СИРІ МАТЕРІАЛИ ДОМЕННОЇ ПЛАВКИ
Кам'яне вугілля, запаси якого дуже великі, не може бути, на жаль, безпосередньо використаний в якості палива в шахтних печах. Вугілля містить 20-40% летких речовин, які вже при нагріванні до 250-350 ° С і вище починають інтенсивно виділятися, розриваючи шматки самого міцного вугілля з утворенням вугільного пилу. Цей пил забиває порожнечі між більшими шматками руди, агломерату, окатишами, різко погіршує газопроникність стовпа шихти в печі, захаращує горн печі вугільним пилом і сміттям. Робота доменних печей на вугіллі завжди пов'язана перш за все з зниженням техніко-економічних показників плавки, а потім з важкими розладами ходу і аваріями.
Лише окремі пласти найстарішого кам'яного вугілля - антрациту використовували в доменних печах невеликої висоти, але в даний час запаси такого вугілля повністю вичерпані (шахтинский антрацит в Донбасі, вугілля пластів «Потужний» у Прокопьевска «Волковський» у Кемерово, Кузбас, а також пенсильванский в США, і уельський в Великобританії), і плавка на антрациті представляє лише історичний інтерес. Зі сказаного випливає, що присутність кам'яного вугілля в шихті доменних печей є неприпустимим і має бути повністю виключено. Якщо з яких-небудь причин організаційного характеру доменний цех вичерпав всі запаси коксу, а поруч на складах ТЕЦ є багато кускового міцного вугілля, доцільно проте повністю зупинити доменні печі, чекаючи прибуття коксу. В кінцевому рахунку втрати виробництв в цьому випадку виявляться набагато меншими, ніж при введенні вугілля в шихту печей без їх зупинки.
З початку залізного віку основним пальним в сиродутних горнах, а потім в домницях і доменних печах був деревне вугілля - продукт піролізу (обвуглювання без доступу повітря) деревини при 350-650 С С. Найбільш древнім є так званий «купчасто» спосіб виробництва деревного вугілля. Високу купу дров засипали по поверхні землею, обкладали дерном, обмазували глиною, залишаючи біля основи купи лише кілька отворів, через які до центру купи надходило невелика кількість повітря, необхідного для спалювання частини дров. У верхній частині купи залишали отвори для виходу продуктів згоряння дров і газоподібних продуктів піролізу деревини. В сучасних вуглевипалювальних печах вагонетки з деревними цурками послідовно проходять через секції камерної печі, де йде піроліз деревини і куди безперервно подаються нагріті В топках продукти згоряння дров і вугілля. Такі печі дозволяють повністю вловити цінні газоподібні продукти переугліванія дров. Вихід деревного вугілля з дров коливається зазвичай в межах від 60 до 74% (об'ємні.), Його уявна густина дорівнює 0,38 г / см 3 (березовий вугілля); 0,29 г / см 3 (сосновий вугілля); 0,26 г / см 3 (ялиновий вугілля). Насипна маса 1 м 3 сухого пічного деревного вугілля становить 130-200 кг / м 3. Механічна міцність деревного вугілля невелика і дозволяє здійснювати плавку на ньому лише В доменних печах з корисною висотою до 18 м.
Деревне вугілля має високу реакційною здатністю і горючістю, що пов'язано з його величезною пористістю (80-87%.). У зв'язку з цим деревне вугілля горить перед повітряними фурмами доменної печі в окислювальних зонах невеликого обсягу, що перешкоджає роботі з високонагретим дутьем, також зменшує розміри окислювальних зон.
В даний час виплавка древесноугольного чавуну в великих масштабах ведеться лише в Бразилії, де на величезних площах в зоні річки Амазонки вирубуються ліси, а оборот рубки евкаліпта становить всього 7 років (оборот рубки хвойних дерев на Уралі 60-70 років). У 1982 р в Бразилії в 134 малих доменних печах було виплавлено на деревному вугіллі 4,4 млн. Т чавуну.
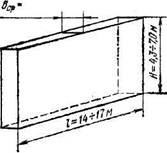
Мал. 4. Камера коксової печі
У зв'язку з обмеженнями рубки лісу в XVI-XVIII ст, були знову зроблені численні спроби доменної плавки на кам'яному вугіллі, але всі вони закінчилися невдачею. Необхідно було створити нове штучне паливо для доменних печей. Таким паливом і став кам'яновугільний кокс.
Процес високотемпературного коксування вугілля був винайдений А. Дербі в 1735 р Він полягає в піролізі вугілля без доступу повітря при 900-1100 ° С протягом 14-18 год.
Розглянемо процес коксування більш докладно.
Перед завантаженням в коксову піч вугільна шихта подрібнюється до фракції <3 мм. Компоненты шахты усредняются по составу на специальных складах, затем тщательно смешиваются.
Після укладання шихти в піч і вирівнювання поверхні шихти планує піч ретельно герметизують. Нагрівання шихти в печі відбувається тільки теплопровідністю від двох її стін всередині яких в, так званих, опалювальних простінках спалюється суміш доменного і коксового газів і досягаються температури до 1350-1400 ° С. Виділяються з шихти гази і негайно відводяться з печі через спеціальні отвори. Як уже згадувалося вище, головною причиною руйнування шматків кам'яного вугілля в доменній печі є інтенсивне виділення з вугільної речовини великої кількості летючих. Тому завдання процесу коксування полягає у видаленні основної маси летких ще в коксової печі і створенні міцного кускового продукту, що містить не більше 1,5-2% летючих речовин, що запобігає руйнуванню коксу в доменній печі.
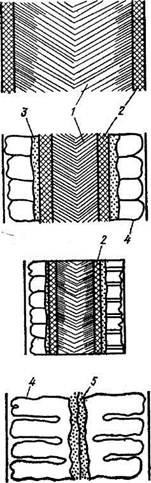
Мал. 5. Стадії коксування вугілля: 1 - шихта; 2 - пластичний шар; 3 - напівкокс; 4 - кокс; 5 - осьова вертикальна тріщина
Розрізняють такі послідовно протікають стадії високотемпературного коксування кам'яного вугілля:
1. Сушка вугілля при нагріванні в інтервалі температур до 100 -120 ° С.
2. Нагрівання вугілля до 300-350 ° С. Хороший коксівне вугілля на цій стадії проходить лише фізичний прогрів часток без руйнування (деструкції) легкоплавких з'єднань - бітумів, при розпаді яких і виділяються летючі речовини. Так, високоякісне коксівне кузнецкий вугілля при нагріванні до 300 ° С виділяє лише до 12-15% всієї маси летких. Бітуми в цьому вугіллі не руйнуються аж до плавлення. Навпаки, некоксівне вугілля на цій стадії виділяє велику масу летких, бітуми в них піддаються деструкції, вугілля втрачає здатність плавитися; кокс з такого вугілля не може бути отриманий.
3. Пом'якшення і плавлення вугілля при 350-500 ° С. Першими плавляться легкоплавкие бітуми. У утворився первинному розплаві розчиняється вся інша маса вугільної шихти. Лише невелика частина вугільних частинок зберігає свою індивідуальність і не розчиняється в рідкій фазі. З розплаву інтенсивно виділяються летючі, що різко змінює його хімічний склад, збільшує в'язкість. Пори в коксі - це бульбашки і трубки, по яких рухалися летючі в масі розплаву; стінки їх тверднуть і зберігаються потім в готовому продукті,
4. При 500-600 ° С розплав твердне у вигляді першого, ще слабкого в механічному відношенні продукту - напівкоксу, зі тримає зазвичай ще близько 50% (по масі) всіх летючих вихідної вугільної шихти.
5. При 600-1100 ° С здійснюється багатогодинне прожарювання коксу, що дозволяє майже повністю видалити з нього летючі, провести часткову графітизацію речовини коксу, т. Е. Перетворення аморфного вуглецю в кристалічний гексагональний графіт. Ступінь графитизации готового коксу оцінюється, за експериментальними даними, в 15-20%. Саме в ході перекристалізації і спікання речовини коксу при 600-1100 ° С його міцність і твердість зростають в 30- 40 разів.
На рис. 4 показана форма робочого простору коксової печі, яка представляє собою прямокутний паралелепіпед, злегка розширюється в бік видачі коксу. Процес коксування йде в ній від двох поздовжніх стін печі в напрямку до осі печі (рис. 5). Так як обсяг готового коксового пирога зазвичай трохи менше обсягу вугільної шихти, по осі пирога утворюється вертикальна тріщина - «розвал». Таким чином, довжина шматка коксу зазвичай становить приблизно половину ширини камери коксової печі.
Особливо ефективний попередній підігрів вугільної шихти нагрітим азотом в реакторі з киплячим шаром до 180 220 ° С. Як видно з даних рис. 6, при коксуванні холодної вологої вугільної шихти температура в осьовій зоні коксової печі (200 мм від стінки печі) навіть через 11 годин після початку коксування становить лише 500 ° С. Вона досягає 1000 ° С лише через 14 год.
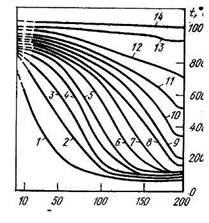
про від стінки млості; мм
Мал. 6. Розподіл температур в коксової печі по її ширині. Загальна ширина камери печі 407 мм. Температура в опалювальних простінках 1300 ° С. Цифри на кривих - час (ч) від початку коксування
2 ч). Міцність формованого коксу, отриманого за розглянутою технологією, виявляється вищою, ніж міцність звичайного коксу. Перша доменна плавка на формованому коксі, проведена в СРСР в 1972 р дала позитивний результат. Хід доменної печі і техніко-економічні показники плавки на новому паливі були краще, ніж на донецькому коксі. Численні досліди за кордоном також показали, що формований кокс є повноцінною заміною звичайного кам'яновугільного коксу.