Процес деасфальтизації гудронів або концен-витрачати зрідженими низькомолекулярними вуглеводні-родами, головним чином рідким пропаном, використовується як при виробництві високов'язких остаточ-них масел, так і компонентів сировини для каталіті-чеського крекінгу і гідрокрекінгу. На деяких заводах деасфальтізата є компонентом мало-сірчистих рідких котельних палив.
При не дуже жорстких вимогах до якості деасфальтізата, в основному по коксованості (2-3 замість 1,0-1,3% мас. По Конрадсону), наприклад для деасфальтізата - сировини крекінгу - розчині-ня компонентів ведуть пропан-бутанової сумішшю, а не технічним пропаном концентрацією 94- 98% (мас.). Вежі НП розроблений процес деас-фальтізаціі залишків бензинової фракцією, так званий процес Добені.
Смоли і особливо асфальтени, - компоненти сировини, найменш розчинні в рідкому пропані. На різній розчинності складових компо-нентов і грунтується використання пропану як де-Асфальтують розчинника. При температу-рах, близьких до критичної температури пропану (близько 96 ° С), розчинність складових частин мас-ляного сировини зменшується. З підвищенням темпе-ратури процесу від 75 до 90 ° С поліпшується якість деасфальтізата, але знижується його вихід, так як з розчину виділяються переважно компоненти з високими значеннями щільності, коефіцієнта заломлення і молекулярної маси; до них, в ча-стності, відносяться високомолекулярні поліціклі-етичні вуглеводні.
Процес деасфальтизації залишкового сировини технічним пропаном - рідиннофазної процес, здійснюваний з метою уникнення випаровування розчини-теля при тиску близько 4 МПа. Вихід деасфальті-затамувавши відповідної якості в значній мірі визначається характером сировини і коливається в ши-роком діапазоні - від 26 до 90% (мас.). З ужесто-ням вимог до якості деасфальтізата і збіль-личением коксованості сировини вихід деасфальтізата зменшується. Для одноступінчатих установок найбільш типовими є деасфальтізата в'язкістю від 18 до 26 мм / с при температурі 100 ° С.
Продуктивність установок деасфальтизації дуже різна - від кількох сотень до кількох тисяч тонн сировини на добу. На потужних установ-ках сировину піддають деасфальтизації в двох або більше паралельно діючих колонах. Розміри колон з жалюзійними нерухомими елементами в зонах контактування наступні: діаметр 2,4 3,6 м, висота 18-23 м. Питома навантаження живого поперечного перерізу колони 28-34 мм / год); об-щий обсяг сировини і пропану визначається, виходячи з їх кількостей і щільності при 20 ° С. Кратність пропану до сировини (масове співвідношення 2,5 -4,5: 1) вибирається тим більшим, чим вище вихід деасфаль-тізата. Процес ведуть в порівняно вузькому інтер-валі температур: верху колони 75-85 ° С, низу 50-65 ° С.
Виробництво нафтових бітумів є одним з термічних процесів нафтопереробки. Основні параметри термічних процесів, що впливають на асортимент, матеріальний баланс і якість одержуваних продуктів, - якість сировини, тиск, температура і тривалість термолізу (термічного процесу).
Залишкові бітуми - м'які легкоплавкі продукти, окислені - еластичні і термостабільні. Бітуми, одержувані окисленням крекінг-залишків, містять велику кількість карбенів і карбоїдів, які порушують однорідність бітумів і погіршують їх цементують властивості.
Залишкові бітуми виробляють з мазутів з високою концентрацією асфальтосмолисті речовин вакуумною перегонкою як залишок цієї перегонки. Нагадаємо, що мазут є залишком від атмосферної перегонки нафти.
Більш докладно зупинимося на окисленні гудронів або залишкових бітумів киснем повітря. Основними параметрами процесу є температура, витрата повітря і тиск.
Чим вище температура, тим швидше протікає процес окислення, але при дуже високій температурі прискорюється утворення карбенів і карбоїдів, які зраджують бітумів небажану підвищену крихкість. Зазвичай температуру підтримують на рівні 250 - 280 0 С.
Чим більше витрата повітря, тим менше потрібно часу на окислення. При надмірно великій витраті повітря температура в окислювальному колоні може зрости вище допустимої. Тому витрата повітря є основним регулюючим параметром для підтримки потрібної температури. Загальний витрата повітря залежить від хімічного складу сировини і якості одержуваного бітуму і складає від 50 до 400 м 3 / т бітуму.
Тиск в зоні реакції при його підвищенні інтенсифікує процес, і якість окисленого бітуму поліпшується. Зокрема, підвищується пенетрація бітуму при незмінній температурі розм'якшення. Зазвичай тиск коливається від 0,3 до 0,8 МПа.
Принципова схема отримання окисленого бітуму показана на малюнку нижче.
Принципова схема установки отримання окислених бітумів
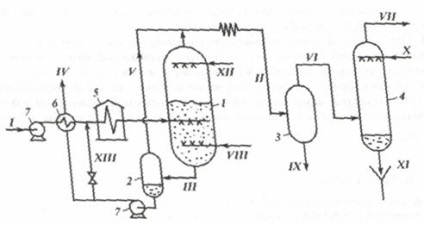
Нарешті, третій спосіб отримання бітумів - це компаундує. Спосіб цей є завершальною стадією отримання бітумів і використовує в якості компонентів як бітуми, отримані у вигляді залишків вакуумної перегонки, так і окислені бітуми. Крім того, одними з важливих компонентів компаундів є екстракти селективного очищення дистилятів масел і деасфальтізата, так як, будучи концентратом поліциклічної многокольчатой ароматики, вони додають бітуму еластичність і хорошу розтяжність.
Технологічний режим такої установки:
температура, 0 С:
сировини на вході в установку ......................... 100 - 120
окислення в реакторах ............................... 260
бітуму після холодильників ...................... 170
тиск, МПа:
повітря на вході в змішувачі ...................... 0,9
суміші на вході в реактора ........................... 0,8
витрата повітря, м 3 / м 3 продукту ........................ 100 - 150
ставлення рециркулят. сировину ............................ 6. 1