Дзидока (автономізація) (англ. - аutonomation, яп. - дзидока) - принцип роботи виробничого обладнання, яке здатне самостійно виявити проблеми, наприклад, несправність обладнання, дефекти в якості продукції або затримка у виконанні роботи, відразу зупинитися і сигналізувати про необхідність надання допомоги . Цей підхід по-японськи називається дзидока (Jidoka). Він виключає перевиробництво, важливу складову виробничих втрат, і запобігає виробництво дефектної продукції. У автономізації верстати наділяються інтелектуальними здібностями, через що її називають розумною автоматизацією. На противагу повної автоматизації на передньому плані стоїть не обсяг випуску, а якість і «здатність автономно запускатися і зупинятися». Кожна машина в робочому процесі може працювати без постійного нагляду з боку оператора і сама відключатися у разі дефекту, так що не браковані деталі не передаються на наступний процес (див. Схему 1).
Приклад. Прес штампує виріб з металевої заготовки. Час від часу металева заготовка розбивається під ударами преса. Продукція, вручну технічні огляди потребували б в робочому, який переглядає кожен виріб, щоб перевірити, розбите воно. Якщо дефектний процес триває, зіпсоване виріб посилається на лінію для подальшої збірки. Це тягне за собою виготовлення кінцевих продуктів з дефектами, які повинні або перероблятися в кінці, або перетворюватися в лом, звідси підвищуються витрати. Застосування автономізації полягало в тому, щоб транспортувати готовий виріб до пристрою, який містить ваги. Якщо виріб стабільно не входить в пристрій, або вага лежить поза прийнятного діапазону, прес зупиняється, і «сигналізує тривогу» робітникові.
- забороняє виробництво несправних деталей;
- оператор може контролювати роботу кількох машин;
- на відміну від повністю автоматизованих систем виробничі системи з автономізацією залишаються гнучкими.
Схема 1. Принцип дії розумних машин - автономізація.
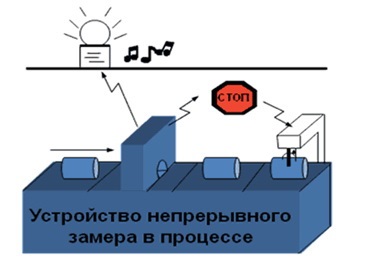
Процес контролю якості в дзидока грунтується на наступних етапах:
- Визначити несправність.
- Зупинитися.
- Зафіксувати або виправити безпосередню передумову.
- Дослідити причину і визначити контрзахід.
Таким чином, в умовах автономізації, замість того, щоб чекати завершення всього процесу, щоб інспектувати готовий продукт, можна на більш ранній щаблі визначити неякісний виріб і скоротити шлюб. Працівник заохочується виконувати самоконтроль своєї роботи, або технічний контроль робочого місця до того, як зафіксується дефект і лінія зупиниться.
Ефективність автономізації полягає в наступному:
- Підвищується швидкість виявлення дефектів.
- Зменшується витрати, в той час як знижується рівень бракованих виробів і несправність устаткування, яке застосовує;
- Запобігає подальша робота з використанням дефектних виробів;
- Поліпшується мотивація обслуговуючого персоналу, особливо якщо робочі навчаються, щоб вирішувати проблеми;
- Може зменшуватися прямі витрати по зарплаті, оскільки створюється можливість одному робітникові одночасно контролювати кілька машин.
Впровадження автономізації включає наступні принципи:
- Оптимізація, виробничого конвеєра, пристроїв, пристосувань: усунення переміщень без вантажів, усунення вантажно-розвантажувальних операцій, поліпшення швидкості руху, подачі інструменту.
- Впровадження економних верстатів і пристроїв: розміри машин і продуктів повинні відповідати умовам робочого місця.
- Пристосування машин потоку: продуктивність машин повинна підходити для часу такту потоку.
- Спрощення переналагодження: поділ переналагодження на внутрішню і зовнішню з використанням Швидкозатискний пристосування.
- Оснащення машин пристроями для автономного визначення дефектів і подальшого виконання всіх процесів щодо усунення дефектів.