Заточка і доведення ріжучих інструментів
Завершальними операціями виготовлення ріжучого інструменту є заточка і доведення. Хоча ці операції виконуються Заточника, слюсар-інструментальник повинен знати основні способи заточування і вміти заточити і довести найбільш прості і поширені інструменти - різці, свердла, розгортки.
Можна прийняти наступні варіанти технологічного процесу заточування інструментів: попередня заточка колами з зеленого карбіду кремнію одночасно державки і твердосплавних пластинки і остаточна заточка і доведення алмазними колами; остаточна заточка і доведення алмазними колами; обробка державки колами з електрокорунду, попередня заточка колами з зеленого карбіду кремнію і остаточна заточка і доведення алмазними колами.
Заточку твердосплавних інструментів колами зеленого карбіду кремнію на неавтоматизованому обладнанні слід проводити без охолодження, а на автоматизованому - з охолодженням водним розчином нітриту натрію з подачею його обов'язково в зону контакту кола і інструменту.
Заточку і доведення ріжучих інструментів здійснюють на точилах, універсальних і спеціальних стайках, а також на кругло, плоско і профілешліфувальні верстатах.
Точила призначені в основному для заточування різців всіх типів. При відсутності спеціальних заточувальних верстатів на точилах заточують і свердла.
Ручна заточка і доведення різців.
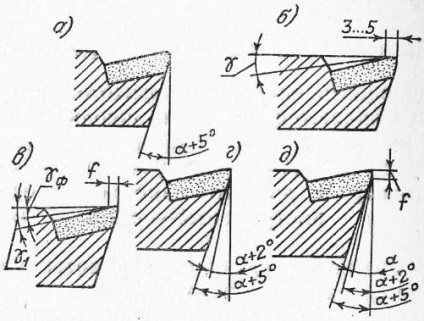
Мал. 1. Схема заточування різців.
У різців основну заточку здійснюють по задніх поверхнях, а допоміжну - по переднім, тому прийнята заточка подвійних кутів по передній поверхні, а потрійних - по головній задній поверхні.
Перед-заточуванням необхідно перевірити технічний стан загострювальної верстата, на якому повинні бути встановлені захисний прозорий екран, підручник і необхідні шліфувальні круги, ванна з охолоджувальною рідиною і кнопки «Пуск-стоп». Зазор між подручником і шліфувальним кругом повинен складати не більше 2 ... 3 мм. По висоті підручник повинен бути встановлений так, щоб при заточенні по платівці ріжучакромка була на висоті осі обертання шліфувального круга в горизонтальній площині. При заточуванні по державке на висоті осі обертання шліфувального круга повинна знаходитися опорна поверхня державки.
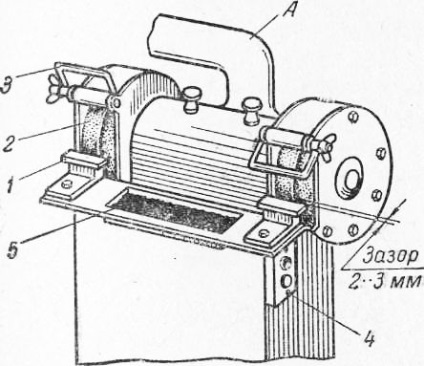
Заточка різця по допоміжної задньої поверхні (по державке) показана на рис. 3. Різець розташовують таким чином, щоб кут між головною і допоміжної поверхнями становив приблизно 90.
Заточка різця по передній поверхні приведена на рис. 3, ст. Заточку проводять на довжині 3 ... 5 мм під кутом у. Різець беруть рукою за державка, а великим пальцем лівої руки притискають його до шліфувального круга. Різець повинен бути встановлений таким чином, щоб головна ріжуча кромка а була розташована паралельно площині обертання кола. Для попередньої заточки по платівці застосовують шліфувальний круг з карбіду кремнію зернистістю 40 ... 25, а для остаточної - одночасно повертаючи його біля вершини за годинниковою стрілкою приблизно на 1/3 обороту,
2. Перевіряють кут нахилу ріжучої кромки до осі свердла. Свердло беруть в ліву руку, а шаблон - в праву і прикладають довгу робочу поверхню Б шаблону до бічної поверхні свердла; по щільності прилягання короткої робочої поверхні шаблону до ріжучої кромці А свердла визначають правильність заточування. Кут нахилу ріжучої кромки до осі свердла можна перевірити і кутоміром, попередньо встановивши його на кут 118 °.
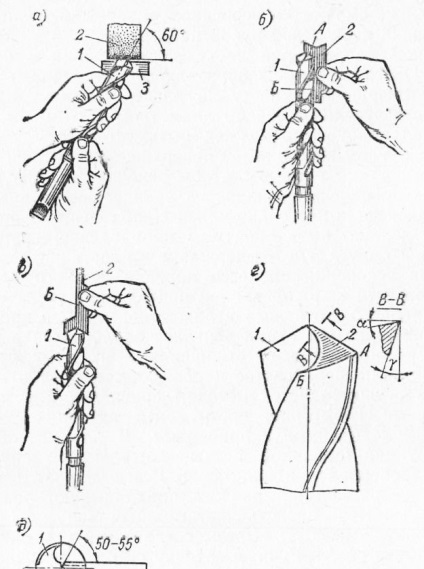
Мал. 3. Ручна заточка свердел.
3. Заточують другу ріжучу кромку. Прийоми заточування і контролю ті ж, що і для першої ріжучої кромки.
4 Перевіряють величину кута заточування різальних крайок при вершині свердла і їх довжину. У ліву руку беруть свердло, а в праву - шаблон і встановлюють шаблон на ріжучі кромки свердла, суворо поєднуючи довгу робочу поверхню Б шаблону з віссю свердла. За щільністю прилягання ріжучих крайок до робочої поверхні шаблону і їх довжині (вона повинна бути однаковою) визначають правильність заточування свердла.
5. Перевіряють задні кути а, що утворюються під час заточування нахилом задніх поверхонь. При правильній заточенню ріжучих крайок точки Б задніх поверхонь повинні бути трохи нижче вершин А різальних крайок.
6. Перевіряють кут нахилу поперечної кромки. Для свердел діаметром до 15 мм він повинен становити 50 °, а понад 15 мм - 55 °. Перевірка кута нахилу поперечної кромки шаблоном показана на рис. 108, о, де 1 - свердло; 2 - шаблон; А - ріжучакромка; Б - поперечна кромка.
Якість заточки рекомендується контролювати засвердленням. Якщо кути нахилу ріжучих крайок до осі свердла і довжина кромок однакові, то стружка буде виходити з отвору за двома спіральних канавках, а якщо кути неоднакові, то стружка буде виходити з однієї канавки.
Доведення розгорток. З усіх кінцевих інструментів тільки розгортки доводяться слюсарем-інструментальником, що пояснюється високою точністю і шорсткістю їх робочих поверхонь.
З ручних способів доведення розгорток найбільш високу якість забезпечує обробка за допомогою разжимного чавунного кільця.
Розгортка з надітим на неї чавунним кільцем встановлюється в центри і через хомутик отримує обертання від шпинделя верстата. На разжимное кільце наноситься доводочна паста. При обертанні розгортки і поздовжньому переміщенні чавунного кільця відбувається доведення по зовнішньому діаметру розгортки.
На деяких підприємствах доведення або калібрування розгорток здійснюють шляхом продавлювання їх через спеціальне каліброване кільце. Такі кільця для доведення циліндричних розгорток виготовляють зі сталі У12 твердістю HRC 62 ... 64.
Процес доведення полягає в наступному. Нова розгортка без фасок діаметром, рівним номінальному плюс 0,03 ... 0,06 мм, продавлюється під пресом через каліброване кільце відповідного розміру. В результаті ущільнення матеріалу на циліндричній частині зубів утворюється фаска шириною 0,03 ... 0,05 мм.

Мал. 5. Доведення розгортки.
Такий спосіб доведення завдяки наклепу зміцнює ріжучі кромки, забезпечує рівномірність висоти зубів калібрує розгортки і підвищує продуктивність праці слюсаря-інструментальника.
Регулювання розгорток. Розтискні ручні розгортки діаметром від 6 до 50 мм призначені для звичайного розгортання отворів. Розміри зношеної разжимной розгортки можна відновити шляхом її регулювання, в процесі якого діаметр інструмента може змінюватися на 0,15 ... 0,5 мм.
Корпус разжимной розгортки виготовлений порожнистим, а його робоча частина має від 3 до 6 (через 2-3 зуба) поздовжніх прорізів. Регулювання здійснюється обертанням гвинта, який переміщує кульку уздовж конічного отвору корпусу і таким чином розтискає розгортку. Після регулювання розгортка доводиться до необхідного розміру.
Виготовляються розсувні регульовані разверт-і перевагою яких є значно більші межі регулювання діаметрів (0.5 ... 3 мм). Більшість машинних розгорток володіє одним загальним недоліком - у міру зносу їх неможливо регулювати по діаметру. Щоб мати таку можливість, застосовують збірні розгортки з різними методами кріплення швидкорізальних і твердосплавних вставних зубів.
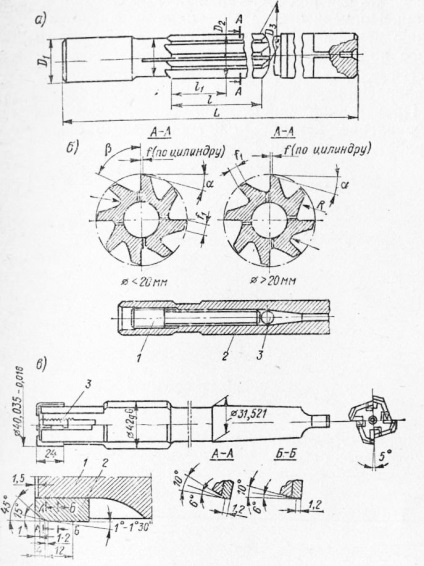
Мал. 6. Регулювання розгорток.
Великий інтерес представляють розгортки з механічним кріпленням пластин твердого сплаву. У пази корпуса вставляються твердо сплавні пластинки і притискаються до стінки паз рифленим клином. На кінці цього клина є заплечик, яким платівка утримується від неремеще. ня уздовж осі під дією осьових сил при развертьь вання. У міру зношування платівка висувається по осно-ванию паза, що має підйом в 5 °, що компенсує знос по діаметру. Знос торця пластинки компенсується перестановкою клина на одне рифлення в осьовому напрямку.
Наведена конструкція розгортки має заднє напрямок, яке може забезпечити більш точну обробку отворів.