Ремонт механізмів управління зводиться до ремонту рульового механізму і гальмівної системи.
Ремонт рульового управління. Для встановлення ступеня зносу і характеру ремонту деталей рульовий механізм необхідно розібрати. При цьому для зняття рульового колеса і сошки керма застосовують знімачі. Основними дефектами деталей рульового механізму є знос черв'яка і ролика вала сошки, втулок, підшипників і місць їх посадки, обломи і тріщини на фланці кріплення картера, знос отвору в картері під втулку вала рульової сошки і деталей кульових з'єднань рульових тяг, погнутість рульових тяг.
Черв'як рульового механізму замінюють при значному зносі робочої поверхні або відшаруванні загартованого шару. Ролик вала сошки бракують при наявності на його поверхні тріщин і вм'ятин. Черв'як і ролик замінюють одночасно.
Розбирання і складання рульового механізму необхідно проводити тільки на стенді, попередньо знявши його з автомобіля, а регулювання можна виконувати як на стенді при складанні, так і на автомобілі при поточному ремонті. Зазор в підшипниках черв'яка рульового вала у автомобілів ВАЗ і ГАЗ-3102 регулюють підбором регулювальних прокладок, у автомобіля «Москвич-2140» регулювальної гайкою, яка спочатку затягується до відмови, потім відпускається до вільного обертання рульового вала без появи осьового люфту і затягується стопорною гайкою. Момент провертання підшипників черв'яка повинен складати для автомобілів ВАЗ і «Москвич» 20. 50 Н * м, для автомобіля ГАЗ-3102 - 40. 80 Н * м.
Бічний зазор в зачепленні черв'яка з роликом регулюють за допомогою регулювального гвинта (або втулки), пов'язаного з валом сошки. Беззазорний зачеплення черв'яка з роликом має бути в межах повороту черв'яка на кут не менше 30. 60 ° вліво і вправо від положення, відповідного прямолінійного руху. В правильно відрегульована рульовому механізмі зусилля на ободі для повороту рульового колеса в середньому положенні має становити 8. 12 Н.
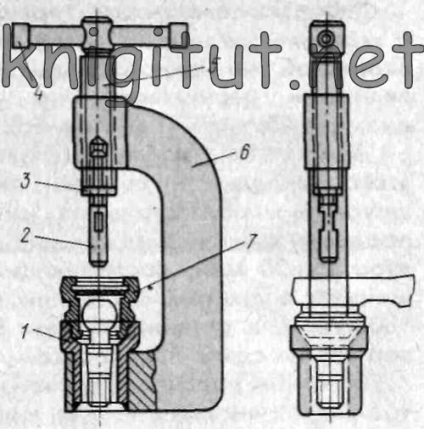
Мал. 157. Пристосування для збирання шарнірів рульових тяг:
1 - втулка з прорізом, 2 - стрижень, 3 - контргайка, 4 - комірець, 5 - гвинт, 6 - корпус, 7 - шарнір рульової тяги
Шарніри рульового приводу автомобілів ВАЗ ремонту не підлягають, а шарніри автомобілів «Москвич» і ГАЗ-3102 підлягають розбиранню і подальшій збірці з заміною зношених сферичних поверхонь пальців і сухарів, із застосуванням спеціального пристосування (рис. 157).
Ремонт гальмівної системи. Гальмівні системи можуть мати такі основні несправності: знос гальмівних накладок, барабанів і дисків, зрив гальмівних накладок, втрату герметичності гідравлічної гальмівної системи, відмови в роботі вакуумного підсилювача.
Робочу поверхню гальмівних барабанів і дисків з дрібними задираками і подряпинами зачищають дрібнозернистою наждачним шкіркою. Барабани з глибокими задираками растачивают, але збільшення розміру по діаметру повинно бути не більше 1 мм.
Замінні гальмівні накладки приклеюють. Для цього накладки і колодки зачищають дрібнозернистою шкіркою і знежирюють, склеюють клеєм ВС-10Т з попередньою витримкою при кімнатній температурі 15. 20 хв, подальшим з'єднанням і розміщенням в стислому стані в сушильній шафі при 180. 220 ° С протягом 45 хв. Якість склеювання перевіряють на зрушення під пресом.
Якщо несправності реєструються загорянням контрольної лампочки (коли зовнішнім оглядом не вдалося виявити підтікання гальмової рідини), то для визначення несправності на автомобілях «Москвич-2140» і ГАЗ-3102 з непрацюючими двигунами треба натиснути на гальмівну педаль і, коли контрольна лампочка зажевріє, утримуючи педаль в цьому положенні, відвернути клапан випуску повітря з великих циліндрів. Якщо педаль гальма отримує додатковий хід при цьому ж зусиллі, значить, несправність в гідравлічній ланцюга малих циліндрів і задніх гальм. Найбільш ймовірна несправність в даному випадку - незадовільний стан манжети другої камери (рис. 158) або поверхні дзеркала головного циліндра в робочій зоні цієї манжети, або пошкодження посадкового місця манжети на поршні.
При відсутності додаткового ходу педалі слід відкрити клапан випуску повітря з малих циліндрів. Якщо педаль в цьому випадку отримала додатковий хід, то пошкоджені манжети (положення в або г). У разі незадовільної роботи манжети (положення г) гальмівна рідина буде перекачуватися всередині бачка з порожнини, розташованої поруч з підсилювачем, в іншу порожнину.
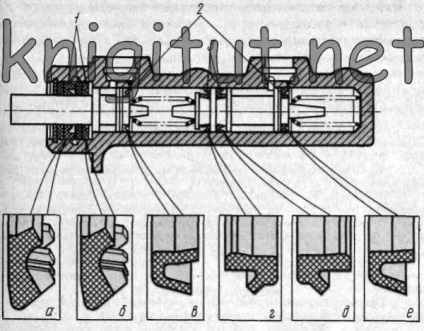
Мал. 158. Установка зовнішніх (1), головних (2) і розподільних (3) манжет головного гальмівного циліндра (а-е - розташування манжет)
Мимовільне гальмування автомобіля може бути через перекриття компенсаційних отворів крайками манжет. Тоді треба зняти бачок головного циліндра і м'яким дротом з затупленим кінцем промацати кромки манжет через компенсаційні отвори. Якщо кінчик дроту, не зустрічаючи пружного опору, проходить на глибину понад 2 мм, то отвір не перекрито кромкою манжети.
Якщо дріт, вставлена в компенсаційний отвір, зустріла пружний опір, треба зняти головний циліндр. Звільнення компенсаційного отвору після зняття головного циліндра вказує на неправильне регулювання підсилювача. Так як головний циліндр знятий, в даному випадку треба рукою натиснути кілька разів на поршень головного циліндра і визначити інтенсивність повернення поршнів в початкове положення.
Якщо компенсаційні отвори на знятому з автомобіля головному циліндрі залишилися перекритими крайками манжет, треба розібрати головний циліндр. Причинами описаного дефекту можуть бути розбухання манжет головного циліндра, забруднення дзеркала головного циліндра, поломка поворотної пружини.
У разі надмірного підвищення зусилля на педалі гальма, а також при постійному пригальмовуванні слід перевірити роботу вакуумного підсилювача і при необхідності відремонтувати його, замінивши зношені деталі.
Перед складанням всі деталі підсилювача повинні бути абсолютно чистими. При необхідності всі деталі підсилювача, за винятком кільця ущільнювача 27 (див. Рис. 85), промити в чистому бензині і висушити струменем стисненого повітря. Тримати деталі в бензині треба мінімально необхідний час.
Розглянемо приклад складання. Збірку і регулювання підсилювача на автомобілях «Москвич-2140» і ГАЗ-3102 здійснюють в такому порядку:
1. В основу 4 вставити направляє кільце 10 і ущільнювальну манжету 11, попередньо змащену мастилом ЦИАТИМ-221.
2. За допомогою оправлення зафіксувати положення ущільнювальної манжети 11 стопорною шайбою 12.
3. Поверхня діафрагми 3 покрити тонким шаром тальку і встановити її на фланець корпусу 13, зафіксувавши запірним кільцем 19. Вкласти в діафрагму опорне кільце 5.
4. Вставити в оболонку сектори опорного диска, фіксуючи їх радіальне положення виступами фіксує шайби 9. Сектори опорного диска розташувати так, щоб гострі кромки, що утворилися при їхній вирубці, були звернені в бік фіксує шайби.
5. Покрити порошком дисульфіду молібдену робочі поверхні центрального клапана, надлишки порошку видалити.
6. Одягти на клапан опорну шайбу і встановити клапан на фіксуючу шайбу 9.
7. Вкласти в назбирати вузол діафрагму. Потім, встановивши пружину 40 і опорну тарілку 6, вставити через отвір в клапані і поршні шток 22.
8. Технологічним гвинтом з'єднати корпус поршня зі штоком, для чого вкрутити технологічний гвинт в шток з боку корпусу поршня приблизно на три оберти. Назбирати вузол вставити в підставу корпусу.
9. Зібрати кришку 1 корпусу зі зворотним клапаном 25. Установити поворотну пружину 20 і, притиснувши діафрагму кришкою корпусу, надіти сполучна кільце 2.
10. Зібрати кришку 1 з підставою 4 корпусу.
11. Установити підсилювач на спеціальний регулювальний стенд і підвести до зворотного клапана 25 розрядження 0,067 МПа. Потім змастити різьбову частину регулювального гвинта 17 спеціальним складом для запобігання від самовідгвинчування і повільно ввертати гвинт в шток підсилювача доти, поки корпус поршня не почне пересуватися всередину підсилювача. У цей момент припинити загвинчування і відвернути гвинт на 1 + 3/4 обороту. При загвинчування гвинта не допускати осьове зусилля від інструменту на регулювальний болт.
12. Змастити спеціальним складом регулювальний болт для запобігання від самовідгвинчування і ввернути його в шток підсилювача, встановити зазор (0,35 ± 0,06) мм між площиною кришки і торцем головки болта. Регулювання регулювальним гвинтом і болтом необхідно закінчити не пізніше ніж через 1 хв після нанесення спеціального складу.
13. Вставити штовхач 16 в корпус 13 поршня, ввернути до упору притискну втулку 14, встановити повітряний фільтр і захисний чохол.
14. Навернути на різьбовий кінець штовхача контргайку і вилку.
На стенді провести контрольну перевірку підсилювача, т. Е .:
натиснути п'ять разів на штовхач підсилювача без подачі розрідження - хід штока 22 при цьому повинен бути 30,50. 33,00 мм;
підвести до зворотного клапана підсилювача розрідження 0,067 МПа, витримати його 5 с і закрити клапан на вакуумному трубопроводі - протягом 15 з розрідження не повинно змінюватися більш ніж на 0,00035 МПа;
підвести до зворотного клапана підсилювача розрідження 0,067 МПа і прикласти до штовхача 16 зусилля 353 Н. Зусилля на штоку 22 повинно бути не менше 529 Н, різниця ходів штовхача і штока 1,65. 2,16 мм;
прикласти до толкателю 16 зусилля (2646 ± 49) Н, при цьому хід штока 22 (до жорсткого упору) повинен складати 3. 30 мм. Підвести до зворотного клапана підсилювача розрідження 0,067 МПа і витримати його 5 с, закрити кран на вакуумному трубопроводі. Протягом 7,5 з розрідження не повинно змінюватися більш ніж на 0,001 МПа.
Примітка. Якщо немає спеціального контрольно-регулювального стенду, пункти 11 і 12 можна виконувати, використовуючи вакуум, створюваний у впускному трубопроводі працює на холостих обертах двигуна.
Передрук матеріалів з даного сайту заборонена.
Допоможіть іншим людям знайти бібліотеку розмістіть посилання: