Ремонт трубних кульових млинів. Особливості їх ремонту.
Дивись питання 31.
Після очищення деталі піддають контролю і сортування (дефектовке).
Дефектовка -.определеніе технічного стану деталей; сортування їх на придатні, що вимагають ремонту і негідні, визначення маршруту для деталей, що вимагають ремонту.
До придатним відносяться деталі, у яких відхилення в розмірах і формі знаходяться в межах допустимого зносу, вказану в технічних умовах на ремонт машини.
Підлягають ремонту деталі, знос яких вище допустимого, або є інші відновлювані дефекти.
Непридатними деталями є ті, відновлення яких неможливе або економічно недоцільне внаслідок великого зносу і інших серйозних дефектів (деформації, злами, тріщини).
Причинами вибракування деталей в основному є різноманітні види зносів, які визначаються наступними факторами:
конструктивним - граничне зміна розмірів деталей обмежена їх міцністю і конструктивним зміною сполучення;
технологічним - граничне зміна розмірів деталей обмежується незадовільним виконанням нею службових функцій в роботі вузла або агрегату (так, знос шестерень насоса не забезпечує тиску або продуктивності нагнітання і ін.);
якісним - зміна геометричної форми деталей при зносі погіршує роботу механізму або машини (знос молотків, щік дробарок та ін.);
економічним - допустиме зменшення розмірів деталей обмежується зниженням продуктивності машини, збільшенням втрати переданої потужності на тертя в механізмах, збільшенням витрат мастила і іншими причинами, що впливає на собівартість виконуваної роботи.
Дефектовка деталей обладнання здійснюється відповідно до технічних умов, які включають: загальну характеристику деталі (матеріал, термічна обробка, твердість і основні розміри); можливі дефекти, допустимий без ремонту розмір; гранично допустимий розмір деталі для ремонту; ознаки остаточного шлюбу. Крім того, в технічних умовах наводяться вказівки про допускаються відхилення від геометричної форми (овальність, конусність).
Технічні умови на дефектовку оформляються у вигляді спеціальних карт, в яких крім перерахованих даних, вказуються способи відновлення і ремонту деталей.
Наведені в технічних умовах дані, що відносяться до допустимих і граничних значень зносів і розмірів, повинні грунтуватися на матеріалах по
вивчення зносів з урахуванням умов роботи деталей.
Деталі дефектуют і контролюють візуально і за допомогою вимірювального інструмента, а в окремих випадках із застосуванням пристосувань і вимірювальних приладів. Візуально перевіряють загальний технічний стан деталей і виявляють видимі зовнішні дефекти. Для кращого виявлення поверхневих дефектів, рекомендується попередньо ретельно очистити поверхню і потім протравить її 10-20% -ним розчином сірчаної кислоти. Крім того, при візуальному методі дефекти виявляють за допомогою остуківанія і обмацування деталей.
Контроль прихованих дефектів здійснюють гідравлічним, пневматичним, магнітним, люмінесцентним і ультразвуковим м про роками, а також рентгенівськими променями.
Гідравлічний і пневматичний методи дефектації застосовують для контролю деталей і вузлів на герметичність (водо- і газонепроникність) і виявлення тріщин в корпусних деталях, судинах. Для цього використовують спеціальні стенди, оснащені ємностями і насосними системами.
Магнітний метод дефектації деталей заснований на появі магнітного поля розсіювання при проходженні через дефектну деталь магнітного потоку. В результаті на їх поверхні під цими дефектами змінюється напрямок ліній магнітного поля (рис. 22) внаслідок неоднаковою магнітноїпроникності.
/ Спосіб контролю - для виявлення дефектів (тріщин і ін.) Поверхню деталі покривають феромагнітним порошком (прокаленная окис заліза-крокус) або суспензією, що складається з двох частин гасу, однієї частини трансформаторного масла і 35-45 г / л феромагнітного мелкодробленим порошку (окалини ). Для більш чіткого виявлення зміни магнітного поля на світлих деталях рекомендується використавши чорні магнітні порошки, на темних поверхнях - червоні. Цей вид контролю більш чутливий при виявленні внутрішніх дефектів деталі і застосовується при невідомих магнітних характеристиках матеріалу деталі.
2 спосіб контролю - виявлення поверхневих тріщин і дрібних і середніх деталях, виготовлених тільки з високовуглецевих і легованих сталей. Він продуктивніше і зручніше I способу. Для кращого виявлення дефектів застосовують різні види намагнічування деталей. Поперечні тріщини краще виявляються при
поздовжньому намагнічуванні, а поздовжні і розташовані під кутом - при циркулярному намагничивании.
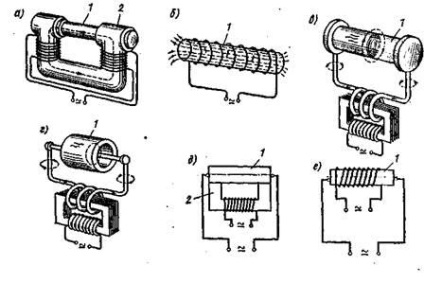
Мал. 23. Схеми способів намагнічування деталей:
Після магнітної дефектоскопії деталі необхідно промити в чистому трансформаторному маслі і розмагнітити. Схема приладу магнітної дефектоскопії показана на рис. 24. Прилад складається з приладу для намагнічування 2, магнітного пускача 3 і трансформатора 4.
Прилад для циркулярного намагнічування являє собою стійку, до якої нерухомо закріплений стіл з нижньої контактної мідної плитою і рухома головка з контактним диском, що переміщається по стійці. Деталь 1 щільно затискають між контактними номерами і плитою і включають трансформатор (або батарею акумулятора). Струм від вторинної обмотки трансформатора напругою 4-6 В підводиться до мідної плиті і контактному диску і при контакті з деталлю 1 відбувається намагнічування, яке триває 1-2 с. Потім деталь занурюють у ванну з суспензією на 1-2 хв, виймають і оглядають для визначення місць дефекту.
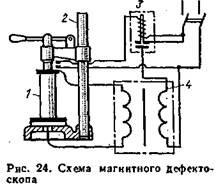
На ремонтних підприємствах найбільшого поширення набув універсальний магнітний
дефектоскоп типу М-217, який дозволяє проводити циркулярний, поздовжнє і місцеве намагнічування, магнітний контроль і розмагнічування.
Дефектоскоп складається з силового агрегату, за допомогою якого створюється магнітне поле, намагнічуються пристрої (контакти і соленоїд) і ванни для магнітної суспензії.
Промисловість випускає і інші магнітні дефектоскопи: стаціонарні - ПЕД-2 і 77ПМД-ЗІ, а також переносний 77МД-1Ш і напівпровідниковий ППД.
Переносні дефектоскопи дозволяють контролювати деталі безпосередньо на машинах, особливо великі деталі, які важко або неможливо зняти і досліджувати за допомогою стаціонарних установок.
Методом магнітної дефектоскопії можна контролювати лише сталеві і чавунні деталі, встановлюючи зовнішні і внутрішні дефекти розміром до 1-10 мкм.
Люмінесцентний метод контролю деталей заснований на здатності деяких речовин флюоресцировать (поглинати) променисту енергію і віддавати її у вигляді світлового випромінювання протягом деякого часу при порушенні речовини невидимими ультрафіолетовими променями.
Цим методом виявляють поверхневі дефекти типу волосяних тріщин на деталях з немагнітних матеріалів. На поверхню досліджуваної деталі наносять шар флюоресцирующей рідини, яка за JO-15 хв проникає в усі поверхневі дефекти. Після цього надлишок рідини видаляють з поверхні деталі. потім на
протерту поверхню наносять тонкий шар виявляє порошку, який витягує з тріщин і інших дефектів проникла туди флюоресцирующую рідина. Після опромінення поверхні деталі ультрафіолетовим світлом ті місця, з яких була витягнута флюоресцирующая рідина, починають світитися, вказуючи на локалізацію поверхневих дефектів.
Як флюоресцирующей рідини застосовують суміш з 85% гасу, 15% малов'язкого мінерального масла з добавкою 3 г на літр емульгатора ОП-7, а проявляють порошки складаються з окису магнію або селикогелем. Джерелами ультрафіолетового випромінювання служать ртутно-кварцові лампи типу ПРК-1, ПРК-4, 77ПЛУ-2 і СВДШ зі спеціальним світлофільтром УФС-3. застосовуються також
переносна установка Люм-1 і стаціонарний дефектоскоп ЛДА-3.
За допомогою люмінесцентного методу можна визначати поверхневі дефекти з розмірами 1-30 мкм.
Ультразвуковий метод контролю заснований на відображенні ультразвукових коливань від наявних внутрішніх дефектів деталі при про ходінні їх через метал внаслідок різкої зміни щільності середовища.
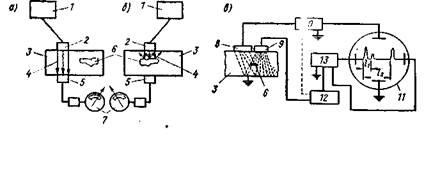
Мал. 25. Схеми дії ультразвукових дефектоскопів:
а -теневой метод (дефект не виявлений); б -теневой метод (дефект виявлений);
• - метод відображення
У ремонтному виробництві існують два способи ультразвукової дефектоскопії: звуковий тіні і відображення імпульсів (сигналів). При способі звуковий тіні (рис. 25, а, б) ультразвуковий генератор / впливає на п'єзоелектричну пластину 2, яка в
свою чергу діє на досліджувану деталь 3. Якщо по шляху ультразвукових хвиль 4 виявляється дефект 6, то вони відіб'ються і не потраплять на приймальню п'єзоелектричну пластинку 5, в результаті чого за дефектом з'явиться тінь, яку зазначає реєструючий прилад 7. '
При способі відображення (рис. 25, в) від генератора 12 через п'єзоелектричний випромінювач 9 ультразвукові хвилі передаються на деталь 3, проходячи її і відбившись від її протилежного кінця, повертаються до приймального щупу 8. При наявності дефекту 6 імпульси ультразвуку позначаться раніше. Потрапили на приймальний щуп
8 і перетворені в електричні сигнали імпульси подаються через підсилювач 10 в електронно-променеву трубку 11. За допомогою генератора розгортки 13, що включається одночасно з генераторів 12, сигнали отримують горизонтальну розгортку променя на екрані трубки 11, де виникає початковий імпульс у вигляді вертикального піку. Відбиваючись від дефекту, хвилі більш швидко повертаються, і на екрані з'являється другий імпульс, віддалений від першого на відстані / j. Третій імпульс відповідає сигналу, відбитому від протилежного боку деталі. Відстань / 2 відповідає товщині деталі, а відстань / t - глибині залягання дефекту. Вимірюючи час від моменту посилки імпульсу до моменту прийому луна-сигналу, можна визначити відстань до внутрішнього дефекту.
Для ремонтних цілей використовується вдосконалений ультразвуковий дефектоскоп УЗД-7Н, виконаний по імпульсної схемою і дозволяє вести контроль виробів за способом відбитих сигналів, а також за способом наскрізного просвічування (звуковий тіні).
Максимальна глибина просвічування для стали становить 2,6 м при плоских і 1,3 м при призматичних щупах, мінімальна глибина 7 мм. Крім того, наша промисловість випускає ультразвукові дефектоскопи ДУК.-5В, ДУК-6В, УЗД-ЮМ і ін. З високою чутливістю, які можна застосовувати в ремонтному виробництві.
Контроль рентгенівськими променями заснований на властивостях електромагнітних хвиль по-різному поглинатися повітрям і твердими тілами (металами). Промені, що проходять через матеріали, незначно втрачають свою інтенсивність, якщо на їх шляху зустрічаються порожнечі в контрольованій деталі у вигляді тріщин, раковин і пір.
Спроектовані на екран вихідні промені покажуть затемнені або більш яскраво освітлені місця, що відрізняються від загального фону.
Ці плями і смуги різної яскравості вказують на дефекти в матеріалі. Крім рентгенівських променів, в дефектоскопії застосовують промені радіоактивних елементів-гамма-промені (кобальт-60, цезіі-137 і ін.). Даний спосіб складний і тому на ремонтних підприємствах застосовується рідко (при контролі швів у корпуса обертових печей і млинів і т. П.).
Дефектовка деталей фарбою широко використовується в ремонтній практиці при ремонті устаткування на місці установки його або в стаціонарних умовах при контролі великих деталей типу рам, станин, картерів та ін.
Суть методу полягає в тому, що знежирену бензином досліджувану поверхню деталі забарвлюють спеціальної яскраво-червоною .Рідина, що володіє хорошою смачиваемостью і проникаючою в дрібні дефекти (протягом 10-15 хв). Потім її змивають з деталі і останню фарбують білою нітроемаллю, яка вбирає в себе проникла в дефекти деталі фарбувальну рідину. Рідина, виступаючи на білому тлі деталі, вказує на форму і величину дефектів. На цьому принципі засновано визначення дефектів за допомогою гасу і млявий обмазки.
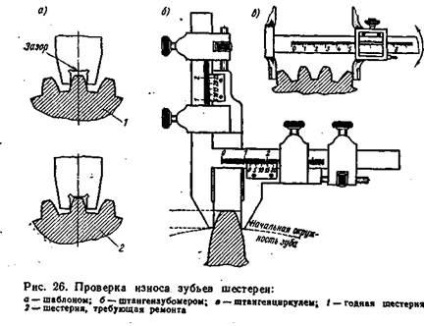
Вали. Найбільш часто зустрічаються дефекти валів - погнутість, знос опорних поверхонь, шпонкових канавок, різьблень, шліців, резьб, шийок і тріщини.
Погнутість валів перевіряють в центрах токарного або спеціального верстата на биття, користуючись для цієї мети індикатором, укріпленим на спеціальній стійці.
Овальність і конусність шийок колінчастого впала визначають виміром мікрометра в двох перетинах, віддалених від галтелів на відстані 10-15 мм. У кожному поясі вимір виробляють в двох площинах. Граничні розміри посадочних місць, шліців, шпонкових канавок оцінюються за допомогою граничних скоб, шаблонів і іншого вимірювального інструмента.
Тріщини валів виявляють зовнішнім оглядом, магнітними дефектоскопами і іншими методами. Вали і осі бракують, якщо виявлені тріщини глибиною понад 10% діаметра вала. Зменшення діаметра шийок вала при проточці (шліфовці) в разі ударного навантаження допускається не більше ніж на 5%, а при спокійній навантаженні-ні
більше 10%.
Зубчасті колеса. Про придатність зубчастих коліс до роботи судять в основному по зносу зуба по товщині (рис. 26). Зуби заміряють по товщині штангензубоміри, тангеціальнимі і оптичними Зубоміри, шаблонами. Товщину зуба циліндричних зубчастих коліс
вимірюють в двох перетинах. У кожного зубчастого колеса вимірюють три зуба, розташованих один щодо іншого під кутом 120 °. Перед початком виміру найбільш зношені зуби відзначають крейдою. Граничний знос зуба по товщині (вважаючи по початковій окружності) не повинен перевищувати: для відкритих передач (III-IVклассов) Підшипники кочення. Для контролю підшипників кочення застосовують пристосування різних типів, на яких визначають радіальні і осьові люфти в підшипниках. Радіальний а)
люфт перевіряють з використанням пристосування, представленого на рис. 27. Перевіряється підшипник внутрішнім кільцем встановлюють на оправлення і затискають гайкою. Зверху одним кінцем стрижень 4 впирається в поверхню зовнішнього кільця підшипника, а іншим - в ніжку контрольного миниметро 5. Знизу одним кінцем стрижень 2 впирається в поверхню зовнішнього кільця підшипника, а іншим кінцем пов'язаний з системою важелів. Стрижень 4 проходить в трубці 3, а стрижень 2 - в голівці. Трубка 3 і стрижень 2 за допомогою важелів з'єднані з лінійкою 1, по якій пересувається вантаж Р. Якщо вантаж Р знаходиться з правого боку, трубка 3 тисне на зовнішнє кільце підшипника зверху - кільце переміститься вниз, внаслідок чого стрижень 4 теж переміститься вниз і на миниметро 5 фіксують показання стрілки. Якщо вантаж Р переміститься на ліву сторону, то на зовнішнє кільце підшипника тисне стрижень 2 - кільце переміститься вгору. Стрижень 4 також переміститься вгору, при цьому знову фіксують показання миниметро. Різниця між показаннями стрілки миниметро і буде радіальним зазором в перевіряється підшипнику.