Механізм швидкостеміра можна розділити на три основних вузла: вимірювач швидкості, годинниковий механізм і реєстратор тиску, які кінематично між собою не пов'язані. Приводний вал швидкостеміра отримує обертальний рух від колеса локомотива через встановлений на ньому редукційний привід. На приводному валу встановлено реверсивний пристрій забезпечує одностороннє обертання основної осі швидкостеміра. Реверсивний пристрій через відповідну передачу пов'язано з сегментним пристроєм і механізмом подзавода. Сегментне пристрій забезпечує вимір пройденого шляху, а годинниковий механізм вимір часу. Спарена робота сегментного пристрою і годинникового механізму забезпечують вимірювання швидкості руху поїзда. На осі покажчика швидкості встановлена стрілка, яка на циферблаті швидкостеміра показує дійсну швидкість руху локомотива. На приводному валу встановлений реєстратор напрямку руху, який забезпечує запис на стрічці швидкостеміра зворотного ходу локомотива.
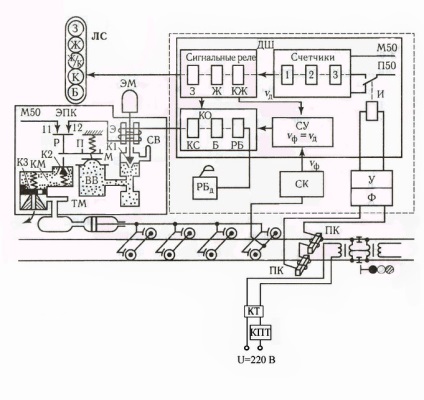
Малюнок 7 -Структурная схема пристрою АЛС
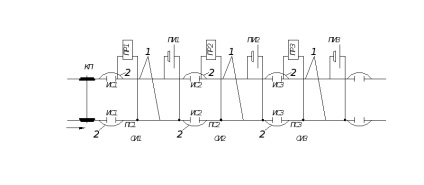
Малюнок 8 - Принципова схема РЦ АБ перегону з тризначною сигналізацією
Комплексна уніфікована система регулювання і забезпечення безпеки руху поїздів за рахунок повноти виконання основних функцій технічних засобів забезпечення безпеки руху поїздів дозволить виключити основні причини сходів рухомого складу і зіткнень рухомого складу.
При впровадженні комплексної уніфікованої системи регулювання і забезпечення безпеки руху поїздів істотно знизиться збиток від втрати вантажів, пошкоджень колії та рухомого складу за рахунок зменшення випадків перевищення швидкості, що не спостереження за сигналами, самовільного виходу поїзда і втрати пильності машиніста.
Удосконалення управління перевезеннями на залізницях шляхом впровадження КЛУБ-У дозволить:
Підвищити рівень і ефективність експлуатаційної роботи на ділянках і експлуатаційних показників за рахунок:
підвищення дільничної швидкості і за рахунок зниження втрат поездочасов;
отримання додаткової інформації про місцезнаходження поїзда і їх швидкості;
додаткової інформації, переданої машиністу (про вільність блок ділянок на попереду лежить шляху і ін.);
передачі інформації про обмеження швидкостей руху;
контролю справності технічних засобів локомотива;
контролю ефективності гальм
Підвищити безпеку руху поїздів.
Перешкоджання рух локомотивів.
Забезпечити реєстрацію інформації про параметри руху поїзда і справності технічних засобів.
Економія експлуатаційних витрат при впровадженні КЛУБ-У забезпечується за рахунок:
Підвищення ефективності експлуатаційної роботи на ділянках залізниць внаслідок зниження інтенсивності відмов бортової апаратури, підвищення дільничних швидкостей і зниження втрат поездочасов.
Скорочення локомотивного парку завдяки використанню локомотивів на будь-яких ділянках з (АЛС, АЛС-ЄП і ін.).
Скорочення збитків внаслідок підвищення безпеки руху поїздів.
Додаткового ефекту від поліпшення експлуатаційних показників ділянок при впровадженні КЛУБ-У.
Ефективність впровадження КЛУБ-У дає також додатковий ефект, який забезпечується за рахунок:
- скорочення апаратних засобів додаткових систем безпеки (виключення індикатора системи САУТ, скорочення від двох до чотирьох датчиків швидкості);
на 50% кількості подорожніх датчиків САУТ, розташованих при вході зі станції за рахунок визначення місця розташування координати) локомотива або МВРС супутниковою навігаційною системою і передачі інформації по цифровому радіоканалу;
на 70% польового обладнання на перегонах (релейних шаф, світлофорів, апаратури електропостачання, дросель-трансформаторів).
скорочення витрат по монтажу систем безпеки (ліквідації витрат на установку ККД, спрощення кабельної мережі).
Економія визначається тим, що колійна апаратура централізованої автоблокування, зосереджена на станціях, і локомотивна апаратури КЛУБ-У з використанням дублюючих каналів зв'язку і супутникової навігаційної системи, дозволяє забезпечити режим АЛСО
12 Колісна пара під час роботи жорстко приймає всі удари від нерівностей шляху як у вертикальному, так і в горизонтальному напрямках, і в свою чергу сама жорстко впливає на шлях. Крім того, деталі колісної пари сприймають крутний момент від валу ТЕД при реалізації тягового зусилля.
Колісна пара складається з осі, колісних центрів, бандажів, зубчатих коліс і бандажних кілець.
13 Збірка Автозчіпні пристрої
● При установці автозчіпного пристрою необхідно, щоб у вагонів і локомотивів з поглинаючими апаратами Ш-1-ТМ, Ш-1-Т і розеткою, яка виступає від кінцевої балки на 185 мм, відстань від упора голови корпусу автозчеплення до межі розетки було не менше 70 мм при повністю втопленою положенні автозчеплення і не більше 90 мм при висунутому положенні.
Для апарату Ш-2-Т, що встановлюється на рухомий склад з розеткою, яка виступає на 95 мм, ці відстані мають бути відповідно не менше 110 і не більше 130 мм.
Поглинаючі апарати Ш-2-В, Ш-6-ТО-4, ПМК-110А, ПМК-110К-23 і 73ZW встановлюються на рухомий склад, що має розетку, яка виступає від кінцевої балки на 130 мм. Для цих апаратів відстань від упора голови автозчеплення до межі розетки повинно бути не менше 120 мм при втопленому положенні автозчеплення і не більше 140 мм при висунутому. Такі ж вимоги повинні бути виконані при установці на вказаний рухомий склад апаратів Ш-1-ТМ (Ш-1-Т).
Відстань від упору голови автозчеплення до розетки при установці поглинаючих апаратів на пасажирський рухомий склад має бути для апаратів Р-2П і ЦНДІ-Н6 не менше 70 мм при втопленому і не більше 90 мм при висунутому положеннях автозчеплення, а для апарату Р-5П - відповідно не менше 80 мм і не більше 100 мм. Зазначені в цьому підпункті відстані перевіряють, коли апарат щільно прилягає дном корпусу до задніх упорів, а через наполегливу плиту - до передніх упорів.
● Висоту автозчеплення над головками рейок а горизонтальному і прямій ділянці шляху вимірюють - допомогою рейки. Ця висота повинна відповідати даним, зазначеним у табл. 2.2.
Підстава рейки кладуть на обидві головки рейок, а стійку з поділами прикладають до ливарному шву, що проходить уздовж хвостовика корпусу автозчеплення. Якщо шов погано помітний, через середину хвостовика проводять подовжнюлінію. Висоту вимірюють в місці виходу хвостовика автозчеплення з ударної розетки по передній площині центрирующей балочки (рис. 2.62, точка а).
● Різниця між висотами осей автозчеплень по обох кінцях вагона, тепловоза або електровоза (однієї секції), вагона електро- або дизель-поїзда при випуску з капітального ремонту повинна бути не більше 15 мм, а при випуску з інших видів ремонту - понад 20 мм ( для вантажного вагона - не більше 25 мм).
● Положення автозчеплення щодо горизонталі визначають по різниці між значеннями її висоти від головок рейок до ливарного шва, яка вимірюється в двох місцях: по лінії зачеплення і біля входу хвостовика в ударну розетку (див. Рис. 2.62, точки а і б). Відхилення автозчеплення вниз (провисання) допускається у вагонів і локомотивів не більше ніж на 10 мм, відхилення вгору - не більше ніж на 3 мм.
Висота осі автозчеплення над головками рейок, мм, при випуску з ремонту
вагонів з деповського; тепловозів, електровозів і вагонів електро- і дизель-поїздів з поточних ТР-2, ТР-3; паровозів з підйомного
Вантажні вагони Пасажирські вагони на візках: КВЗ-5, КВЗ-ЦНИИ інших типів Рефрижераторні вагони Електровози Тепловози, паровози, тендери, дизель-поїзди серій Д1, ДР1 Вагони електропоїздів серій Сд, Ср, СПЗ Вагони електропоїздів решти серій: проміжні головні
1080-1020 1080-1030 1080-1020 1080-1030 1080-1000 1080-1020 1167-1097 1160-1090 1070-1000 *
1080-1000 1080-1020 1080-1010 1080-1020 1080- 990 1080-1010 1167-1090 1160-1080 1070-990 *
Примітка. У паровозів і тендерів з повним запасом води і палива при випуску з ремонту висота автозчеплення допускається не менше 990 мм.
Значення вказані для автозчеплень, розташованих з боку кабін.
У вагонів моторвагонного рухомого складу провисання допускається не більше ніж на 3 мм, а відхилення вгору - не більше ніж на 5 мм.
● При центрир приладі з маятниковому підвішуванням зазор між верхньою площиною хвостовика і стелею ударної розетки на відстані 15-20 мм від зовнішньої її кромки повинен бути не менше 25 мм і не більше 40 мм, а між цією ж площиною хвостовика і верхньою кромкою вікна в кінцевий балці - не менше 20 мм.
При центрир приладі з подпружиненной опорою для хвостовика автозчеплення вказаний зазор не контролюється.
● Автосцепка повинна вільно переміщатися з середнього положення в крайнє від зусилля, прикладеного людиною, і повертатися назад під дією власної ваги. Перевірку цієї вимоги виконують, коли апарат щільно прилягає дном корпусу до задніх упорів і через наполегливу плиту до передніх упорів.
● Довжина ланцюга Розчіпна приводу повинна бути відрегульована. Рукоятка Розчіпна важеля повинна укладатися на поличку фіксуючого кронштейна так, щоб нижня частина замку не виступала назовні від вертикальної стінки горла.
Перед регулюванням довжини ланцюга попередньо перевіряють довжину короткого плеча важеля від осі стержня до центру отвору, яка повинна складати 190 (+10) мм.
● Що поглинає апарат повинен прилягати до задніх упорів і через наполегливу плиту до передніх упорів. Ослаблені заклепки упорів і ударної розетки повинні бути переклепани, болтові з'єднання закріплені.
● Обмежувальну планку або скобу на хребтової балці (або інше обмежувальне пристрій), що охороняє тяговий хомут від підняття і автозчеплення від провисання, необхідно замінити, якщо вона погнута або в ній є тріщини.
● Вимоги, зазначені в цій главі, відносяться до огляду, перевірки і ремонту автозчіпного пристрою при поточного ремонту вагонів, єдиної технічної ревізії пасажирських вагонів (ТО-3), промивально ремонті паровозів, поточний ремонт ТР-1 тепловозів, електровозів і вагонів дизель- і електропоїздів.
● Під час зовнішнього огляду необхідно перевірити:
а) дію механізму автозчеплення;
б) знос тягових і ударних поверхонь великого і малого зубів, ширину зіва корпусу, стан робочих поверхонь замку;
в) стан корпусу автозчеплення, тягового хомута, клина тягового хомута і інших деталей автозчіпного пристрою (наявність в них тріщин і вигинів);
г) стан Розчіпна приводу і кріплення валика підйомника автозчеплення;
д) кріплення клина тягового хомута;
е) прилягання поглинає апарату до наполегливої плиті і заднім наполегливою кутника (упору);
ж) зазор між хвостовиком автозчеплення і стелею ударної розетки;
з) зазор між хвостовиком автозчеплення і верхньою кромкою вікна в кінцевій балці;
і) висоту поздовжньої осі автозчеплення пасажирських вагонів від головок рейок;
к) положення поздовжньої осі автозчеплення щодо горизонталі;
л) стан валика, болтів, пружин і кріплення паровозної розетки.
У разі виявлення несправності дії механізму автозчеплення, а також при єдиної технічної ревізії пасажирських вагонів механізм автозчеплення розбирають, кишені корпусу оглядають, при необхідності очищають, несправні деталі замінюють справними і після складання перевіряють дію механізму в установленому порядку.
● Чи не дозволяється випускати рухомий склад в експлуатацію при наявності хоча б однієї з таких несправностей:
а) автозчеплення не відповідає вимогам перевірки комбінованим шаблоном 940р;
б) деталі автозчіпного пристрою з тріщинами;
в) різниця між висотами автосцепок по обох кінцях вагона понад 25 мм, провисання автозчеплення рухомого складу більше 10 мм; висота осі автозчеплення пасажирських вагонів від головок рейок більш 1080 мм і менше 1010 мм у вагонів на візках КВЗ-5, КВЗ-ЦНИИ і менше 1000 мм на візках інших типів;
г) ланцюг Розчіпна приводу довжиною більш-менш допустимої; ланцюг з незаварених ланками або надривами в них;
д) зазор між хвостовиком автозчеплення і стелею ударної розетки менше 25 мм; зазор між хвостовиком і верхньою кромкою вікна в кінцевій балці менше 20 мм (при жорсткій опорі хвостовика);
е) замок автозчеплення, віддалений від зовнішньої вертикальної кромки малого зуба більш ніж на 8 мм або менше ніж на 1 мм; лапа Замкодержаки, що відстоїть від кромки замку менш ніж на 16 мм (у Замкодержаки, які не мають скоса, - менш ніж на 5 мм);
ж) валик підйомника заїдає при обертанні або закріплений нетиповим способом;
з) товщина перемички хвостовика автозчеплення, яка встановлюється замість несправної на вагон, що випускається з поточного ремонту, менше 48 мм;
і) поглинає апарат не прилягає щільно через наполегливу плиту до передніх упорів, а також до задніх упорів (для апарату 73 ZW допускається наявність сумарного зазору між переднім упором і наполегливої плитою або корпусом апарату і заднім упором до 5 мм);
к) наполегливі косинці, передні і задні упори з ослабленими заклепками;
л) планка, підтримуюча тяговий хомут, товщиною менше 14 мм, або укріплена болтами діаметром менше 22 мм, або без контргаек і шплінтів на болтах (допускається кріплення підтримуючої планки болтами діаметром 20 мм, але в кількості 10 шт.);
м) нетипове кріплення клина (валика) тягового хомута;
н) неправильно поставлені митників підвіски центрує приладу (широкими головками вниз);
о) обмежувальний кронштейн автозчеплення з тріщиною в будь-якому місці, зносом горизонтальної полиці або вигином більше 5 мм;
п) відсутність запобіжного гака у паровозної автозчеплення; валик розетки, закріплений нетиповим способом; ослаблені болти розетки; болти без шплінтів або зі шплинтами, що не проходить через прорізи корончастих гайок.
● Порядок перевірки автозчеплення комбінованим шаблоном 940р:
а) перевірка справності дії запобіжника замку. Прикладають шаблон і одночасно натискають рукою на замок, пробуючи заштовхнути його в кишеню корпусу автозчеплення. Догляд замку повністю в кишеню корпусу вказує на неправильне дію запобіжника замку. Якщо запобіжник діє правильно (верхнє його плече впирається в противагу Замкодержаки при натисканні на лапу ребром комбінованого шаблона), то замок повинен йти від кромки малого зуба автозчеплення не менше ніж на 7 мм і не більше ніж на 18 мм (вимірюють у верхній частині замку) ;
б) перевірка дії механізму на утримання замку в розчеплення положенні. Шаблон прикладають. Потім поворотом до відмови валика підйомника відводять замок всередину порожнини кишені і звільняють валик, продовжуючи утримувати шаблон в зіві автозчеплення. Якщо замок опускається назад вниз, значить механізм несправний;
в) виявлення можливості передчасного включення запобіжника замку при зчепленні автосцепок. Шаблон встановлюють так, щоб його відкидна скоба стороною з вирізом 35 мм натискала на лапу Замкодержаки, а лист шаблону стосувався великого зуба. Автосцепка вважається придатної, якщо при натисканні на замок він безперешкодно йде в кишеню на весь свій хід;
г) перевірка товщини замикає частини замку. Прикладають шаблон. Якщо шаблон одночасно прилягає до бічних сторонах малого зуба і замку, значить замок непридатний (тонкий);
д) перевірка ширини зіву автозчеплення (без замка). Шаблон прикладають одним кінцем до кута малого зуба, а іншим підводять до носку великого зуба. Якщо шаблон проходить повз носка великого зуба в зів, то корпус автозчеплення непридатний. Перевірка проводиться по всій висоті носка великого зуба;
е) перевірка зносу малого зуба. Шаблон прикладають, як показано. Якщо шаблон стикається з бічною стінкою малого зуба, то автозчеплення непридатна. Перевірку виконують на відстані 80 мм вгору і вниз від поздовжньої осі корпусу;
ж) перевірка зносу тягової поверхні великого зуба і ударної поверхні зіва. Шаблон встановлюють. Якщо шаблон входить в зів, то автозчеплення непридатна. Перевірку виконують у середній частині великого зуба по висоті на 80 мм вгору і вниз від середини (перевірка великого зуба проти вікна для лапи Замкодержаки не проводиться).
● При єдиної технічної ревізії пасажирських вагонів (1 раз в 6 місяців) проводиться перевірка піднесення противаги Замкодержаки над поличкою. Для цієї мети на лапу Замкодержаки, навішеній на шип корпусу, натискають шаблоном 940р, після чого планку 7 з вирізом 11 мм встановлюють на противагу Замкодержаки. Піднесення противаги над поличкою вважається достатнім, якщо між планкою 7 і поличкою 2 є зазор, 3 при цьому тягові і ударні поверхні контуру зачеплення корпусу автозчеплення повинні задовольняти вимогам перевірки шаблоном 893р.
● Після усунення виявлених несправностей зібрана автозчеплення повинна бути перевірена шаблоном 940р.
● Автозчіпне пристрій електропоїздів слід перевіряти відповідно до зазначених в цьому розділі вимог один раз між поточними ремонтами ТР-1.
14 Для ремонту колісних пар застосовується потоковий метод контролю: