Процес металізації полягає в нанесенні на поверхню деталі розплавленого металу струменем стисненого повітря. Товщина покриття в залежності від його призначення може бути від 0,03 до 10 мм і більше. При ремонті машин металлизация напиленням має поки обмежене застосування: нарощування зношених поверхонь валів, цапф, усунення різних дефектів в корпусах (раковин, пор), декоративні та антикорозійні покриття.
Фізична сутність процесу металізації полягає в наступному: напилюваний метал розплавляється будь-яким джерелом тепла і за допомогою стиснутого повітря або інертного газу розпорошується на дрібні частинки діаметром від 3 до 300 мкм.
Розплавлені частки металу, пролітаючи відстань від зони плавлення до поверхні деталі, встигають кілька охолонути і з рідкого стану переходять в твердий. У момент удару ці частинки, володіючи досить велику кінетичну енергію, контактують з мікрорельєфом поверхні деталі і між собою, утворюючи на поверхні деталі покриття. Міцність покриття визначається молекулярними силами зчеплення контактних ділянок та чисто механічним зчепленням напилюються частинок за нерівності поверхні деталі. Середня температура потоку частинок у поверхні деталі відносно невисока (близько 70 ° С), що пов'язано з подачею великого об'єму повітря і невеликого обсягу частинок металу. В процесі напилення частки металу піддаються окисленню. Покриття виходить пористим, досить крихким, що мають низький межа міцності на розтяг. Залежно від джерела розплавлення металу розрізняють наступні види металізації: Газополум'яний, дугову, високочастотну, плазмову.
Газопламенная металлизация. На рис. 11.1 показана схема розпилення металу газовим металізатора: присадний дріт 3 розплавляється полум'ям суміші горючого газу (ацетилену або пропан-бутану) з киснем. Ця суміш подається по кільцевому каналу 1, а по кільцевому каналу 2 подається стиснене повітря або інертний газ, який розпилює рідкий метал. Розплавлення металу проводиться в відновному полум'ї 4, що дозволяє зменшити вигоряння легуючих елементів (вуглецю, марганцю та ін.) І тим самим підвищити якість напилюваного металу. Перевагою газопламенной металізації є порівняно невелике окислення металу. Недолік способу - складність установки і невисока продуктивність процесу (2-4 кг напилюваного металу в 1 ч).
Дугова металізація полягає в тому, що електрична дуга збуджується між двома присадні дріт 1 (рис. 11.2), які ізольовані одна від одної і безперервно подаються роликовим механізмом 2 зі швидкістю 0,6-1,5 м / хв через наконечник 3. Одночасно через сопло 4 в зону дуги надходить повітря або інертний газ під тиском 0,4-0,6 МП а. Розплавлений метал видувається стисненим повітрям на поверхню деталі 5.
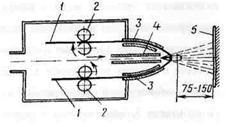
Переваги дугового металізації - відносно висока продуктивність процесу (від 3 до 14 кг напилюваного металу в 1 ч) і досить просте обладнання. До недоліків процесу відносяться значне вигоряння легуючих елементів і підвищений окислення металу.
Високочастотна металлизация заснована на розплавлення присадочного дроту за допомогою індуктора, який харчується струмом високої частоти (200-300 кГц) від лампового генератора. Високочастотна металлизация в порівнянні з дугового має ряд переваг: зменшується вигоряння легуючих елементів дроту в 3-6 разів і зменшується пористість покриття; збільшується продуктивність процесу, так як застосовується дріт більшого діаметру (3-6 мм); зменшується приблизно в 2 рази питома витрата електроенергії. Недолік - більш складне обладнання.
Плазмова металізація - вельми перспективний спосіб напилення металів, так як дозволяє отримувати покриття з тугоплавких і зносостійких матеріалів, в тому числі з твердих сплавів. Цей спосіб заснований на здатності газів переходити за певних умов в стан плазми. Плазмою називається газ, що знаходиться в сильно іонізованому стані під впливом різних факторів: температури, електричного або високочастотного розряду, # 947; - випромінювання, детонації.
При плазмової металізації плазма утворюється пропусканням плазмо-утворить газу через дугового розряд, який збуджується між двома електродами. Плазмова обробка здійснюється в спеціальних установках, які називаються плазмотронами, або плазмовими головками. На рис. 11.3 показана принципова схема установки для плазмового металізації. Установка складається з плазмотрона і пристрої для подачі напилюваного-порошку.
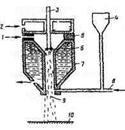
Плазмотрон складається з катода 3 і анода (сопла) 7, охолоджуваних потоком води 2.Катод виготовлений з вольфраму, анод - з міді. Катод ізольований від анода прокладкою 5. Для отримання плазмового струменя між катодом і анодом збуджують електричну дугу 6. Плазмообразующий газ, введений в зону горіння дуги по каналу 1, іонізується і виходить з сопла 7 у вигляді струменя невеликого перерізу.
Як плазмообразующего газу використовують аргон або азот і рідше водень або гелій. Температура плазмового струменя досягає 10 000-30 000 ° С. Більш високу температуру (15 000-30 000 ° С) має аргону плазма, однак азотна плазма є великим носієм теплової енергії. Як напилюваного матеріалу застосовують гранульований порошок 4.
Подача порошку в плазмовий струмінь здійснюється по каналу 8 транспортирующим газом (азотом). Витрата порошку регулюють в межах від 3 до 12 кг / год. Напилюваний порошок розплавляється плазмовим струменем 9 і наноситься на поверхню 10 деталі.