Вперше у світовій практиці підводний дугове різання вугільним електродом в лабораторних умовах здійснили в 1887 р М.М. Бенардос і проф.Д.А. Лачинов. Продовження ці роботи не отримали.
Тільки на початку 30-х рр. ХХ ст. були відновлені роботи по застосуванню зварювання під водою. У 1932 р К. К. Хренов розробив електроди для підводного зварювання і провів натурні випробування їх в Чорному морі. В середині 30-х рр. ручна дугова зварка під водою була застосована для ряду робіт, наприклад ремонту пароплава «Уссурі» і підйому пароплава «Борис». Однак в ті роки підводне зварювання застосовувалася епізодично.
У післявоєнні роки значно розширилися області застосування і обсяги підводного зварювання. Будівництво морських нафтопромислових гідротехнічних споруд, підводних трубопроводів різного призначення, ремонт судів на плаву, відновлення шлюзових затворів портових споруд та інших об'єктів виявилися немислимими без застосування підводного зварювання. Однак забезпечити прочноплотним шви і високу продуктивність праці існували тоді способи підводного зварювання не могли. Крім того, для виконання підводного зварювання по «мокрому» методу були потрібні водолази-зварювальники високої кваліфікації. «Мокрий» метод - процес, який наразі триває без видалення води із зони зварювання. У той же час ручна підводне зварювання володіла винятковою маневреністю і простотою обладнання, а для її здійснення були не потрібні спеціальні пристосування для видалення води із зони зварювання, що обумовлювало низьку вартість робіт. Спроби поліпшити механічні властивості зварних з'єднань і механізувати процес в кінці 50-х рр. ХХ століття не увінчалися успіхом.
У ці роки за кордоном розробляється «сухий» спосіб підводного зварювання. Спосіб заснований на застосуванні спеціальних населених камер різної конструкції. Камери можуть бути різного розміру і конструкції:
- великі глибоководні, коли і місце зварювання і зварник ізольовані від водного середовища за рахунок подачі повітря в камеру і відтискування води за її межі;
- водолазні дзвони, щоб забезпечити виконання зварювання в «сухий» середовищі, хоча сам зварник знаходиться по пояс у воді;
- портативний сухий бокс, який забезпечує «суху» середу тільки в зоні зварювання.
Застосування будь-якого виду показало, що зварні шви виходять такої ж якості, як і на суші, але є й істотні недоліки, які не привели до широкого поширення «сухий» підводного зварювання.
При застосуванні глибоководних камер, як показала практика, необхідні попередня підготовка і спеціальне технічне супроводження. Виявилося, що необхідно розробити і виготовити камеру потрібної конструкції, підготувати технічні засоби (плавучі крани, насоси та інше устаткування), задіяти обслуговуючий персонал. Такий варіант виконання підводного зварювання виявився досить дорогим.
Два інших варіанти виявилися менш дорогими, але і менш маневреними і універсальними, ніж «мокрий» спосіб підводного зварювання. У 1965 р в нашій країні були розпочаті дослідження, що дозволили усунути недоліки «мокрого» способу.
Аналіз підводного зварювання «мокрим» способом показав, що основними причинами низьких механічних характеристик зварних швів є пористість за рахунок розчинення водню, шлакові включення за рахунок окислення компонентів металу киснем, збільшення швидкості охолодження за рахунок контакту нагрітого металу з водою. Низька продуктивність підводного зварювання не може бути подолана при використанні покритих електродів, так як зміна їх через кожні 1-2 хвилини є в підводних умовах складної операцією, а козирок обмазки погіршує спостереження за формуванням шва.
Проведені роботи показали, що найбільш перспективною є напівавтоматичне зварювання. Метод досить маневрений і універсальний, а механізована подача дроту дозволяє тривалий час вести процес зварювання без перерв. Оскільки дріт має менший діаметр, ніж електрод, і не має покриття, створюються сприятливі умови для спостереження за формуванням зварного шва.
Застосування суцільного дроту без захисту зони зварювання і з подачею захисних газів (аргон, вуглекислий газ) не забезпечили отримання необхідних механічних властивостей зварних з'єднань. Подальші дослідження показали, що ефективний захист зони зварювання можлива при використанні порошкових самозахисних дротів. Розроблена в Інституті електрозварювання ім. Є.О. Патона порошковий дріт марки ППС-АН1 діаметром 1,2-2,0 мм вперше дозволила провести підводне зварювання «мокрим» способом з отриманням якісних зварних з'єднань. При сучасному рівні техніки дугове зварювання порошковим дротом «мокрим» способом здійснюється на глибині до 30 м. Існують серйозні обмеження по номенклатурі металів, придатних для зварювання таким способом. Зі збільшенням глибини різко змінюються властивості дуги, інтенсифікується взаємодія розплавленого металу з навколишнім середовищем і стає проблематичним отримання якісного з'єднання. Крім того, слід враховувати, що «мокрий» спосіб підходить для глибини, доступною для людини в скафандрі - не більше 120-160 м.
Розробка спеціального устаткування для підводного напівавтоматичного зварювання також зажадала рішення ряду складних завдань, які були успішно завершені створенням напівавтомата для підводного зварювання А1660.
Механізована підводне зварювання застосовується для будівництва та ремонту металоконструкцій різного призначення. Проводяться роботи по подальшій механізації і автоматизації процесу підводного зварювання. Розробляються автомати, які зможуть здійснювати зварювання під водою з мінімальною участю людини. Удосконалюються системи дистанційного спостереження та управління процесом.
Не виключена можливість застосування в зазначених умовах контактного стикового зварювання оплавленням. Попередні експерименти і дослідно-промислова перевірка розробленої в ІЕЗ ім. Є.О. Патона установки для автоматичної стикового зварювання оплавленням труб під водою при будівництві і ремонті морських трубопроводів підтвердили перспективність використання цього способу зварювання.
Очевидно, що в найближчому майбутньому необхідно буде вдосконалювати як «мокрий», так і «сухий» способи зварювання, а також розробляти нові механізовані способи зварювання та обладнання, придатні для використання на кілометровій глибині.
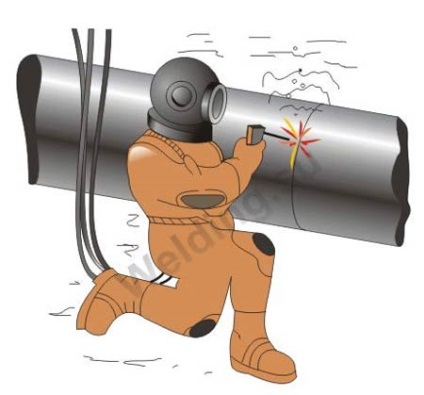
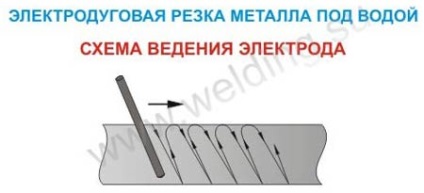
Мал. 1. Зварювання та різання металу під водою. Електрична дуга, що горить під водою, знаходиться в газовому міхурі, виникає через випаровування і розкладання води. Для стійкого горіння дуги на електрод наносять товстий шар покриття. При горінні дуги виступає шар покриття утворює козирок, що сприяє утриманню газового міхура навколо дуги і сталого її горіння.
Мал. 2. Схема ведення електрода при різанні металу під водою
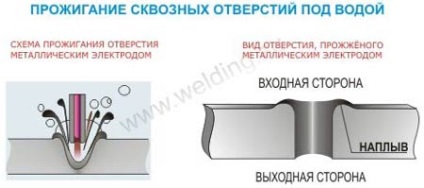
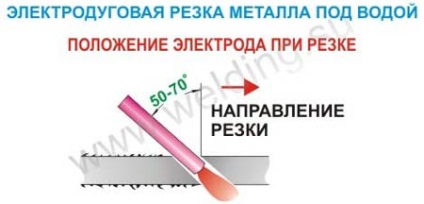
Мал. 3. Схема пропалювання отвори металевим електродом під водою.
Мал. 4. Електродугова зварювання під водою. Положення електроду при різанні
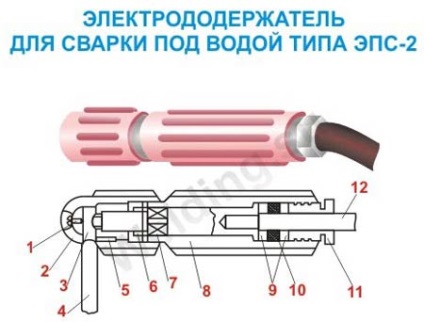
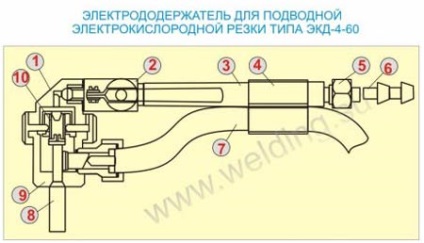
Мал. 5. електротримачі для зварювання під водою типу ЕПС-2. 1 - стопорний гвинт; 2 - Стакан; 3 - Контактний наконечник; 4 - Електрод; 5 - Шпонка; 6 - Зажимная гайка; 7 - Стрижень з квадратним виступом; 8 - Рукоятка; 9 - Латунні кільця; 10 - Гумова кільце ущільнювача; 11 - Сальникова втулка; 12 - Зварювальний кабель.
Мал. 6. електротримачі для підводного електрокіслородной різання типу ЕКД-4-60. 1 - Корпус; 2 - Кисневий клапан з важелем; 3 - Трубка; 4 - Обойма; 5 - Накидна гайка; 6 - Ніпель; 7 - Зварювальний кабель; 8 - Електрод; 9 - Головка; 10 - іскрогасні камера.
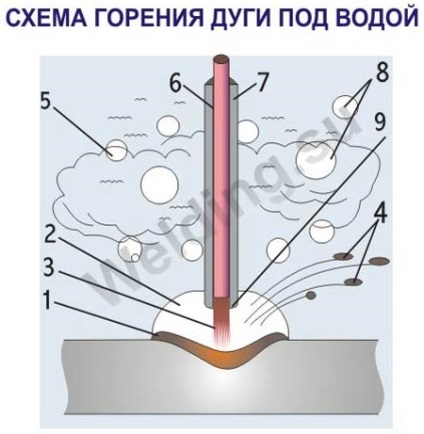
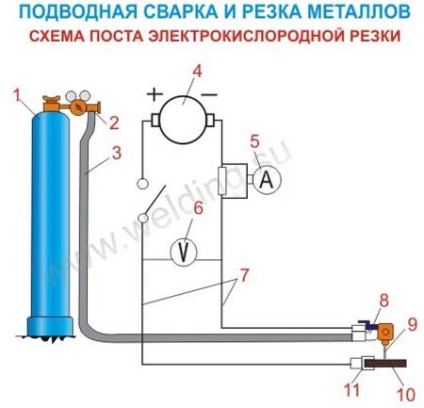
Мал. 7. Схема горіння дуги під водою. 1 - Зона розплавленого металу; 2 - Газовий міхур навколо дуги; 3 - Дуга; 4 - Бризки металу; 5 - Хмарка газу; 6 - Стрижень; 7 - Обмазування; 8 - Бульбашки газу; 9 - Козирок.
Мал. 8. Схема поста електрокіслородной різання під водою. 1 - Балон з киснем; 2 - Редуктор; 3 - Кисневий шланг; 4 - Зварювальний генератор; 5 - Амперметр з шунтом; 6 - Вольтметр; 7 - Зварювальні кабелі; 8 - Електрокіслородная держатель; 9 - Трубчастий електрод; 10 - розрізати виріб (лист); 11 - Струбцина
Технологія дугового зварювання та різання під водою
У рідких середовищах, в тому числі і в воді, можна отримати досить стійкий дугового розряд, який, утворюючи високу температуру і маючи велику питому теплову потужність, випаровує і розкладає навколишнє рідина. Пари і гази, що утворюються при дуговому розряді, створюють навколо зварювальної дуги газову захист в формі газового міхура, т. Е. По суті дуга горить не в воді, а в газовому середовищі. Газ складається в основному з водню, що утворюється при термічній дисоціації водяної пари, а що утворюється при дисоціації кисень окисляє матеріал електродів.
Стійка зварювальний дуга при використанні звичайних джерел живлення зварювальної дуги може бути отримана при застосуванні вугільних або металевих електродів.
Електроди, застосовувані для підводної різки, повинні мати товсте водонепроникне покриття, яке охолоджується зовні водою і тому плавиться повільніше стрижня електрода, утворюючи в кінці електрода «козирок». Утворився козирок виступає вперед у формі невеликої чашечки і сприяє сталому існуванню газового міхура і горінню дуги.
Водопроникність покриття негативно впливає на стійкість горіння дуги, так як вода, що випаровується у гарячій поверхні електродного стрижня, руйнує покриття і зриває його шматками зі стрижня. Водонепроникність досягається в основному просоченням покриття парафіном. В якості покриття застосовують склад з суміші залізного сурику (80%) і крейди (20%) з додаванням для їх зв'язування рідкого натрієвого скла. Нанесення покриття виробляють зануренням. Електродним стрижнем служить зварювальний дріт Св-08 або Св-08ГС.
Величину струму підбирають з розрахунку 60 - 70 А на 1 мм діаметра електрода. Напруга дуги під водою трохи більше, ніж на повітрі. Різка під водою застосовується при ремонті суден, пристрої різних гідроспоруд та ін.