З кожним днем системи водяного охолодження стають все більш поширеними. Виробники випускають все більше готових рішень. Однак, не секрет, що всі системи по більш-менш прийнятною ціною програють хорошим повітряним кулерам, які нерідко коштують значно дешевше і набагато простіші в установці і експлуатації. Системи ж, дійсно перевершують можливості повітряного охолодження, обходяться покупцям в пару-трійку сотень євро як мінімум. Далеко не кожен користувач може дозволити собі такі витрати.
Значно скоротити витрати на побудову системи рідинного охолодження дозволяє використання автомобільних радіаторів від обігрівача і акваріумних або фонтанних помп. Такий мідний радіатор, з можливістю обдування двома вентиляторами на 120 мм, обійдеться приблизно в 1000-1200 рублів, алюмінієвий варіант - приблизно в 600 руб. помпа - в суму від 600 до 1000 рублів. Однак залишається найголовніша деталь - ватерблок.
Високопродуктивні моделі обійдуться більш ніж в півсотні євро. До того ж купити їх можна, як правило, тільки в онлайн-магазинах, що теж несе з собою певні труднощі з націнкою і доставкою (особливо якщо врахувати розміри нашої країни).
Вихід з даної ситуації лише один - виготовити водоблок самостійно. При наявності фрезерного обладнання - це лише справа техніки. В результаті виходить ватерблок, нітрохи не поступається за красою заводським. Продуктивність же залежить від обраної автором конструкції. Але, на жаль, не всі бажаючі мати недорогу систему водяного охолодження мають доступ до такого устаткування. І виходу, здавалося б, немає. Однак в такому випадку до чого було б писати настільки довгий вступ?
Насправді, вихід є, і процес створення ватерблока без спеціального обладнання буде описаний нижче.
Отже, перше, що слід зробити перед початком виготовлення - це ретельно розрахувати всі розміри, визначитися з конструкцією ватерблока і інструментом.
Вивчивши конструкції готових ватерблоков, теоретичні основи теплотехніки і гідродинаміки, а також керуючись здоровим глуздом, я вибрав контактний тип ватерблока з ромбоподібним перетином штирьків. Підстава було вирішено робити товщиною 5 мм, висоту штирьків - 8 мм. Форму і розмір штирьків після довгих роздумів було вирішено зробити наступними: сторона штирі 4 мм, пропив між штирями 2 мм, менший кут в ромбі близько тридцяти градусів. Природно, створення гарної речі вимагає відповідних матеріалів, тому вибір припав на мідну заготовку циліндричної форми перетином 60 мм. Мідь є найкращим металом по співвідношенню теплопровідності і ціни. Інструмент, який нам буде потрібно: лещата, ножівка по металу (головний інструмент), дремель з відрізними кругами великого діаметра, набір свердел, напилок або напилки (ніяких особливих вимог по формі не потрібно), наждачний папір різної зернистості, паяльник, маслянка з маслом, лінійка, олівець або тонкий маркер.
Для того щоб відпиляти заготовку потрібного розміру, відзначаємо за допомогою лінійки точки на заданій відстані від краю, постійно повертаючи заготовку. В результаті маємо сукупність точок на однаковій відстані від краю, далі просто з'єднуємо їх за допомогою маркера. Отримана лінія є лінією розпилу.
Далі затискаємо заготовку в лещата.
Заготівля в лещатах
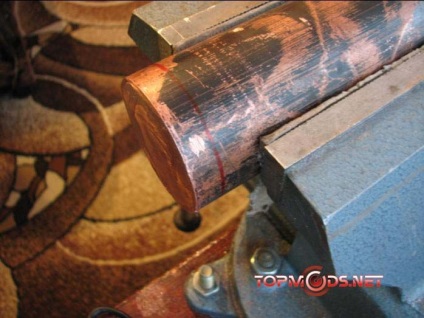
Для того щоб на заготівлі не залишалося слідів від губок лещат, я використовував підкладки з товстого картону. Практично всі роботи проводилися з їх використанням, так як естетична складова для мене теж була важлива.
Пиляти варто починати потроху, повертаючи заготовку для того, щоб розпил був без перекосу, і заготівля вийшла рівної товщини у всіх частинах. Вирішено було відпиляти заготовку товщиною 14 мм. На дану операцію у мене пішло близько півгодини.
Важливою деталлю є масло, яке слід капати в місце пропила, коли ножівка почала заходити в метал глибше, ніж на 3 мм. Це значно полегшить процес розпилювання, так як масло значно знизить дію сил тертя.
Наступним етапом є виготовлення штирьків. Для цього потрібно випиляти майбутній радіатор з масиву міді. Робиться це також за допомогою ножівки. Попередньо намітивши кордони робочої частини майбутнього радіатора, відпилюємо зайве з країв.
Видалення зайвого матеріалу з боків
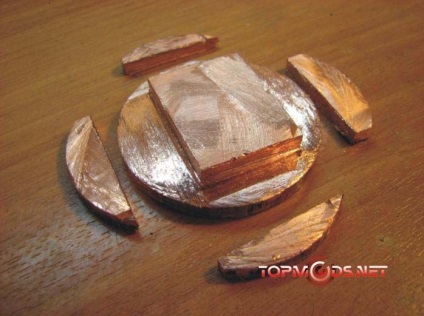
Процес виготовлення штирьків включає в себе три стадії. Спочатку дремелем намічаємо майбутні пропили. Це потрібно для того, щоб було легше почати пиляти ножівкою. Я вважав за краще використовувати для пропила ножівку, так як це виявився більш швидкий, тихий і менш витратний спосіб. В процесі розпилювання також капає масло (я використовував старий шприц на 5 мл і моторне масло).
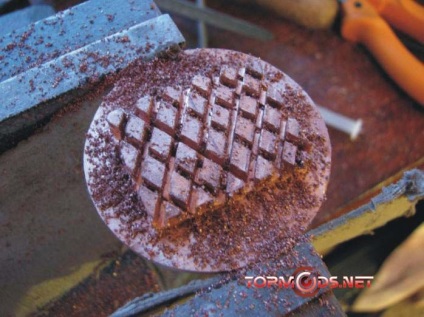
У фінальній стадії знову беремося за дремель, так як зробити пропили ножівкою до рівня підстави технічно дуже складно. Набагато зручніше використовувати кола досить великого діаметру. Я використовував кола на 45 мм, зроблені самостійно з відрізних кругів діаметром 125 мм. Поглиблювати пропили слід вкрай обережно. Мідь дуже в'язкий метал, тому зупинити дремель, навіть на максимальній потужності, досить просто. А це може призвести до перегріву двигуна дремеля або поломки насадки.
Вийшло підставу виглядає трохи грубувато, його можна обробити надфілем, щоб прибрати всі задирки і гострі кути, що я згодом і зробив.
Заготівля після поглиблення пропилов дремелем
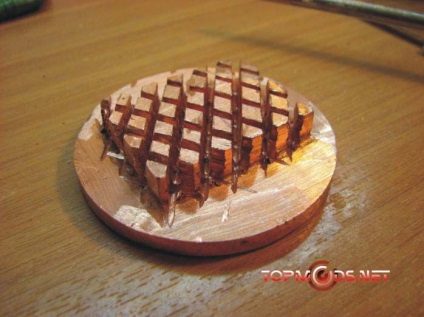
Маючи листову мідь, латунь або ж нержавіючу сталь, можна легко спаяти кришку ватерблока. Але тоді він вийшов би нерозбірний. До того ж подібних матеріалів у продажу виявити не вдалося. Тому вирішено було зробити кришку з двох пластикових кілець і сталевий пластини 1,2 мм завтовшки. А щоб сталь не коррозіровать, її планувалося залудити за допомогою паяльника.
Для кілець був узятий пластик 4,5 мм завтовшки. Звичайно, в даному випадку бажано використовувати один товстий лист, але такого у мене не виявилося, тому було вирішено виготовити два кільця. На аркуші я розмістив окружності діаметром 60 мм. Після чого з великого шматка були випив два квадрата, відповідно, зі стороною теж 60 мм. У центрах заготовок були просвердлені отвори, для того щоб стягнути їх болтиком і далі обробляти разом. За допомогою ножівки по металу я випиляв з них два кола.
Заготовки стягнуті болтиком і обробляються разом
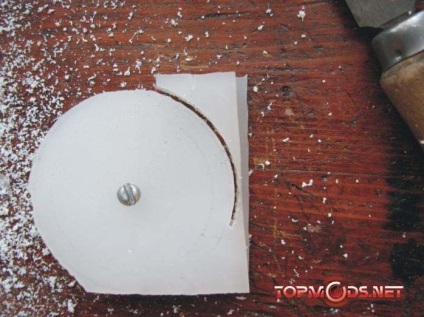
Для видалення внутрішньої частини свердлимо по периметру отвору і акуратно за допомогою надфіля пропилюємо перемички.
З листової сталі вирізаємо за допомогою дремеля коло діаметром 60 мм. Свердлимо отвори в ватерблоке і деталях кришки. Збираємо все воєдино за допомогою болтів М5 і обробляємо всі разом в лещатах для додання всім частинам одного розміру. Для усунення грубих слідів від напилка я використовував наждачний папір зернистістю 320.
Стягаємо деталі водоблока разом і вирівнюємо в лещатах
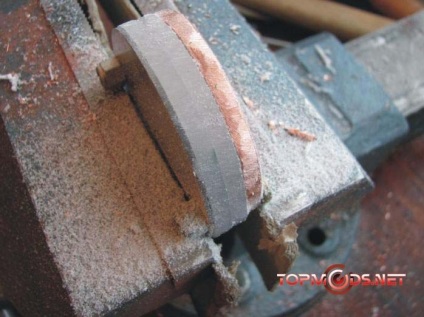
Практично ідеально рівна підошва ватерблока
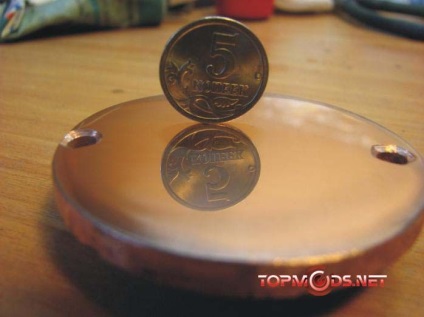
Важливим моментом в свердлінні підстави є те, що головки болтів повинні повністю йти вглиб матеріалу, так як на сучасних материнських платах часто зустрічаються конденсатори, рівні по висоті поверхні процесора і розташовані досить близько до сокету. Виступаючі болти можуть пошкодити їх при монтажі ватерблока. Для того щоб вони повністю йшли вглиб, слід використовувати болти з потайними головками і робити під них поглиблення за допомогою більшого свердла. Зокрема, я використовував свердло діаметром 8 мм.
Нарешті, всі частини ватерблока готові!
Готові частини ватерблока
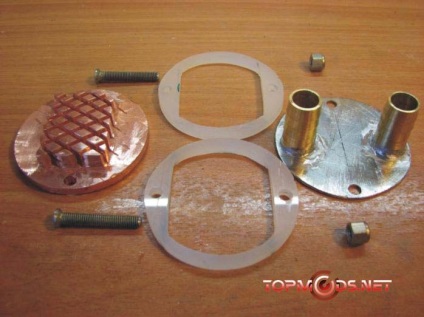
Наступним етапом стало виготовлення притискної пластини, без якої ватерблок марний. Після роздумів і трійки ескізів була визначена її форма. Як матеріал вирішено було використовувати алюмінієвий лист товщиною 2.5 мм, так як він практично не схильний до деформацій, що в притискної пластини дуже важливо. За допомогою стандартної мультікрепежной пластини від процесорного кулера були намічені отвори на аркуші. Далі за допомогою циркуля, лінійки та маркера був намічений контур майбутньої деталі.
Розмітка листа алюмінію
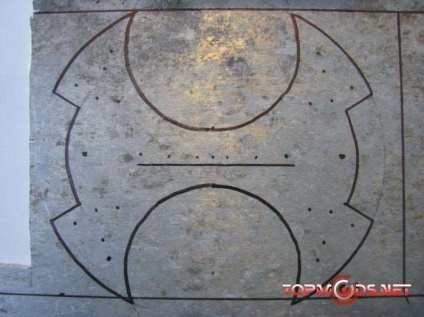
За допомогою ножівки по металу вона була випиляна. Далі були спиляні непотрібні кути заготовки. Для видалення внутрішніх частин в пластині були зроблені пропили на максимальну глибину, потім по периметру, де ножівкою це зробити неможливо, свердлом на 5 мм було насверліл необхідне число отворів. Свердлити їх в алюмінії - справа не настільки просте, як здається. Незважаючи на заздалегідь намічені за допомогою керна місця свердління, свердло в процесі часто йде в бік. Тому мною спочатку були просвердлені отвори свердлом на 4 мм, і після корекції вони рассверливают свердлом на 5мм. Після цього непотрібні частини були виламані за допомогою щипців.
Видалення зайвого матеріалу
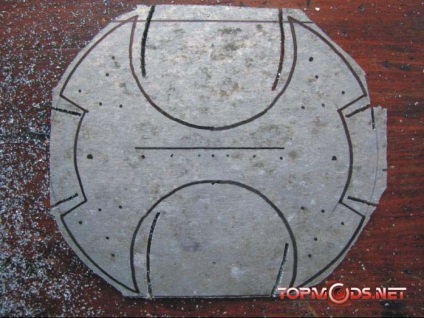
Висвердлювання отворів по контуру
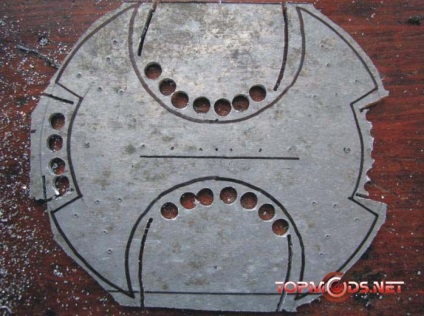
Після виламування зайвих шматків алюмінію пассатижами
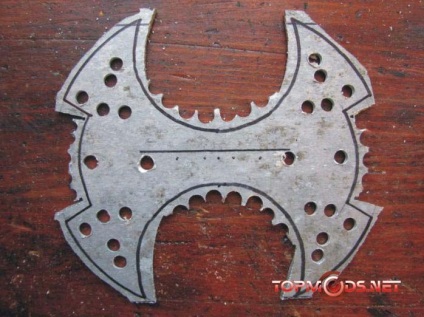
Наступний етап є найбільш трудомістким і копіткою. За допомогою напилка сточується зайвий метал, і контури наближаються до намічених кордонів пластини. При роботі я використовував в основному плоский напилок, а при обробці вигнутих кордонів - напівкруглий. Для того щоб прибрати задирки і сліди від напилка, я використовував ту ж наждачний папір. В результаті вийшла пластина, підходяща до всіх сучасних платформ і з вигляду нагадує кастети з гри Lineage II.
