Мал. 3, Залежність в'язкості смол і мазуту від температури
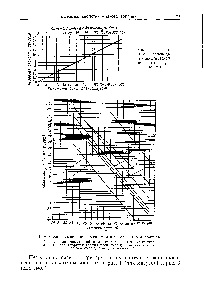
По-друге, при звичайній температурі і при відсутності аминного затверджувача ці речовини з епоксидними смолами практично не реагують, що дає можливість вводити їх в смоли задовго до використання, знижувати тим самим в'язкість і поставляти на об'єкти споживання в технологічно зручному вигляді. Відзначимо, що матеріал з невисокою в'язкістю вигідний і економічно, так як повніше використовується. Наприклад, через надмірно високої в'язкості смоли марки ЕД-16 велику кількість її залишаються в ємностях, в яких вона надходить, і пропадають. [C.55]
Застосування підігріву для зменшення технологічної в'язкості смоли зменшує життєздатність сполучного, прискорює процес полімеризації і погіршує просочувальні властивості смоли. [C.78]
Після підготовки корпусу готується композиція (безпосередньо перед її застосуванням). Попередньо тара з епоксидною смолою ЕД-16 поміщається в будь-яку посуд з водою і нагрівається до 60-80 ° С. В'язкість смоли при цьому значно знижується, що полегшує відбір певної кількості (зазвичай 100 г). Потім смола охолоджується до 30-40 ° С і при ретельному перемішуванні протягом 5 хв н неї вводиться по частинах пластифікатор (дибутилфталат). В отриману суміш також по частинах при ретельному перемішуванні додається наповнювач (алюмінієвий порошок. Який попередньо повинен бути висушений при 100-120 ° С протягом 2 год). Далі вводиться затверджувач (поліетиленполіамін, який попередньо витримується при 105-110 ° С протягом 3 год для видалення з нього низкокипящих компонентів). Поліетиленполіамін в приготовлену суміш з епоксидної смоли. пластифікатора і наповнювача додається невеликими частинами при ретельному перемішуванні, так як його введення викликає підвищення температури суміші. Тому необхідно стежити, щоб температура композиції не перевищувала 30-40 ° С. [C.246]
Після закінчення процесу полікондепсаціі (про який судять по в'язкості смоли-) починають сушку продукту. Для цього холодильник 14 перемикають на прямий і поступово, щоб уникнути сильного спінювання, створюють вакуум (спочатку з залишковим тиском близько 80 кПа (600), а потім 47- 53 кПа (350-400 мм рт. Ст.). У сорочку апарату подають пар під тиском 0,5-0,8 МПа (5 8 кгс / см). Після відгону основної кількості води температура маси починає підвищуватися. Сушку ведуть до досягнення певної температури каплепадения смоли. Потім тиск пара в сорочці зменшують і в реактор вводять олеїнову кислоту. [c.54]
Мал. 3. Температура зливу, в'язкість смол і мазуту в залежності від температури
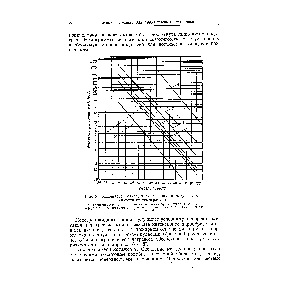
Найбільш загальноприйнята форма модернізації опалювальних газом смоловаренних котлів - забезпечення автоматичного управління температурним режимом. Так як в'язкість смол багатьох видів значно змінюється в дуже вузьких температурних межах. то автоматизація забезпечує хорошу і економічну смачиваемость покривається без ризику перегріву і загоряння. [C.298]
Завдання 1. Визначити в'язкість смоли (ГОСТ 10759-64). [C.77]
В'язкість алкида залежить від кількості полієнових кислот. містяться в жирних кислотах. використаних для синтезу алкида. Чим більше подвійних зв'язків витрачено в процесі синтезу алкида. тим менше їх кількість буде присутній в алкидном покритті при його старінні і тим, отже, менше буде пожовтіння. Залежність ступеня пожовтіння алкида від в'язкості смоли визначається наступним емпіричним рівнянням [c.117]
Реакційна здатність залежить від багатьох факторів. зокрема від тривалості храпения смоли зі збільшенням тривалості храпения вона зменшується. При кімнатній температурі час зберігання висококонцентрованих резолів зазвичай не перевищують 4 міс. при цьому в'язкість значно зростає (для переробки в пінопласт в'язкість смоли не повинна перевищу- пать 10000 мПа-с). [C.174]
Для очищення стічних вод, забруднених жирами, маслами, смолами, застосовують жироловки, масло і смолоотстойнікі. Для зменшення в'язкості смоли забруднену воду перед відкачуванням підігрівають паром до 60 ° С. [C.228]
В'язкість смол з бітумів, отриманих в результаті фурфурольной і крезольно очисток, настільки висока, що її не можна було визначити навіть при 90 ° С. Ці смоли - тверді й тендітні речовини. [C.41]
Відомо, що структура адсорбційного шару. отриманого при адсорбції з розчину, неідентичних тієї, яка реалізується за відсутності розчинника. Тому становить інтерес зіставлення результатів визначення товщини адсорбційних шарів. отриманих з розчинів і за відсутності розчинника. Це виявилося можливим лрі використанні олігомерних сполук, які, перебуваючи в в'язкотекучий стані з відносно невисокою в'язкістю, мають практично ті ж властивості, що і високомолекулярні сполуки. Вивчення реологічних властивостей олігомерів та їх розчинів було проведено в роботах [358, 359]. При дослідженні епоксидної смоли (ЕД-20) з молекулярною масою 500, наповненою 17% (об.) Скляного порошку, було знайдено, що смола ЕД-20 і система ЕД-20 - наповнювач в діапазоні швидкостей зсуву у від 10 2 до 10 з поводяться як ньютонівські рідини. т. е. їх в'язкість не залежить від режиму деформування. В'язкість смоли ЕД-20 закономірно зростає зі збільшенням вмісту скляного порошку. [C.186]
Умовна в'язкість смоли з затверджувачем по кулькового віскозиметру при 100 ° С, з 1 10 10 20 20 50 [c.212]
На рис. 14 показана залежність між (в'язкість і температурою смоли. Криві I п 2 дають нижчий і вищий межі. В'язкість смоли, отриманої З одного вихідної сировини. Змінюється в залежності від вологості і технології перегонки вугілля. [C.42]
Карбамідомеламіноформальдегідная смола ММ-6 являє собою сиропообразную рідина світло -сірого або жовтуватого кольору, що містить 60 2% сухих речовин. В'язкість смоли по ВЗ-4 становить 1,5-4,0 хв pH смоли 6,5-7,5. [C.304]
Порівнюючи наведені дані з даними для смоли напівкоксування прибалтійських сланців видно, що теплостійкість останньої вкладається приблизно в ті ж межі температур і часу нагрівання. Наведені в табл. 74 результати дослідів по нагріванню смоли напівкоксування прибалтійських сланців показують, що зниження часу нагрівання з 2 години до 1 години при 275 ° дає зменшення зростання в'язкості смоли проти вихідної величини з 112 до 66,7%, а нагрівання до 300 ° при тих же умовах- з 278 до 96,9% о. Нагрівання до 220 230 ° навіть протягом 1-2 годин не призводить до помітних змін смоли, проте з підвищенням температури термічні процеси напіврозпаду смоли швидко посилюються. Зі зменшенням часу нагрівання смоли до 20-30 хвилин нагрів до 280-300 ° цілком можливий без істотних змін якості залишку. [C.195]
Для точного дозування твердих і рідких компонентів використовуються вже наявні дозатори. До складу покриття входять смола, кокс, двоокис титану, розчинники і пластифікатор. Оскільки в'язкість смоли при ні 1кіх температурах досить велика, рекомендується заздалегідь довести температуру смоли до 20-25 ° С. Кокс і двоокис титану подаються в змішувач, що представляє собою порожній циліндр з порцеляновими кулями. Після змішувача суміш пігменту і наповнювача подається в живильник, звідки порціями надходить в дисольвер, [c.320]
Епоксидні смоли знаходять різноманітне застосування. Їх використовують в якості сполучного у виробництві склопластиків і плівкоутворювального в лакофарбової промисловості. як клейовий матеріал і як заливний компаунд. Епоксидні смоли тверднуть з малою усадкою. в початковій стадії вони є нізконлавкімі масами. В'язкість смоли в розплавленому стані настільки низька, що дозволяє змішувати її з сполучною без застосування розчинників. Розплавлена епоксидна смола має високу адгезію до скловолокну і склотканини, значно перевищує адгезію всіх вироблюваних в даний час отверждающихся смол. Склотекстоліт отримують склеюванням листів склотканини епоксидною смолою. змішаної з затверджувачем, і наступним затвердінням смоли. витримуючи склеєний пакет склотканини під тиском 1-2 кг / см Склотекстоліт, отриманий на смолі Епон. має наступні показники. [C.740]
Фізичні властивості масел і смол, що містяться в бітумі, залежать від природи нафти. Зі збільшенням вмісту парафіну в бітумі знижуються щільність і коефіцієнт рефракції масел і смол. Про парафінистої характер бітуму можна судити по в'язкості смол. Так, в'язкість смол високопарафінових бітумів (8-10% парафіну) в 1000 разів менше в'язкості смол, виділених з албанських бітумів. містять 0,5% парафіну. В'язкість смол з малопарафіністих албанських дорожніх бітумів при 20 ° С становить 10 пз (10 н-сек1м), з Ромашкінська 3% парафінів) - 10 пз (10 н-сек / ж), з Мухановське (8% парафінів) - 10 з 10 н-сек1.м), а з польських і саратовских (10% парафінів) - 105 пз (10И-сек м) [425]. [C.41]
Для очищення виробничих стічних вод, забруднених смолою. застосовують радіальні отстойннкі-смолоуловітелі (рисунок 16). Для зменшення в'язкості смолу перед відкачуванням підігрівають паром до температури 60 ° С. Накопичуються на поверхні масла перетікають в радіальні лотки, за якими вони відводяться в кільцевої збірник, розташований навколо центральної труби. Масло зі збірки відкачується насосом. [C.35]
Відстійна смола отримана при термолизе лігніну Ленінградського гидролизного заводу. При розгоні більше половини смоли залишається у вигляді пеку, що ускладнює переробку її в трубчастих печах і інших апаратах з зовнішнім обігрівом. Як показали досліди, при тривалому нагріванні до температури 80 ° в'язкість смоли значно зростає, смола стає малотекучей, що вказує на процес часткової полімеризації при цій температурі окремих її компонентів. [C.12]
Хід визначення. Перед визначенням в'язкості смолу або клей ретельно розмішують. Визначення проводять при 20 2С Лівою рукою зачерпують повну кружку смоли або клею, піднімають-її і дивляться всередину спостерігаючи за рівнем смоли або клею. Коли рівень смоли або клею в гуртку іонізігся і відкриється верхнє бічний отвір, включають секундомір я осту-іавлінают його в той момент, коли рівень досягне ііжнего бічного отвору. [C.144]
Ударна в'язкість смоли ЕКЬ-4221 зростає приблизно в два рази при введенні в неї еластомеру. Одночасно відбувається підвищення межі міцності нри розтягуванні і подовженні, тоді як спостерігається зниження модуля пружності і теплостійкості не надто велі1 о. Винятком є лише ПБ-3000, введення якого в систему призводить до зниження межі міцності. Межа міцності і розривне подовження при введенні в смолу СБАК зростають з 525 кгс / см і 1,9% до 840 кгс / см і 5%, що відповідає поліпшенню властивостей в процентному вираженні на 60% і 250%, відповідно. Максимальне падіння модуля становить лише 7% [c.261]
Подальше підвищення температури нагріву вже значно змінює в'язкість смоли. При нагріванні до 270 ° С протягом 60 хвилин в'язкість зростає до 75 ° Е, а при 120 хвилинах-до 9б ° Е. Нагревдо 315 ° підвищує в'язкість відповідно до 150 і 230 ° Е. Значно змінюється і температурна крива в'язкості. Чим вище температура. тим більше круту температурну криву в'язкості має смола таким же чином діє і час нагрівання. [C.147]
Хімія штучних смол (1951) - [c.47]