При Залізнення в порівнянні з хромуванням застосовуються більш деше-ші електроліти, розчинні аноди. При цьому процесі можна застосовувати більш високі щільності струму. Вихід опадів по току становить 85. 90%. Процес відрізняється значно меншою тривалістю і вартістю і дозволяє відновлювати деталі з більшою величиною зносу (до 1,5 мм на сторону). Ско-кість залізнення вище, ніж при хромування, тому що електрохімічний еквівалент-стрічок заліза дорівнює 1,042 г / А-ч, а хрому - 0,324 г / А-ч.
При осталивание можливе отримання покриттів з досить високою твердістю (3000. 7000 Н / м 2) і по зносостійкості не нижче загартованої сталі 45. Ці позитивні сторони пояснюють його широке застосування при ремонті машин. Властивості покриттів залежать від режимів їх нанесення.
Твердість опадів електролітичного заліза збільшується при зниженні концентрації солей в електроліті, зростанні щільності струму, зниженні температу-ри, введенні в електроліти різних органічних і мінеральних добавок (рис. 57).
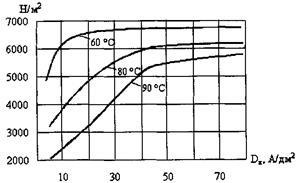
Малюнок 57 - Вплив температури і щільності струму на мікротвердість
Як анодів при осталивание використовуються пластини з малоуглеро-дист стали. У виробничих умовах приготування хлористого електро-літа ведуть шляхом травлення стружки з маловуглецевої стали 20 в соляній ки-слоті. Співвідношення катодного і анодного поверхні рекомендується витримай-вать рівним 2: 1. Рівномірне нанесення покриття на деталь забезпечується за рахунок надання анодам форми катодів (деталей).
Плавне збільшення щільності струму від нуля до заданої технічними ус-ловіямі величини протягом 5. 10 хв дозволяє отримувати хороше зчеплення опадів з основним металом.
Для приготування хлористих електролітів застосовують хлористе залізо FeC12 • 4Н2 О, невелика кількість соляної кислоти НС1 і деякі інші компоненти, наприклад, хлористий марганець МпС12 • 4Н2 О, хлористий нікель NiC12 • 4Н2 О, які вводять для підвищення міцності зчеплення і зносу-кістки. На катоді крім заліза осідає водень і потрапляє в кристалічну решітку осаду, підвищуючи його крихкість і схильність до утворення тріщин. Низькотемпературний відпустку (150. 200 ° С) не дозволяє знімати внутрішні на-напруги, а високотемпературний (450 ° С) хоча і робить позитивний вплив на міцність від утоми (підвищує), але знижує зносостійкість покриттів.
Концентрація хлористого заліза в електроліті може змінюватися від 200 до 700 г / л. Електроліти низькій концентрації містять 200. 220 г / л хлористого заліза. Він дає можливість отримувати опади високої твердості, але невеликої товщини (0,3. 0,4 мм).
Електроліт високої концентрації (650. 700 г / л FeC12 • 4Н2 О) дають мож-ливість отримувати покриття більшої товщини, але меншою твердості. Най-більшого поширення набули електроліти середньої концентрації, содер-жащие 400 г / л FeC12 • 4Н2 О, 2 г / л НС1 і 10 г / л МпС12 • 4Н2 О. Цей електроліт име-ет високий вихід по току і забезпечує хороші механічні властивості по-критий.
Для отримання якісних покриттів з інтенсивним протіканням про-процесу осталивание застосовують нестаціонарні електричні режими.
У практиці ремонтного виробництва знаходить застосування осадження ме-Таллі при реверсивному, асиметричному і імпульсному токах.
Покриття при осталивание наносять в сталевих ваннах, шляхом вневаннового проточного осталивание. Для виготовлення ванн використовують стали антихлор, і деякі хромонікелеві сталі, які добре працюють з хлористими електролітами при висо-кою температурі. Ванни для осталивание виготовляють також з фаоліту, вини-пласта, а також з титану.
Великогабаритні корпусні деталі відновлюють вневанновим способом.