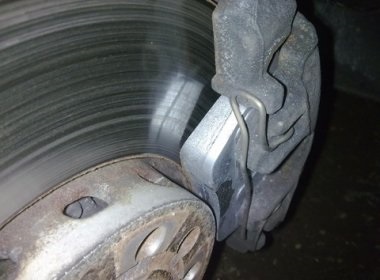
При експлуатації автомобіля ці деталі притираються один до одного в процесі гальмування з утворенням ідеально прилягає поверхні. У тому випадку, коли диски і гальмівні колодки нові, їх поверхні оброблені в заводських умовах з необхідною шорсткістю, тому при установці їх притирання, як правило, відбувається природним чином, коли проводиться гальмування автомобіля. Але коли автомобіль має деякий пробіг, а колодки, встановлені одночасно з дисками, зносилися, потрібна установка нових гальмівних колодок. При цьому бічні поверхні гальмівних дисків напевно мають підвищену шорсткість по площі тертя з колодками. На дисках з'являються так звані ризики по всьому діаметру диска.
Ризики - це не що інше, як западини і виступи металу, утворені шляхом нерівномірного зносу, в результаті тертя поверхонь. Нерівномірність зносу відбувається через різницю структури за хімічним складом, як гальмівних колодок, так і дисків. Але в основному ризики з'являються через попадання між поверхнями, що труться сторонніх включень. Найчастіше це пісок, вода, пил та інші чужорідні включення. Глибина западин і висота виступів може бути незначною, зазвичай, якщо пробіг автомобіля не великий, а колодки при цьому змінюються вперше. Але якщо пробіг автомобіля вже значний і гальмівні колодки вже змінюються третій, а то і четвертий раз, в цьому випадку шорсткість поверхні диска дуже висока, тому потрібно притирання нових колодок до цих дисків за певною методикою і технології.
Наукові методи відновлення деталей
Звичайно, добре б було, якби при заміні колодок на нові змінювалися б і диски. Але це досить накладно і фінансово відчутно. Деякі автовиробники рекомендують при заміні колодок на нові виробляти ще й проточку бічних поверхонь дисків, з подальшою їх шліфуванням і поліруванням. Але не у багатьох автовласників є така можливість, в силу певних причин. Будь то фінансові або технологічні причини, коли в автосервісах немає спеціального обладнання для проточки, шліфовки і подальшій поліровці дисків.
Наслідки встановлення не притертих колодок
Зустрічаються випадки, коли при зносі гальмівних колодок нові не вставляються між супортом і диском. І причиною цього буває не гальмівний робочий циліндр супорта, шток якого не відійшов в початковий стан, а товщина самої колодки, що перевищує необхідну. Деякі автовласники в даному випадку сточують гальмівну колодку на жорні, що абсолютно неприпустимо, так як напевно при установці колодки площині поверхонь колодки і диски не будуть паралельні один щодо одного. В цьому випадку при русі автомобіля з подальшим гальмуванням виникне сильне биття колеса, а ефективність гальмування буде вкрай низькою і можливо з провалами. Більш того, гальмівний циліндр супорта може піти на перекіс і заклинити, а гальмівний диск отримає деформацію. Бувають випадки, коли колодки не прітерти або оброблені на жорні, доводиться різко загальмувати на значній швидкості руху автомобіля по мокрій дорозі. При таких обставинах взагалі може утворитися мікротріщина на диску, з наступним повним його руйнуванням. Тріщини на дисках зазвичай виникають при різких перепадах температури у вологому середовищі, коли проводиться екстрене гальмування, при цьому диск сильно нагрівається і на нього потрапляє волога. При цьому псується не тільки диск, але і гальмівні колодки.
Технологія притирання гальмівних колодок до дисків має свої специфічні нюанси, і повинна проводитися за такою методикою:
- Після заміни гальмівних колодок на нові, в перші 200-250 кілометрів пробігу не слід різко натискати на педаль гальма. Гальмування по більшою мірою необхідно здійснювати двигуном, лише не сильно і недовго натискаючи на педаль гальма. Не допускати нагрівання колодок. В даний початковий момент відбувається лише сточування поверхні колодок поверхнею диска під певний малюнок шорсткості. В результаті, на колодках повинен сформуватися так званий первинний дзеркальний слід від контактіруемие поверхні диска. Якщо знехтувати цим пунктом, то напевно швидкому, навіть стихійному стирання піддадуться як мінімум дві-три колодки, і через невеликий проміжок часу їх знову доведеться міняти, а ефективність гальмування буде вкрай низькою і не рівномірною.
- Другий етап по тривалості також повинен бути близько 200 кілометрів пробігу. У цей період гальмування автомобіля повинно проводитися більш впевнено, але також не докладаючи особливих зусиль. У цей період притирання відбувається остаточне формування поверхні феррадо (фрикційний матеріал колодки), який можна порівняти з поверхнею дисків. Відбувається повне зіткнення поверхонь. Слід врахувати, що в цей період не бажана експлуатація автомобіля в дощову погоду або по грунтових грязьовим або курних дорогах. Поїздки повинні проводиться по асфальтовому або бетонному сухому покриттю.
- Остаточна приробітку. У цей період, по закінченні 300-400 кілометрів пробігу, необхідно пробувати максимально тривалий гальмування із зусиллям. Час натискання на педаль повинна становити 5-7 секунд. Потім слід дати охолонути як диску, так і колодок. У цей період відбувається хімічне перетворення поверхні колодок внаслідок нагрівання і тиску. На поверхні феррадо утворюється тонка і міцна еластична структура, що володіє потужними фрикційними властивостями і стійкістю до зносу.