Основними дефектами підшипників ковзання є: знос і спотворення форми робочих поверхонь; відшарування, викрошіванія або часткове виплавлення бабіту; ризики, збільшені зазори, відколи, тріщини, раковини на поверхнях ковзання; спотворення профілю мастильних канавок; відсутність запасу на регулювання в підшипниках з регульованим зазором; знос торців вкладишів; порушення кріплення втулок і вкладишів; поломка деталей корпусу і кришки, зрив різьби, засмічення і пошкодження маслоподводящие отворів і трубопроводів.
Наслідком зносу робочих поверхонь підшипника є збільшення зазору, поява овальності, конусо- і бочкоподібності. Величину зазору визначають щупом, а для рознімних підшипників також за допомогою двох-трьох свинцевих зволікань або пластинок, які закладаються між валом і вкладишем в розібраний підшипник. Розмір отвору для порівняння його з діаметром валу і визначення таким чином зазору, а також похибка форми отвору встановлюють мікрометричним або індикаторним нутромером.
У нероз'ємних нерегульованих підшипниках ковзання при зносі втулку заміняють або ремонтують. Нову втулку виготовляють із зовнішнім діаметром під запрессовку в корпус і припуском по внутрішньому діаметру під подальшу розгортку або розточування до потрібного розміру.
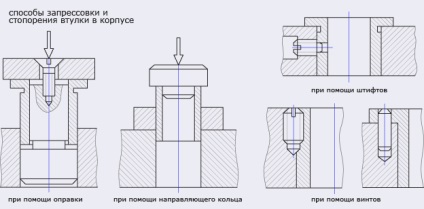
Запресовують втулку пресами, гвинтовими пристосуваннями або вручну молотком. Щоб уникнути перекосу і деформації втулки при запресовуванні, застосовують оправлення або направляючі кільця. Запресовану в корпус втулку стопорять від проворота і осьового зсуву за допомогою гвинтів або штифтів, а потім розгортають або розточують до потрібного розміру. Обробку декількох втулок, розташованих на одній осі, ведуть однієї рядків або набором розгорток з однієї установки з метою забезпечення співвісності отворів. Зношені втулки ремонтують наступними способами:
- Розгортка або розточування втулки з подальшим шабрением під ремонтний розмір при збільшенні діаметра вала нарощуванням.
- Зменшення внутрішнього діаметра втулки осадкою з подальшим розгортанням.
- Біметалічні втулки пере бабітом в наступному порядку: спочатку нагрівають втулки до температури плавлення бабіту, слив розплавленого металу, очищення втулки від залишків бабіту і бруду, знежирення поверхні зануренням в нагрітий до 70-80 ° С розчин каустичної соди, промивка в гарячій воді, лудіння внутрішньої поверхні припоєм ПОС-30 або ПОС-50 і негайна заливка (в тому числі і відцентрова) бабітом, нагрітим до температури заливки, з установкою всередину втулки стрижня з листової сталі, труби або дерева.
температура плавлення і заливання бабіту різних марок
Порядок виготовлення вкладиша наступний: виготовлення втулки, розрізування її на дві половини; припилюванням площин роз'єму по плиті; збірка вкладиша з двох половин з прокладками і фіксація паянням; остаточна обробка зовнішньої і внутрішньої циліндричних поверхонь вкладиша; роз'єднання половин; шабреніе площин роз'єму до 4-6 плям; шабреніе зовнішньої циліндричної поверхні нижнього вкладиша по корпусу, а верхнього - по кришці за умови їх посадки в корпус і кришку з невеликим натягом; розмітка отвори в нижньому вкладиші під штифт, що оберігає від провертання, по паперовому шаблоном, обжимаються по корпусу; свердління непрямого отвори під штифт; свердління по кришці мастильного отвору в верхньому вкладиші; розмітка мастильної канавки; вирубання крейцмейселем із закругленою ріжучої крайкою і обробка напилками мастильної канавки; прішабріваніе внутрішньої циліндричної поверхні вкладиша по шийці вала або шпинделя. При невеликих износах і збільшенні зазору в рознімних регульованих підшипниках прибирають (або замінюють) потрібну прокладку з комплекту, а правильність геометричної форми отвори відновлюють шабрением тригранними або спеціальними шаберами. Порядок робіт при цьому наступний:
- перевірка по фарбі і за допомогою щупа, а при необхідності пригонка зовнішньої циліндричної поверхні і буртиков до корпусу і кришки;
- зачистка мастильних канавок і холодильників;
- попереднє шабреніе нижнього вкладиша по шийці вала або шпинделя з установкою в корпусі або спеціальному пристрої (рекомендується одночасне шабреніе нижніх вкладишів переднього і заднього підшипників);
- попереднє шабреніе верхнього вкладиша по шийці вала або шпинделя;
- остаточне шабрування нижнього і верхнього вкладишів до отримання потрібного числа плям за умови рівномірного їх розташування і покриття не менше 75% поверхні;
- затягування гайок підшипника динамометричним ключем з постійним зусиллям хрест-навхрест, починаючи з середнього підшипника (при його наявності);
- перевірка легкості провороту шпинделя від руки;
- перевірка масляного зазору щупом або свинцевими тяганиною;
- при недостатньому зазорі його збільшують шабрением поверхні;
- перевірка нутромером овальними і конусності отвори вкладиша;
- перевірка індикатором биття вала, встановленого в відремонтованому підшипнику.
Оброблювана поверхня вкладиша
Мінімальна кількість плям в квадраті 25x25 мм
Внутрішня поверхня отвору при діаметрі:
Зовнішня циліндрична поверхня
Торцева поверхня буртів, наполегливих кілець, настановних гайок
Нероз'ємні регульовані підшипники з внутрішнім конусом при зносі і спотворенні форми ремонтують підтяжкою втулки за допомогою настановних гайок і шабрением внутрішньої поверхні втулки по шийці вала. Остаточне шабреніе виробляють без фарби - «на блиск». При використанні всієї різьблення втулку заміняють нової або нарощують по внутрішній поверхні з подальшим розточуванням і приганянням по шийці вала.
Нероз'ємні регульовані підшипники з зовнішнім конусом при зносі ремонтуються стисненням втулки при її осьовому переміщенні за допомогою настановних гайок і шабрением по шийці вала. При використанні всієї різьблення для гайки зовнішня поверхня втулки може бути нарощена металізацією або наплавленням з наступною обробкою.
Для всіх типів підшипників при ремонті повинні ретельно прочищати, перевірятися і при необхідності відновлюватися мастильні отвори і канавки.