
Однак, оскільки ручне зварювання неповоротних стиків дуже праце-емка і часто стримує темп прокладки трубопроводу, останнім часом все частіше застосовують прогресивну напівавтоматичну і автоматичні-кую зварювання таких стиків за допомогою, наприклад, зварювального автомата, з-стоїть з самохідного візка, зварювальної головки і пульта управління. У процесі зварювання головка переміщається навколо труби по направляючої поясу і зварює труби електродної дротом.
Також пріменятеся спосіб еле-ктроконтактной стикового зварювання шляхом безперервного оплавлення торців труб за допомогою установки типу ТКУС (для зварювання труб в секції) і типу ТКУП (для зварювання секцій в нитку трубопроводу).
На зварювальних базах (стаціонарних і напівстаціонарних) зварювання труб в секції найчастіше виконують під флюсом за допомогою зварювального го-спритні (рис. 6.22, ж), кореневої шов - під захистом уг-лекіслого газу за допомогою напівавтомата (рис. 6.22, з) .
Для збільшення терміну служби трубопроводів і забезпечення їх безаварійної роботи виконують їх захист від корозії.
Ізоляційні покриття повинні володіти пліт-ністю, що забезпечує гідро- і електроізоляційні властивості, хорошою прилипаемостью до металу (адгезію), стійкістю до температурних через трансформаційних змін і здатність зберігати свою форму в умовах навколишнього середовища (пластичністю), витримувати значні навантаження в процесі укладання (механічної міцністю).
Найбільш ефективною для забезпечення довговічності трубопрово-да є комплексна протикорозійний його захист, що включає так звану «пасивну» їх захист різними ізоляційними покриття-тиями і «активну» (катодний, протекторний і дренажну) захист від віз-дії блукаючих струмів (електрокорозії), так як вона часто буває небез-неї грунтової (гальванокоррозіі).
Принцип дії катодного, протекторного і електродренажного за-щити сталевих труб від електрокорозії блукаючими струмами укладає-ся в наступному. Поблизу трубопроводу обладнають станцію катодного захисту і-ти (СКЗ), до складу якої входять джерело постійного струму, анодное за-землення і дренажні кабелі. Негативну клему джерела струму при-з'єднують до сталевого трубопроводу, а позитивну - до заземлення. В результаті струм стікає з анодного заземлення, підтікає до трубопроводу і повертається до джерела по дренажному кабелю. Струм СКЗ створює негативні-вальний потенціал на трубопроводі і при його роботі відбувається зруйнований-ня анодного заземлення, але при цьому одночасно захищається сталевий підземний трубопровід.
Протекторний захист застосовують для захисту сталевих трубопроводів, що проектують-дов невеликою протяжністю від блукаючих струмів, якщо необхідне зміщення потенціалу трубопроводу не перевищує 0,3 В. Протектор виготовляють з металу з більш негативним електродним по-потенціалом, ніж метал підземного трубопроводу. Встановлений в грунт і наведений в контакт з трубопроводом протектор разом з ним утворює гальванічну пару. Протектор (гальванічний анод) при цьому руйнується, а підземний трубопровід поляризується до захисних потенціалів і не руйнується.
Електродренажного захист сталевих трубопроводів полягає у відведенні блукаючих струмів, які проникли в трубопровід, в мережу зворотних струмів електричного рейкового транспорту шляхом приєднання трубопро-вода через дренажний пристрій з елементами цієї мережі (негативною шиною тягової підстанції, що відсмоктує пунктом або рейкою). Завдяки цьому на трубопроводі створюється негативний потенціал, що запобігання-обертає вихід блукаючих струмів з металу труби в грунт і її зруйнований-ня.
Для захисту трубопроводів від грунтової корозії застосовують, головним чином, покриття на основі нафтових бітумів і полі-мірних липких стрічок.
Конструктивно ізоляційні покриття складаються з грунтовки, одно-го або декількох шарів ізоляційного матеріалу (мастики, липкою льон-ти), армуючого і обгорткового шарів. Вони бувають трьох основних типів: нормальні, посилені і дуже посилені. Для магістральних трубопро-водів застосовують покриття нормального і посиленого типів, а для роз-дящих, прокладених в межах міста або промислового підприємства, дуже посиленого типу.
Покриття дуже посиленого типу загальною товщиною 9 ± 0,5 мм з-стоїть з одного шару бітумної грунтовки, трьох шарів мастики товщиною по 3 мм, поділюваних двома шарами армуючої обмотки з скловолокна і зовнішньої обгортки з міцної крафт-паперу.
Нормальне покриття складається з грунтовки, мастики шаром 4 мм, одного шару скловолокна і захисної обгортки.
Посилене покриття. нанесене в базових умовах, складається з грунтовки, двох шарів мастики з 3 мм, двох шарів скловолокна і захисної обгортки, а в польових умовах - з грунтовки, одного шару мастики 6 мм, одного шару скловолокна і захисної обгортки.
Нанесення покриття з полімерних липких стрічок зазвичай механізоване. Такі стрічки виготовляють з поліетилену або полівінілхлориду з нанесенням на них клейового шару. Покриття складаються з шару грунтів-ки, одного, двох або трьох шарів стрічки (що відповідає нормальній, посиленої і вельми посиленої ізоляції) і захисної обгортки.
Нанесення ізоляційних покриттів. Перед нанесенням покриттів поверхню трубопроводу ретельно очищають від окалини, іржі та інших забруднень на стаціонарній трубоочістной машині. Очищені труби негайно покривають ґрунтовкою, а після її висихання - бітум-ної мастикою. В умовах бази мастику на труби наносять за допомогою трубоізоляціонной установки. При використанні для ізоляції труб липких стрічок їх намотуючи-ють на труби спеціальними ізоляційними машинами. Ізоляційні ра-боти по суміщеному методу безпосередньо на трасі виконують ко-лонної машин, що включає крани-трубоукладачі, очисні і ізоляці-ційні машини, тобто з суміщенням процесів очищення, ізоляції та укладання трубопроводу в траншею.