Гуд Вуд фотографії з виробництва.
Як виробляють клеєний брус для дерев'яних будинків.
escogido7 пише в kak_eto_sdelano Питання про власну житлоплощі виникає рано чи пізно у кожної людини. Хвилює ця проблема і мене в тому числі. Нещодавно, побувавши на одній виставці присвяченій будівництву будинку я зацікавився питанням, з чого і як робляться будматеріали для простого дерев'яного будиночка, який за ціною доступніше, ніж найдешевша однокімнатна квартира в столиці. Я домовився з заводом Good Wood про екскурсію на виробництво, і днями з'ясував як це робиться.
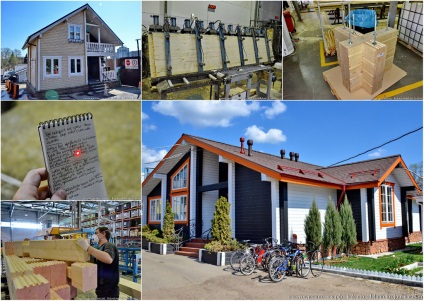
Сьогодні в спеціальному репортажі для kak_eto_sdelano ми подивимося як виробляють брус з якого будують сучасні дерев'яні будинки.
Все починається з того, що на завод надходять ось такі пакети з дерев'яними дошками. Спеціаліст виробництва перед початком виробничого циклу перевіряє кожен такий пакет на відповідність якості.
Вибірково перевіряються дошки і після підтвердження якості вони відправляються на перший етап. Якщо відсоток дефектів і сучковін на заготовках перевищують допустимі норми, то такий пакет відправляється назад постачальнику.
Сировина, з якого буде зроблений брус - з сосни і ялини.

Територія заводу не маленька, далеко можна бачити, що будується корпус, в якому буде проводиться більше заготовок ніж в інших цехах.
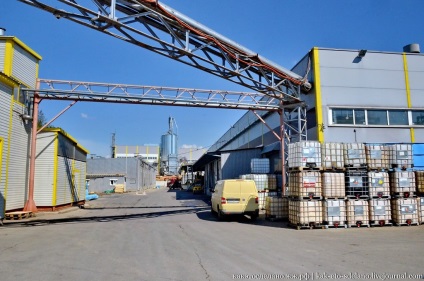
Після того, як дошки обрані, вони збираються в сушильний пакет - набір з заготовок, який буде поміщений в сушильну камеру. Дошки попередньо перетягують такою стрічкою, щоб в процесі сушіння вони не деформувалися.
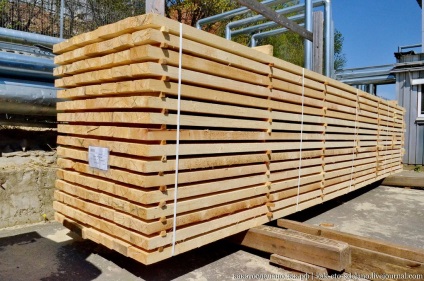
На виробництві 6 сушильних камер об'ємом до 75 куб.м.
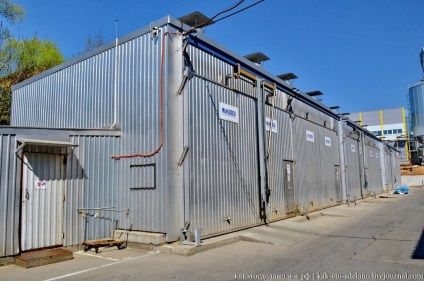
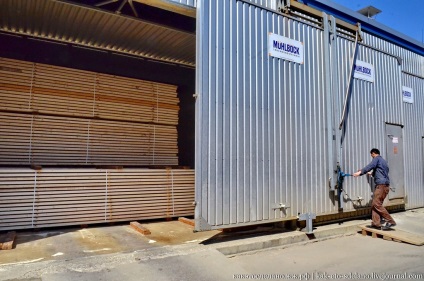
Пакети з дошками знаходяться в камері 6-8 днів, при температурі 65-68 градусів. Сушильна камера забезпечена датчиками вологості повітря, температури, щоб стежити за правильною технологією сушіння дощок.
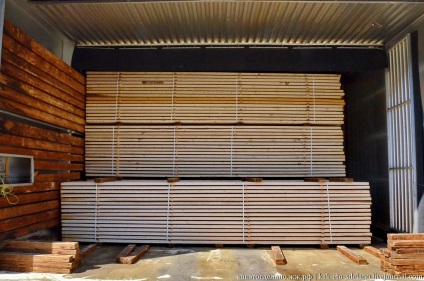
Це фото свежесклеенного не оброблені бруса, тут можна бачити, як з дощок різного розміру роблять єдиний міцний брус. Про нього я розповім далі.
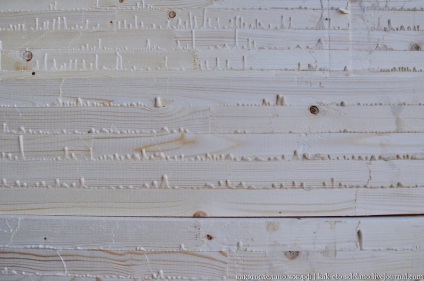
Але повернемося до виробництва. Після сушіння пакет з дошками потрапляє в цех.
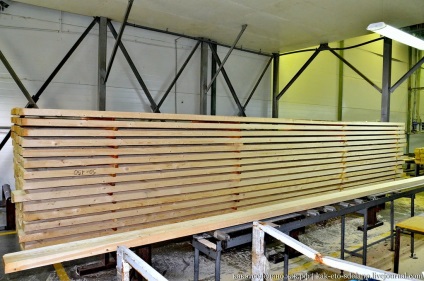
Тут він проходить через верстат, який струже дошку з усіх чотирьох сторін. На цьому етапі робітники проводять візуальний контроль, кожна дошка заново перевіряється на наявність дефектів і сучковін. Тут же визначається які дошки підуть на внутрішню і зовнішню сторону майбутнього бруса. Красивіші дошки, з меншою кількістю сучковін йдуть на зовнішню сторону.
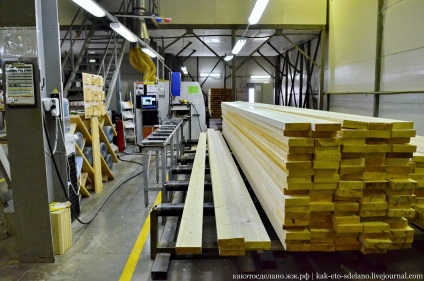
Як я говорив, дошки з яких робиться брус з сосни та ялини. Так як вони схожі за структурою волокон, їх можна без особливих проблем склеювати один з одним. І ще інформація для спостережних - дошки ялини і сосни можна відрізнити по сучковінам - у сосни вони крупніше, ніж у ялини.
Далі, дошки склеюють. Тут апарат був відключений тому можна на фото з сусіднього цеху побачити склеює апарат в роботі.
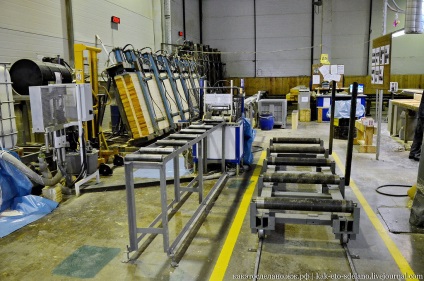
Ось таким дощем клей покриває дошку з одне сторони.
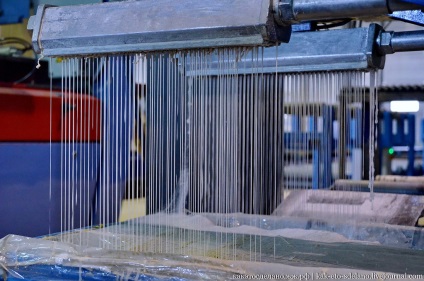
Зайве забирається валком. Залежно від кожного індивідуального замовлення брус роблять / склеюють з декількох дощок різної довжини і ширини. Мало не забув сказати - на виробництві не роблять заздалегідь брус. Його виготовлення починається тільки після того, як клієнт замовив будинок (вже підготував фундамент) або окремі деталі.
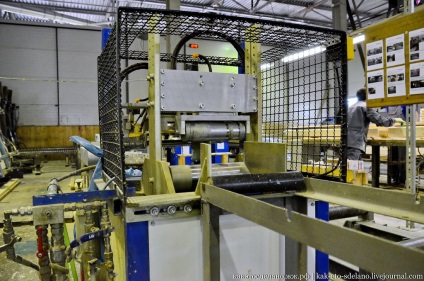
Клей використовується у виробництві пройшов сертифікацію на безпеку і не містить формальдегідів і небезпечних для людини речовин.

У цій бочці затверджувач, який змішується з клеєм безпосередньо перед склеюванням.
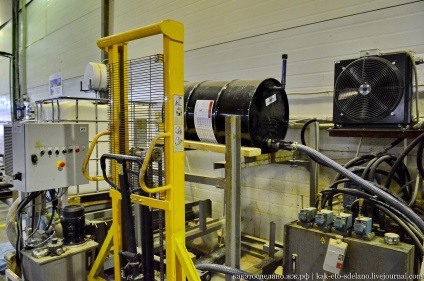
Після того, як дошки змащені клеєм і правильно укладені, вони поміщаються під прес, в якому знаходяться 40 хвилин. Потім їх виймають і вони "відпочивають" ще дві години до того, як потраплять на наступний етап.
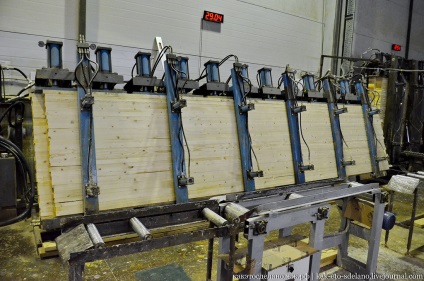
Далі заготовки пересуваються на наступний етап, але перед цим заготівля бруса знову проходить через верстат, який обробляє його з чотирьох сторін.
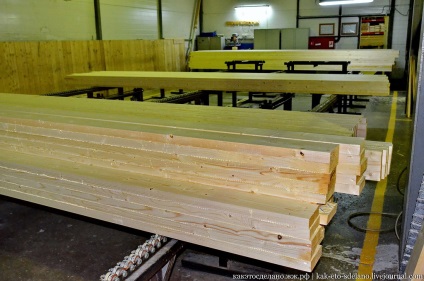
Так виглядає брус після профілювання, але і це ще не все. Як бачите торці нерівні, і бруси розрізані на потрібні деталі.
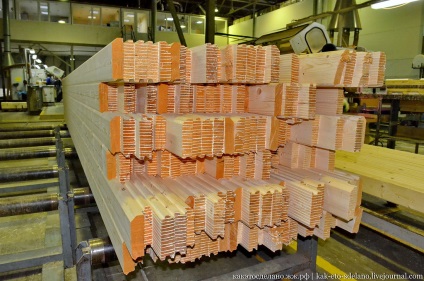
До речі, точність нарізки профілю визначається такими лазерними датчиками.
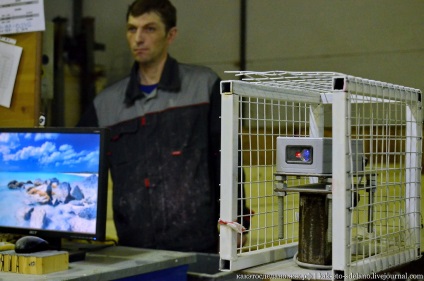
Спробував пропалити свій блокнот, але чомусь не вийшло.
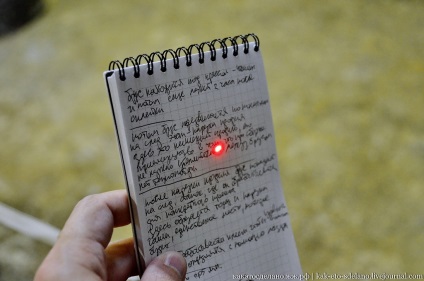
Ще одна приємна деталь - кулер з прохолодною водою. Дуже потрібна річ на виробництві.
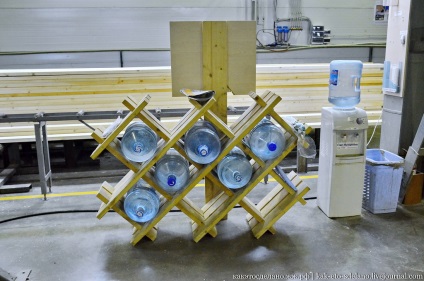
Але ми відволіклися. Далі брус потрапляє на верстат, який обрізає торець і.
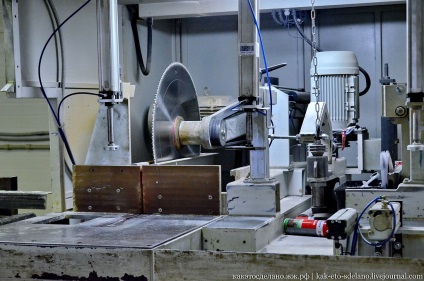
нарізає чашу - поглиблення в брусі, необхідне для поперечної збірки. Чаша, до речі, єдине місце, яке буде обкладено утеплювачем. При складанні стін будинку утеплювач не використовується, тільки в місцях стику.
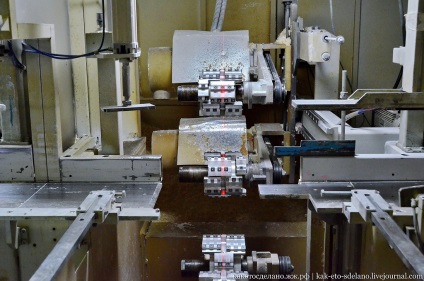
Ну, ось і готові деталі для будинку. Торці обробляються торцевих герметиком.
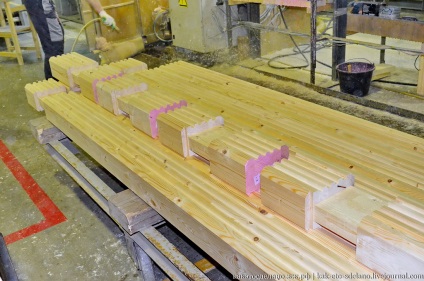
А це вже готовий пакет для будинку. Таких для одного будинку буде кілька.
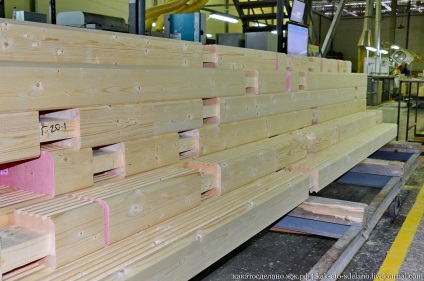
Кожна деталь маркується папірцем зі штрих-кодом, в якому міститься вся інформація про брусі, аж до того, де він повинен бути покладений в будинку.
І ще одна деталь: після підготовки кожної такої партії для окремого проекту, робляться контрольні зрізи, які потім досліджуються в заводській лабораторії на відповідність якості. Зріз нагрівається і охолоджується до певної температури протягом 50 циклів, які імітують зиму і літо, тобто теоретично будинок з такого бруса може простояти 50 років.
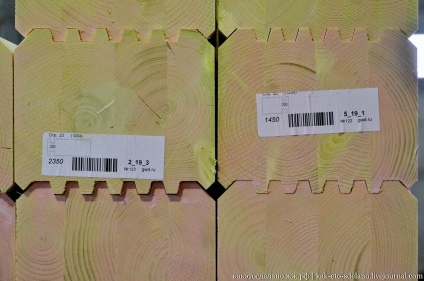
За процесом стежить і камера, яка, як мені сказали показує процес виробництва онлайн відвідувачам сайту заводу.
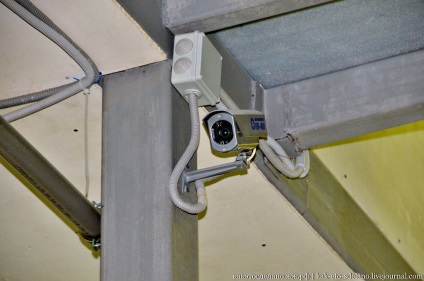
На моніторах відображаються деталі виробничого процесу. На фотографіях - проекти, які здійснюються в даний момент.
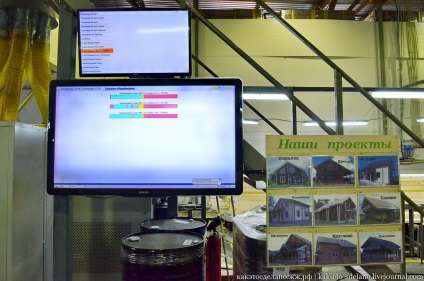
На прикладі цього зразка, який стоїть в цеху можна бачити як виглядає кут стін будинку. Такими залізними штирями скріплюються тільки кути, а по решті довжині стін бруси насаджуються на дерев'яні штирі.
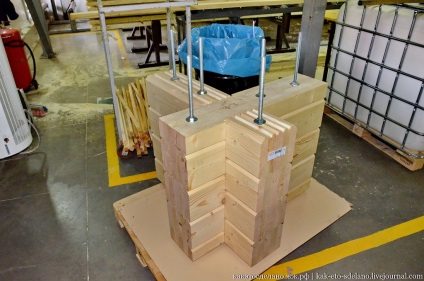
Йдемо на наступний етап. Тут готовий брус обробляється антисептиком для вогне-біозахисту. Він оберігає його від жучків-короїдів, цвілі, гниття і запобігає будинок від пожежі. Повинен уточнити, що дія антисептика звичайно не вічне, але він зберігає властивості бруса на деякий час, і в разі пожежі будинок не запалиться як сірник, тому що при обробці антисептиком з дерева виводиться кисень.
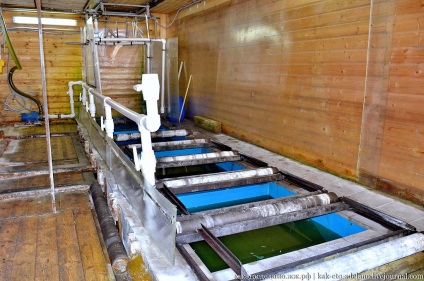
При необхідності брус може прийняти антисептичні ванни.
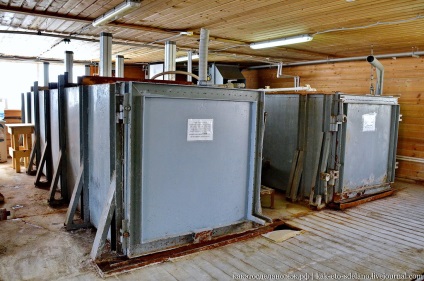
Після цього етапу, можна сказати, що процес виробництва і підготовки бруса для замовника завершено. Однак це ще не все.
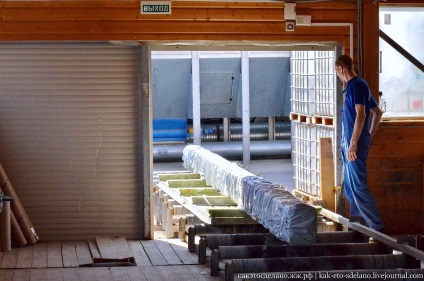
Після обробки антисептиком брус збирають знову в такі пакети готові до відправки клієнтові.
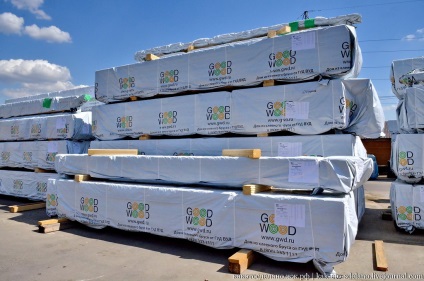
На кожному пакеті інформація про замовника і вмісті. Зверніть увагу на слова "хв. Вінець 20" і "макс. Вінець 43" - це означає, що в цьому пакеті є деталі, які підходять для складання від 20 "шару" стін до 43. Це потрібно для того, щоб не розкривати всі пакети в пошуках потрібних деталей - всі вони можуть виявитися в одному пакеті, до певного етапу зборки.
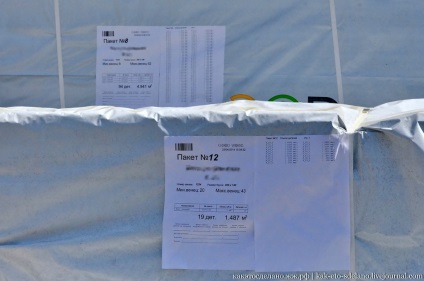
Ми побачили практично весь ланцюжок виробництва, проте, наша екскурсія не завершена, ми йдемо в наступний цех, щоб дізнатися ще деякі деталі. До речі, зверніть увагу на цей будиночок, тут знаходиться один з офісів компанії, в якому працюють менеджери з продажу, фахівці колл-центру, архітектори і конструктори. Як розумієте, він повністю зроблений на цьому виробництві і зібраний працівниками компанії.
До речі, про велосипеди на фото - вони безоплатно купуються компанією будь-якого працівника виробництва, який готовий їздити на ньому з дому до роботи і назад). Ще одна цікава інформація про компанію: працівникам виробництва, які кинули курити видається премія в 10 тис. Руб! Правда, якщо працівник не справляється з нестачею нікотину і знову починає курити, його штрафують на 15 тис).
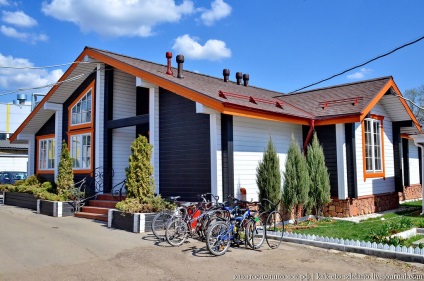
Наступний цех виробництва більше розміром, тут більш нові, німецькі верстати, тут роблять брус довжиною до 12 метрів і супербрус, перетин яких більше, ніж у тих, які ми бачили раніше.
У цьому цеху брус також роблять з окремих дощок, які зрощують за допомогою клею в довгу дошку.
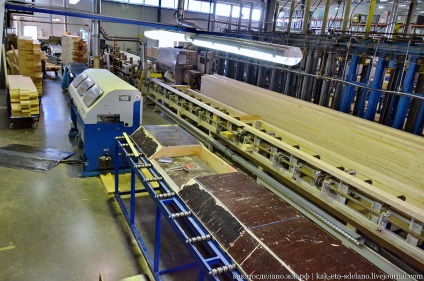
Ділянки дощок з дефектами і сучковінамі, які можуть пошкодити майбутньому виробу вирізають. На цьому фото - відхід виробництва.
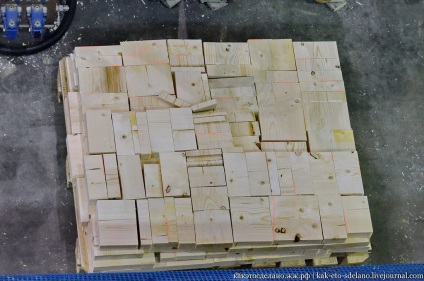
А це готові дошки, з яких будуть клеїти брус. Тут відбувається вся та ж технологічний ланцюжок, що ми бачили раніше, тому не буду повторюватися.
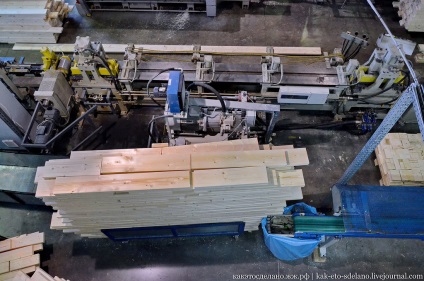
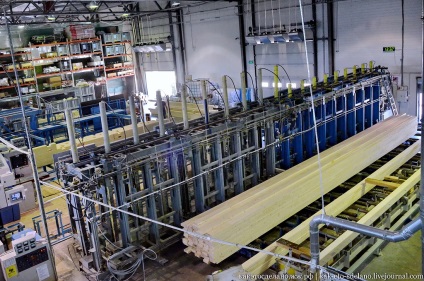
Після обробки дощок, їх торці нарізаються "ялинкою" і далі верстат при склеюванні з тиском притискає дошки один до одного. Цього достатньо, щоб склеїти дошку.
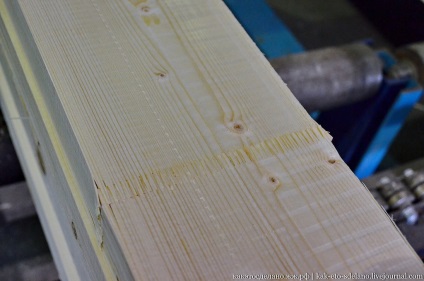
Ну а далі дошки склеюються в брус, обробляються, і на цьому верстаті нарізається профіль. І ще додам, що брус, склеєний з окремих дощок різного розміру міцніше, ніж з цілісних дощок, тому що дерево з часом дає усадку і в ньому підвищується напруга між іншими склеєними дошками, а короткі нарізані заготовки повністю мінімізують цей ефект. Поперечні балки при будівництві будинку теж роблять з такого бруса, в обов'язковому порядку.
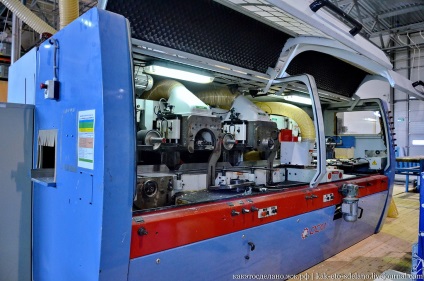
А ось і супербрус. До речі, клієнт, який замовляє брус для свого будинку, вибирає розмір перетину під свій смак. Тут же, компанія може допомогти йому визначитися з проектом, або створити власний проект за допомогою архітектора і інженерів компанії Good Wood.
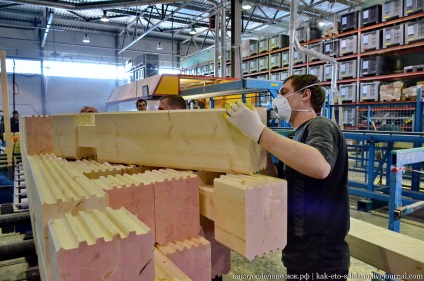
А це суперстанок Хундеггера, який в цей момент нарізає чашу в брусі.
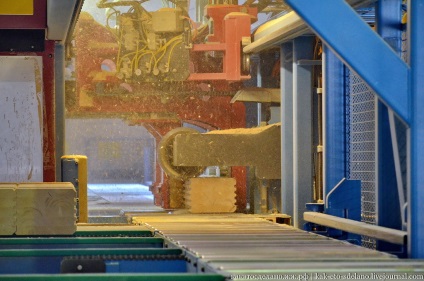
Помітив, що в цехах добре працює вентиляція і пил, яка неминуча на такому виробництві не висить довго в повітрі.
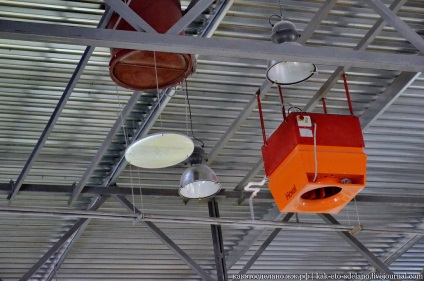
З пилом і дрібними тирсою також борються і зволожувачі повітря. Хороша річ, треба завести собі вдома.
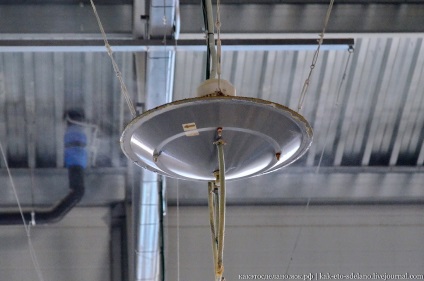
Хоча у виробництва бувають відходи у вигляді обрізків, можна сказати, що це практично безвідходне виробництво (в економічному плані), тому що деревина не придатна для виготовлення бруса продається як паливо для каміна, і використовується для власних потреб, також як паливо.

З тирси роблять ось такі брикети для розпалювання камінів.
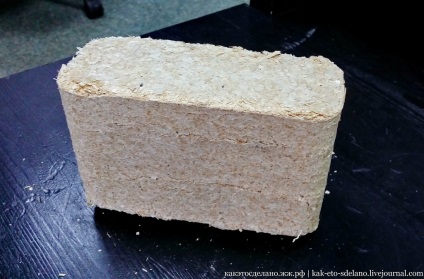
В кінці екскурсії мені знову зустрічаються готові пакети для сушильної печі.

У цю ємність збираються тирса виробництва.
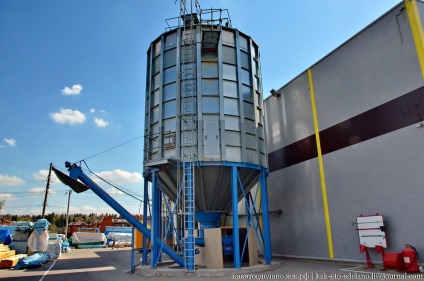
Наостанок зайдемо в невеличкий двоповерховий будиночок на території компанії, який може оглянути кожен бажаючий. Виглядає симпатично.
Мало не забув сказати, будинки для своїх клієнтів збирають тільки фахівці компанії, починаючи від закладки фундаменту, до покрівельних робіт і установки бойлера, і т.п. що дуже зручно.
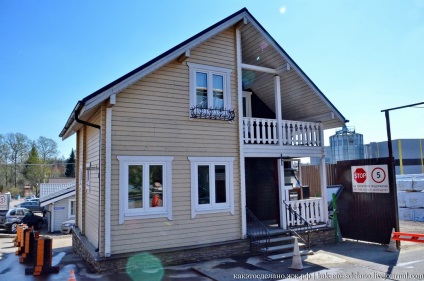
Тут є своя котельня, що важливо.

Будиночок зроблений з самого простого бруса. Звичайно ж, після складання будинку потрібно його пофарбувати, щоб зберегти його властивості. До речі, перевага бруса перед звичайним колодою в тому, що з часом брус дає усадку всього в 1-2% а колода - 15%! До того ж цільна колода неможливо піддати сушінню без деформації.
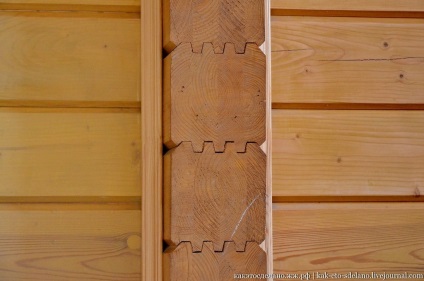
Дуже простора, світла кухня.
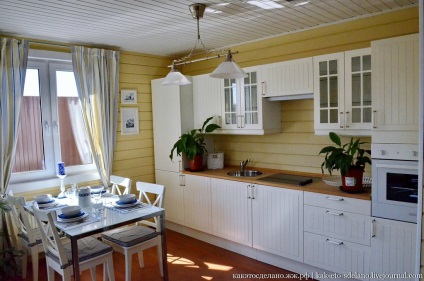
Плавно переходить у вітальню. В туалет і ванну заглядати не став, тому що в цей момент ними були зацікавлені потенційні покупці, що блукали по дому).
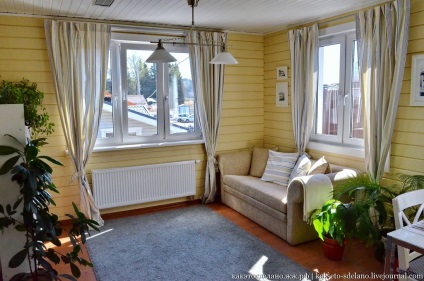
На першому поверсі немає житлових кімнат, тому що площа будиночка зовсім невелика. А на другому поверсі їх три. Перші дві - дитячі кімнати.
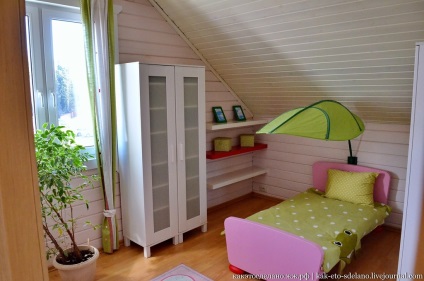
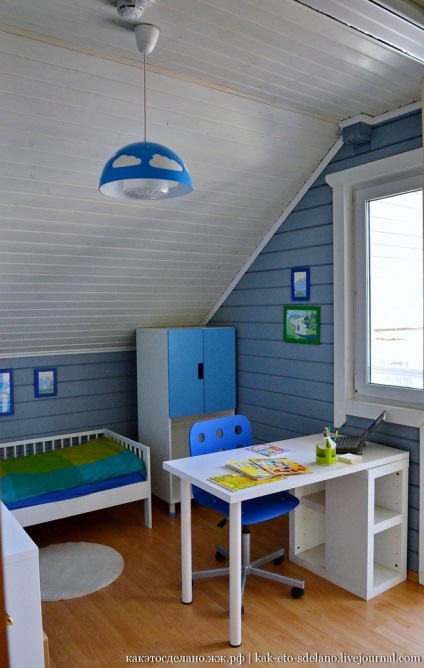
Третя кімната - спальня для батьків.
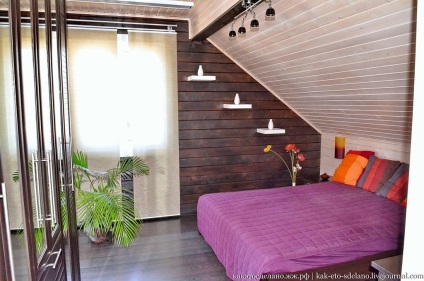
Тут же є балкончик. Будиночок гарний, але малуватий, буду доглядати собі інший проект.
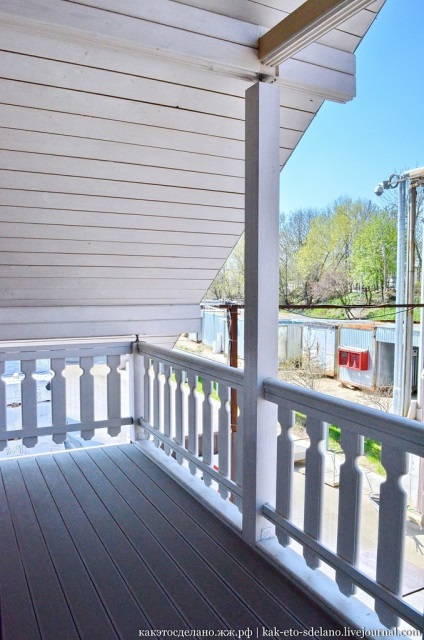
Тепер і ви знаєте, як робиться брус для будівництва будинку. Спасибі всім, хто дочитав до кінця.
А всім, хто зацікавився будівництвом власного будиночка раджу відвідати сайт компанії Good Wood. де дуже детально розповідається про різні проекти таких будинків, і можна підібрати під свій смак і ціну.