При виготовленні більшості деталей потрібно обробляти отвори. Отвори можуть бути як типовими елементами деталі, і використовуватися, наприклад, для розміщення кріплення, або бути виконавчими поверхнями, за якими відбувається сполучення деталей у механізмі, або служити каналами для передачі рідин або газів. Таким чином, в залежності службового призначення вимоги до точності і якості обробки поверхні можуть істотно відрізнятися. Найбільш важливим параметром, що впливає на вибір технології обробки отворів, є ставлення глибини до діаметру. У сучасній металообробці прийнято вважати отвори неглибокими якщо це ставлення не перевищує 5. Для обробки таких отворів, без будь-яких обмежень можуть бути застосовані всі види свердління і остаточної обробки кінцевим і розточувальним інструментом. У той же час до глибоких, однозначно відносяться отвори, з відношенням глибини до діаметру більше 20. Тут доводиться використовувати спеціалізоване обладнання та інструменти для глибокого свердління й розточування, відмінною рисою, яких є наявність напрямних елементів для опори ріжучої частини інструменту об стінки самого оброблюваного отвору. Відповідно, в діапазоні проміжних співвідношень довжини до діаметру можуть використовуватися з певними обмеженнями, як подовжені версії звичайних інструментів, так і інструменти для обробки глибоких отворів. Кожна з представлених систем показує найвищу ефективність у своєму діапазоні діаметрів і глибин свердління.
Свердління і розсвердлювання
Найбільш поширеним методом отримання отворів в суцільному матеріалі є свердління. Рух різання під час свердління - обертальний, рух подачі - поступальний. Перед початком роботи перевіряють збіг вершин переднього і заднього центрів верстата. Заготівлю встановлюють в патрон і перевіряють, щоб її биття (ексцентричність) щодо осі обертання не перевищувала припуску, що знімається при зовнішньому обтачивании. Перевіряють биття торця заготовки, в якому буде оброблятися отвір, і вивіряють заготовки по торця. Перпендикулярність торця до осі обертання заготовки можна забезпечити підрізуванням торця, при цьому в центрі заготовки можна виконати поглиблення для потрібного напрямку свердла і запобігання його відведення та поломки.
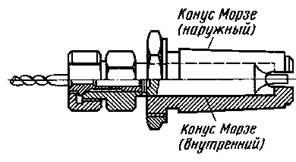
При свердлінні отвору, глибина якого більше його діаметра, свердло періодично виводять з оброблюваного отвору і очищають канавки свердла і отвір заготовки від накопичилася стружки. Для зменшення тертя інструмента об стінки отвору свердління виробляють з підведенням мастильно-охолоджувальної рідини (МОР), особливо при обробці сталевих і алюмінієвих заготовок. Чавунні, латунні і бронзові заготовки можна свердлити без охолодження. Застосування МОР дозволяє підвищити швидкість різання в 1,4-1,5 рази. Як МОР використовуються розчин емульсії (для конструкційних сталей), компаундують масла (для легованих сталей), розчин емульсії і гас (для чавуну і алюмінієвих сплавів). Якщо на верстаті охолодження не передбачено, то в якості МОР використовують суміш машинного масла з гасом. Застосування МОР дозволяє знизити осьову і тангенціальну сили різання на 10-35% при свердленні сталей, на 10-18% при свердлінні чавуну і кольорових сплавів і на 30-40% при свердленні алюмінієвих сплавів. При свердлінні на прохід в момент виходу свердла з заготівлі необхідно різко знизити подачу щоб уникнути поломки свердла. Для збереження інструменту при свердлінні слід працювати з максимально допустимими швидкостями різання і з мінімально допустимими подачами. Якщо вісь свердла збігається з віссю шпинделя токарного верстата, свердло правильно заточене і жорстко закріплено, то оброблене отвір має мінімальні похибки. У правильно заточеного свердла працюють обидві ріжучі кромки, і стружка сходить по двом спіральних канавках. Розміри отвору при свердленні виходять більше заданих в наступних випадках: ріжучі кромки свердла мають різну довжину, хоча і заточені під однаковими кутами; ріжучі кромки мають різну довжину і заточені під різними кутами; ріжучі кромки мають рівну довжину, але заточені під різними кутами. При неправильно і недостатньо заточеним сверл виходить косе отвір з великою шорсткістю поверхні. Крім того, при роботі недостатньо заточеним (тупим) свердлом у вихідний частини отвори утворюються задирки. Неоднакова довжина ріжучих крайок і несиметрична їх заточування, ексцентричне розташування перемички і різна ширина стрічок викликають защемлення свердла в отворі, що збільшує сили тертя (у міру поглиблення свердла в заготовку) і, як наслідок, призводить до поломки інструменту. Обробляється отвір називається глибоким, якщо його глибина в 5 разів більше його діаметра. При свердлінні глибокого отвору застосовують довге спіральне свердло зі звичайними геометричними параметрами, яке періодично виводять з оброблюваного отвору для охолодження і видалення накопичилася в канавках стружки. Для підвищення продуктивності обробки застосовують свердла з примусовим відведенням стружки, які здійснюються за допомогою рідини (або повітря), що підводиться в зону різання під тиском.
Зі збільшенням глибини свердління погіршуються умови роботи свердла, погіршується відведення теплоти, підвищується тертя стружки об стінки канавок інструмента, утруднюється підведення МОР до ріжучим кромок. Тому якщо глибина свердління більше трьох діаметрів оброблюваного отвору, то швидкість різання слід зменшити. Для свердління отворів застосовують спіральні свердла, які виготовляють з інструментальних сталей (вуглецевої У12А і легованої 9ХС), з швидкорізальних сталей (Р6М5 та ін.), А також з твердих сплавів (ВК6М, ВК8М і ВК10М). Для свердел з швидкорізальних сталей швидкість різання u = 25-35 м / хв, для свердел з інструментальних сталей u = 12-18 м / хв, для твердосплавних свердел u = 50-70 м / хв. Причому великі значення швидкості різання приймаються при збільшенні діаметра свердла і зменшенні подачі. При ручній подачі свердла важко забезпечити її постійне (стабільне значення). Для стабілізації подачі використовують різні пристрої. Для механічної подачі свердла його закріплюють у різцетримачі. Свердло 1 з циліндричним хвостовиком, малюнок снізулева - а) за допомогою прокладок 2 і 3 встановлюють в резцедержателе так, щоб вісь свердла співпадала з лінією центрів. Свердло 1 з конічним хвостовиком, малюнок ліворуч - б) встановлюють в державке 2, яку кріплять у різцетримачі.
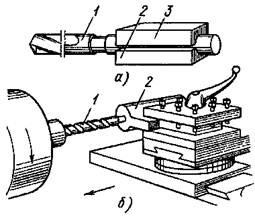
Після вивірки збігу осі свердла з лінією центрів супорт зі свердлом вручну підводять до торця заготовки і обробляють пробне отвір мінімальної глибини, а потім включають механічну подачу супорта. При свердлінні на прохід перед виходом свердла з заготівлі механічну подачу значно зменшують або відключають і закінчують обробку вручну. При свердлінні отворів діаметром 5-30 мм подача S = 0, l-0,3 мм / об для сталевих деталей і S = 0,2-0,6 мм / об для чавунних деталей. Різання під час свердління має ряд особливостей в порівнянні з різанням при точіння, оскільки спіральне свердло - багатолезовий інструмент, який виробляє різання п'ятьма ріжучими крайками (двома головними, двома допоміжними і поперечної).
При свердлінні отворів у міру зносу свердла по задній поверхні осьова сила і крутний момент збільшуються; наприклад, при зносі задньої поверхні свердла на 1 мм вказані параметри зростають майже на 60-80%. Для підвищення ефективності роботи спіральними свердлами використовують такі способи, як подточка поперечної кромки, зміна кута при вершині, подточка стрічки, подвійна заточка, попереднє розсвердлювання отворів і ін. Стандартні свердла мають кут при вершині 118 градусів, однак для обробки більш твердих матеріалів (і більш глибоких отворів) рекомендується застосовувати свердла з кутом при вершині 135 градусів. Форми заточування ріжучої частини свердла показані на малюнку нижче.
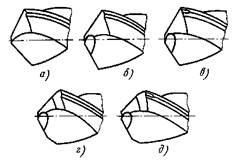
а) - нормальна, б) - нормальна з подточкой перемички, в) - нормальна з подточкой перемички і стрічки, г) - подвійна з подточкой перемички, д) - подвійна з подточкой перемички і стрічки
Розсвердлювання дозволяє отримати більш точні отвори і зменшити відведення свердла від осі деталі. При свердлінні отворів великого діаметра (понад 25-30 мм) зусилля подачі може виявитися надмірно великим. Тому в таких випадках свердління виробляють в кілька прийомів, т. Е. Отвір рассверливают. Режими різання при розсвердлювання отворів ті ж, що і під час свердління. На малюнку зліва елементи різання при свердлінні -а) і розсвердлюванні - б) отвори: n - обертання свердла, Sz - подача припадає на одну ріжучу кромку, a і b - товщина і ширина зрізаногошару, t - припуск на сторону, D - діаметр основного отвори, Do - діаметр попередньо просвердлений отвори
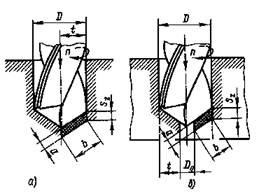
Зенкування і розгортання
Зенкування. Зенкером обробляють отвори, попередньо штамповані, литі або просвердлені. Малюнок - а). Припуск під Зенкер (після свердління) складає 0,5-3 мм на сторону. Зенкер вибирають в залежності від оброблюваного матеріалу, виду (наскрізне, ступеневу, глухе) і діаметра отвору і заданої точності обробки. Зенкер має три і більше ріжучі кромки, тому при зенкеровании знімається тонша стружка і виходять більш точні отвори, ніж під час свердління; він міцніше свердла, завдяки чому подача при зенкування в 2,5-3 рази перевищує подачу при свердлінні. Зенкування може бути як попередньої (перед розгортанням), так і остаточної операцією. Крім обробки отворів зенкери застосовуються для обробки торцевих поверхонь. Для підвищення точності зенкерования (особливо при обробці литих або штампованих глибоких отворів) рекомендується заздалегідь розточити (різцем) отвір до діаметру, рівного діаметру зенкера на глибину, приблизно рівну половині довжини робочої частини зенкера. Для обробки високоміцних матеріалів (sв> 750 МПа) застосовують зенкери, оснащені пластинами з твердого сплаву. Швидкість різання для зенкерів зі швидкорізальної сталі така ж, як і для свердел. Швидкість різання твердосплавних зенкерів в 2-3 рази більше, ніж зенкерів з швидкорізальної сталі. При обробці високоміцних матеріалів і лиття по шкірці швидкість різання твердосплавних зенкерів слід зменшувати на 20-30%.
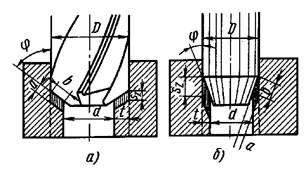
Розгортання. Для отримання отворів високої точності і якості оброблюваної поверхні застосовують розгортання. Малюнок - б). Розгортка має значно більше різальних крайок, ніж зенкер, тому при розгортанні знімається тонша стружка і виходять більш точні отвори, ніж при зенкеровании. Отвори діаметром до 10 мм розгортають безпосередньо після свердління. Перед розгортанням отворів більшого діаметра їх попередньо обробляють, а торець підрізають. Припуск під розгортання t = 0,15-0,5 мм для чорнових розгорток і 0,05-0,25 мм для чистових розгорток. При роботі чистовими розгорненнями на токарних і токарно-револьверних верстатах застосовують хитні оправлення, які компенсують розбіжність осі отвору з віссю розгортки. Для того щоб забезпечити високу якість обробки, свердління, зенкування (або розточування) і розгортання отвори виробляють за одну установку заготовки в патроні верстата. Подача при розгортанні сталевих деталей 0,5-2 мм / об, а при розгортанні чавунних деталей 1-4 мм / об. Швидкість різання при розгортанні 6-16 м / хв. Чим більше діаметр оброблюваного отвору, тим менше швидкість різання при однаковій подачі, а при збільшенні подачі швидкість різання знижують.
Якщо діаметр отвору перевищує діаметр стандартних свердел або зенкерів, то такий отвір розточують. Розточування застосовується також при обробці отворів з нерівномірним припуском або з непрямолінійних утворює. Токарні розточувальні різці для обробки наскрізних - а) і глухих - б) отворів показані на малюнку нижче. У токарних розточувальних стрижневих різців, малюнок в) і г) консольна частина В виконується круглої, а стрижень С, службовець для кріплення різця - квадратним (12Х12, 16х16, 20х20 і 25х25 мм); такими різцями можна розточувати отвори діаметром 30-65 мм. Для підвищення вібростійкості ріжучакромка різців виконується по осі стрижня, малюнок д) і е). На токарно-револьверних верстатах застосовують розточувальні різці круглого перетину, які кріпляться в спеціальних державках, малюнок ж). Форма передньої поверхні і всі кути у розточувальних різців, за винятком заднього, приймаються такими ж, як і у прохідних, що застосовуються при зовнішньому точінні. Задній кут a<12 градусов при растачивании отверстий диаметром более 50 мм и a>12 градусів при розточування отворів діаметром менше 50 мм. Значення кутів різання у розточувальних різців можна змінювати шляхом установки ріжучої кромки різців щодо поздовжньої осі деталі (вище або нижче осі). При розточуванні різець знаходиться в більш важких умовах, ніж при зовнішньому поздовжньому точінні; так як погіршуються умови для відводу стружки, підведення МОР і відведення теплоти. Розточувальний різець має менший перетин державки і більший виліт, що викликає віджимання різця і сприяє виникненню вібрацій; тому при розточування, як правило, знімається менший перетин стружки і знижується швидкість різання. При чорновому розточуванні стали приймають глибину різання до 3 мм; подовжню подачу 0,08- 0,2 мм / об; швидкість різання близько 25 м / хв для різців з швидкорізальної сталі і 50-100 м / хв для твердосплавних різців. При чистовому розточування глибина різання не перевищує 1 мм, поздовжня подача 0,05-0,1 мм / об, швидкість різання 40-80 м / хв для різців з швидкорізальної сталі і 150-200 м / хв для твердосплавних різців.
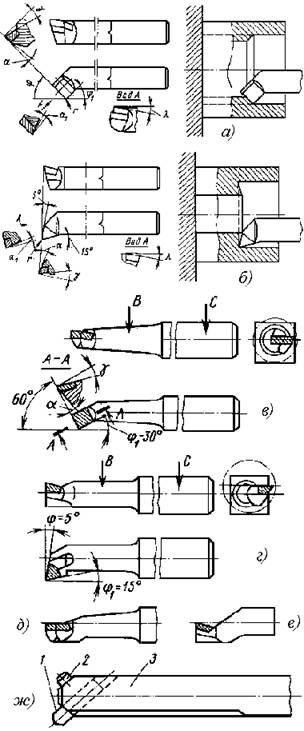
розрізання отвір різьблення складальний